Induction Annealing
What is Annealing?
Annealing is a process of heat treatment that is used to alter the physical and chemical properties of a material. The main objective of annealing is to increase the ductility of a material while reducing its hardness, making it more workable. The process of annealing involves heating a material to a specific temperature and then cooling it slowly. The temperature to which the material is heated, as well as the rate at which it is cooled, depend on the type of material being annealed and the desired outcome.
Annealing is commonly used in the production of metals, such as steel, copper, and aluminium. It is used to relieve internal stresses in the material that can result from previous processing steps, such as rolling or forging. It can also be used to refine the grain structure of the material, making it more uniform and improving its overall properties. In addition to its use in metalworking, annealing is also used in the production of glass, where it can help to reduce internal stresses and improve the clarity of the finished product. It is also used in the semiconductor industry, where it is used to relieve stresses that can occur during the manufacturing process.
The most common method used for annealing is full annealing, which involves heating the material to a temperature above its critical point and then allowing it to cool slowly in the furnace. Induction heating is becoming increasingly popular as a method for annealing because it offers several advantages over traditional furnace heating.
Why is the Induction Heater used for Annealing Processes?
Induction heaters are commonly used for annealing processes because they offer fast and efficient heating, precise temperature control, cleanliness, and controllability. Induction heating generates heat directly within the material being treated, reducing the overall annealing cycle time. It allows for specific temperature ranges, ensuring the material is heated to the correct temperature for the required amount of time. Induction heating is also a clean and environmentally friendly process that produces no emissions or waste. Additionally, it provides consistent and repeatable annealing results, making it a preferred choice for industries that require high-quality materials with consistent properties.
Introduction to Industrial Induction Heater for Annealing
Annealing is a process that involves heating a material to a specific temperature and then cooling it slowly to alter its physical and chemical properties. Industrial induction heaters are extensively used for annealing processes in various industries, including manufacturing, automotive, and aerospace. The use of industrial induction heaters for annealing offers several advantages over traditional heating methods, including fast and efficient heating, precise temperature control, cleanliness, and controllability. This results in reduced annealing cycle times, higher-quality materials, and increased productivity. GM Industries is a major player in providing industrial induction heaters for annealing processes in various industries. Their products offer fast and efficient heating, precise temperature control, cleanliness, and controllability, resulting in reduced annealing cycle times, higher-quality materials, and increased productivity. With their focus on customer satisfaction and quality products and services, GM Industries is a trusted supplier of industrial induction heaters for annealing.
Advantages of Using an Industrial Induction Heater for Annealing
Using an industrial induction heater for annealing offers several advantages over traditional heating methods. Here are some of the benefits:
Fast and Efficient Heating
Induction heating generates heat directly within the material being treated, resulting in faster and more efficient heating compared to traditional methods.
Precise Temperature Control:
Industrial induction heaters offer precise temperature control, allowing for specific temperature ranges and ensuring the material is heated to the correct temperature for the required amount of time.
Cleanliness
Induction heating is a clean and environmentally friendly process that produces no emissions or waste, making it a preferred choice for industries that require environmentally friendly processes.
Controllability
Industrial induction heaters offer controllability, allowing operators to adjust the heating process as required to ensure optimal results.
Consistent and Repeatable Results
Induction heating provides consistent and repeatable annealing results, making it a preferred choice for industries that require high-quality materials with consistent properties.
Reduced Annealing Cycle Times
The fast and efficient heating provided by industrial induction heaters results in reduced annealing cycle times, increasing productivity and reducing costs.
In summary, using an industrial induction heater for annealing offers several advantages over traditional heating methods, including faster and more efficient heating, precise temperature control, cleanliness, controllability, consistent and repeatable results, and reduced annealing cycle times.
Induction Heater for Various Annealing Process
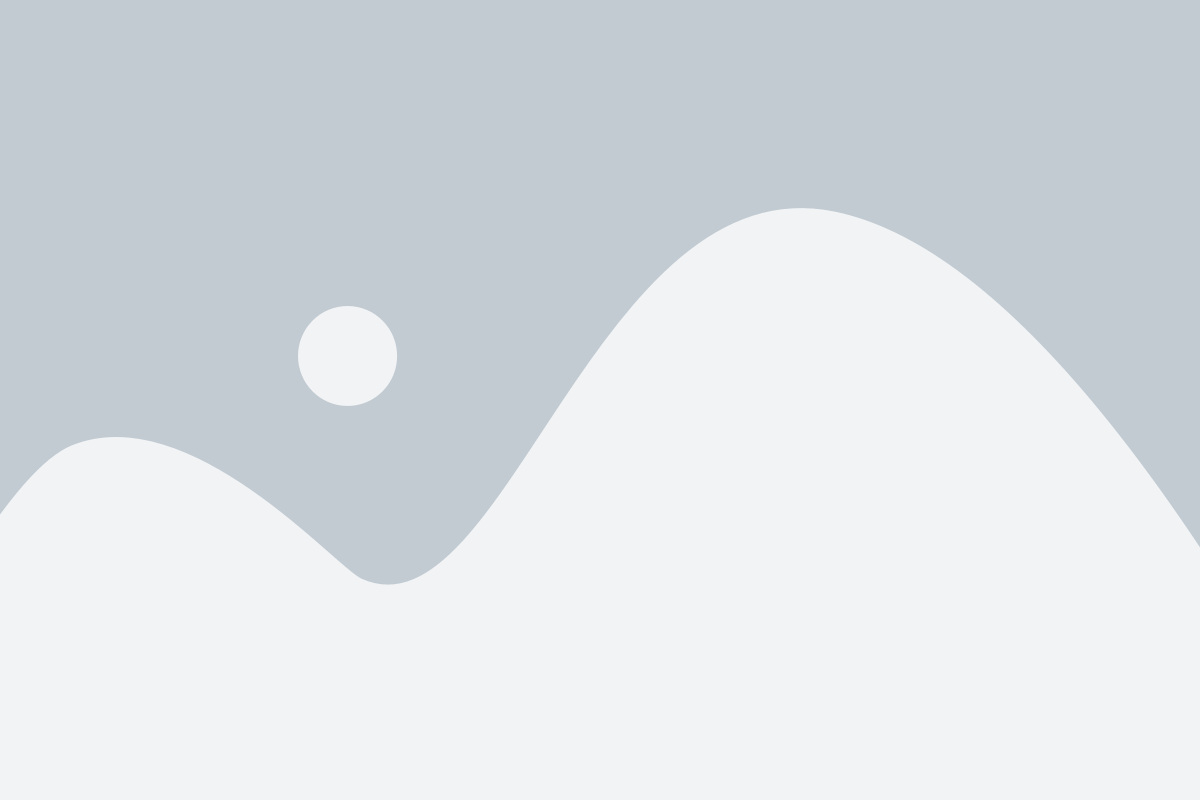
Wire Induction
Wire annealing is the process of heating and cooling metal wire to change its physical and chemical properties, making it more malleable and easier to work with. To anneal wire, it is first wound into a coil and placed in an induction heater. The induction heater generates an electromagnetic field that heats the wire coil quickly and uniformly, allowing it to reach the desired annealing temperature without overheating or damaging the wire.
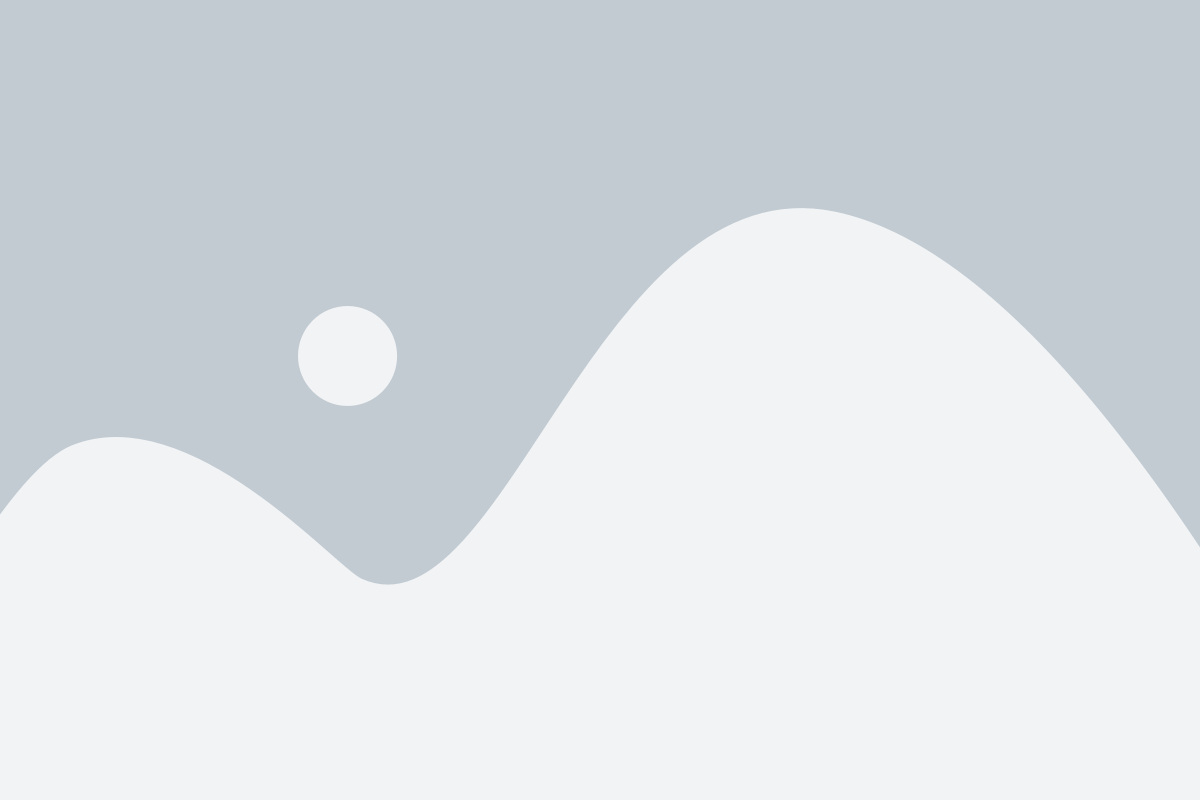
Induction Tube
Tube annealing is a heat treatment process that improves the ductility and machinability of metal tubes. Induction heaters are commonly used for this process because they can heat the tube quickly and uniformly, allowing for precise temperature control and consistent results. The tube is placed in the induction heater, and the heat generated by the electromagnetic field causes the metal to soften and become more malleable.
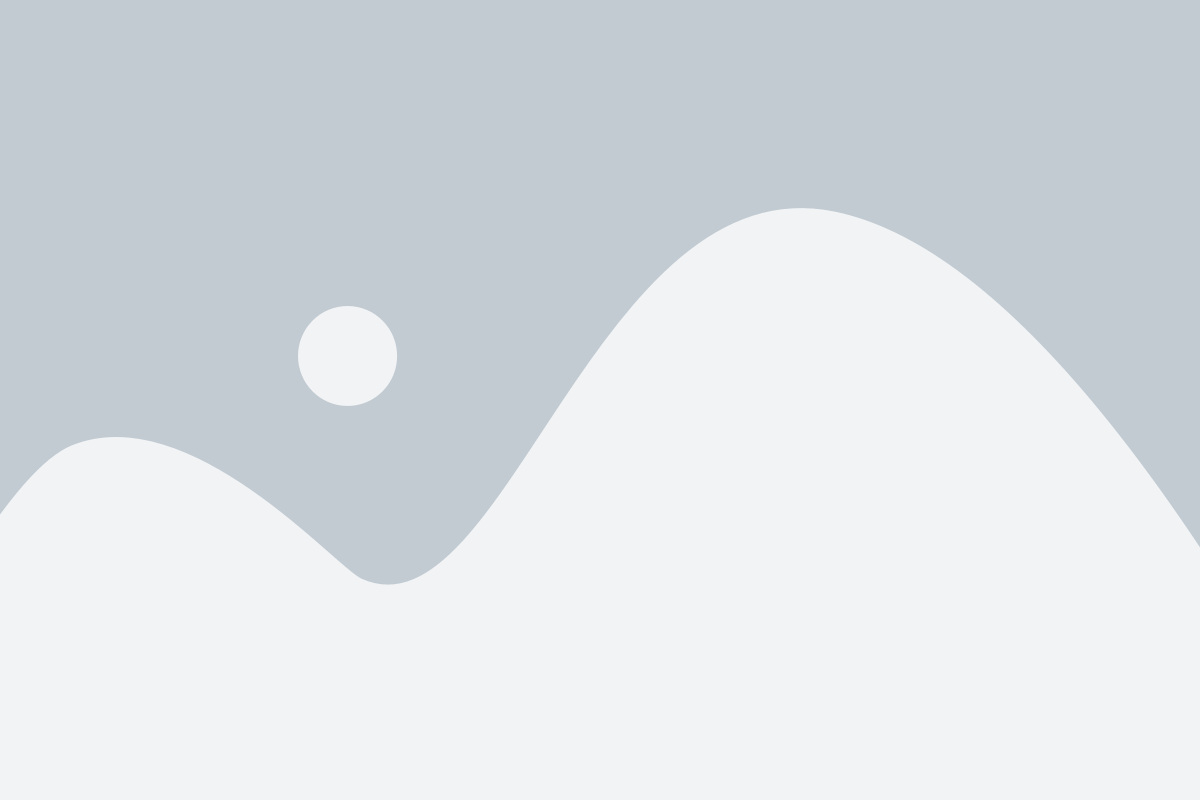
Pipe Induction
Pipe annealing is a similar process to tube annealing, but is used for larger diameter metal pipes. The pipe is placed in the induction heater and heated uniformly to the desired annealing temperature, which improves its ductility and makes it easier to work with. Induction heaters are preferred for this process because they can heat the pipe quickly and evenly, without the risk of overheating or damaging the metal. Induction Heater for Annealing Steel Strips: Annealing steel strips involves heating and cooling the metal to improve its ductility and reduce its hardness. Induction heaters are ideal for this process because they can heat the steel strips quickly and uniformly, resulting in consistent results. The steel strips are placed in the induction heater and heated to the desired temperature, allowing for controlled annealing of the metal.
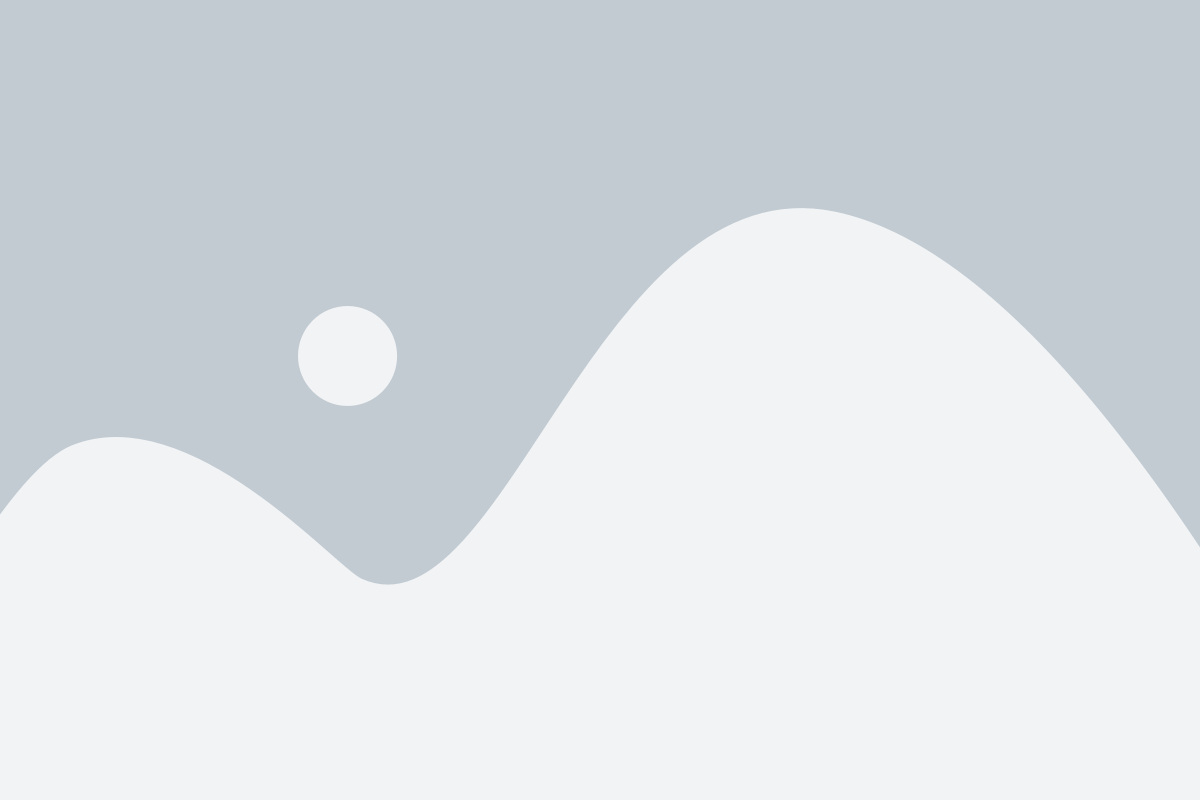
Induction Heating Coil
Induction heaters are commonly used for annealing metal coils, which are used in a variety of industries. The metal coil is placed in the induction heater, which heats the coil quickly and uniformly, resulting in controlled annealing of the metal. Induction heaters are preferred for this process because they can heat the metal to the desired temperature quickly and precisely, without the risk of overheating or damaging the coil.
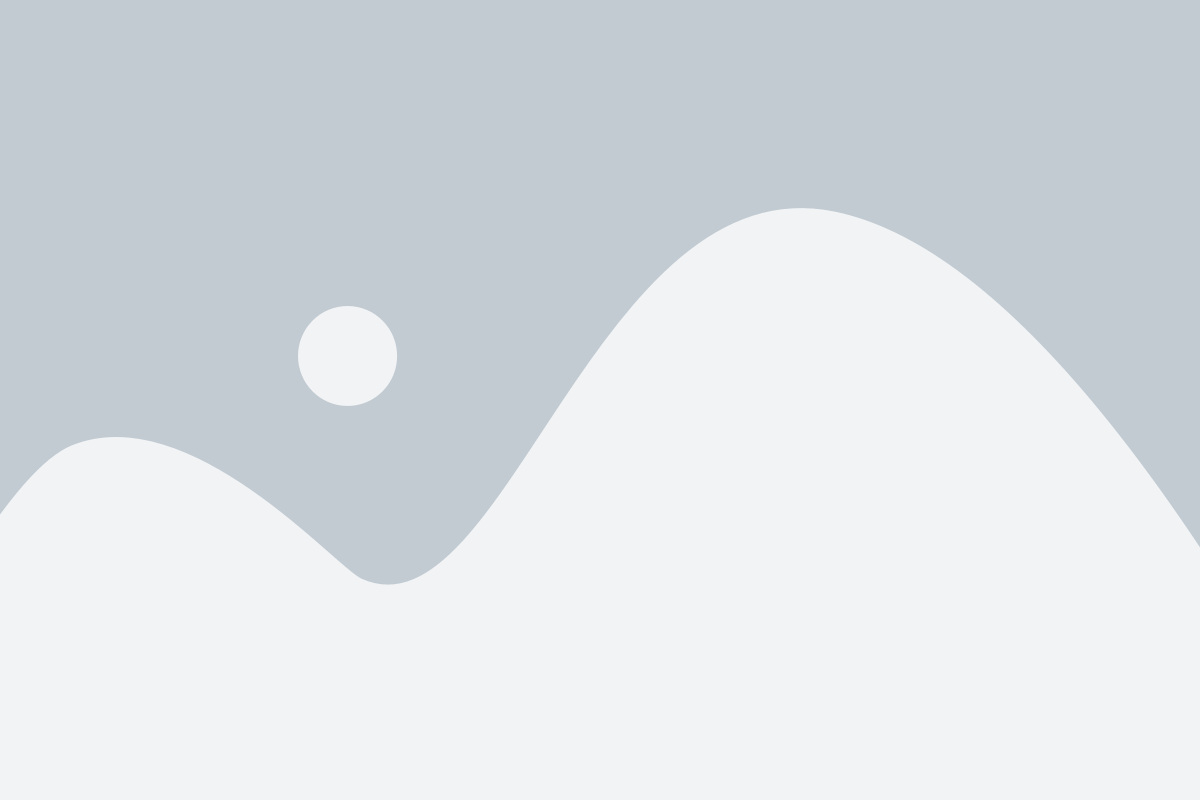
Induction Heater for Annealing Sheet Metal
Sheet metal annealing is a process that involves heating and cooling the metal to improve its ductility and reduce its hardness. Induction heaters are ideal for this process because they can heat the sheet metal quickly and uniformly, resulting in consistent results. The sheet metal is placed in the induction heater and heated to the desired temperature, allowing for controlled annealing of the metal.
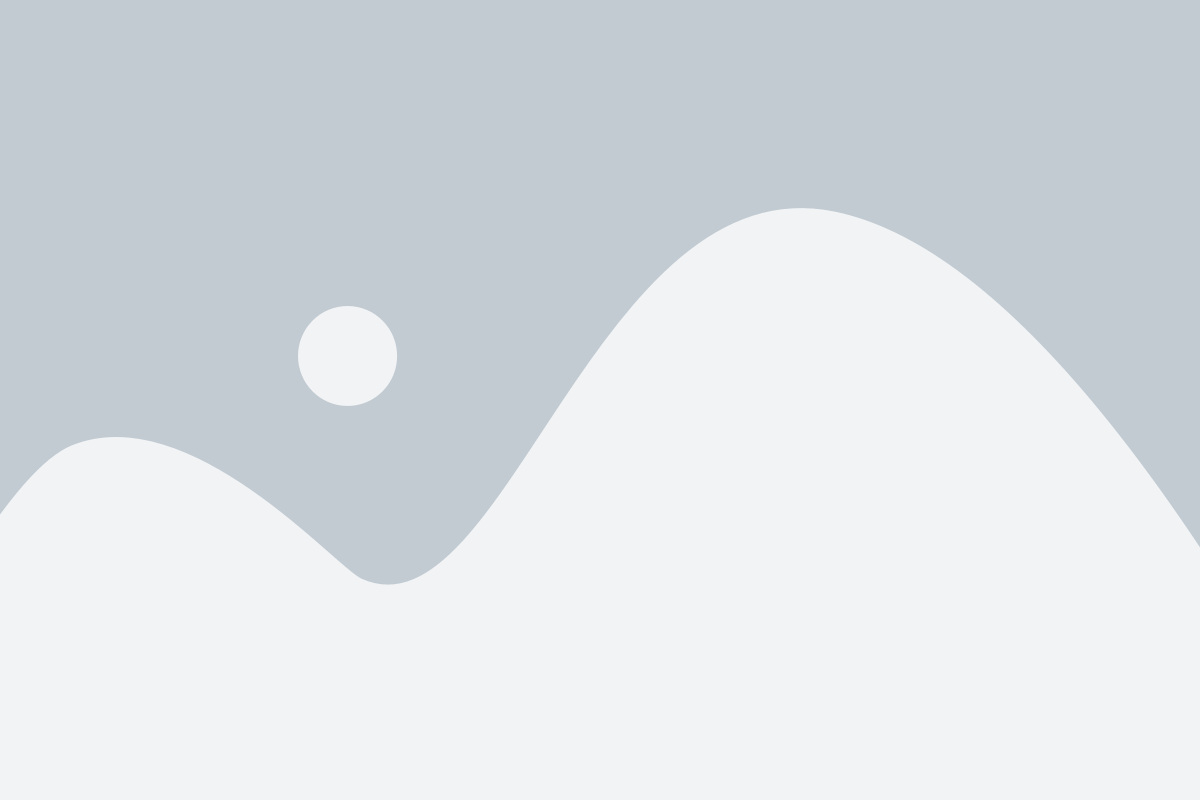
Induction Heater for Annealing Fasteners
Annealing fasteners involves heating and cooling metal screws, bolts, and nuts to improve their strength and durability. Induction heaters are preferred for this process because they can heat the fasteners quickly and uniformly, resulting in consistent results. The fasteners are placed in the induction heater and heated to the desired temperature, allowing for controlled annealing of the metal.
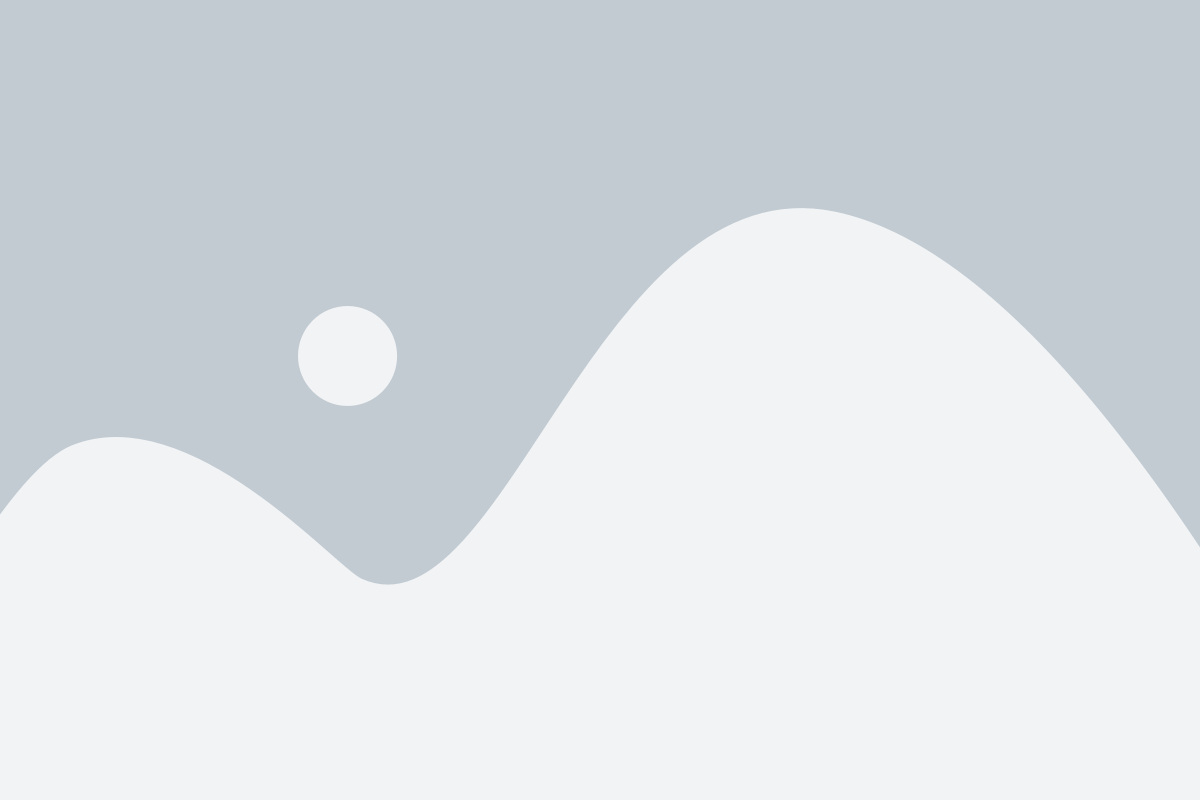
Induction Heater for Annealing Turbine Blades
Turbine blades are subject to high levels of stress and require heat treatment to improve their strength and durability. Induction heaters are ideal for annealing turbine blades because they can heat the blades quickly and uniformly, resulting in consistent results. The turbine blades are placed in the induction heater and heated to the desired temperature, allowing for controlled annealing of the metal.
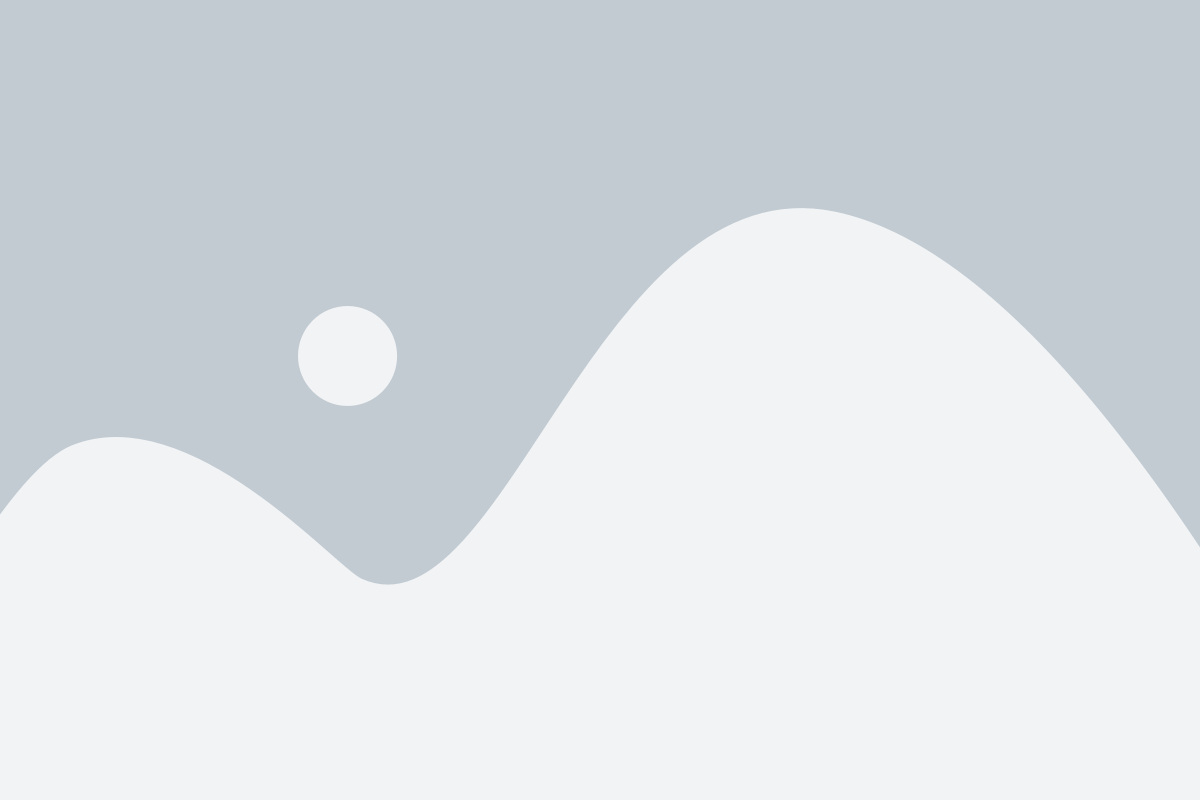
Induction Heater for Annealing Transformer Cores
Transformer cores are made of metal and require heat treatment to improve their magnetic properties. Induction heaters are preferred for annealing transformer cores because they can heat the metal quickly and uniformly, resulting in consistent results. The transformer core is placed in the induction heater and heated to the desired temperature, allowing for controlled annealing of the metal.
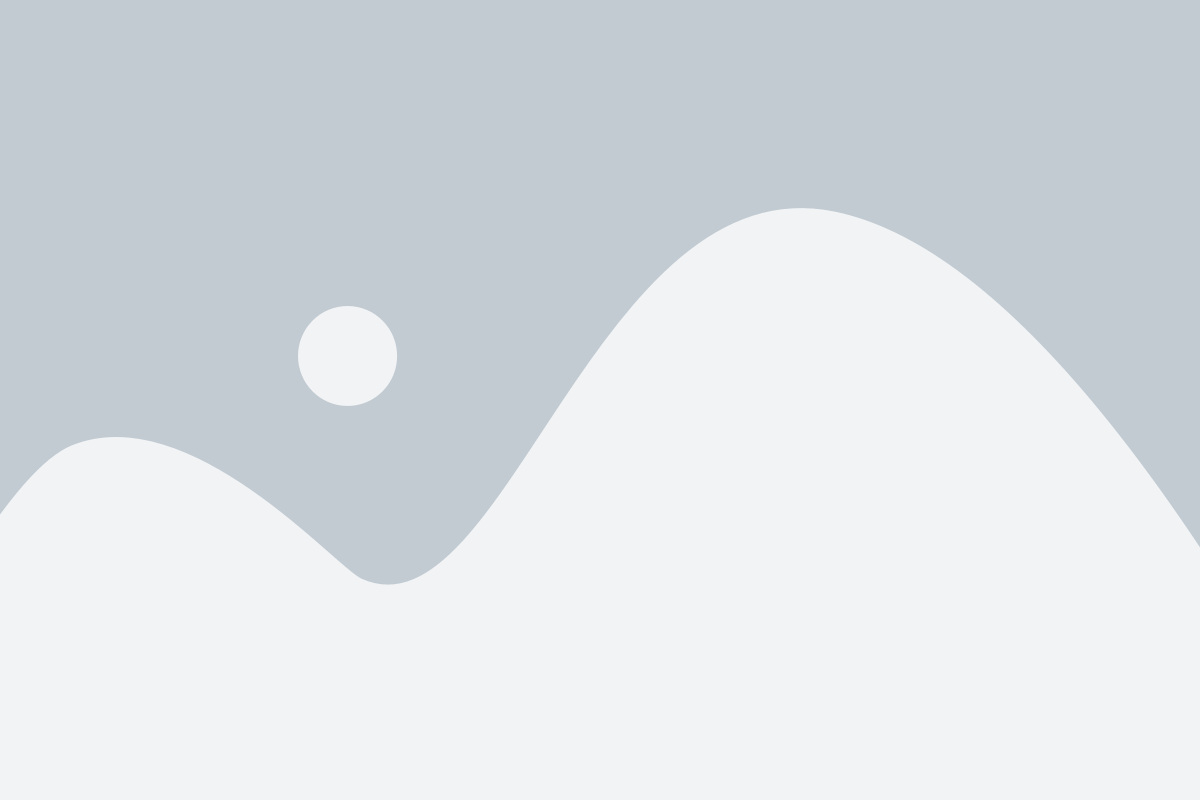
Induction Motor Parts
Motor parts are essential components of various machinery and equipment. Annealing of motor parts is crucial to reduce internal stress and increase the material’s ductility. Induction heaters are used in annealing motor parts due to their ability to heat the material uniformly and quickly. This reduces the chances of distortion and material damage, resulting in a longer lifespan of the motor part. Induction heating is important for annealing motor parts because it ensures precise and consistent heat treatment, which is necessary for optimal motor performance.
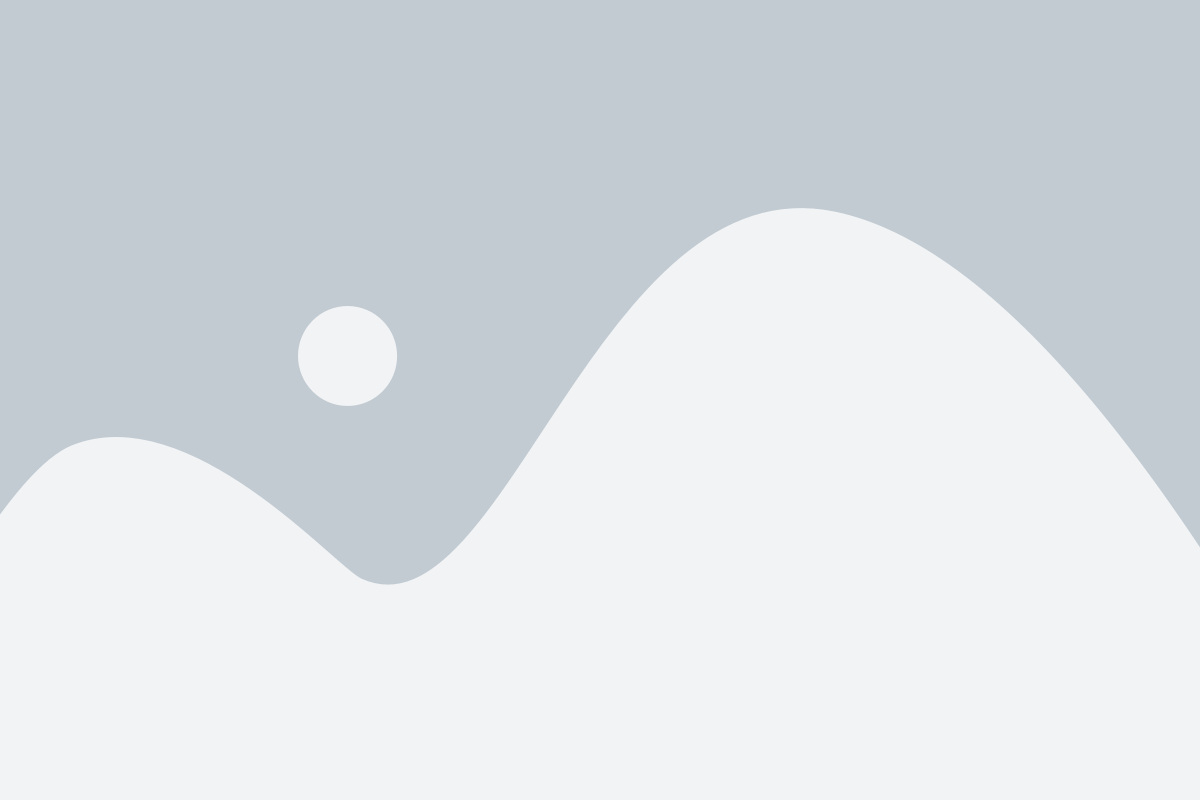
Spring Induction
Springs are used in various applications and industries, such as automotive and aerospace. Annealing of springs is essential to increase their ductility and reduce the risk of failure due to fatigue. Induction heaters are used in annealing springs due to their ability to heat the material quickly and uniformly, resulting in a more effective heat treatment process. The use of induction heaters ensures that the material properties are not compromised, leading to a longer lifespan and improved performance of the spring.
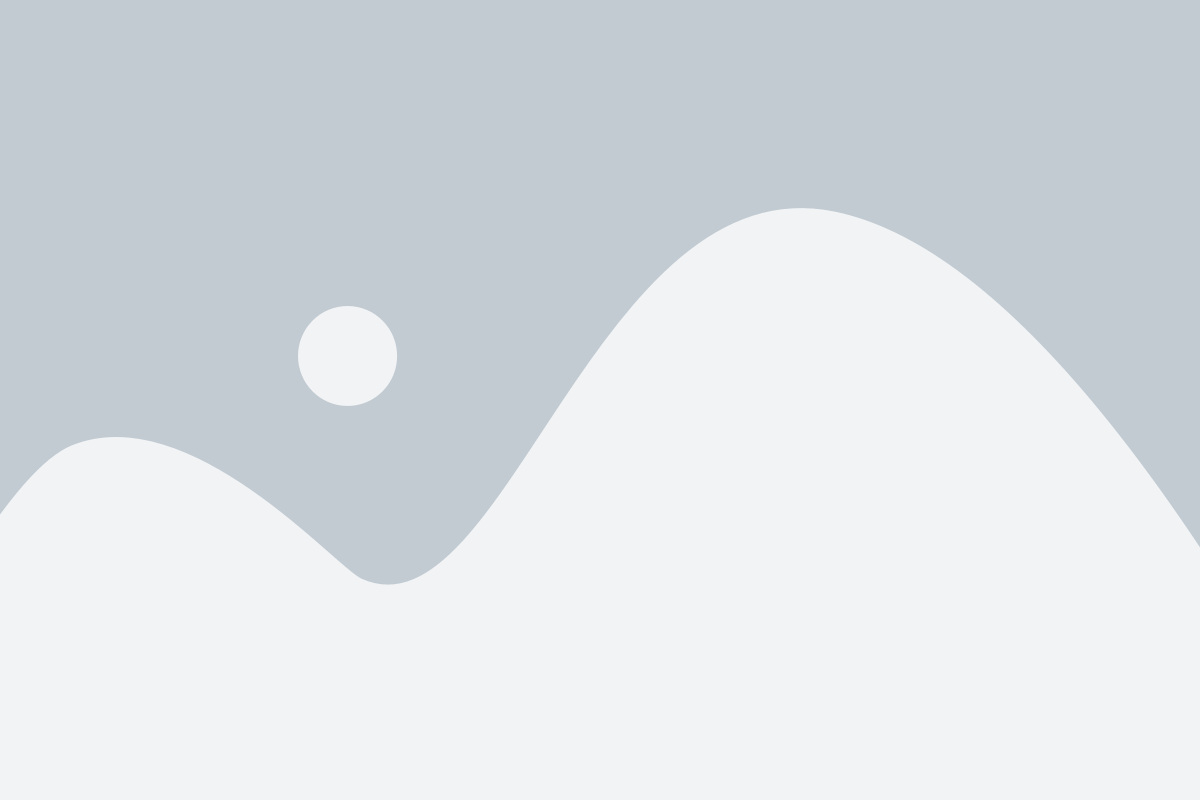
Induction Heating Bearings
Bearings are essential components of various machinery and equipment, such as automobiles, aircraft, and industrial machines. Annealing of bearings is essential to improve their wear resistance, reduce internal stress, and increase ductility. Induction heaters are used in annealing bearings due to their ability to heat the material uniformly and quickly, resulting in a more effective heat treatment process. The use of induction heaters ensures that the bearings are annealed with precision, resulting in improved performance and a longer lifespan.
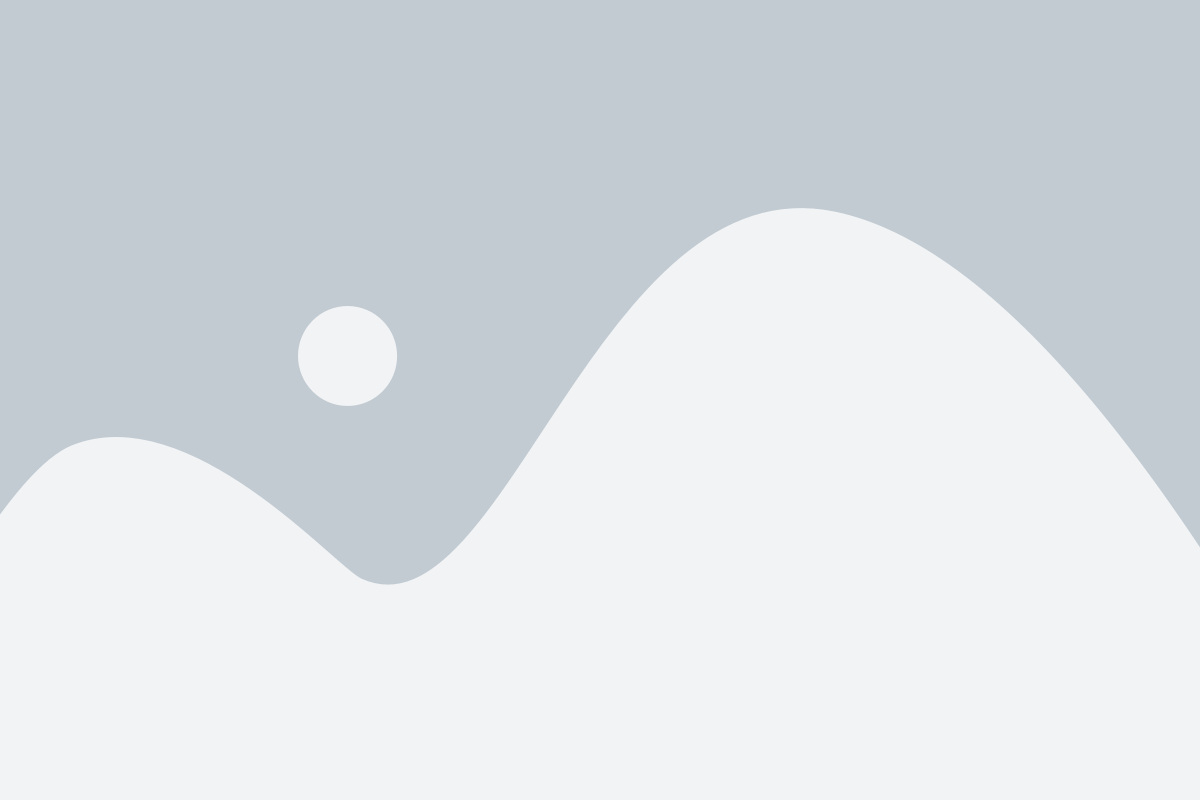
Induction Tank
Tanks are used in various industries, such as chemical and pharmaceutical, for storage and transportation purposes. Annealing of tanks is essential to improve their corrosion resistance and durability. Induction heaters are used in annealing tanks due to their ability to heat the material uniformly and quickly, resulting in a more effective heat treatment process. The use of induction heaters for annealing tanks is crucial for ensuring their longevity and preventing material damage.
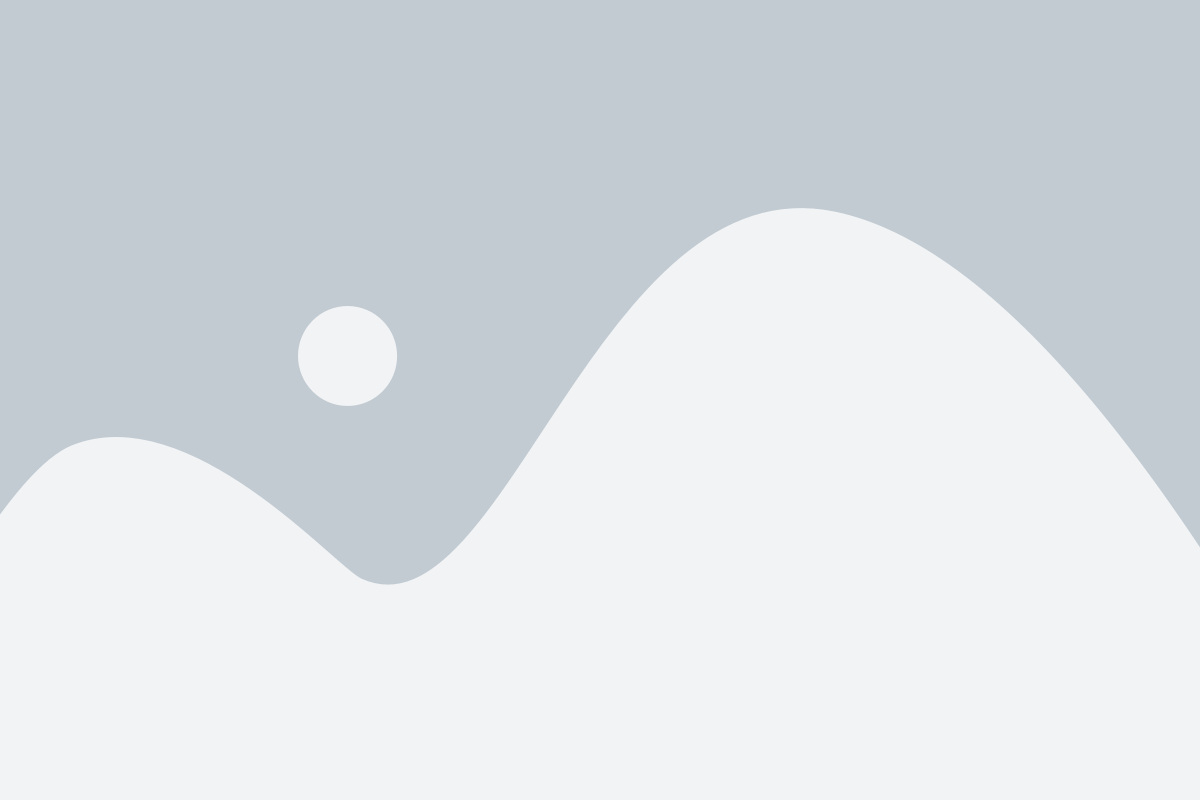
Induction heater for annealing shafts
Shafts are essential components of various machinery and equipment. Annealing of shafts is necessary to improve their wear resistance, reduce internal stress, and increase their ductility. Induction heaters are used in annealing shafts due to their ability to heat the material uniformly and quickly, resulting in a more effective heat treatment process. The use of induction heaters ensures that the shafts are annealed with precision, resulting in improved performance and a longer lifespan.
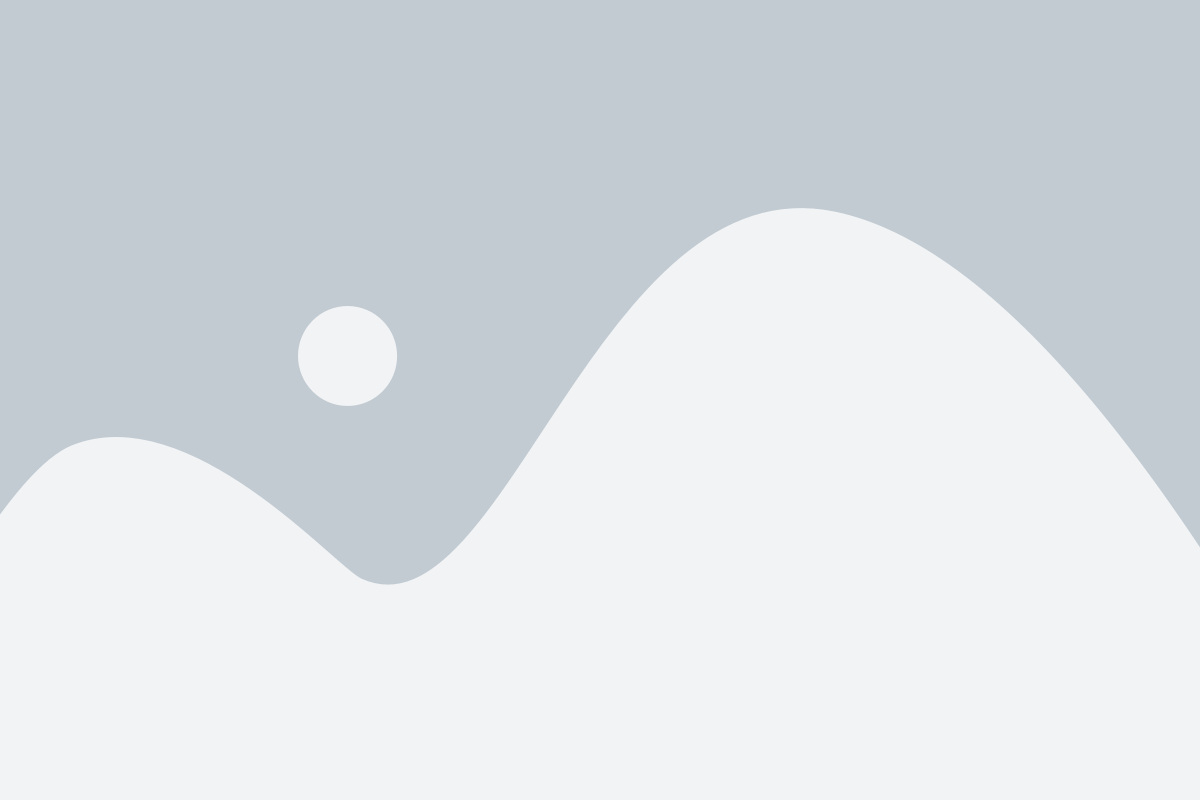
Induction Valve
Valves are crucial components in various industries, such as oil and gas and chemical processing. Annealing of valves is necessary to improve their wear resistance, reduce internal stress, and increase their ductility. Induction heaters are used in annealing valves due to their ability to heat the material uniformly and quickly, resulting in a more effective heat treatment process. The use of induction heaters for annealing valves ensures that the material properties are not compromised, leading to improved performance and a longer lifespan.
Induction Heaters Offered by GM Industries
For more information on any of our high quality products or getting accurate prices contact GM Industries at
Call Us
+(91)-9820533489 / 7738562224
Enquiry Form
Submit
Frequently Asked Questions
An induction heater is used to heat metal components to a specific temperature for annealing, which involves heating and cooling metal to improve its strength and durability.
An induction heater uses electromagnetic induction to heat metal components. An alternating current is passed through a coil, creating a magnetic field that induces eddy currents in the metal, causing it to heat up.
A wide range of metal components can be annealed using an induction heater, including wire, tube, pipe, steel strips, sheet metal, fasteners, turbine blades, transformer cores, motor parts, springs, bearings, gears, tanks, shafts, and valves.
No, induction heating is a safe and controlled method of heating metal components. The heating process can be precisely controlled to prevent damage to the metal.
The length of time required to anneal a metal component depends on various factors such as the size and thickness of the component and the desired temperature. However, induction heating provides faster heating compared to other methods.
The temperature range of an induction heater for annealing typically ranges from 200°C to 1200°C.
Yes, an induction heater can be programmed to carry out multiple annealing processes for various components.
The temperature of the metal component is monitored using thermocouples, which are placed on the surface of the component. The data from the thermocouples is used to control the heating process.
Yes, induction heaters can be used for annealing large metal components such as tanks and shafts.
No, induction heaters are specifically designed for annealing metal components.
Induction heaters are highly energy-efficient, using up to 90% less energy compared to other heating methods.
Yes, induction heaters can be used for continuous annealing processes in industries such as automotive and aerospace.
Yes, induction heaters are easy to operate and require minimal training to use.
Induction heaters have minimal maintenance requirements and typically only require periodic checks and inspections.
How does an industrial induction heater compare in terms of cost-effectiveness with other dismounting methods?
The cost of an induction heater for annealing varies depending on the size, features, and specifications of the equipment.
Yes, induction heaters can be customized to meet specific annealing process requirements.
Induction heaters typically include safety features such as overheat protection, overcurrent protection, and insulation monitoring.
Yes, induction heating is an environmentally friendly heating method that emits no harmful gases or pollutants.
The size of the workpiece affects the annealing process in induction heating because larger workpieces require more power and longer heating times to reach the desired temperature.
Safety measures such as wearing heat-resistant gloves, using protective eyewear, and ensuring proper grounding and ventilation should be taken while using an induction heater for annealing processes.