Induction Forging
What is Forging?
Forging is a manufacturing process that involves shaping a metal or alloy using pressure or impact. It typically involves heating the material to a high temperature and then applying force to shape it into a specific form or design. There are several different methods of forging, including open-die forging, closed-die forging, and ring rolling. Open-die forging involves shaping the material between two flat or contoured dies, while closed-die forging uses a set of dies that are designed to shape the material into a specific form. Ring rolling involves shaping a ring-shaped piece of material by rotating it and applying pressure with a set of rollers.
Forging is commonly used in the production of metal parts for various industries, including aerospace, automotive, construction, and manufacturing. It is often preferred over other manufacturing processes because it can produce parts with superior strength, durability, and reliability.
The most common method used for forging is closed-die forging. In closed-die forging, the metal is placed between two dies that are designed to shape it into the desired form. The dies are typically made from steel and are machined to precise specifications. Induction heating is a popular method for heating the metal prior to forging. This involves using an electromagnetic field to heat the metal without making direct contact with it. Induction heating is often preferred over other heating methods because it is fast, efficient, and produces uniform heating. It also allows for precise temperature control, which is important in ensuring the quality and consistency of the forged parts.
Why is the Induction Heater used for Forging Processes?
Induction heater is often used in forging processes because it offers several advantages over other heating methods. Initially, induction heating is a fast and efficient heating method that can quickly heat the metal to the required temperature for forging, reducing heating time and energy consumption. Furthermore, induction heating is a clean heating method that does not produce any harmful emissions, making it a more environmentally friendly option. Thirdly, induction heating provides precise control over the heating process, allowing for accurate temperature control and reducing the risk of overheating or under heating the metal. Lastly, induction heating is a flexible method that can be used for a wide range of metals and forging applications, making it a versatile tool for forging processes.
Introduction to Industrial Induction Heater for Forging
An industrial induction heater for forging is a specialized heating system designed to rapidly and efficiently heat metal to the required temperature for forging processes. Induction heating is a method of heating metal using electromagnetic induction, which involves the use of a high-frequency alternating current to create an electromagnetic field that induces eddy currents in the metal. These eddy currents cause the metal to heat up rapidly and uniformly, allowing it to be quickly brought to the desired forging temperature. Industrial induction heaters for forging typically consist of a power supply unit, which generates the high-frequency alternating current, and an induction coil, which is used to transfer the energy from the power supply to the metal being heated. The induction coil is typically designed to fit around the metal being heated, allowing for efficient energy transfer and minimizing heat loss.
Industrial induction heaters for forging are commonly used in a range of applications, including the production of automotive parts, aerospace components, and other metalworking applications. GM Industries is a leading provider of industrial induction heaters for forging, with a reputation for delivering high-quality and reliable heating systems. With years of experience in the industry, GM Industries has developed a deep understanding of the specific needs of forging processes and offers a wide range of induction heating solutions to meet these requirements.
Advantages of Using an Industrial Induction Heater for Forging
There are several benefits to using an industrial induction heater for forging:
Speed and Productivity
Induction heating is a fast and efficient heating method, allowing the metal to be rapidly brought to the desired temperature, reducing heating time and energy consumption.
Accuracy and Control
Induction heating provides precise temperature control, allowing for accurate and consistent heating of the metal. This minimizes the risk of overheating or under heating the metal and ensures that it is heated to the exact temperature required for the forging process.
Quality and Reliability
Induction heating provides uniform heating of the metal, resulting in high-quality forgings with consistent properties.
Versatility
Induction heating is a flexible method that can be used for a wide range of metals and forging applications, making it a versatile tool for metalworkers
Cost-effective
While the initial cost of an industrial induction heater may be higher than other heating methods, the efficiency and precision of induction heating can result in cost savings over time due to reduced energy consumption and increased productivity.
Reduced Labour Costs
Industrial induction heaters for forging are designed for automation, reducing the need for manual labour in the heating process. This not only increases efficiency but also reduces labour costs.
Longer Life of Heating Coils
Industrial induction heaters for forging are designed to have longer lives, reducing the need for frequent replacements and maintenance.
Space-saving
Induction heating systems are compact and can be easily integrated into existing production lines, saving valuable floor space.
Overall, the use of an industrial induction heater for forging offers numerous benefits, including speed and efficiency, precision and control, versatility, cleanliness and safety, quality and consistency, and cost-effectiveness.
Induction Heater for Various Forging Process
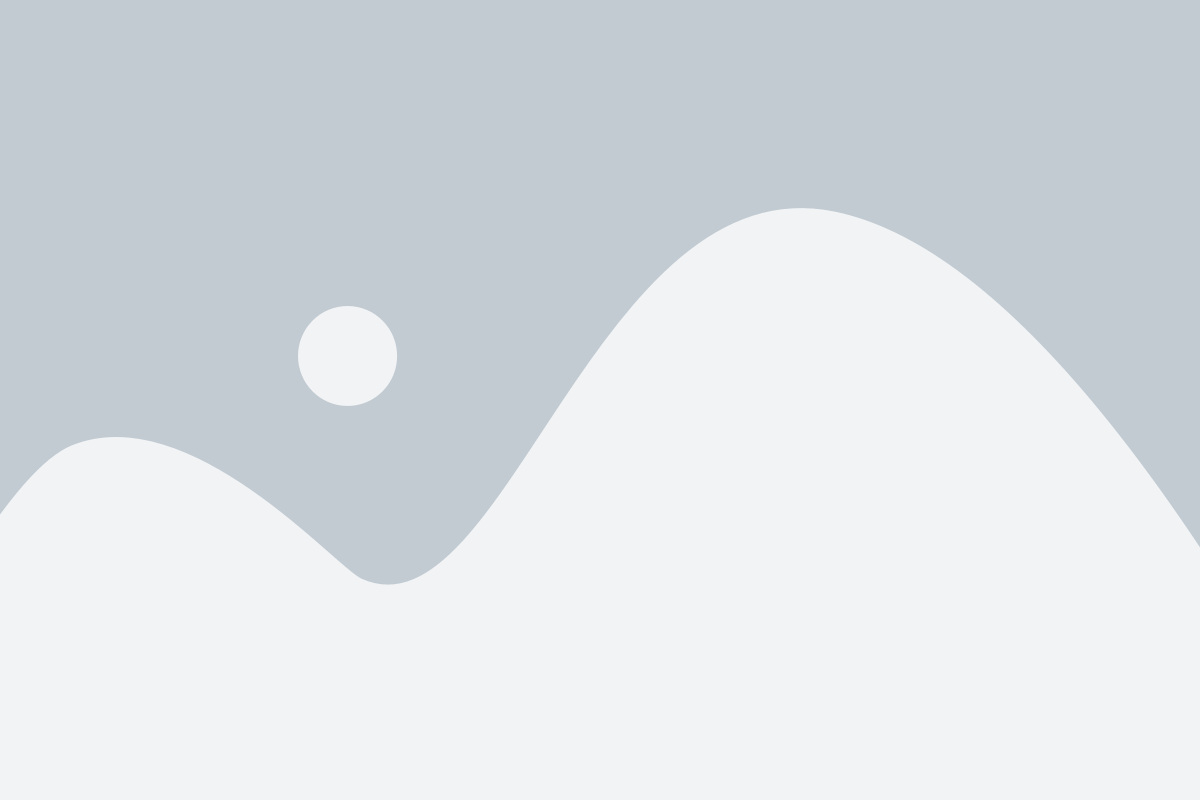
Induction Heater for Forging Turbine Blades
Turbine blades are critical components in jet engines used in the aerospace industry. These blades must be forged to precise specifications to ensure optimal performance and safety. The forging process involves heating the metal to a high temperature and then shaping it using a die. Induction heaters are used in the forging process of turbine blades to achieve the required temperature. Induction heating is a highly efficient process that allows for precise temperature control. The process involves passing an alternating electric current through a coil, which generates a magnetic field that induces eddy currents in the metal. These eddy currents generate heat, which raises the temperature of the metal. By adjusting the frequency and power of the electric current, the temperature can be precisely controlled. Using induction heaters for forging turbine blades is important because it allows for more precise temperature control compared to traditional heating methods. This results in more consistent and high-quality blades, which improves the performance and safety of the jet engine.
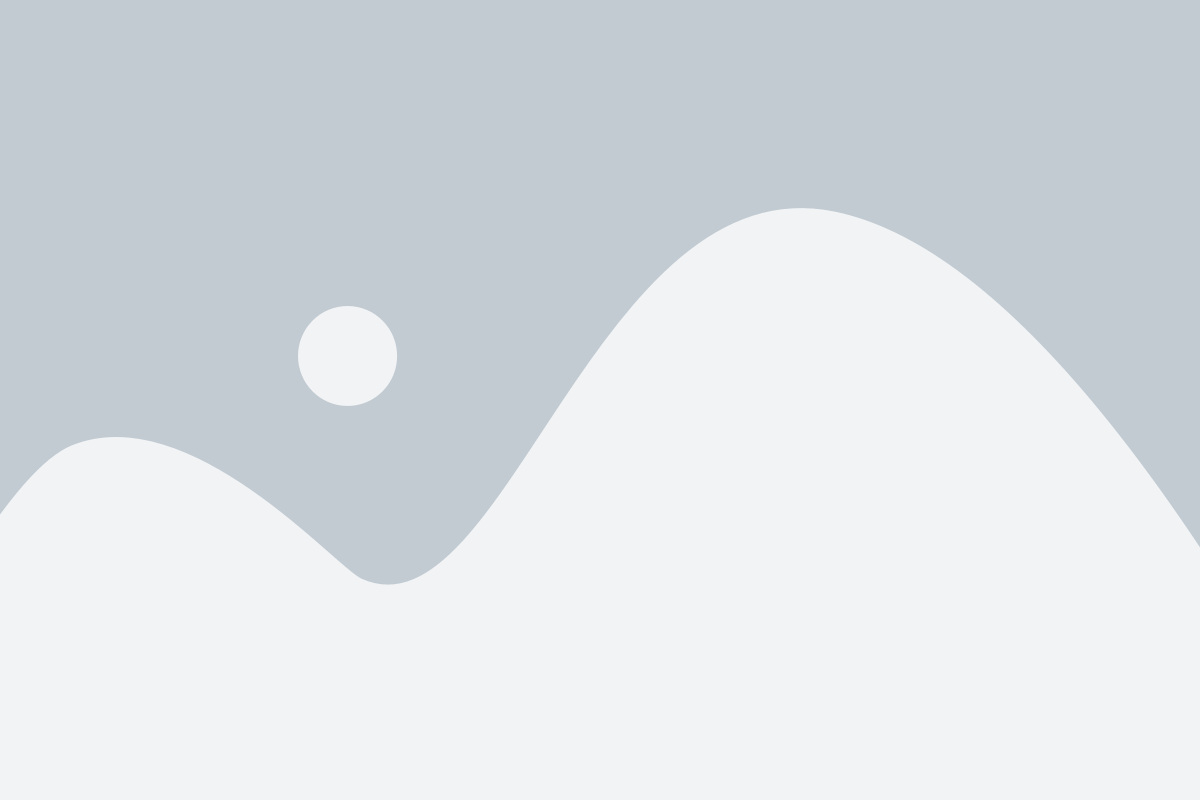
Induction Heater for Forging Compressor Blades
Compressor blades are another critical component in jet engines used in the aerospace industry. These blades compress the air entering the engine, which is necessary for combustion. The forging process for compressor blades is similar to that of turbine blades, and induction heaters are also used in the process for precise temperature control. Using induction heaters for forging compressor blades is essential for ensuring consistency and high-quality. Induction heating allows for precise temperature control, which helps to avoid defects and ensure uniformity in the blade. This improves the performance and safety of the jet engine.
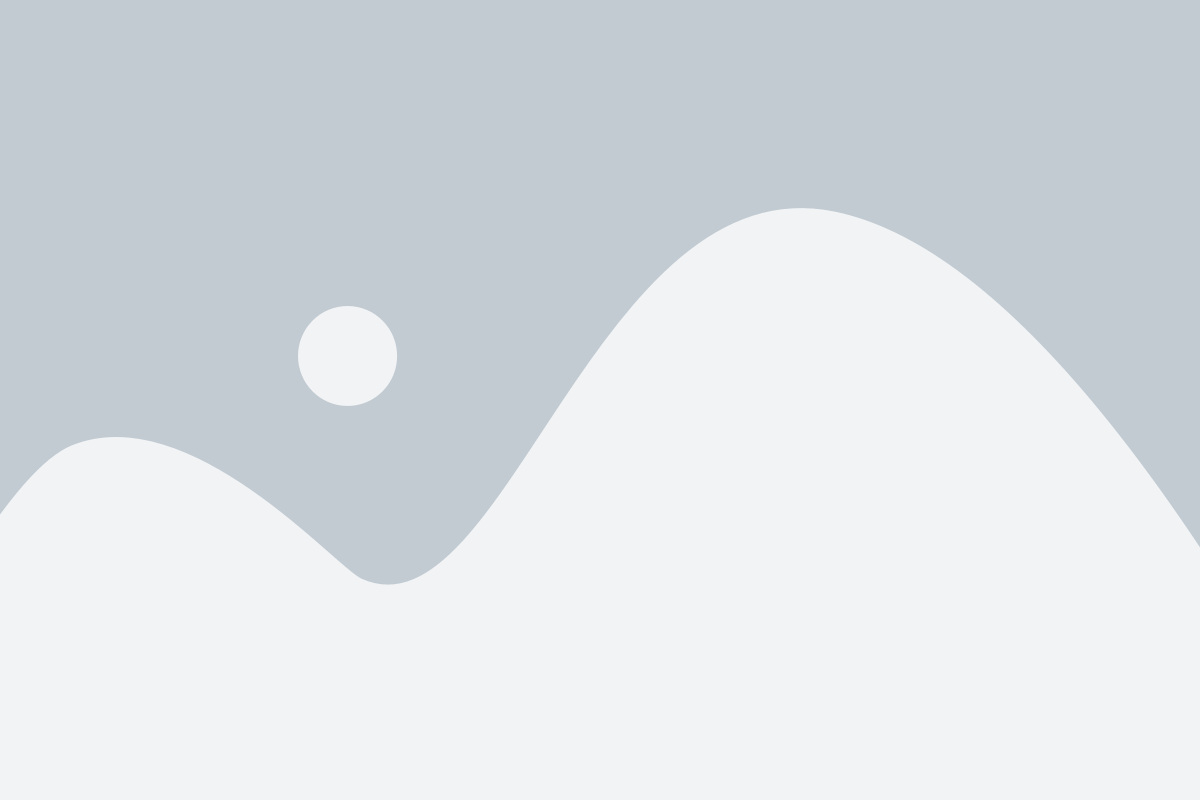
Induction Heater for Forging Rotor Shafts
Rotor shafts are used in a wide range of applications, including in jet engines, industrial machinery, and vehicles. The forging process for rotor shafts involves heating the metal to a high temperature and then shaping it using a die. Induction heaters are used in the process for precise temperature control. Induction heating is important in the forging of rotor shafts because it allows for more precise temperature control compared to traditional heating methods. This results in more consistent and high-quality rotor shafts, which improves the performance and reliability of the machinery.
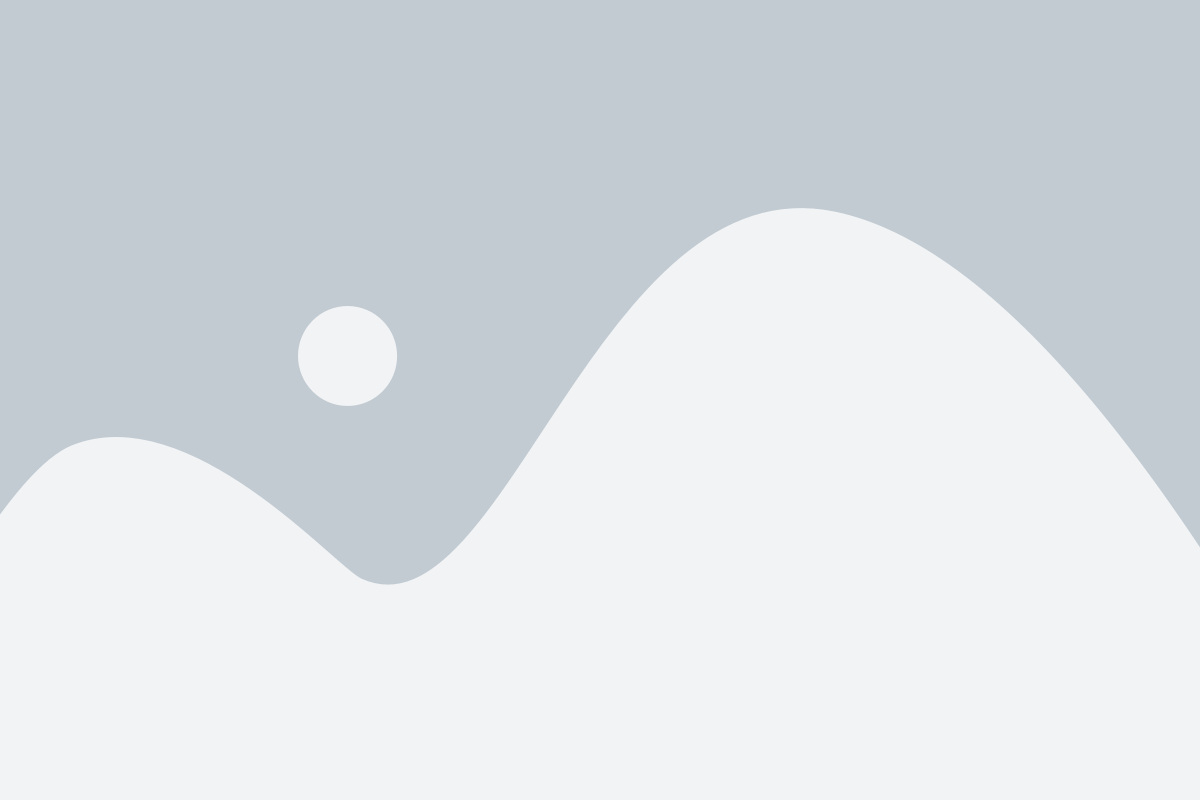
Induction Heater for Forging Gears
Gears are used in a wide range of applications, including in vehicles, industrial machinery, and consumer products. The forging process for gears involves heating the metal to a high temperature and then shaping it using a die. Induction heaters are used in the process for precise temperature control. Induction heating is essential in the forging of gears because it allows for more precise temperature control compared to traditional heating methods. This results in more consistent and high-quality gears, which improves the performance and durability of the machinery.
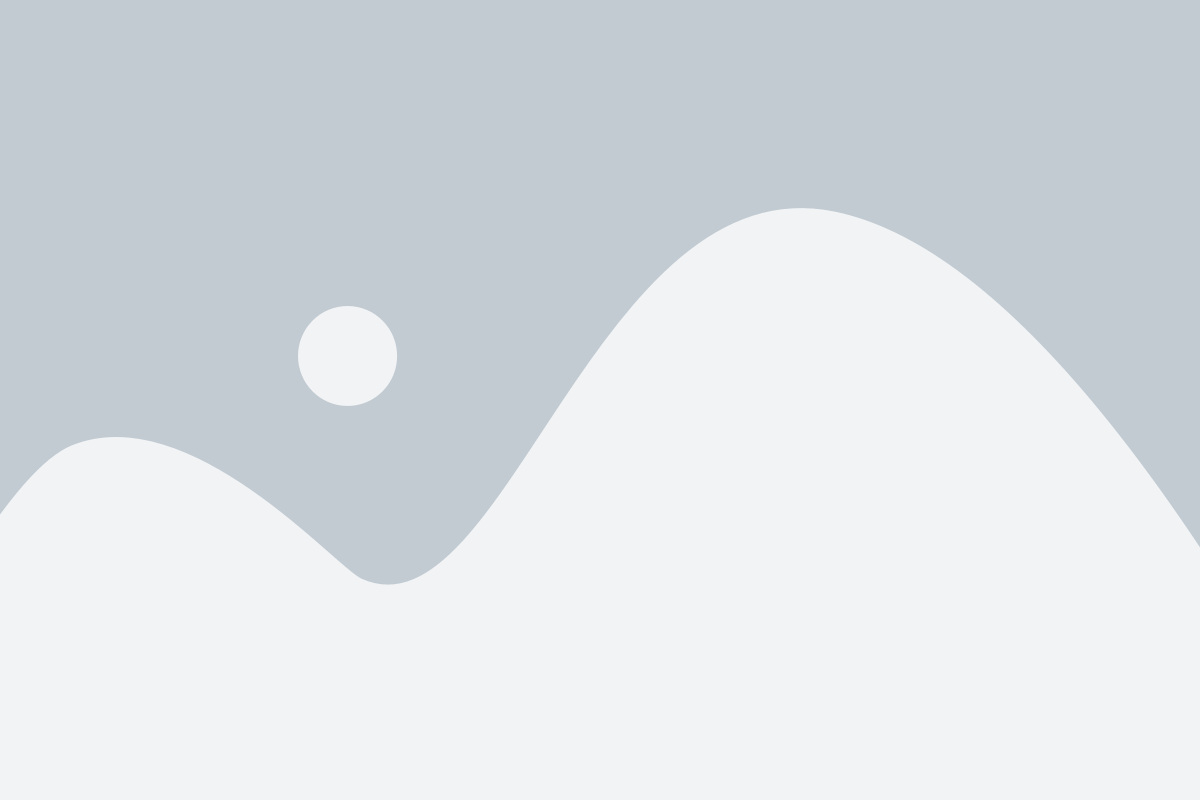
Induction Heater for Forging Crankshafts
Crankshafts are critical components in engines used in the automotive industry. These components convert the reciprocating motion of the pistons into rotary motion, which is necessary for the operation of the engine. The forging process for crankshafts involves heating the metal to a high temperature and then shaping it using a die. Induction heaters are used in the process for precise temperature control. Induction heating is important in the forging of crankshafts because it allows for more precise temperature control compared to traditional heating methods. This results in more consistent and high-quality crankshafts, which improves the performance and durability of the engine.
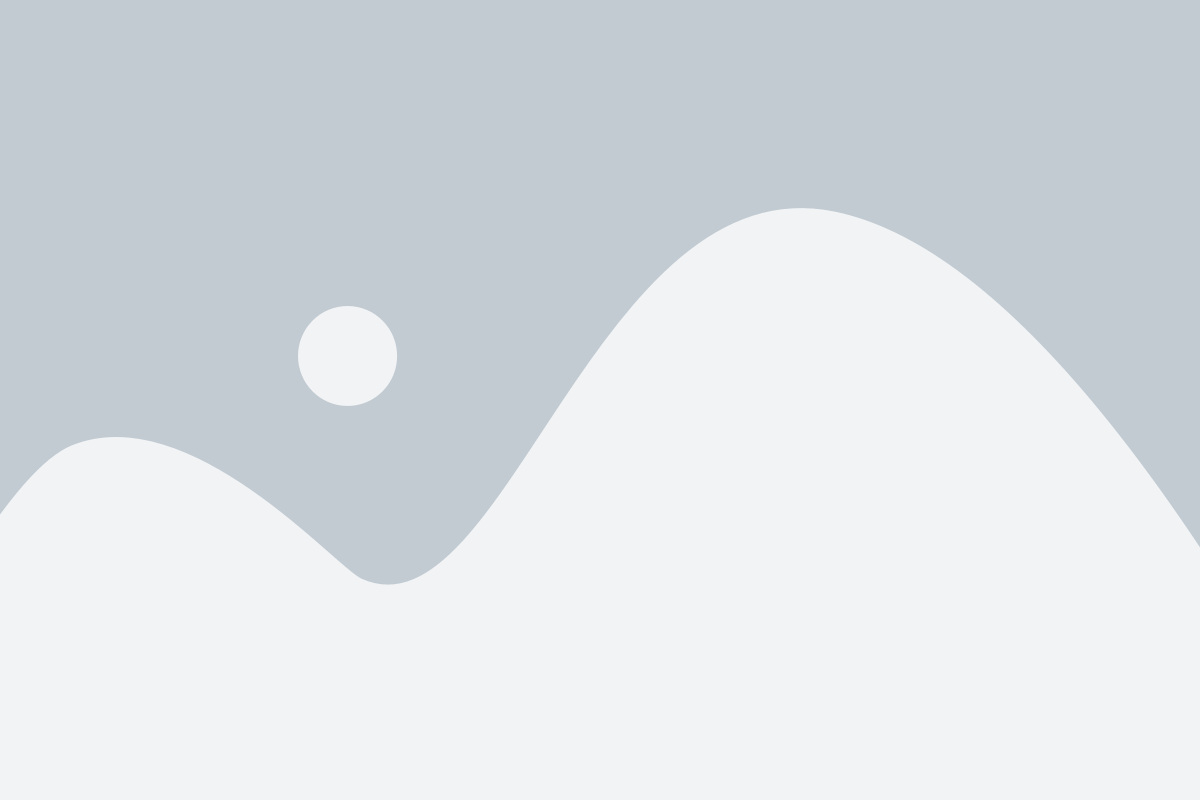
Induction Heater for Forging Axles
Axles are an essential component of vehicles that carry the weight of the vehicle and transfer the torque from the engine to the wheels. Induction heating is widely used in the production of axles, where it is used to heat the steel to forging temperatures. The process involves passing an electric current through a coil, which generates a magnetic field. The magnetic field then induces eddy currents within the workpiece, causing it to heat up.
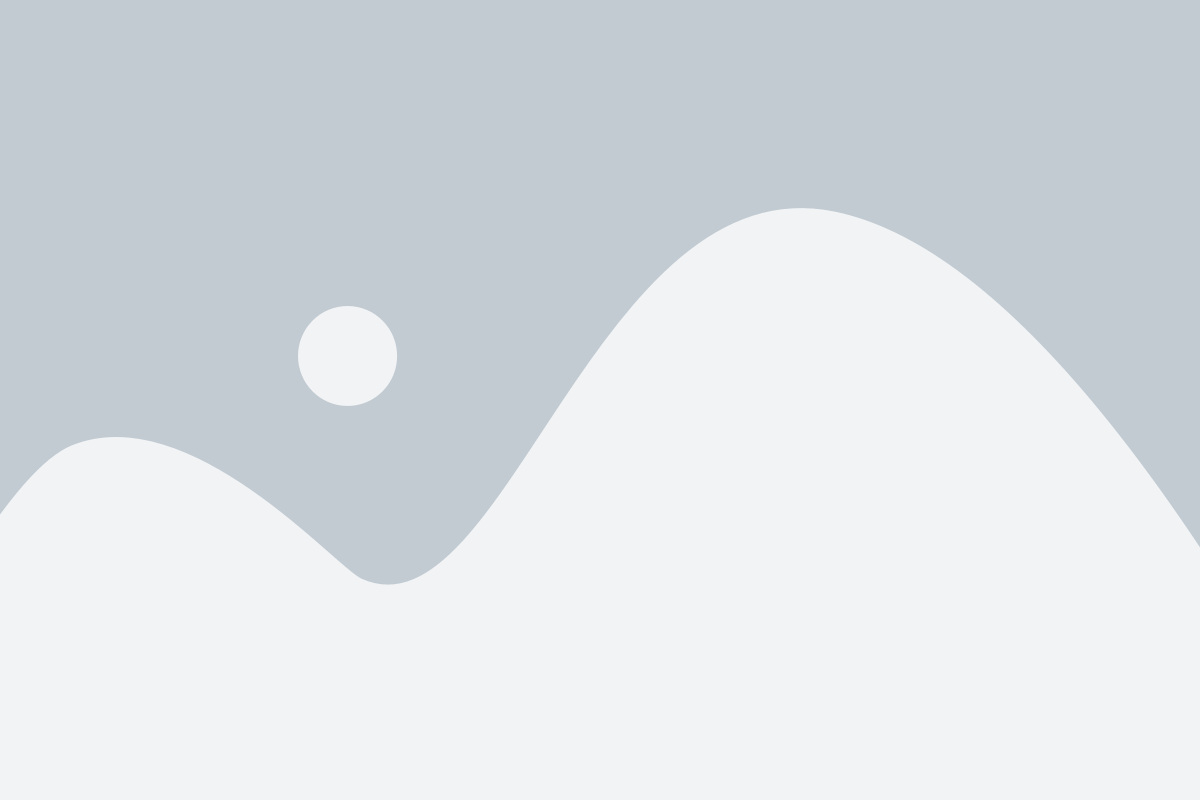
Induction Heater for Forging Suspension Components
Suspension components are an essential part of a vehicle’s suspension system, which provides a smooth and stable ride. Induction heating is commonly used in the production of suspension components such as control arms and tie rods. The process involves heating the steel to forging temperatures, which softens it and makes it easier to forge into the desired shape.
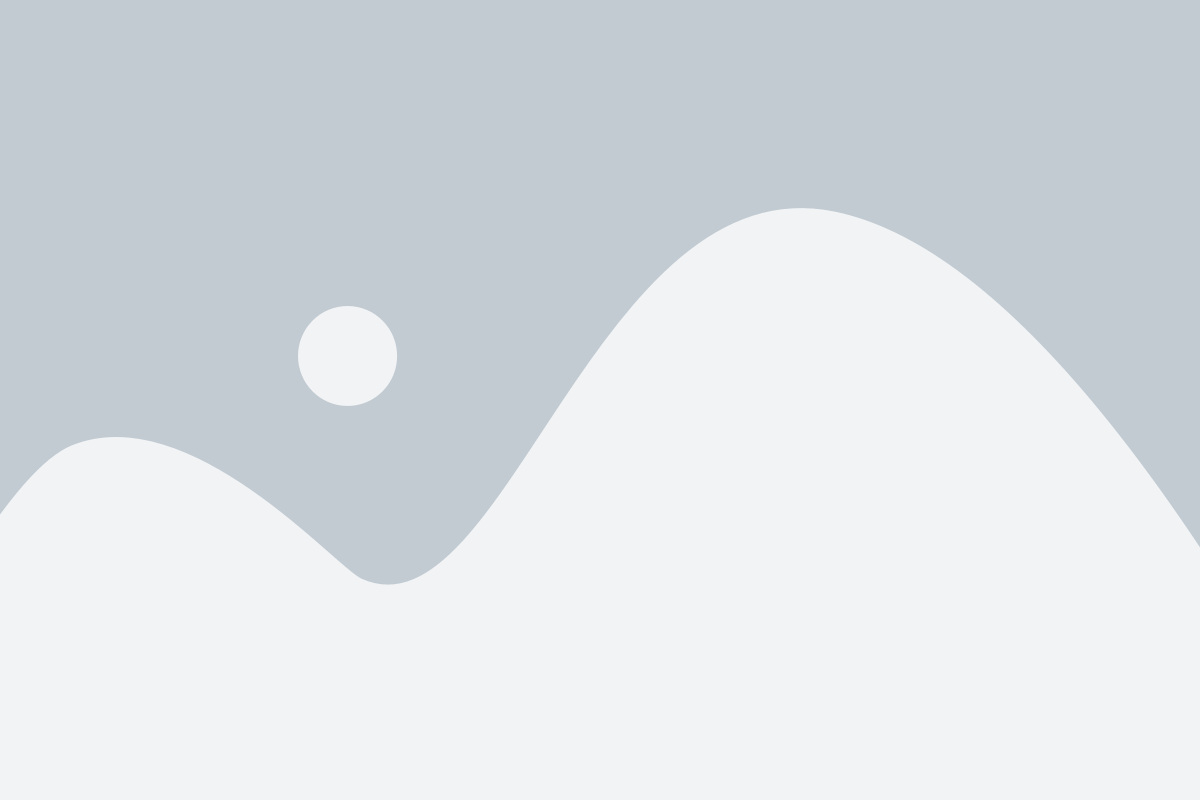
Induction Heater for Forging Hydraulic Cylinders
Hydraulic cylinders are used in a wide range of applications, including heavy machinery and industrial equipment. Induction heating is used in the forging of hydraulic cylinders, where it is used to heat the steel to the required temperature for forging. The process is fast and efficient, and it ensures that the cylinders are produced to the required specifications.
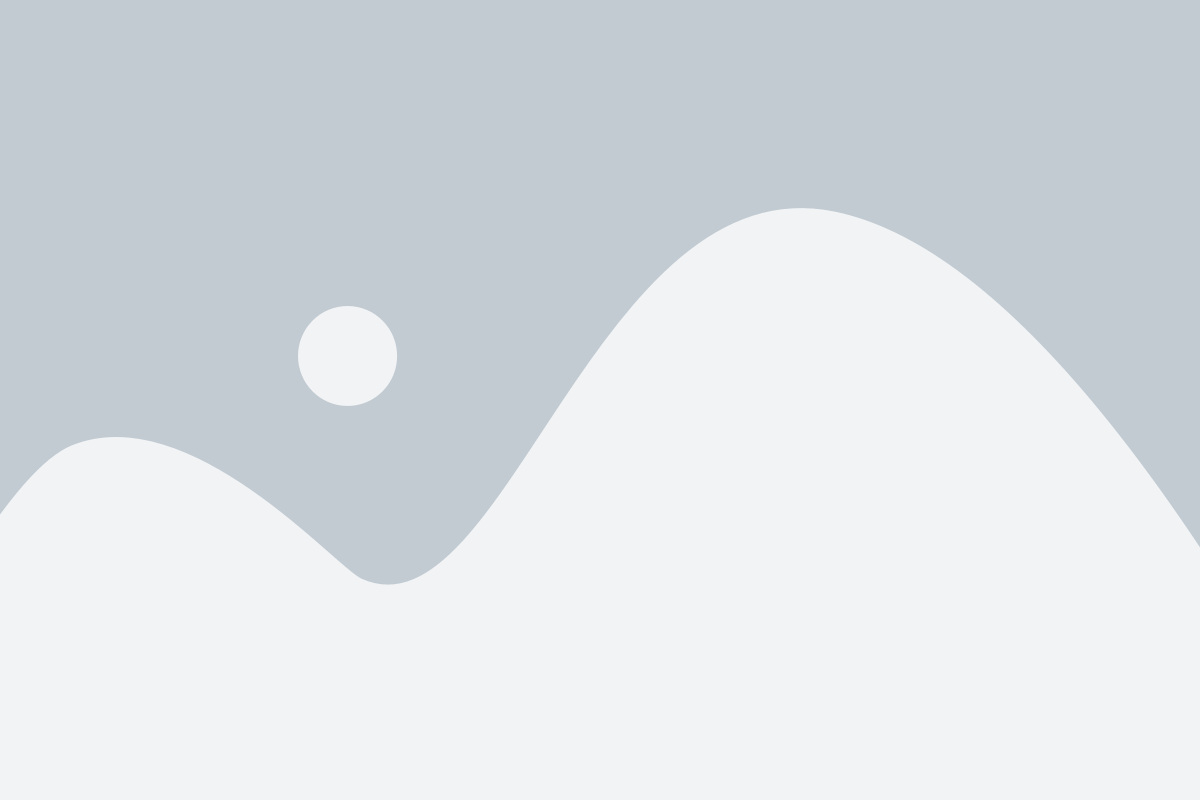
Induction Heater for Forging Pins
Pins are used in a wide range of applications, from construction equipment to automotive parts. Induction heating is used in the forging of pins, where it is used to heat the steel to forging temperatures. The process is efficient and produces high-quality pins that are strong and durable.
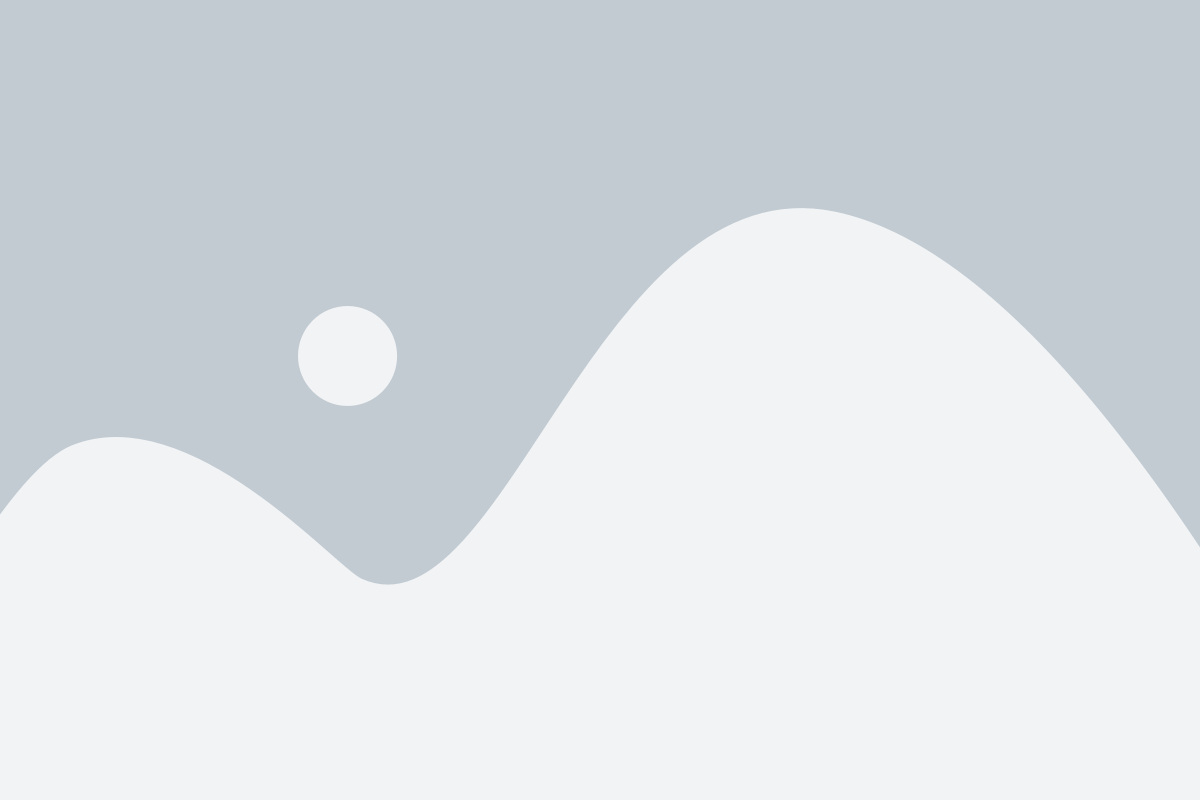
Induction Heater for Forging Bearings
Bearings are essential components in machines and equipment, providing smooth operation and reducing friction. Induction heating is used in the forging of bearings, where it is used to heat the steel to the required temperature for forging. The process is fast and efficient, and it ensures that the bearings are produced to the required specifications.
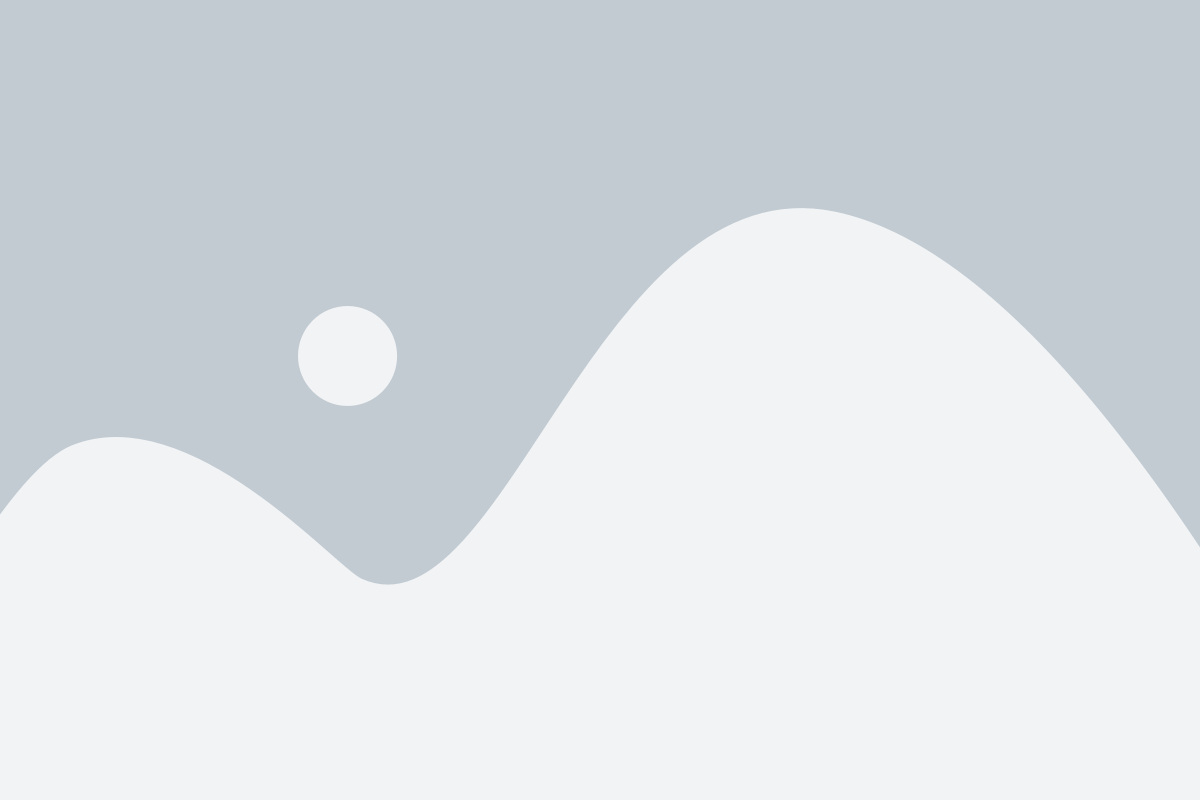
Induction Heater for Forging Valves
Valves are used in a wide range of applications, from pipelines to engines. Induction heating is used in the forging of valves, where it is used to heat the steel to the required temperature for forging. The process is efficient and produces high-quality valves that are strong and durable.
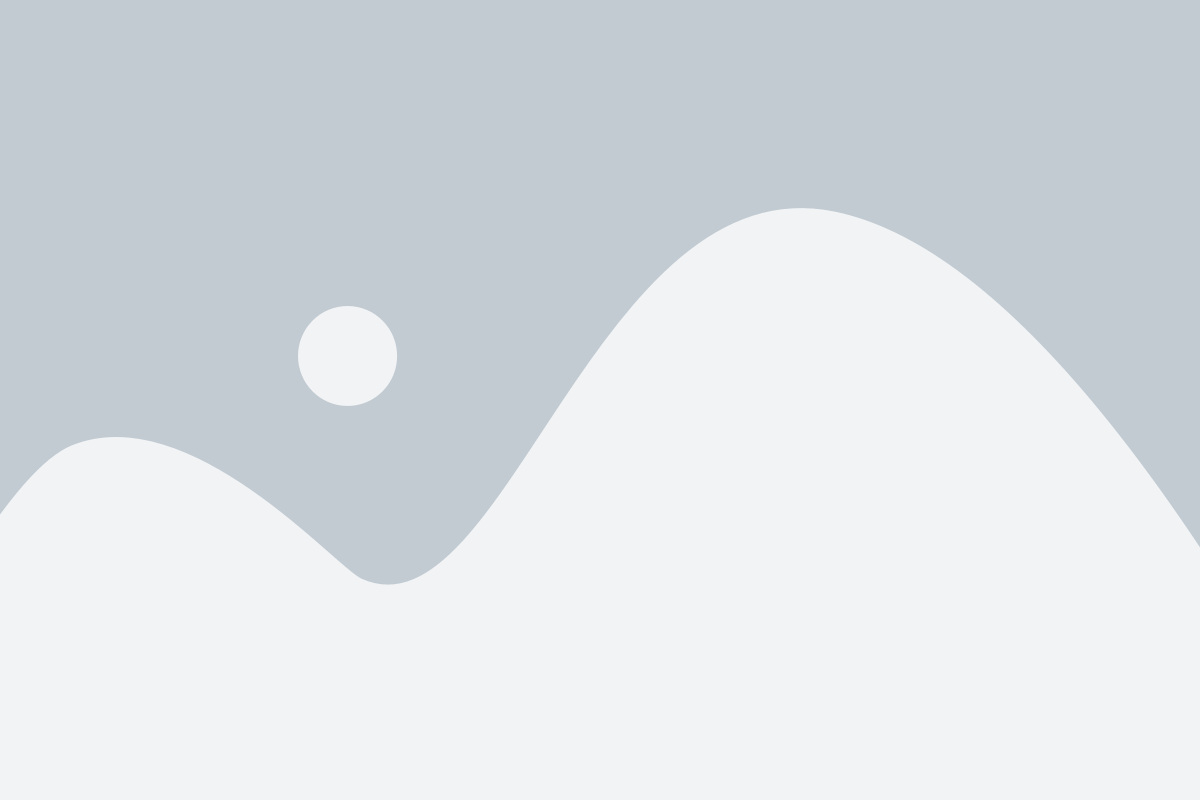
Induction Heater for Forging Couplings
Couplings are used to connect two shafts together, allowing them to transmit torque between them. Induction heating is used in the forging of couplings, where it is used to heat the steel to forging temperatures. The process is efficient and produces high-quality couplings that are strong and durable.
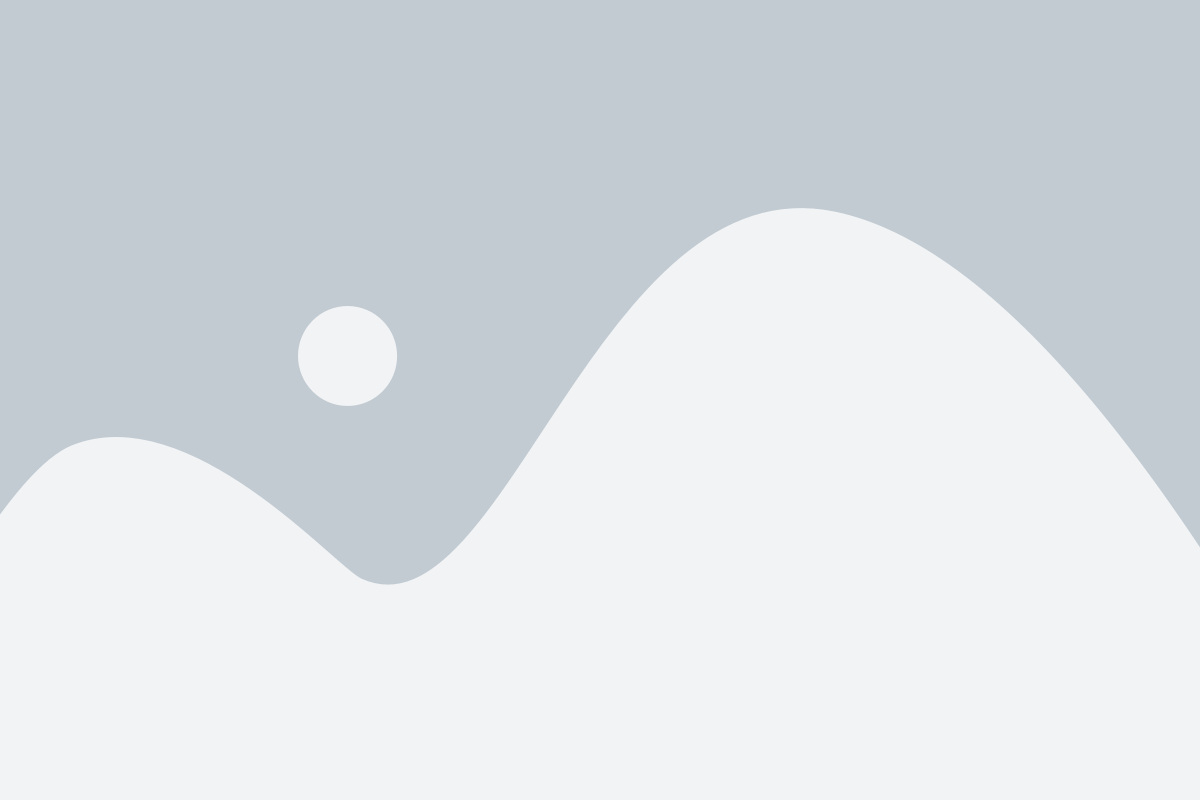
Induction Heater for Forging Dies
Forging dies are used to shape metal into the desired shape during the forging process. Induction heating is used to heat the dies to the required temperature for forging. The process is efficient and produces high-quality dies that are strong and durable.
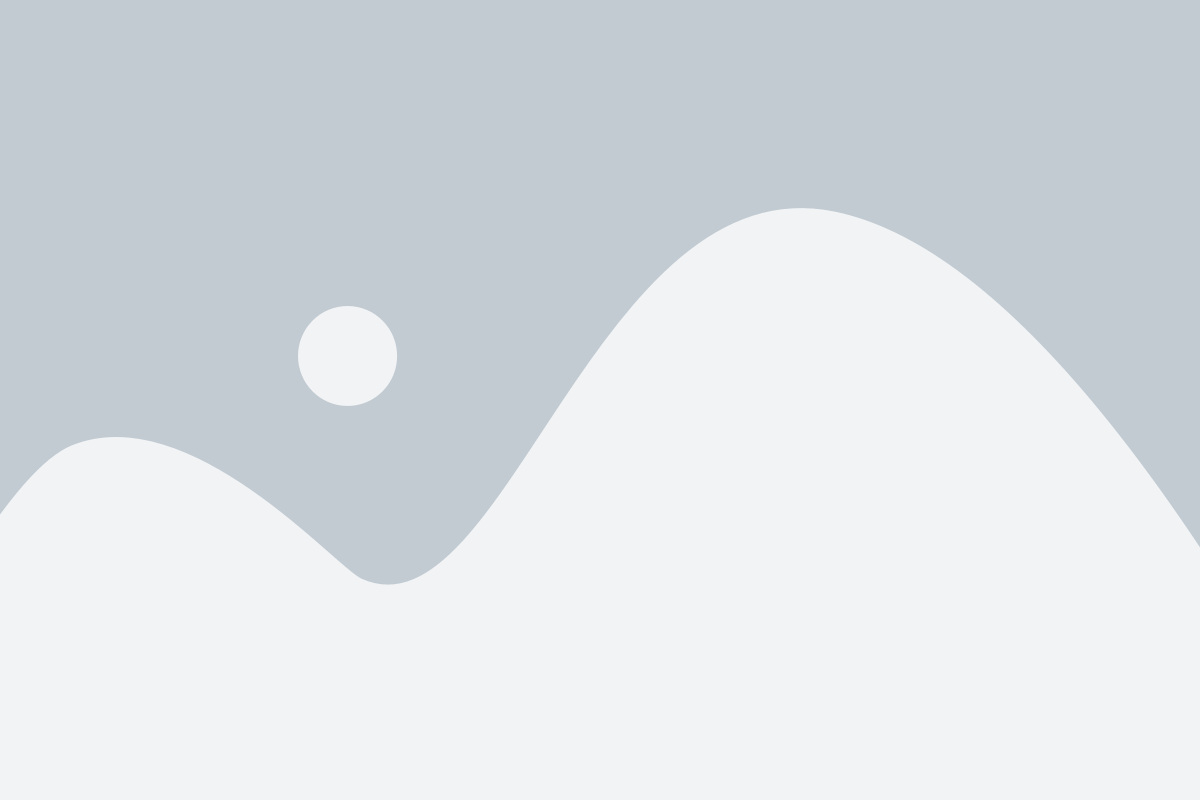
Induction Heater for Forging Hammers
Hammers are used in the forging process to shape metal into the desired shape. Induction heating is used to heat the hammers to the required temperature for forging. The process is efficient and produces high-quality hammers that are strong and durable.
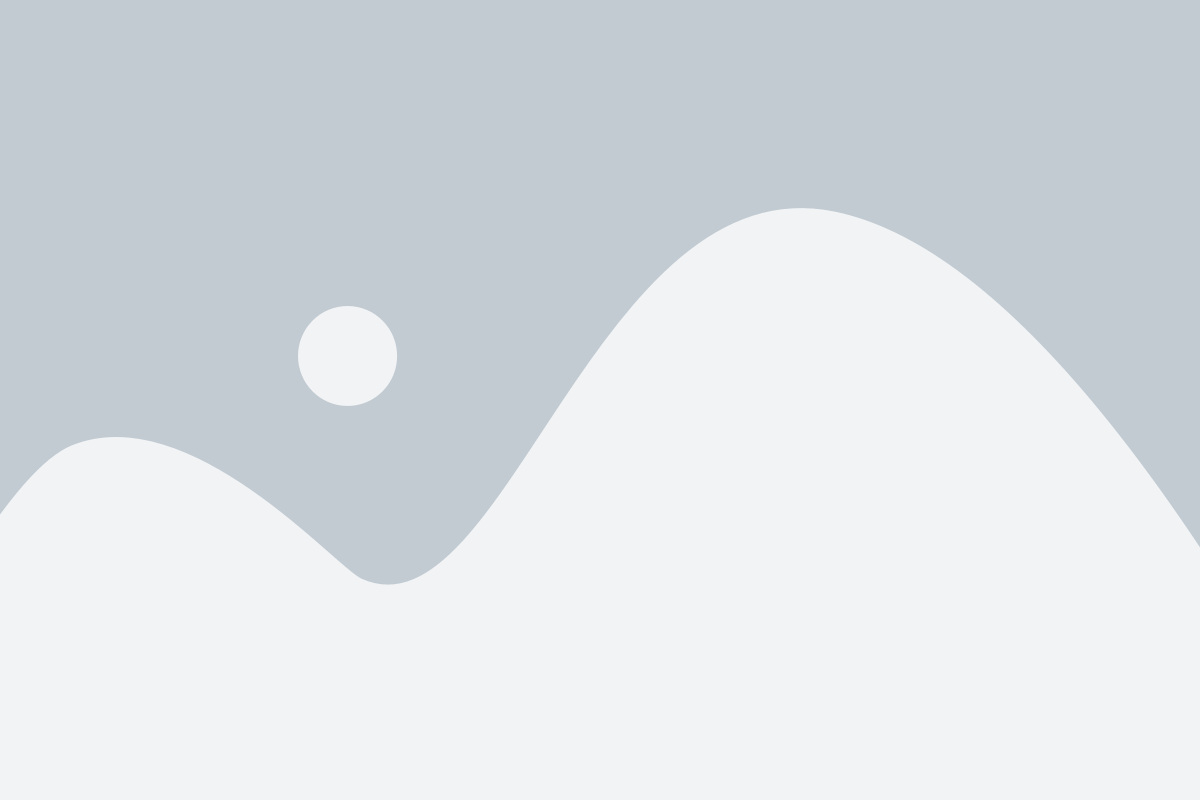
Induction Heater for Forging Anvils
Anvils are a crucial component in the forging process, providing a sturdy surface for the metal to be shaped upon. However, in order to properly shape the metal, the anvil must be heated to the correct temperature. By using an induction heater to heat the anvil, the process becomes much more efficient and effective. Induction heating works by passing an alternating current through a copper coil, which generates a magnetic field that induces eddy currents in the metal being heated. These eddy currents create heat, quickly and efficiently raising the temperature of the metal.
Induction Heaters Offered by GM Industries
For more information on any of our high quality products or getting accurate prices contact GM Industries at
Call Us
+(91)-9820533489 / 7738562224
Enquiry Form
Submit
Frequently Asked Questions
An induction heater is used to heat the metal to the required temperature for forging.
An induction heater works by passing an alternating current through a copper coil, which generates a magnetic field that induces eddy currents in the metal being heated. These eddy currents create heat, quickly and efficiently raising the temperature of the metal.
Induction heating can be used to heat a wide range of metals including steel, aluminium, copper, brass, and titanium.
The temperature range depends on the specific application, but induction heating can achieve temperatures up to 2500 degrees Fahrenheit.
Induction heating is more efficient than other heating methods, such as gas or oil heating, because it directly heats the metal and does not require a heat transfer medium.
The induction heating process involves passing an alternating current through a copper coil, which generates a magnetic field that induces eddy currents in the metal being heated.
Safety precautions include using proper protective gear, keeping the work area clean, and following manufacturer guidelines for operation and maintenance.
Induction heating can improve the quality of the final product by providing precise temperature control and reducing the likelihood of material distortion or defects.
Regular maintenance is required, such as cleaning the equipment and inspecting it for signs of wear or damage.
Yes, an induction heater can be used for both small and large-scale forging operations.
The size of the metal being heated affects the amount of power required and the heating time needed to reach the desired temperature.
Yes, induction heating provides precise temperature control, making it an ideal choice for precision forging.
No, induction heating requires the metal to be heated to a specific temperature in order to be shaped through forging.
Induction heating is an energy-efficient process that produces less waste and emissions than traditional heating methods.
The cost depends on the specific equipment and the size and scope of the forging operation.
The energy consumption depends on the specific equipment and the size and scope of the forging operation.
Yes, induction heating can be used for a variety of applications including brazing, annealing, and heat treating.
The lifespan depends on the specific equipment and the level of use and maintenance.
Yes, induction heating can be easily integrated with automation systems for efficient and precise forging operations.