Dismounting Induction Heater
What is Dismounting?
Dismounting refers to the process of removing a component from a shaft or housing. It is the opposite of mounting, which involves installing a component onto a shaft or housing. Dismounting can be necessary for repair or replacement of a component, or for maintenance purposes. The process may involve using specialized tools, such as pullers or presses, to safely and efficiently remove the component. Induction heating is becoming more popular for dismounting processes because it offers several advantages over traditional methods such as puller tools. With puller tools, there is a risk of damaging the component or surrounding machinery during the removal process. Induction heating provides a more controlled and gentle method of heating the component, causing it to expand and release its grip on the shaft or housing without damaging either component.
Why is the Induction Heater used for Dismounting Processes?
Induction heaters are used for dismounting processes because they can quickly and safely heat the workpiece to the desired temperature, allowing for the expansion of the component and making it easier to remove. Unlike traditional dismounting methods such as puller tools, induction heating can be used on a wide range of components and can apply heat to specific areas without affecting surrounding parts. Induction heating is also less likely to cause damage to the workpiece or the equipment, reducing the risk of costly repairs and downtime. Overall, induction heating is a reliable and efficient method for dismounting processes in various industries.
Introduction to Industrial Induction Heater for Dismounting
The process of removing or disassembling components or machines from a larger structure or system is referred to as dismounting. This procedure is frequently required for the maintenance, repair, or replacement of worn or damaged parts. To avoid damaging the components or the larger structure or system, dismounting necessitates the use of specialised tools and techniques. Dismounting is commonly used to remove inner racers from bearings, throwers from centrifugal pumps, and tubes from piping or equipment. Dismounting must be done with care and attention to ensure that it is done safely and efficiently. An induction heater can also help with the removal of components from larger structures or systems. When a component, such as a bearing on a shaft, becomes stuck or seized in place, an industrial induction heater can be used to heat the component and cause it to expand, breaking the friction bond between the component and the larger structure. This can make removing the component easier without damaging it or the larger structure. GM Industries is a prominent manufacturer and supplier of industrial induction heaters for a wide range of processes. Processes like dismounting require precise and controlled heating, which is made possible by the high level of control offered by induction heating technology.
Advantages of Using an Industrial Induction Heater for Dismounting
Using an industrial induction heater for dismounting has several advantages over other methods:
Efficiency
Induction heating is a quick and efficient way to heat metal parts. It quickly and directly heats the metal, allowing for faster dismounting of parts.
Accuracy
Induction heating is an accurate method of heating metal parts. It enables precise temperature control, lowering the risk of component damage.
Security
Induction heating is a safe way to heat metal parts. It avoids direct contact with the metal, lowering the possibility of accidents and injuries.
Cost-effective
Using an induction heater can be less expensive than other methods of heating. It uses less energy and requires less labour than other methods.
Flexibility
Induction heating is suitable for a wide range of metal parts and applications. It can be used to detach bearings.
Overall, using an industrial induction heater for dismounting provides a safer, faster, more efficient, and more precise method for heating metal parts compared to other methods. It can save time, reduce labour costs, and minimize the risk of damage to parts.
Induction Heater for Various Dismounting Process
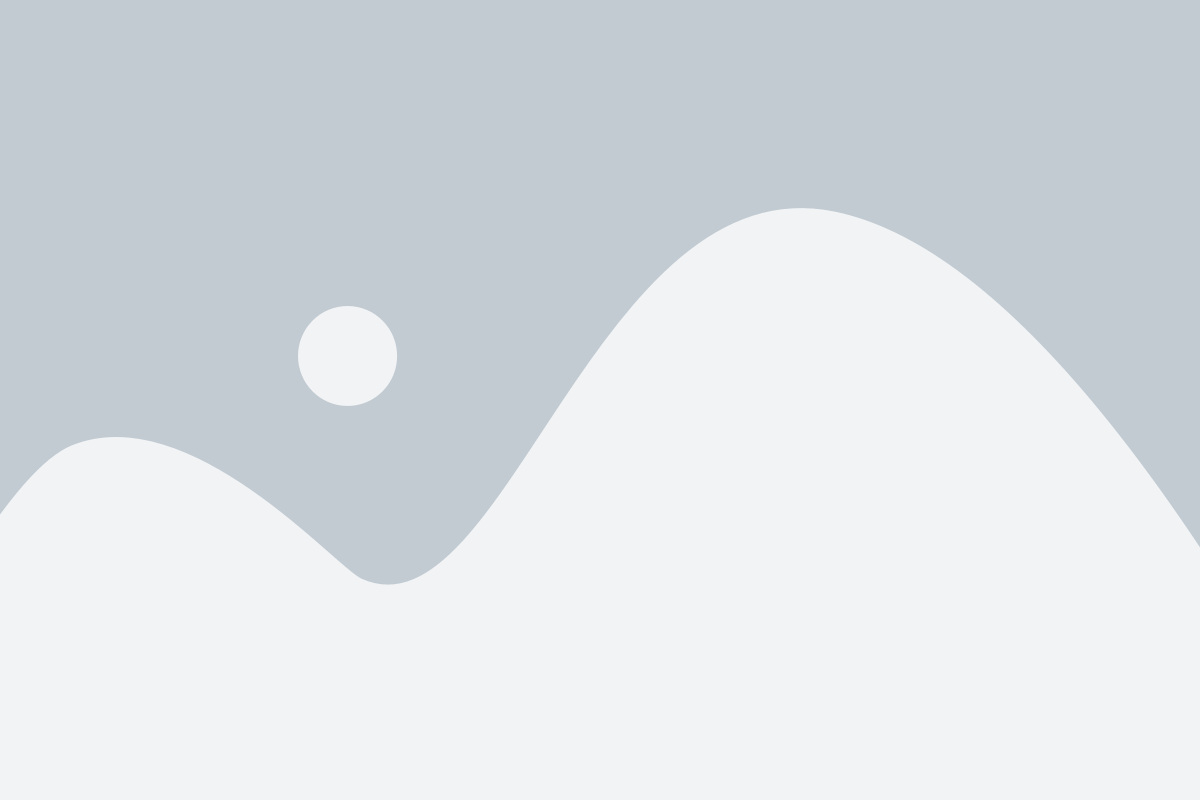
Induction Heater for Dismounting of Inner Racer
The inner race is a component of a bearing that rotates along with the shaft. Dismounting of the inner race involves removing the race from the shaft or housing, often using specialized tools such as bearing pullers or hydraulic presses. An induction heater is used for dismounting the inner race of a bearing because it heats up the race quickly and uniformly, allowing it to expand and loosen its grip on the shaft. This makes it easier to remove the race from the shaft without damaging either component.
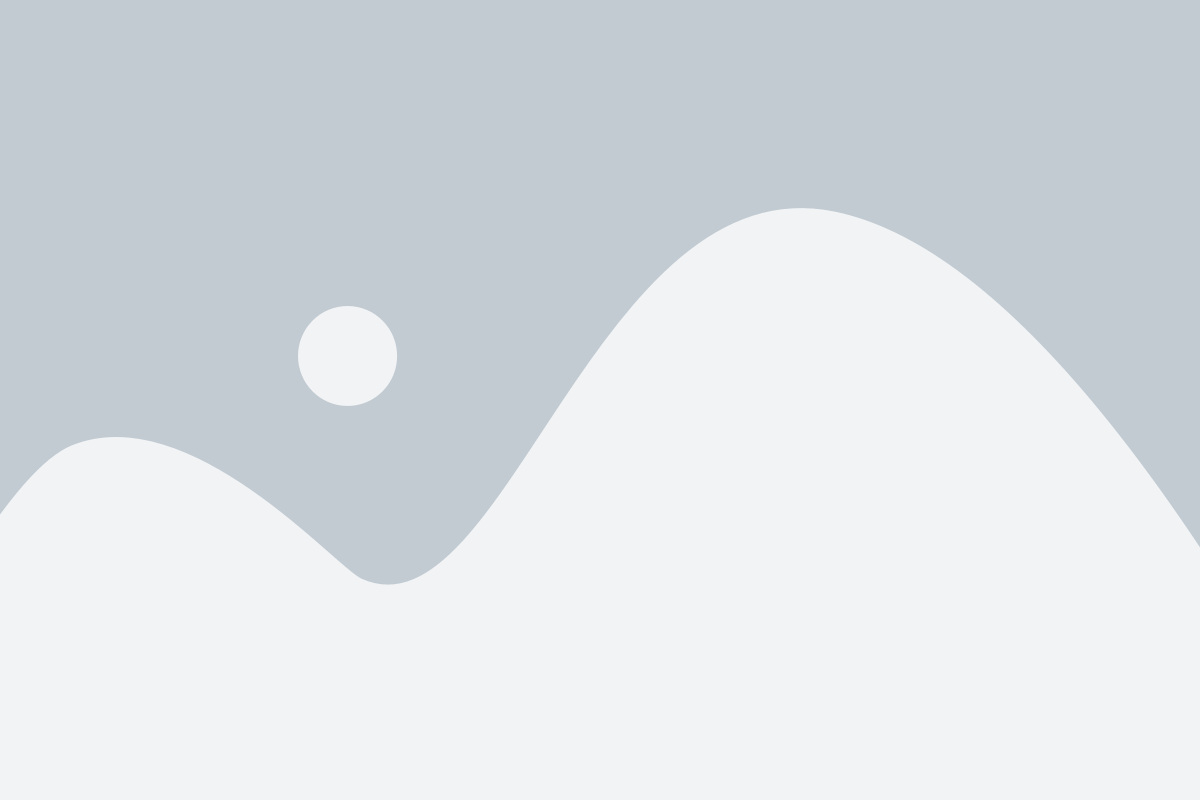
Induction Heater for Dismounting of throwers
Throwers are components that are used in centrifugal pumps to prevent debris from entering the impeller. Dismounting of throwers involves removing the thrower from the pump housing, which may require the use of specialized tools such as pullers or cutters. An induction heater is often used for dismounting throwers because it can heat up the metal of the thrower without touching it directly. When a metal object is heated, it expands, and when it cools, it contracts. This principle can be used to loosen metal parts that are stuck together due to rust or other types of corrosion. By heating the thrower, the metal expands, which can break the bond between the thrower and the shaft. This makes it easier to remove the thrower from the machine.
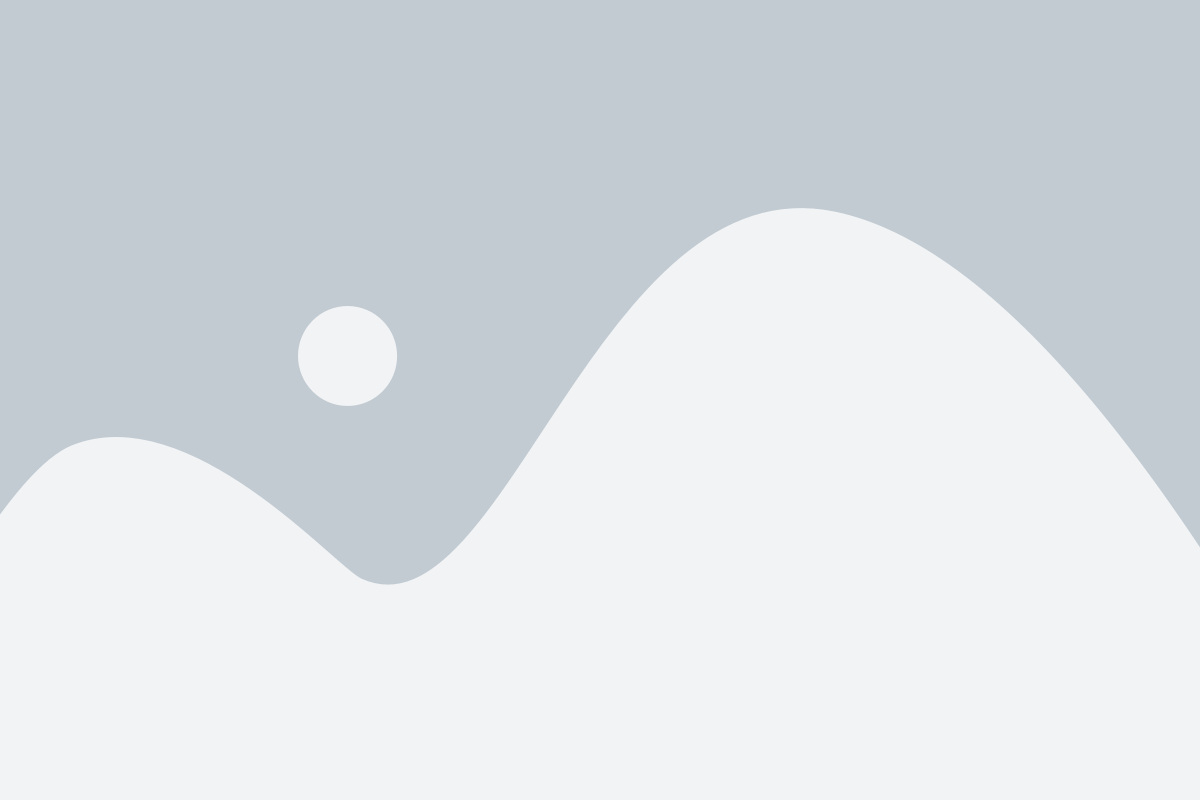
Induction Tube Heater
Tubes are used in various industrial applications for conveying fluids or gases. Dismounting of tubes involves disconnecting the tube from the piping or equipment, often requiring the use of specialized tools such as wrenches or cutters. An induction heater is frequently used for tube dismounting because it can heat the tube’s metal without directly touching it. A metal object expands when heated and contracts when cooled. This principle can be used to disassemble metal parts that have become stuck together due to rust or other forms of corrosion. When the tube is heated, the metal expands, which can cause the bond between the tube and the surrounding structure to break. This makes removing the tube from the assembly easier.
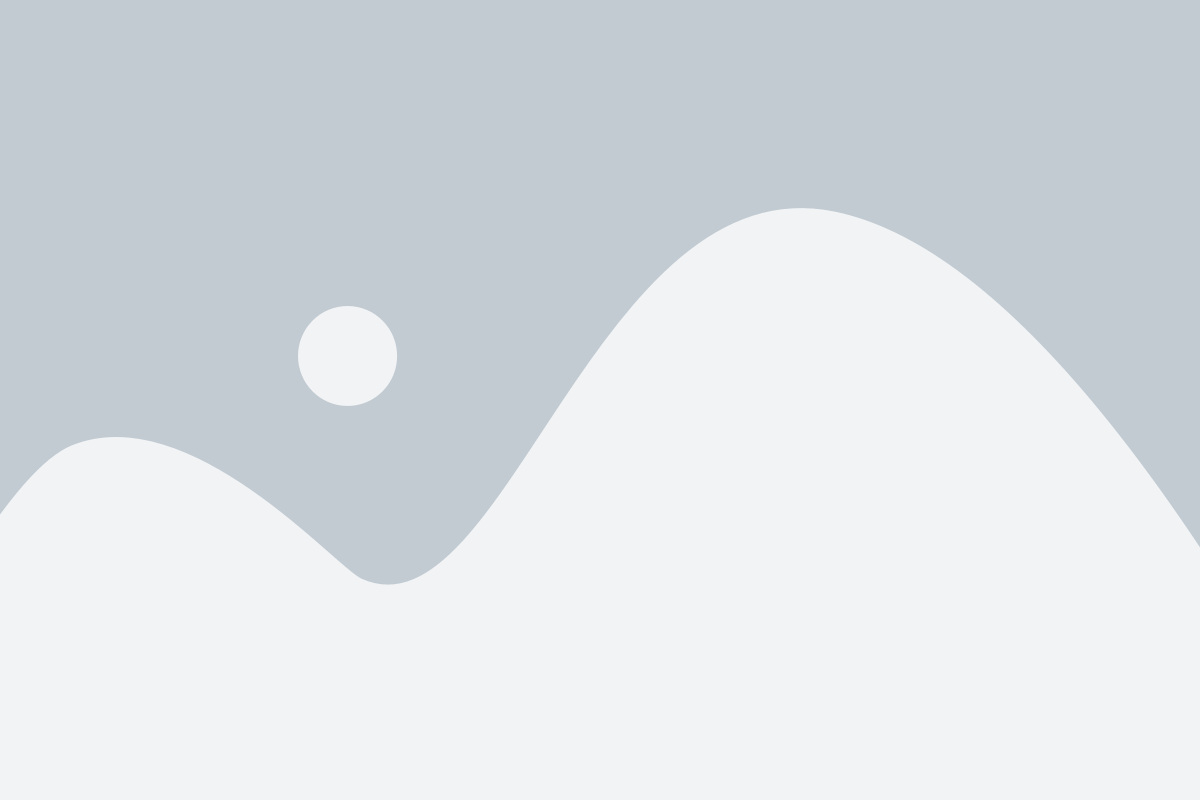
Induction Heater for Bearing Removal
The process of bearing removal involves the dismounting of the bearing from a shaft or housing. An induction heater can be used to heat the bearing and make it easier to remove from the shaft without damaging either component. The heat generated by the induction heater can be precisely controlled to ensure that the bearing is heated uniformly, allowing it to expand and loosen its grip on the shaft. This method is more efficient than using traditional methods like bearing pullers or hydraulic presses, which can damage the bearing or the shaft.
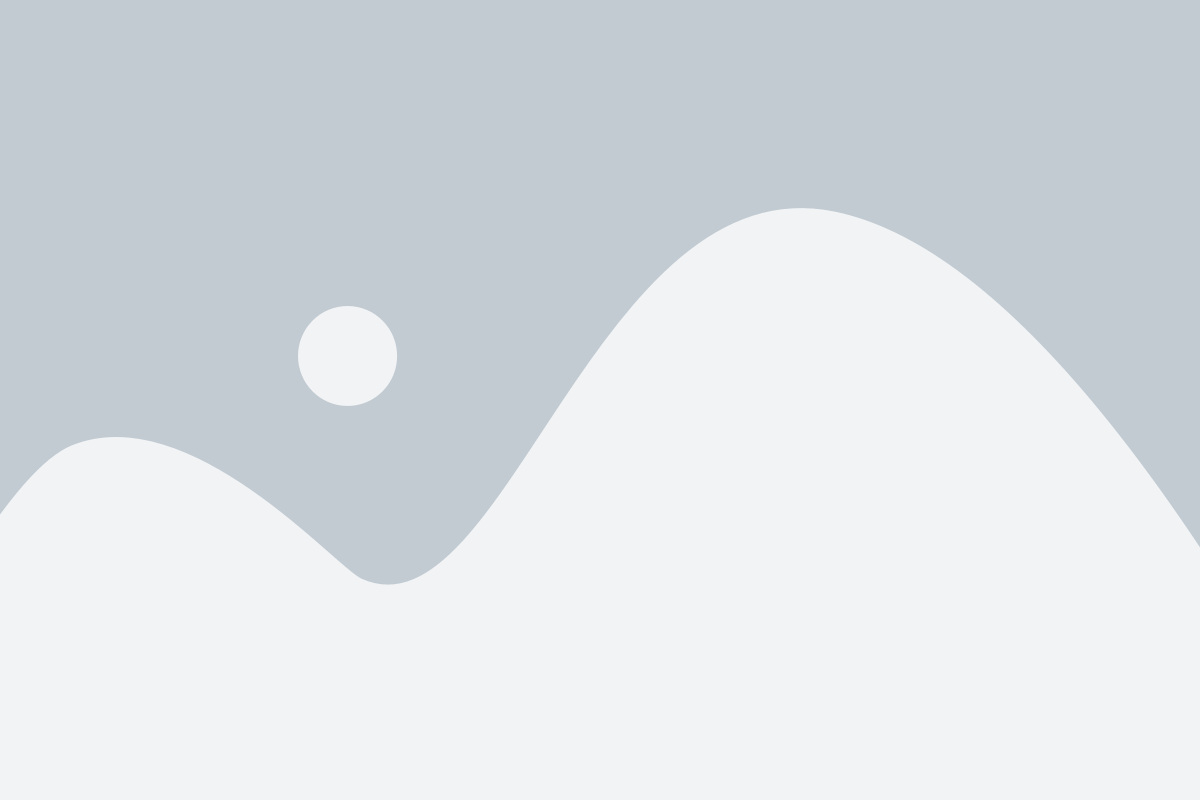
Induction Heater for Gears
Gears are critical components in various industrial applications, including machinery, vehicles, and aerospace. The removal of gears can be a challenging task due to the complexity of their shape and size. Induction heating is an effective method for dismounting gears, as it provides a quick and efficient way to expand or shrink the gear. The heat generated by the induction heater can be precisely controlled to ensure that the gear is heated uniformly, allowing it to expand or shrink and make it easier to install or remove from the shaft or housing.
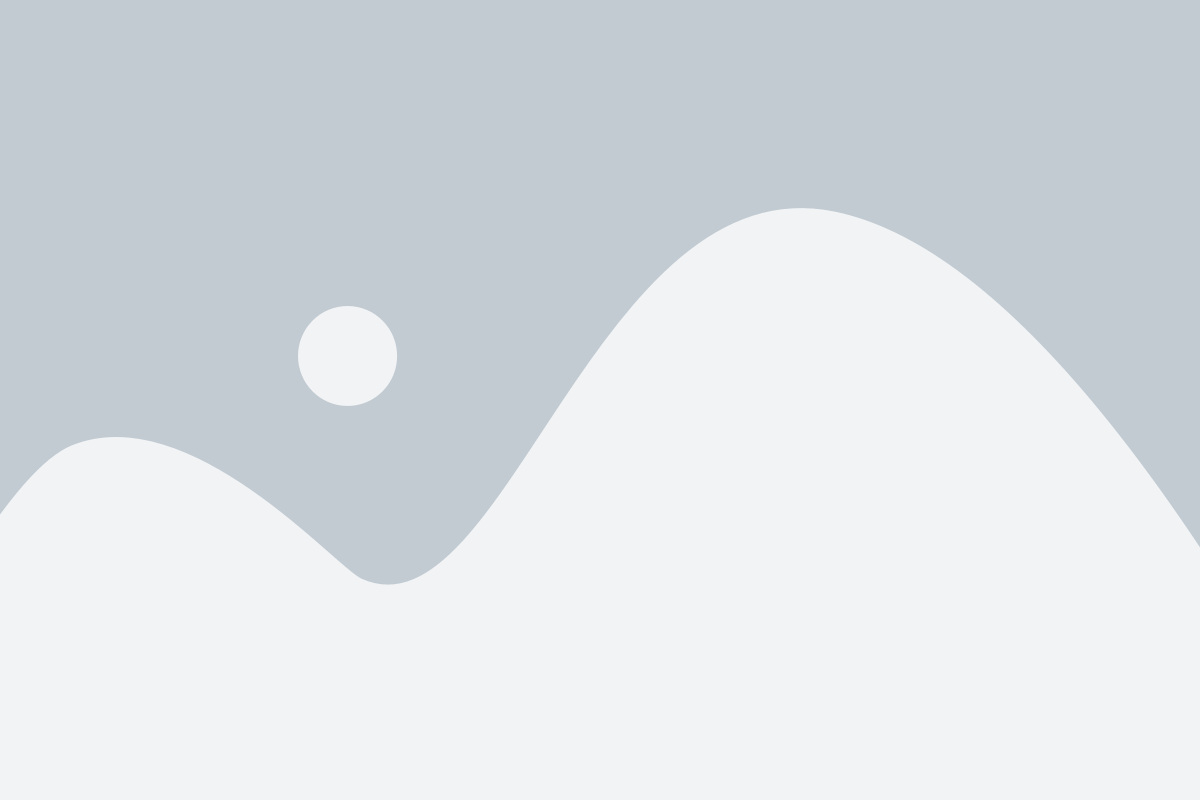
Induction Heater for Shafts
Shafts are components that rotate along with the bearings, gears, or other moving parts. The removal of shafts can be challenging due to their size and complexity. Induction heating is an efficient method for dismounting shafts, as it provides a quick and safe way to expand or shrink the shaft. The heat generated by the induction heater can be precisely controlled to ensure that the shaft is heated uniformly, allowing it to expand or shrink and make it easier to install or remove from the bearings, gears, or other moving parts.
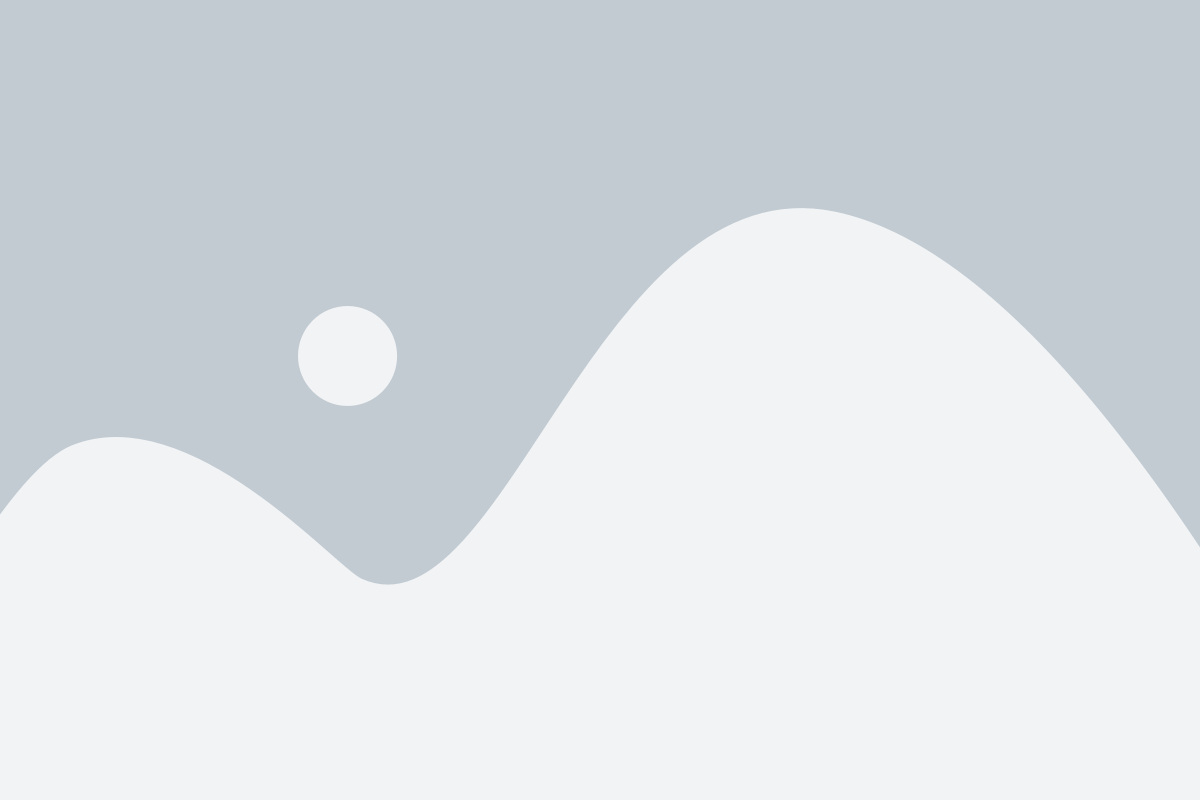
Coupling Induction
Couplings are components used to connect two shafts together and transmit power from one shaft to another. The removal of couplings can be a challenging task due to their size and complexity. Induction heating is an effective method for dismounting couplings, as it provides a quick and efficient way to expand or shrink the coupling. The heat generated by the induction heater can be precisely controlled to ensure that the coupling is heated uniformly, allowing it to expand or shrink and make it easier to install or remove from the shafts.
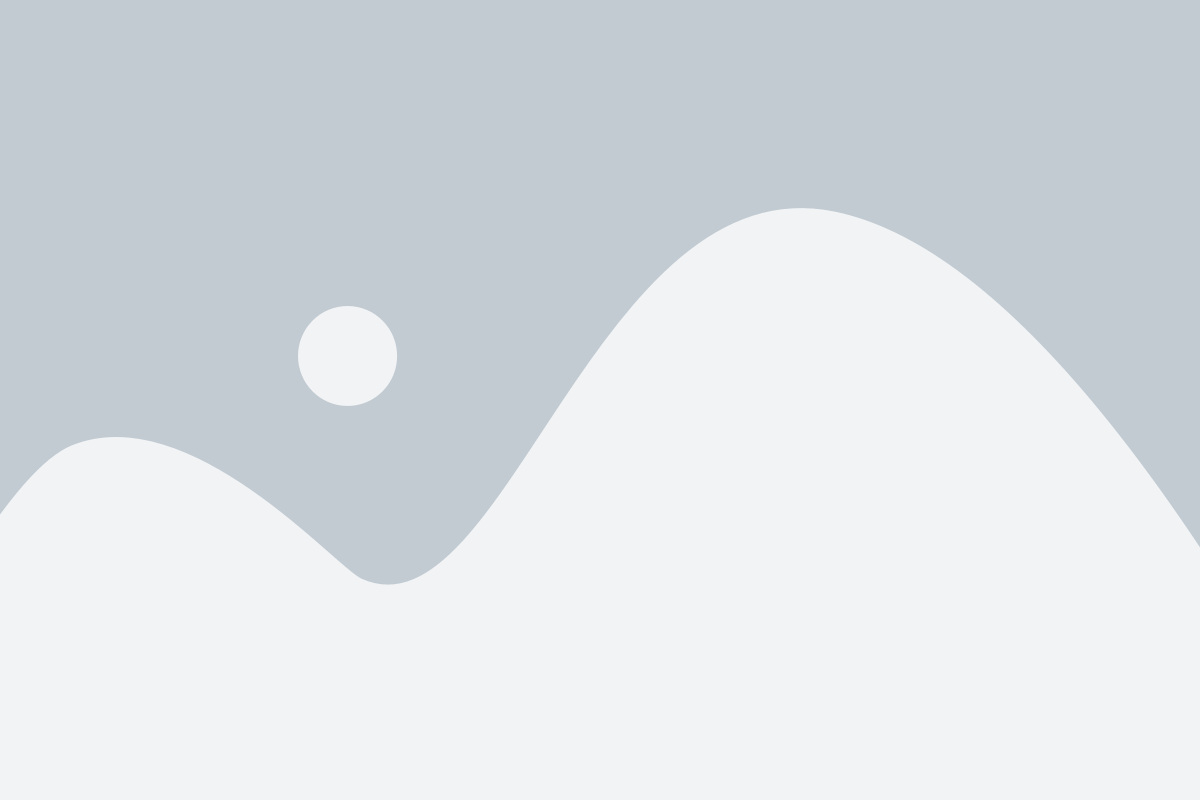
Induction Heater for Bolt Removal
Bolts are components used to fasten parts together. The removal of bolts can be a challenging task, especially if they are rusted or seized. Induction heating is an efficient method for bolt removal, as it provides a quick and safe way to expand the bolt and break its grip on the thread. The heat generated by the induction heater can be precisely controlled to ensure that the bolt is heated uniformly, allowing it to expand and make it easier to remove from the thread.
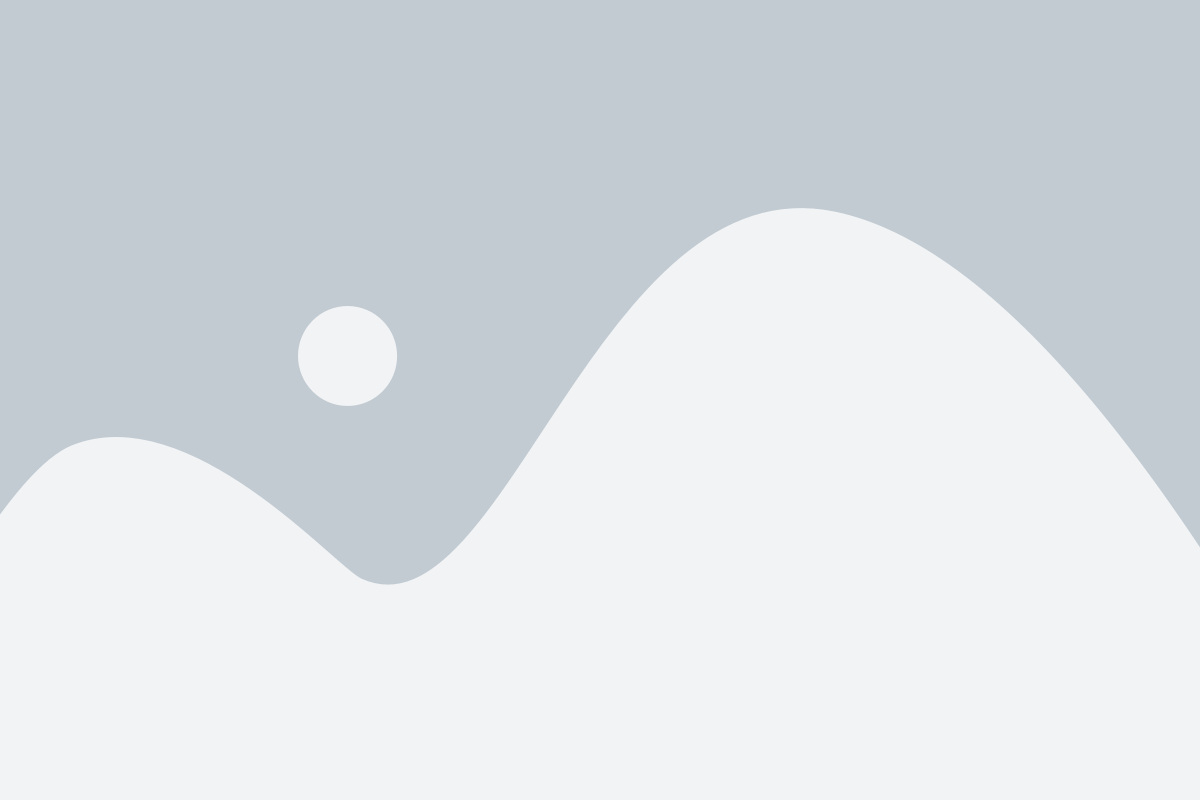
Induction Heater for Bushings
Bushings are components used to reduce friction between moving parts. The removal of bushings can be a challenging task due to their size and complexity. Induction heating is an effective method for dismounting bushings, as it provides a quick and efficient way to expand or shrink the bushing. The heat generated by the induction heater can be precisely controlled to ensure that the bushing is heated uniformly, allowing it to expand or shrink and make it easier to install or remove from the housing or shaft.
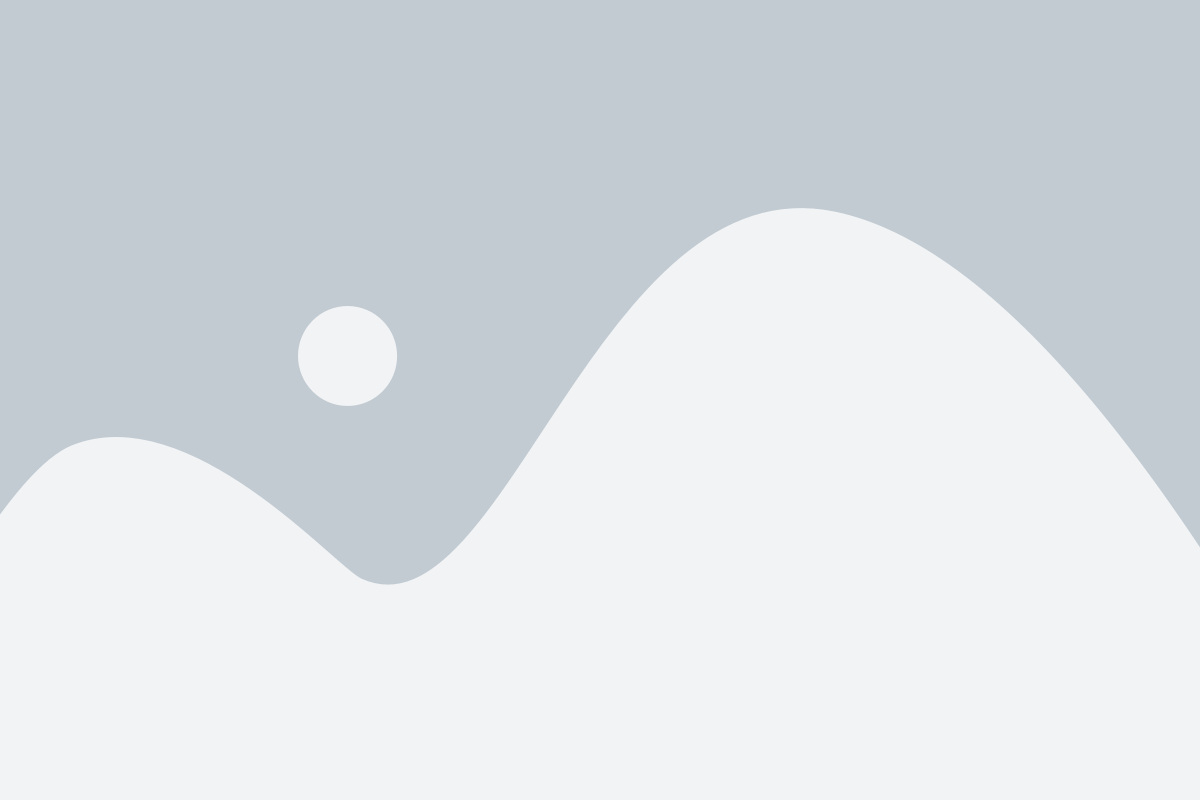
Induction Heater for Sleeves
Sleeves are used to cover or protect components such as bearings, shafts, and cylinders. Installing or removing sleeves can be a challenging task, especially if they are tightly fitted. An induction heater can be used to expand the sleeve, making it easier to install or remove it from the component. The heater applies heat evenly and quickly to the sleeve, allowing it to expand and loosen its grip on the component. This ensures that the sleeve can be safely removed without damaging the component, saving time and reducing the risk of costly repairs.
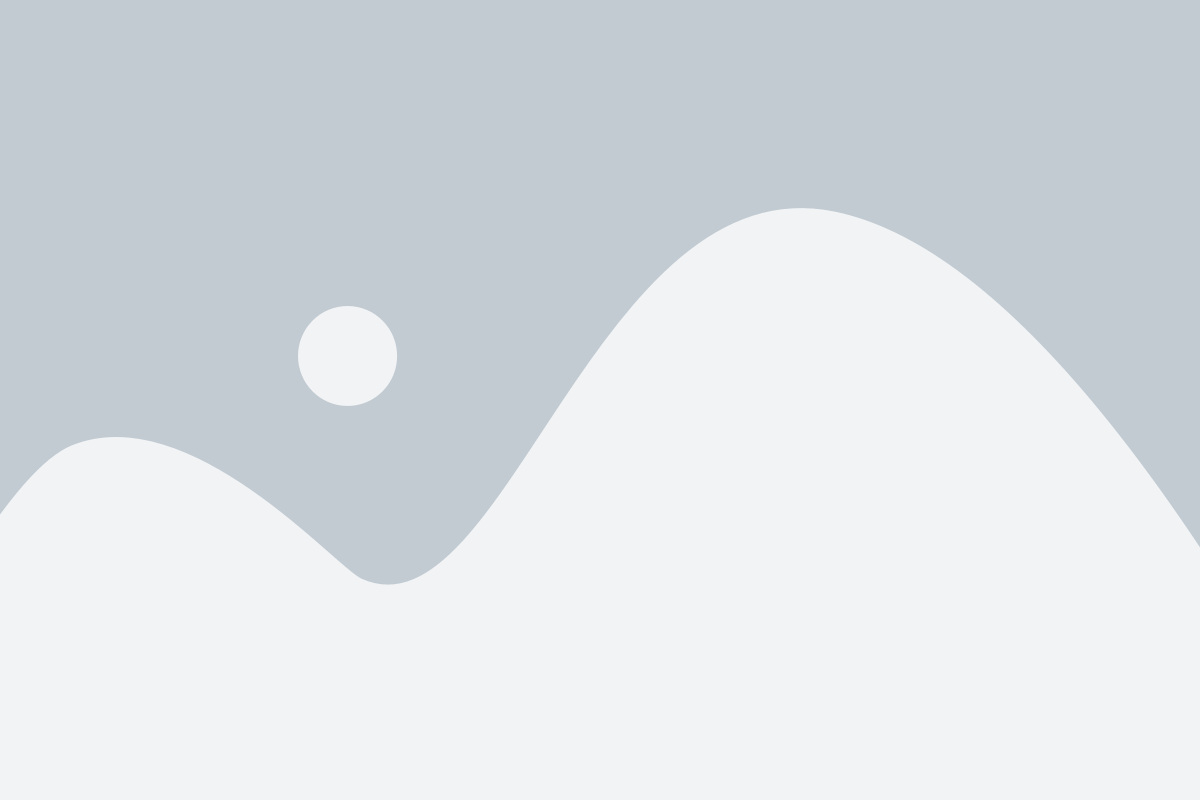
Induction Heater for Seals
Seals are critical components that prevent fluid or gas leakage in machinery such as pumps, valves, and engines. When replacing or repairing a seal, it is essential to remove it without damaging the surrounding components. An induction heater can be used to heat the seal uniformly and quickly, allowing it to expand and loosen its grip on the component. This makes it easier to remove the seal without damaging the component, ensuring that the new seal can be installed securely.
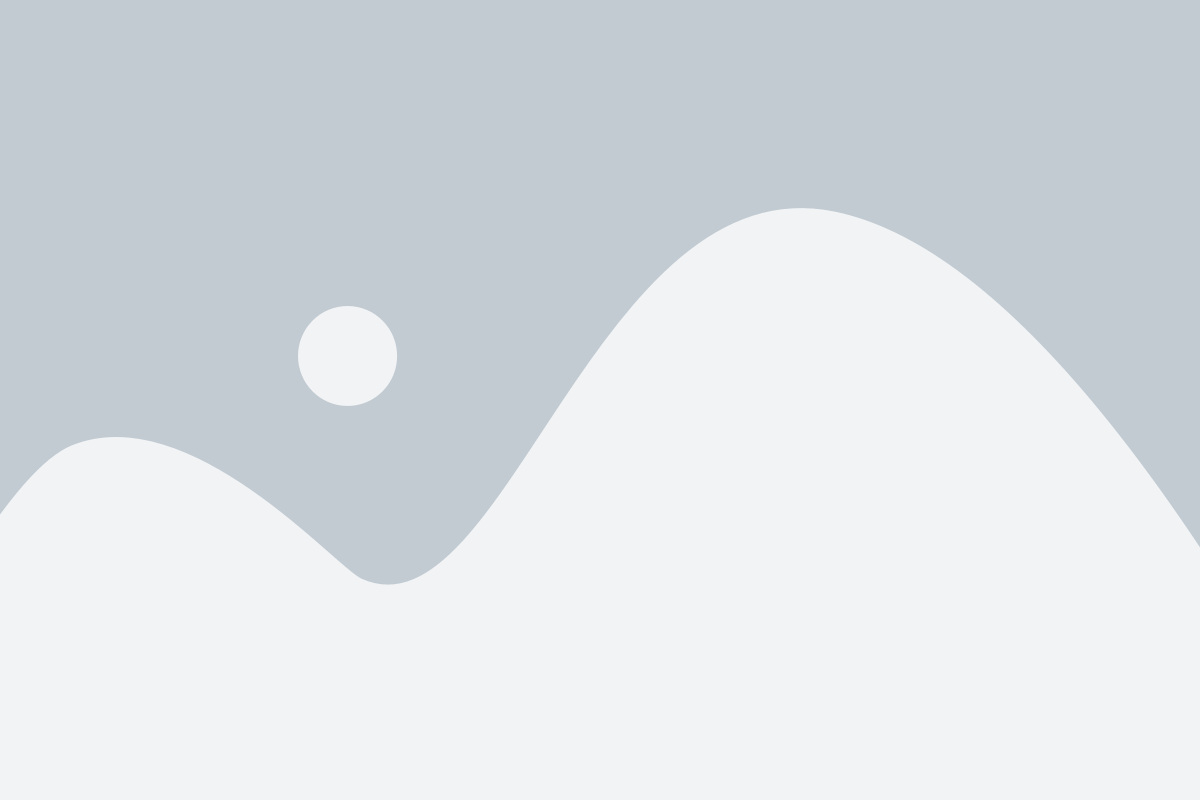
Induction Heater for Retaining Rings
Retaining rings are used to hold components such as bearings and gears in place. Removing retaining rings can be challenging, especially if they are tightly fitted. An induction heater can be used to heat the retaining ring, allowing it to expand and loosen its grip on the component. This makes it easier to remove the retaining ring without damaging the component.
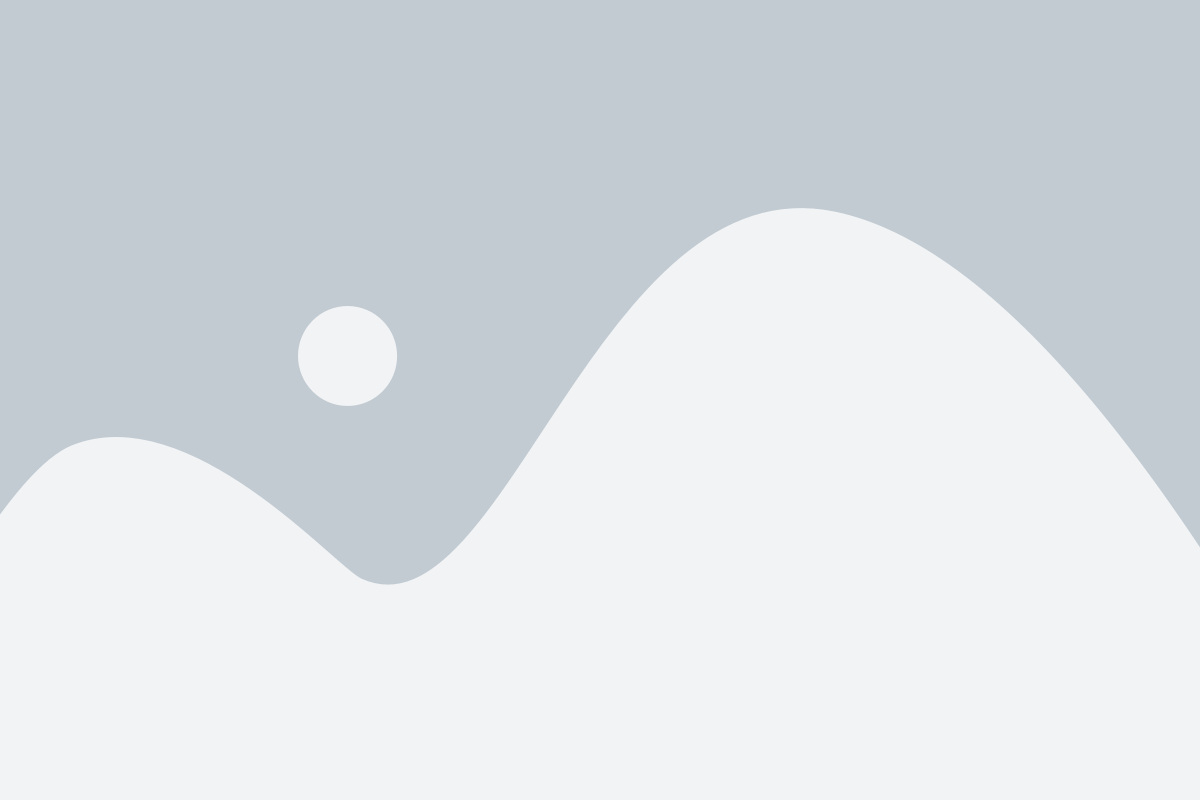
Induction Heater for Sprockets
Sprockets are used in various industrial applications such as conveyor systems and power transmission systems. Removing sprockets can be challenging, especially if they are tightly fitted. An induction heater can be used to heat the sprocket, allowing it to expand and loosen its grip on the shaft. This makes it easier to remove or install the sprocket without damaging the shaft or the sprocket.
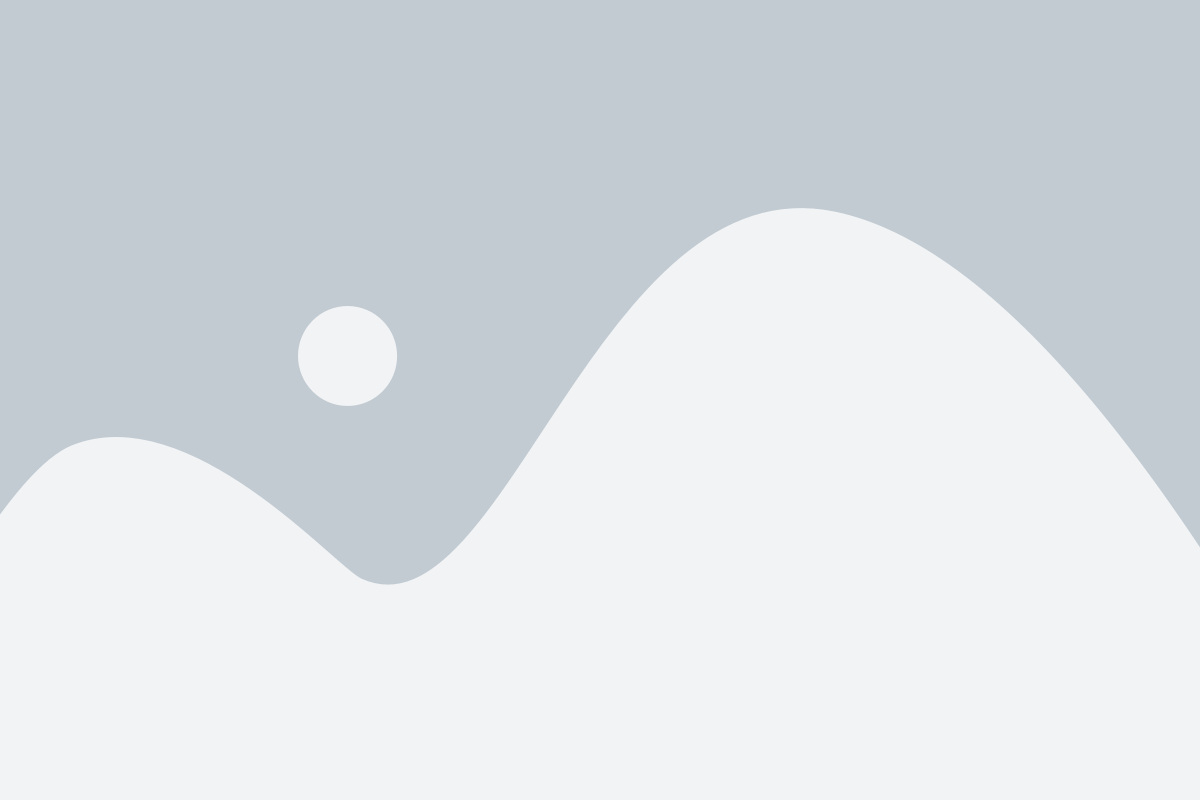
Induction Heater for Impellers
Impellers are critical components in various industrial applications such as pumps and turbines. Removing impellers can be a challenging task, especially if they are tightly fitted. An induction heater can be used to heat the impeller, allowing it to expand and loosen its grip on the shaft. This makes it easier to remove the impeller without damaging the shaft or the impeller.
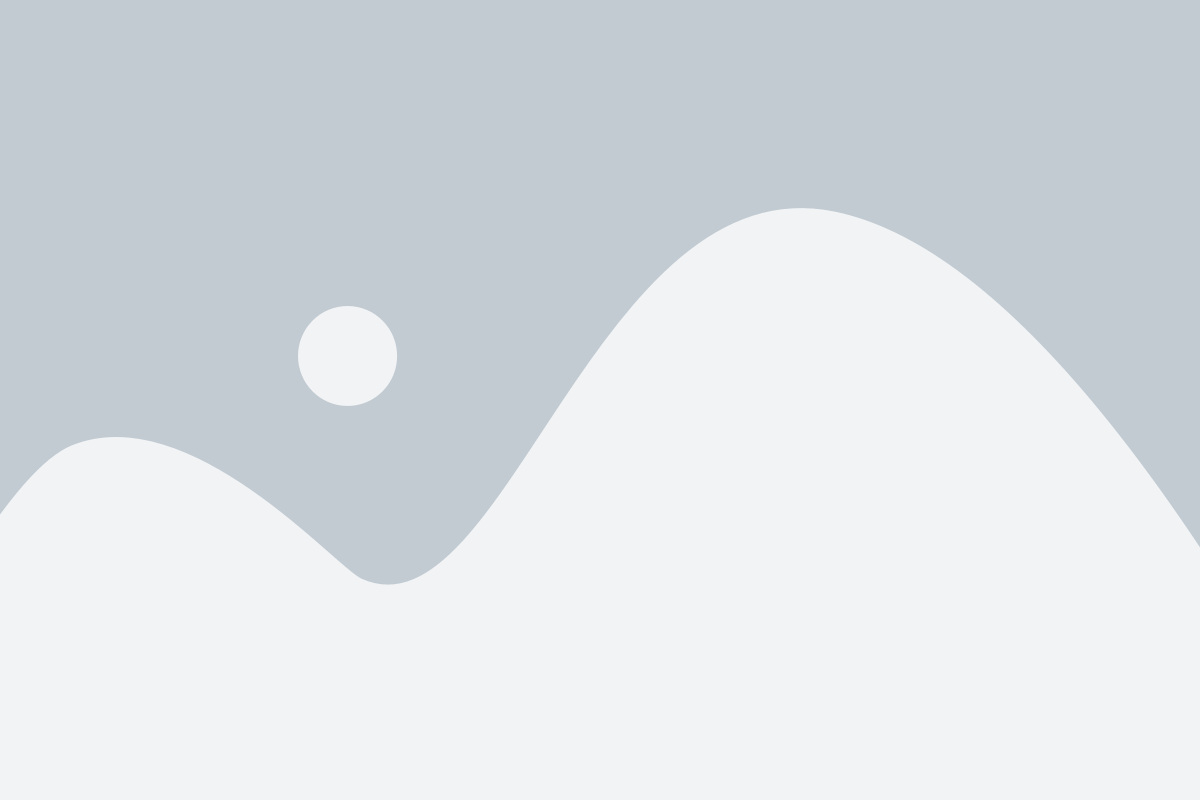
Induction Heater for Turbines
Turbines are used in various industrial applications such as power generation and aerospace. Removing turbines can be a challenging task, especially if they are tightly fitted. An induction heater can be used to heat the turbine, allowing it to expand and loosen its grip on the shaft. This makes it easier to remove the turbine without damaging the shaft or the turbine.
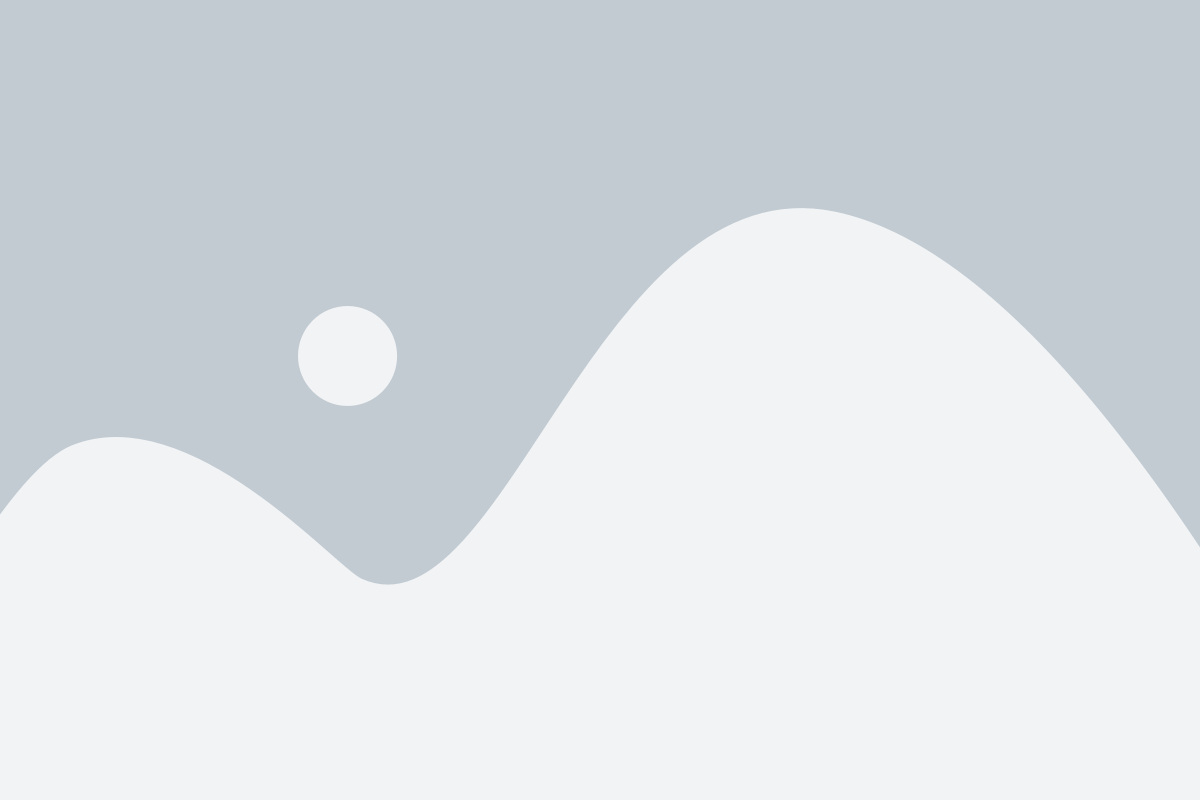
Induction Heater for Fasteners
Fasteners such as nuts, bolts, and screws are critical components that hold machinery together. Removing fasteners that are tightly fitted can be a challenging task. An induction heater can be used to heat the fastener, allowing it to expand and loosen its grip on the component. This makes it easier to remove the fastener without damaging the surrounding components.
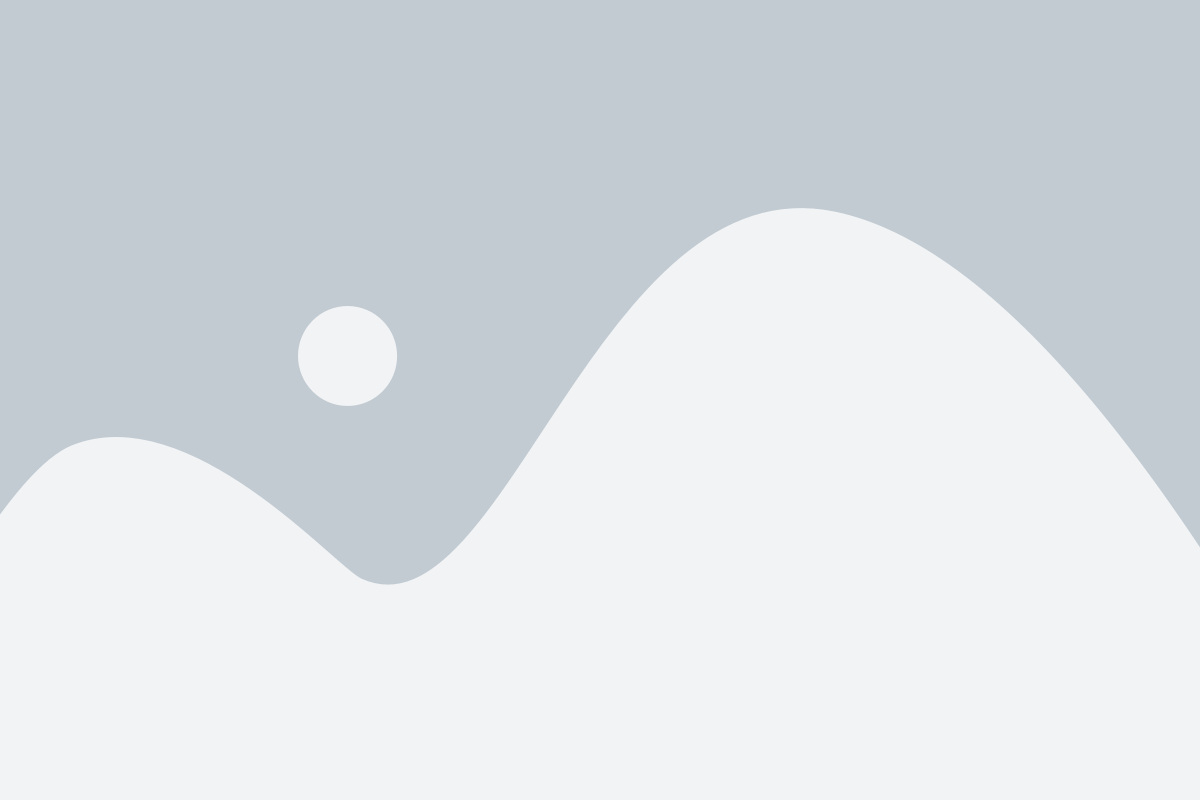
Pipe Induction Heating
Pipe induction heating is used to heat pipes quickly and uniformly for various industrial applications. The process involves placing the pipe inside an induction coil, which generates an alternating magnetic field. The magnetic field heats up the pipe, allowing it to be bent, welded or annealed without damaging the surrounding components.
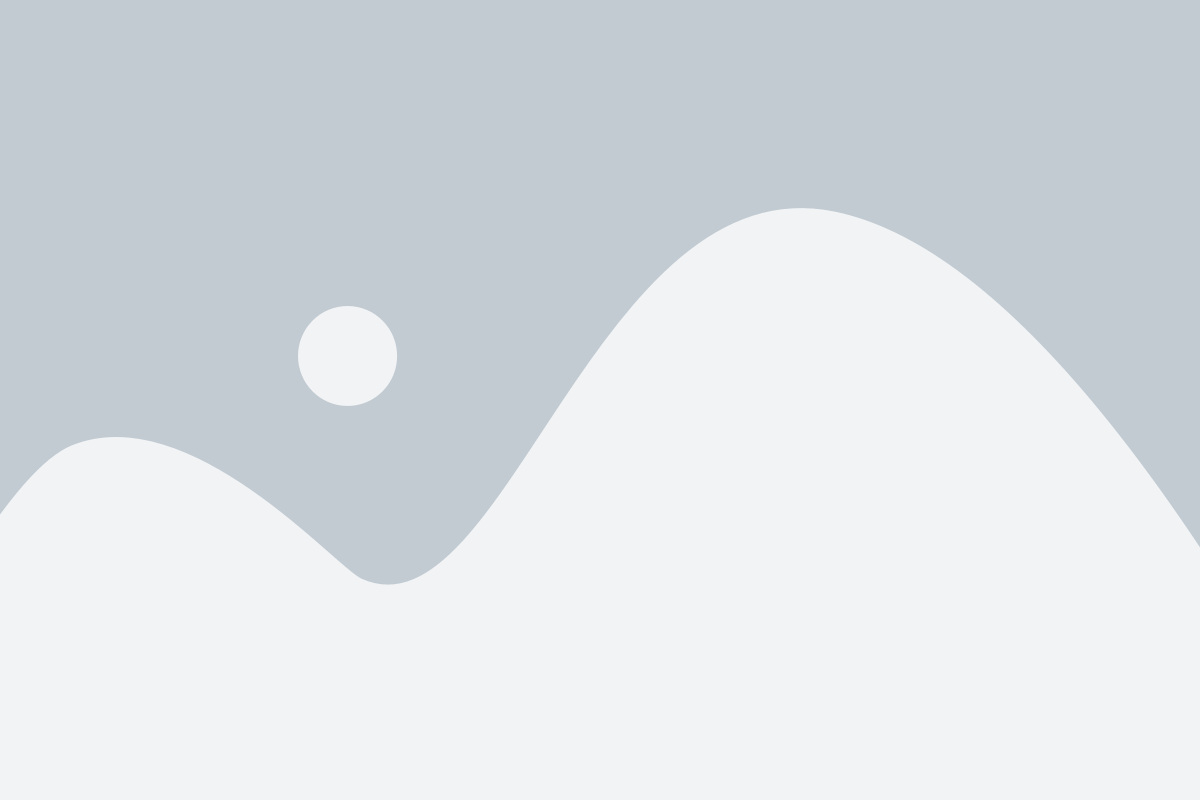
Induction Heater for Heat Sink
Heat sinks are commonly used in electronic devices to dissipate heat generated by electronic components such as processors and graphics cards. An induction heater can be used to heat the heat sink quickly and evenly, allowing it to expand and be easily removed from the device for maintenance or replacement. This process can be done without damaging the delicate components of the device.
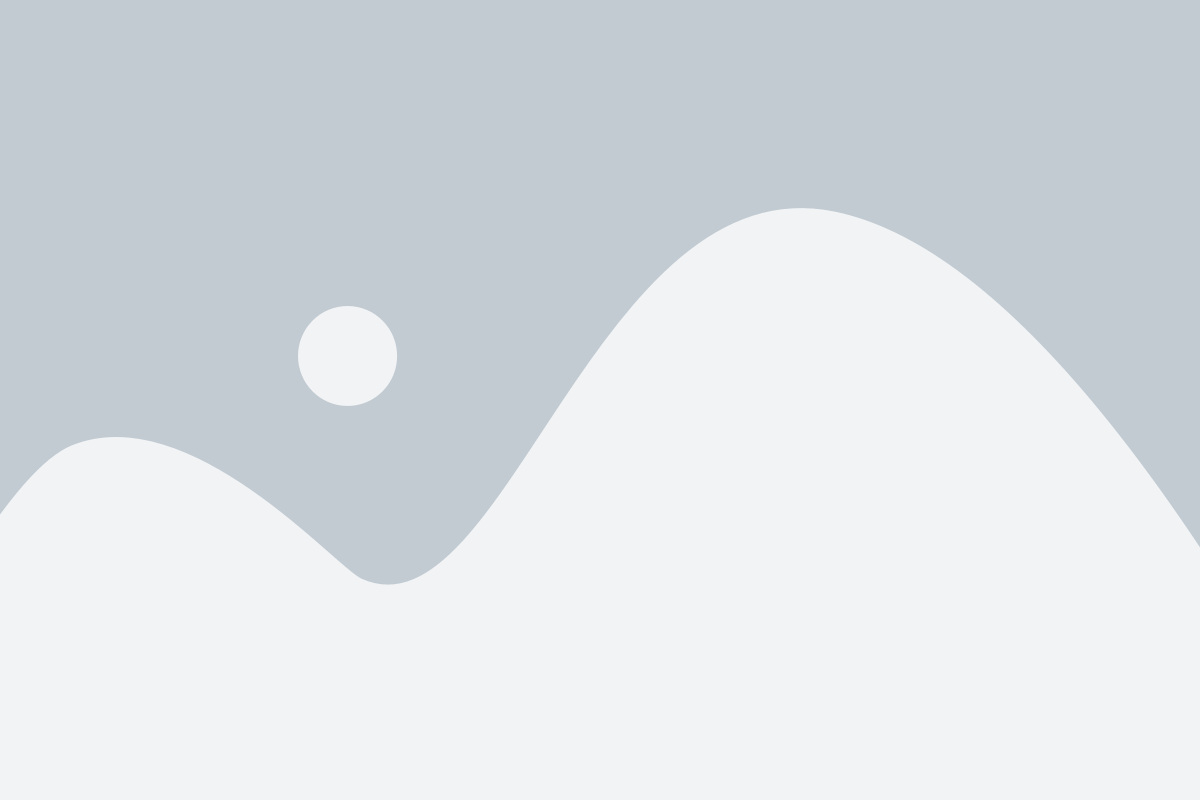
Induction Heater for Valves
Valves are used in various industrial processes to control the flow of fluids or gases. The removal and maintenance of valves require precise fitting and alignment. An induction heater can be used to expand the valve body, making it easier to remove from pipes or vessels. The process ensures consistent quality and performance, reducing the risk of leaks and other issues.
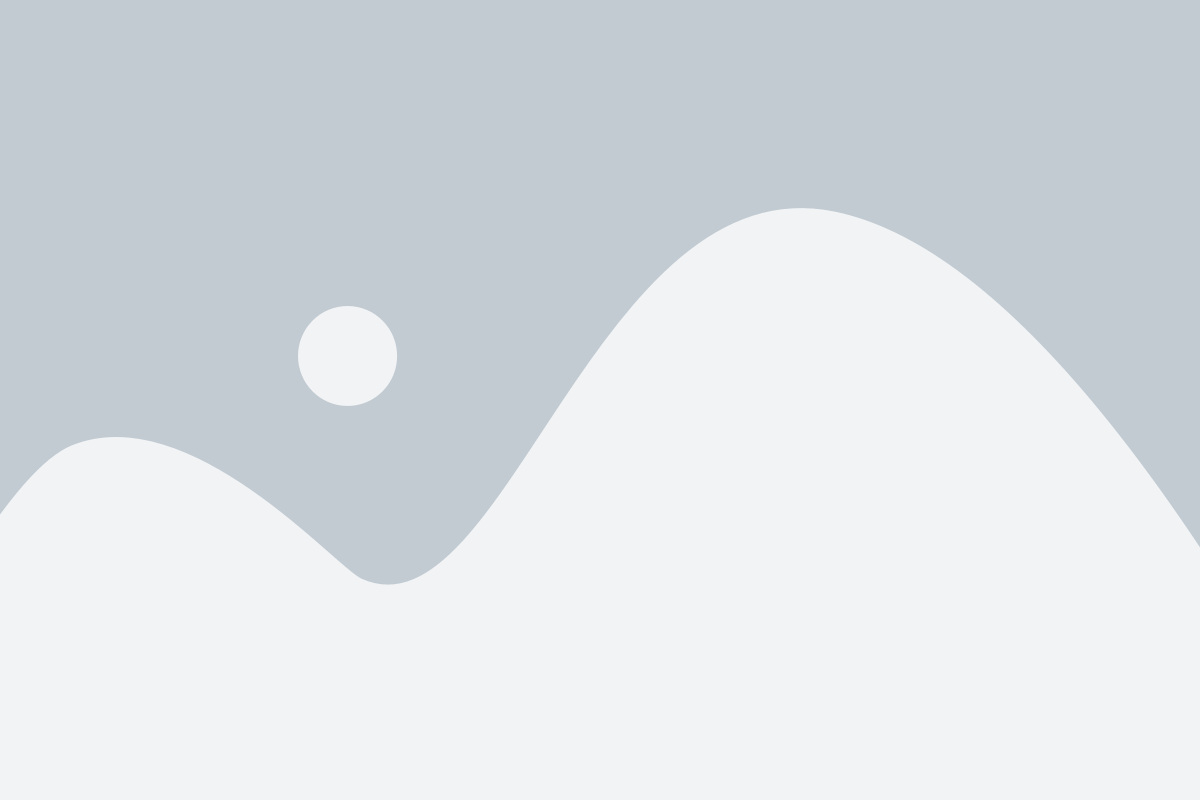
Transformer Induction
Transformers are widely used in power transmission and distribution systems. Induction heating can be used to remove transformer components such as bushings, coils, and cores. The process ensures fast, efficient, and safe installation and maintenance of transformers, reducing downtime and improving reliability.
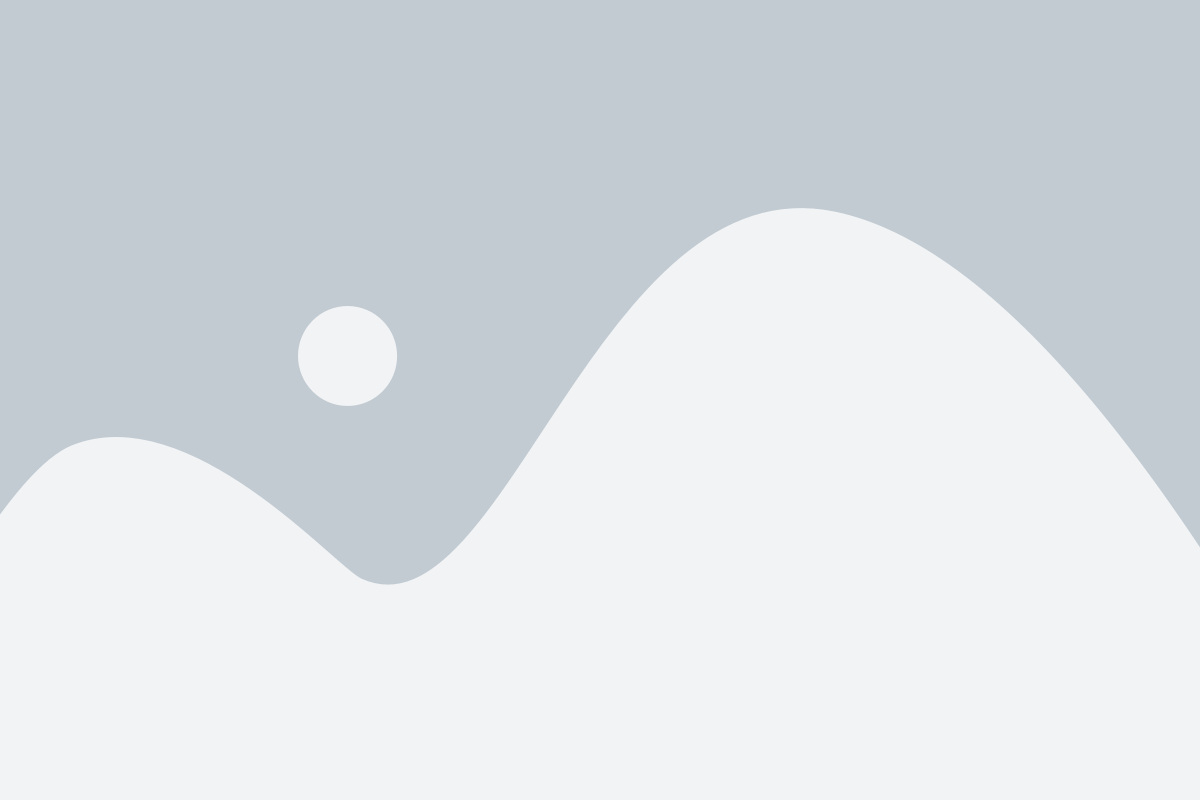
Induction Heater for Spindles
Spindles are used in various industries for precision machining and drilling. An induction heater can be used to heat up the spindle to expand it, making it easier to remove it onto the machine. This ensures accurate alignment and smooth operation of the machine, reducing the risk of errors and defects.
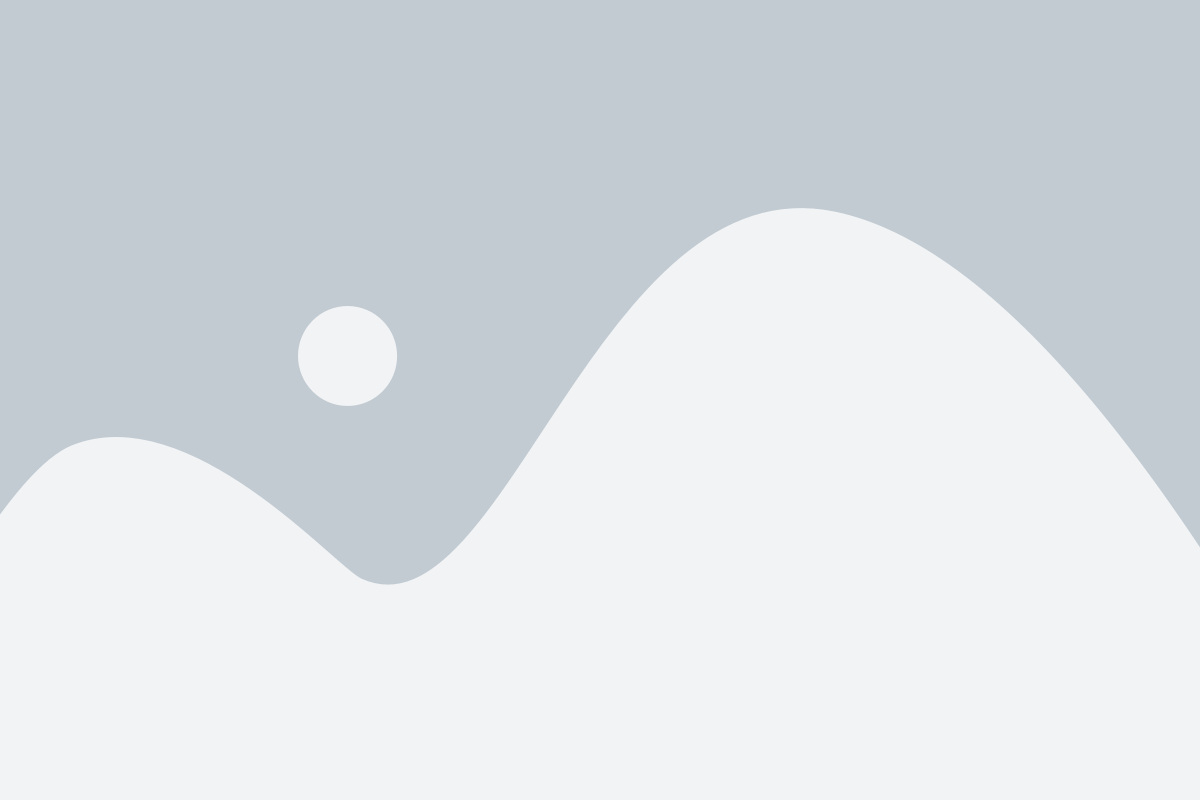
Induction Pump
Pumps can have many different types of components that need to be dismounted, including bearings, impellers, shafts, and seals. Using an induction heater allows for precise and targeted heating of these components, which can reduce the risk of damage during the disassembly process. An induction heater is often used for the dismounting of pumps because it can efficiently heat up specific components, such as bearings or shafts, to a temperature that will cause them to expand and loosen their grip on other parts. This makes it easier to disassemble the pump without damaging the components or the pump itself.
Induction Heaters Offered by GM Industries
For more information on any of our high quality products or getting accurate prices contact GM Industries at
Call Us
+(91)-9820533489 / 7738562224
Enquiry Form
Submit
Frequently Asked Questions
Industrial induction heaters can be used to dismount a wide range of metallic components, including bearings, gears, couplings, valves, and shafts.
Compared to traditional methods such as hammering, hydraulic pressing, or heating with a torch, an industrial induction heater is faster, more precise, and safer. It can also dismount components that are difficult to access or have complex shapes.
Operators should follow safety guidelines, wear protective equipment, and avoid touching the heated component or the coil. The device should be properly grounded and isolated from water and flammable materials.
The heating time depends on the size, shape, and material of the component, as well as the power and frequency of the device. Typically, heating times range from a few seconds to several minutes.
The size and shape of the component affect the positioning and movement of the coil, the heating time, and a
The size and shape of the component affect the positioning and movement of the coil, the heating time, and the force required to dismount it. Components with complex shapes or tight tolerances may require specialized coils or adapters.
the force required to dismount it. Components with complex shapes or tight tolerances may require specialized coils or adapters.
Industrial induction heaters can heat up most metallic materials, including steel, aluminium, brass, and copper. However, some materials may require higher or lower frequencies, powers, or heating times.
The temperature control system on an industrial induction heater uses sensors to measure the temperature of the component and adjusts the power output of the device to maintain a constant temperature or heating rate.
Industrial induction heaters should not be used in hazardous environments, such as those with explosive gases, dust, or flammable liquids. They should also be used with caution in wet or humid conditions.
Operators should have basic knowledge of the principles and safety guidelines of industrial induction heating. Specialized training may be required for specific applications or devices.
Proper use of an industrial induction heater can prolong the lifespan of the component by reducing the risk of damage or wear caused by traditional dismounting methods.
Yes, an industrial induction heater can be used on components that are still in operation, provided that the heating process does not cause any damage or interference with the operation of the component.
An industrial induction heater generates heat by inducing an electric current in the component being heated, which can lead to the emission of electromagnetic fields. However, proper shielding and grounding can minimize any potential effects on the surrounding environment.
Yes, an industrial induction heater can be used for components with complex shapes or designs, as the heating process is localized and can be tailored to specific areas of the component.
An industrial induction heater can heat specific areas of a component without affecting the surrounding areas, making it ideal for components with tight tolerances.
How does an industrial induction heater compare in terms of cost-effectiveness with other dismounting methods?
Regular maintenance and cleaning are required for an industrial induction heater, including cleaning the coils and ensuring proper grounding and insulation. It is also important to regularly check for any signs of wear or damage to the heater.
There are some limitations to using an industrial induction heater for dismounting processes, such as the size and shape of the component, the material of the component, and the potential interference with surrounding equipment. Additionally, the process can be more difficult to control for components with varying thicknesses or shapes.