Induction Hardening
What is Hardening?
Industrial hardening typically involves modifying the physical and/or chemical properties of a material or component to increase its resistance to various forms of damage. This can involve processes such as heating, which involves heating the material to a specific temperature and then cooling it rapidly or slowly to alter its microstructure and mechanical properties. Surface hardening may involve techniques such as nitriding, carburizing, or ion implantation, which introduce additional elements or compounds into the surface layer of the material to increase its hardness, wear resistance, or corrosion resistance. Coatings can also be applied to the surface of the material to provide additional protection against environmental factors such as humidity, chemicals, or abrasion. By hardening materials and components, industrial processes can improve their durability, reliability, and safety, ultimately leading to more efficient and productive operations. Induction heating is one of the most commonly used methods for hardening because it offers several advantages over other heating methods. It is a fast and efficient way to heat materials, as it can rapidly bring them up to the required temperature without requiring direct contact. This not only saves time and energy, but also reduces the risk of distortion or other undesirable effects that can occur with other heating methods.
Why Induction Heater is used for Hardening Processes?
Induction heating is often used for hardening processes because it can quickly and efficiently heat a material to the required temperature without requiring direct contact. Induction heater is particularly well-suited to hardening because it can be used to heat only the surface layer of a material, leaving the core relatively unaffected. This means that only the part of the material that needs to be hardened is heated, reducing the risk of distortion or other undesirable effects that can occur with other heating methods. Furthermore, induction heating is a highly controllable process, allowing for precise control over the temperature and heating time, which is essential for achieving consistent and repeatable results in the hardening process.
Introduction to Industrial Induction Heater for Hardening
Industrial induction heaters for hardening are used in a wide range of applications, from the hardening of metals and alloys to the heating of various other materials. They are particularly well-suited to applications where high volumes of parts or components need to be processed quickly and efficiently, as they offer a fast and controllable method of heating. An industrial induction heater for hardening uses electromagnetic induction to rapidly and efficiently heat materials for the purpose of hardening. This type of heater typically consists of a power supply unit that generates a high-frequency alternating current, a coil that creates a strong magnetic field, and a workpiece that is positioned within the coil. When the alternating current flows through the coil, it generates a magnetic field that induces electrical currents, known as eddy currents, within the workpiece. These eddy currents generate heat within the material due to its electrical resistance, causing it to rapidly reach the desired temperature for hardening.
GM Industries is a leading manufacturer of industrial induction heaters for hardening, and plays a major role in helping businesses find the perfect heating solutions for their needs. With years of experience in the industry, GM Industries has developed a range of innovative and reliable induction heating systems that are designed to meet the needs of a wide range of applications.
Advantages of Using an Industrial Induction Heater for Hardening
Using an industrial induction heater for hardening offers several key features that make it a popular choice for a wide range of applications. Some of the main features of using an industrial induction heater for hardening include:
Fast heating
Industrial induction heaters can rapidly heat materials to the desired temperature for hardening. This allows for faster processing times and increased productivity.
Precise control
Industrial induction heaters offer precise temperature control, which is essential for achieving consistent and repeatable results in the hardening process. This level of control is not always possible with other heating methods.
Energy efficiency
Industrial induction heaters are typically more energy-efficient than other heating methods, as they use electromagnetic induction to heat the material directly. This results in less energy waste and lower operating costs.
Reduced distortion
Industrial induction heaters can be used to selectively heat only the surface layer of a material, leaving the core relatively unaffected. This reduces the risk of distortion or other undesirable effects that can occur with other heating methods
Improved safety
Industrial induction heaters are a safe and clean method of heating, as they do not involve the use of open flames or hot surfaces. This makes them a popular choice for industrial processes where safety is a concern.
Versatility
Industrial induction heaters can be used for a wide range of materials and applications, making them a valuable tool for many industries. They can be used for hardening metals and alloys, as well as for the heat treatment of other materials.
Overall, using an industrial induction heater for hardening offers several key advantages over other heating methods. Its fast heating, precise control, energy efficiency, reduced distortion, improved safety, and versatility make it a popular choice for businesses in a wide range of industries.
Induction Heater for Various Hardening Process
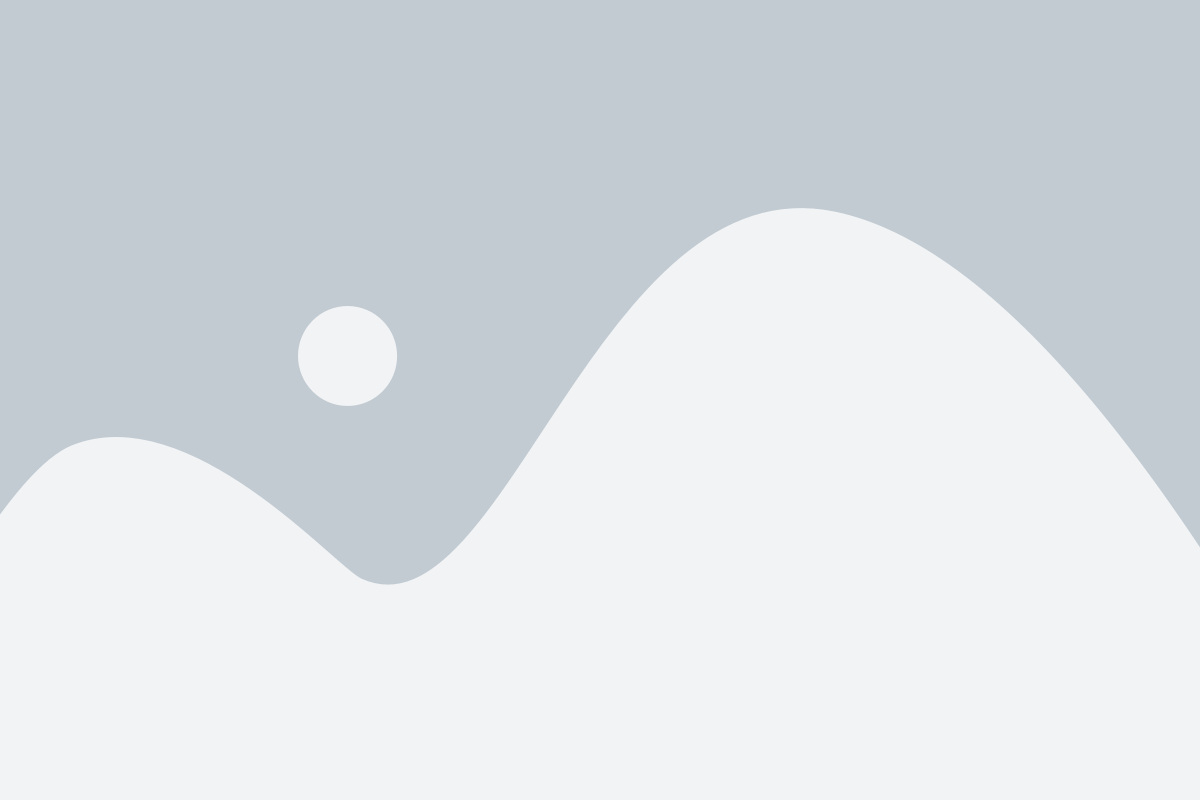
Induction heater for hardening gears
Gears are commonly used in mechanical systems, and their teeth often require hardening to improve their wear resistance and prolong their lifespan. Induction heating can be used to selectively harden the teeth of gears by heating them to the desired temperature and then quenching them in a cooling medium. This process helps to improve the hardness and durability of the gear teeth. Induction heating is often used for this application due to its precise and controllable heating process, which allows for consistent and repeatable results.
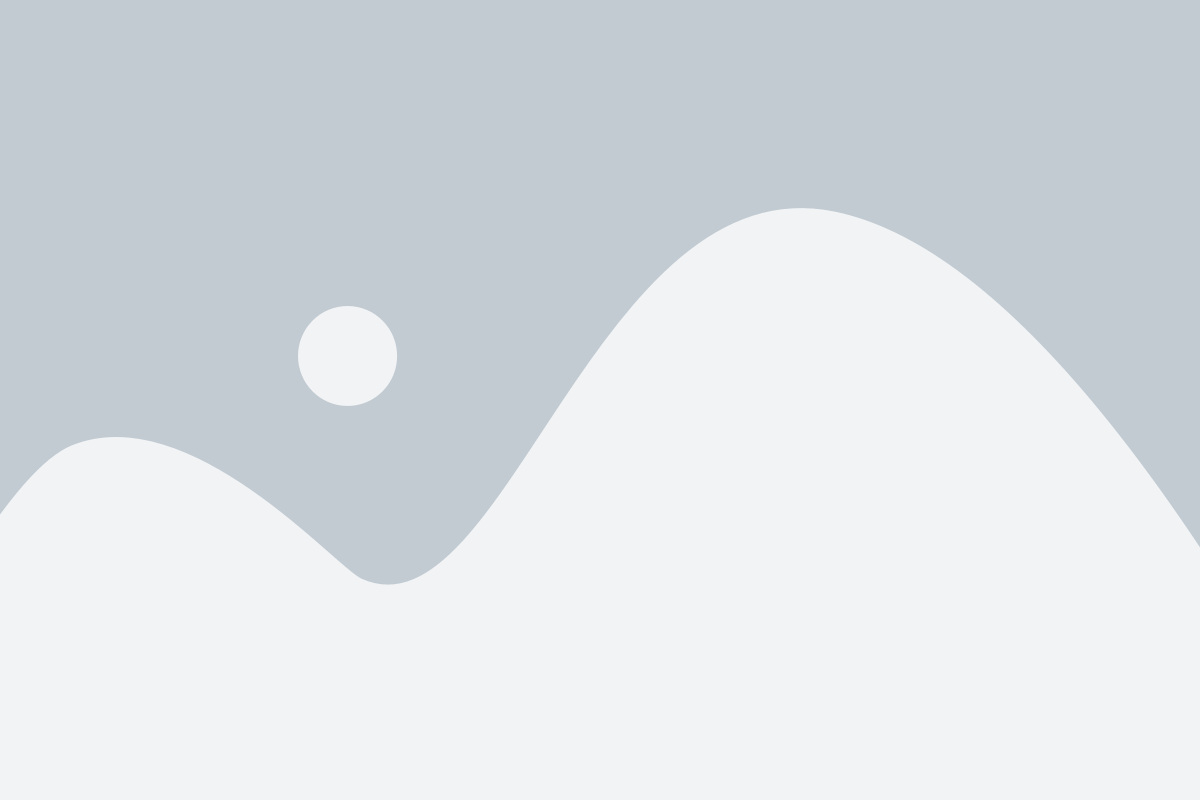
Induction heater for hardening shafts
Shafts are critical components in many mechanical systems, and their surfaces often require hardening to improve their strength and durability. Induction heating can be used to harden the surfaces of shafts by heating them to a specific temperature and then quenching them in a cooling medium. This process creates a hardened layer on the surface of the shaft, which helps to improve its wear resistance and prolong its lifespan. Induction heating is an ideal method for this application due to its precise and localized heating process, which minimizes the risk of overheating or distortion.
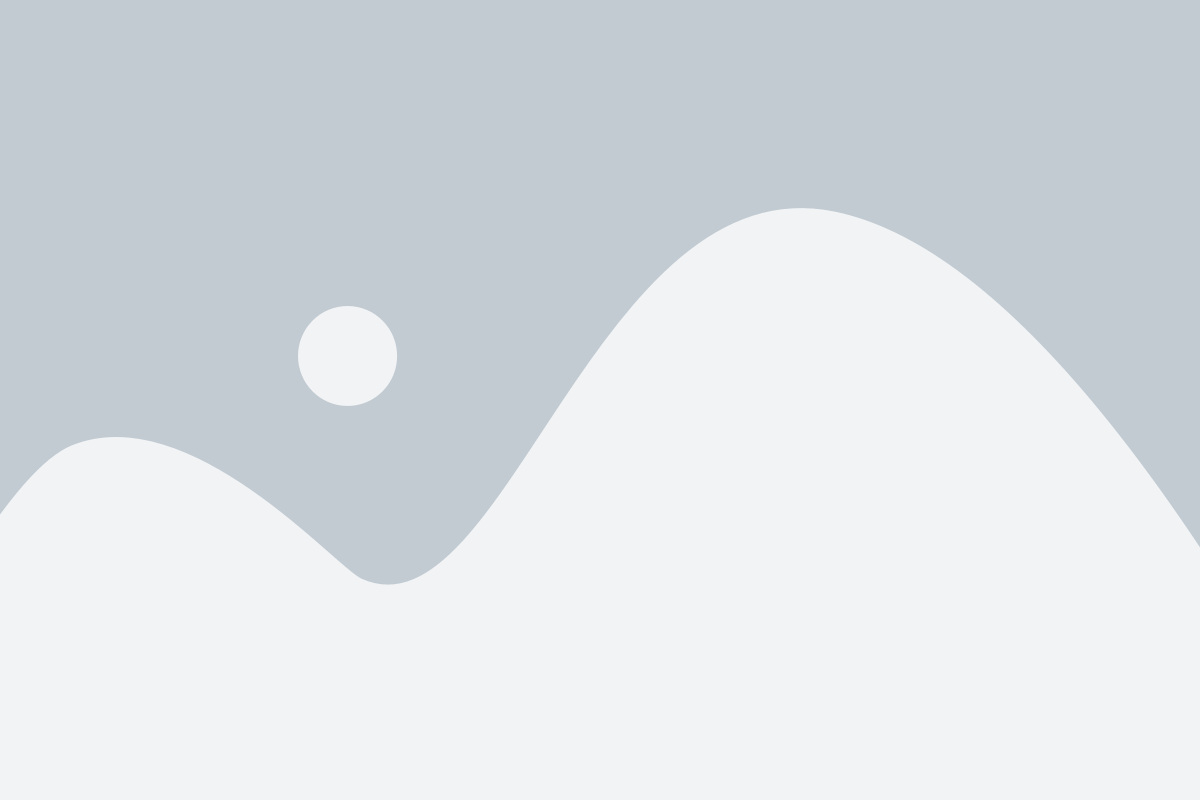
Induction heater for hardening bearings
Bearings are used in a variety of applications, and their races often require hardening to improve their wear resistance and performance. Induction heating can be used to selectively harden the races of bearings by heating them to a specific temperature and then quenching them in a cooling medium. This process creates a hardened layer on the surface of the race, which helps to improve its durability and reduce wear. Induction heating is an ideal method for this application due to its precise and localized heating process, which minimizes the risk of overheating or distortion.
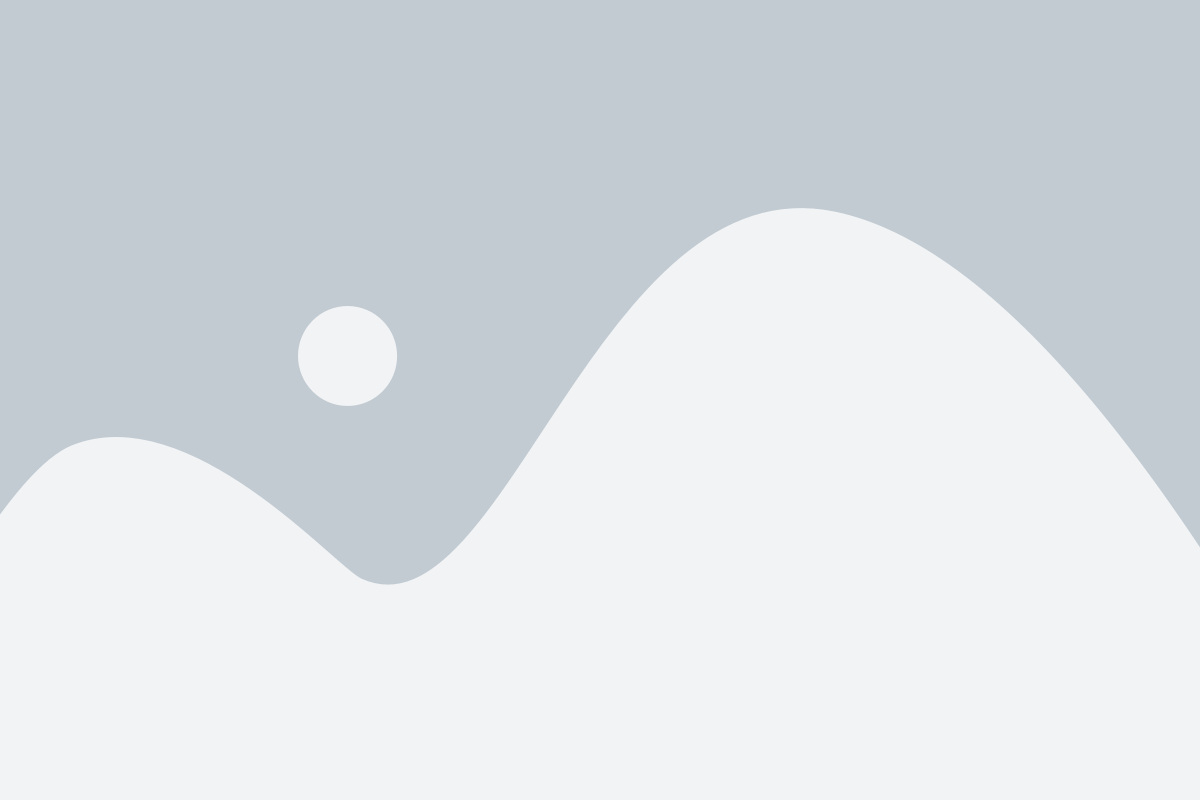
Induction heater for hardening tooling (e.g. dies, molds)
Tooling components such as dies and molds are used in many manufacturing processes and often require hardening to improve their wear resistance and extend their lifespan. Induction heating can be used to harden the surfaces of tooling components by heating them to a specific temperature and then quenching them in a cooling medium. This process creates a hardened layer on the surface of the tooling, which helps to improve its durability and resistance to wear. Induction heating is often used for this application due to its precise and localized heating process, which allows for consistent and repeatable results.
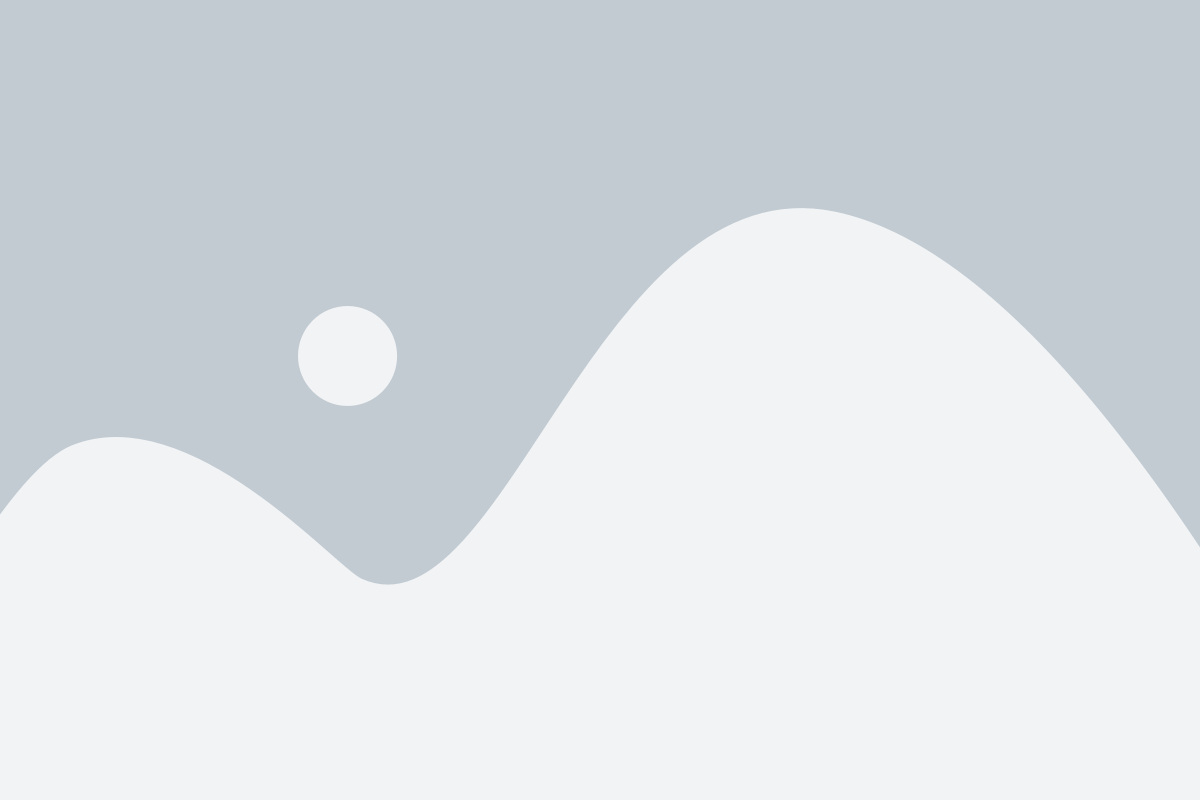
Induction heater for hardening turbine blades
Turbine blades are critical components in the aerospace industry, and their surfaces often require hardening to improve their strength and durability. Induction heating can be used to harden the surfaces of turbine blades by heating them to a specific temperature and then quenching them in a cooling medium. This process creates a hardened layer on the surface of the blade, which helps to improve its resistance to fatigue and prolong its lifespan. Induction heating is often used for this application due to its precise and localized heating process, which minimizes the risk of overheating or distortion.
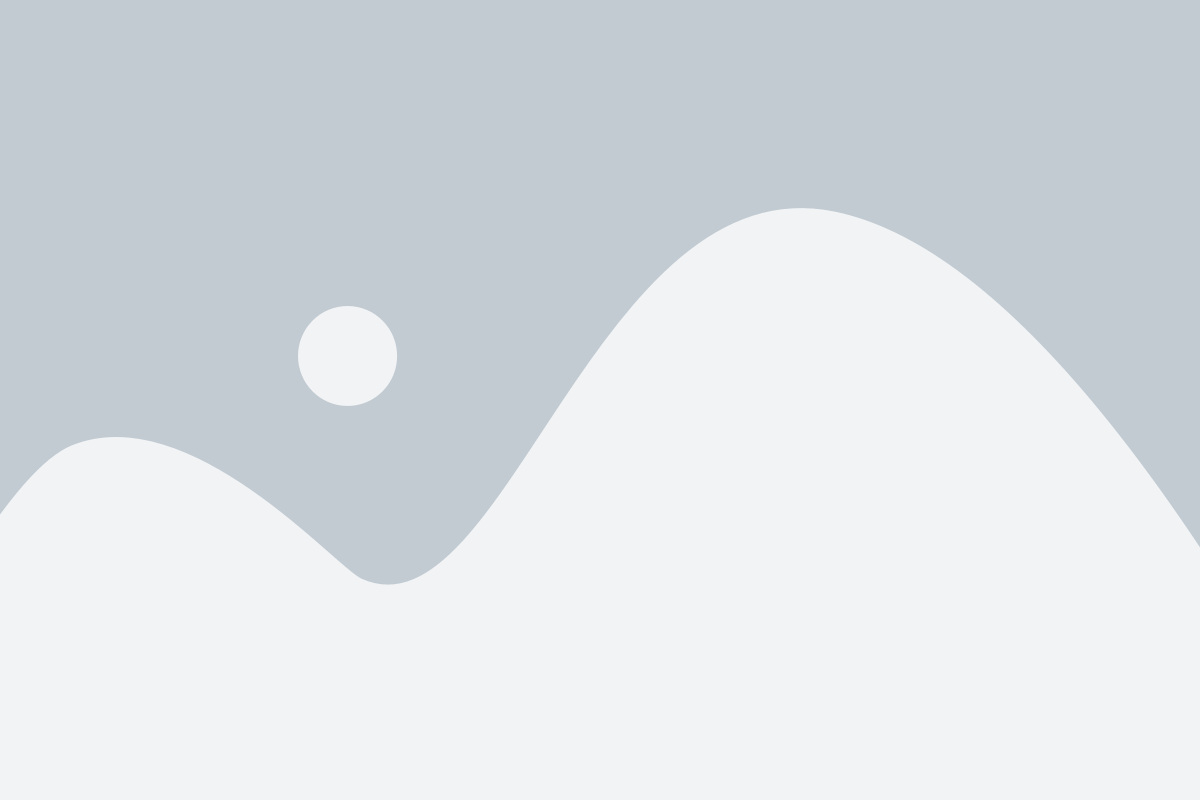
Induction heater for hardening springs
Springs are used in a variety of applications and require a certain level of hardness to function properly. Induction heating can be used to harden the surface of the spring by heating it to a specific temperature and then quenching it in a cooling medium. This process creates a hardened layer on the surface of the spring, which helps to improve its durability and resistance to wear. Induction heating is often used for this application due to its fast heating rate, which allows for high throughput and improved efficiency.
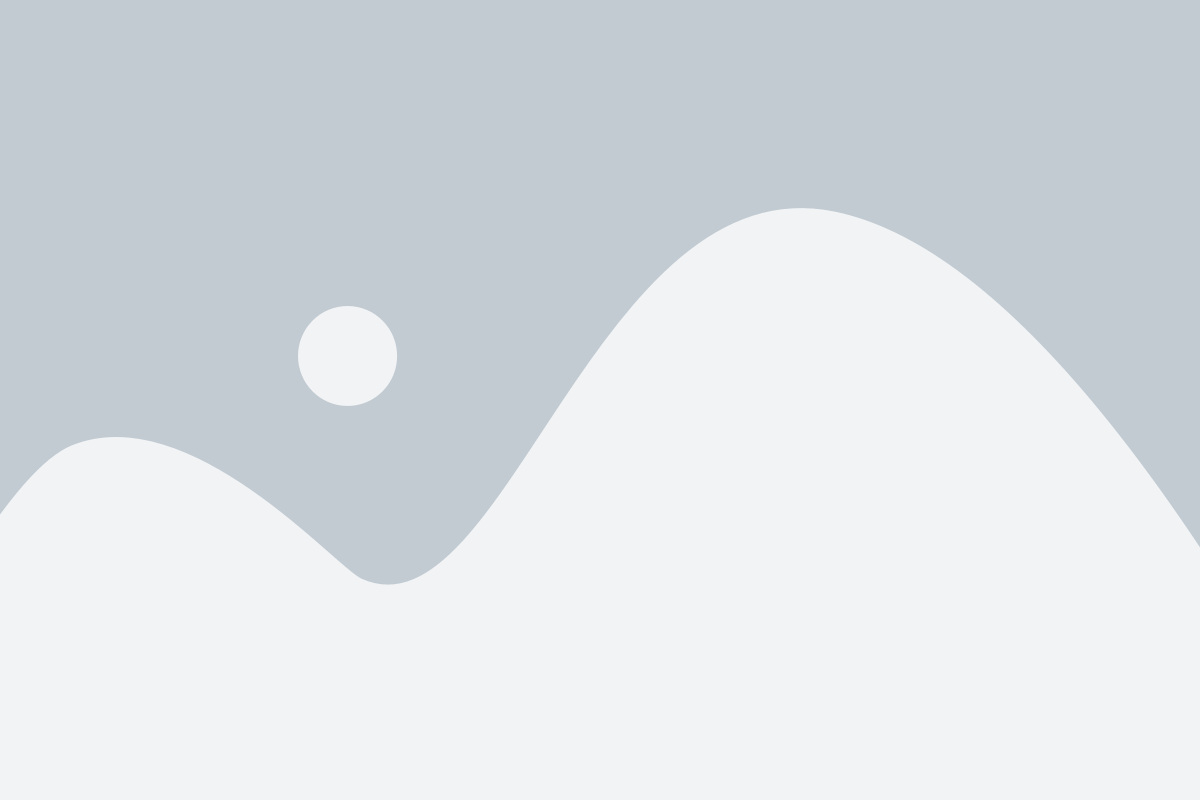
Induction Heater for Hardening Camshafts
Camshafts are a crucial component of internal combustion engines that control the opening and closing of valves. To increase their durability and longevity, camshafts are hardened using induction heating. The process involves heating the camshafts to a specific temperature, usually between 800°C to 900°C, followed by quenching them in a bath of oil or water. This results in a hardened surface layer that is resistant to wear and tear. An induction heater for hardening camshafts utilizes a high-frequency electromagnetic field to generate heat in the metal. This process is more efficient than traditional heating methods, such as gas or electric furnaces. Induction heating is more accurate and faster, allowing for precise control over the heating process and reducing the risk of distortion or cracking in the camshaft.
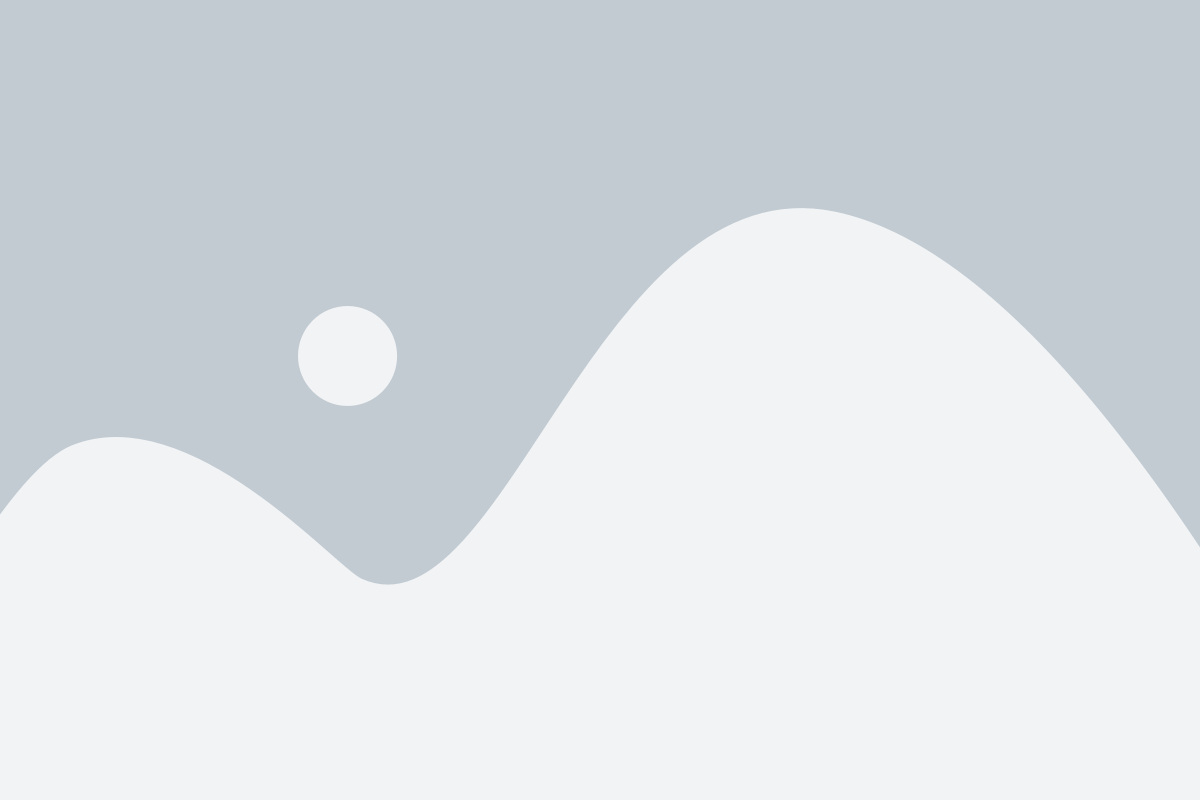
Induction Heater for Hardening Crankshafts
Crankshafts are another critical component of internal combustion engines that convert reciprocating motion into rotational motion. To increase their strength and durability, crankshafts are hardened using induction heating. The process involves heating the crankshafts to a specific temperature, usually between 800°C to 900°C, followed by quenching them in a bath of oil or water. An induction heater for hardening crankshafts utilizes a high-frequency electromagnetic field to generate heat in the metal. This process is more efficient than traditional heating methods, such as gas or electric furnaces. Induction heating is more accurate and faster, allowing for precise control over the heating process and reducing the risk of distortion or cracking in the crankshaft.
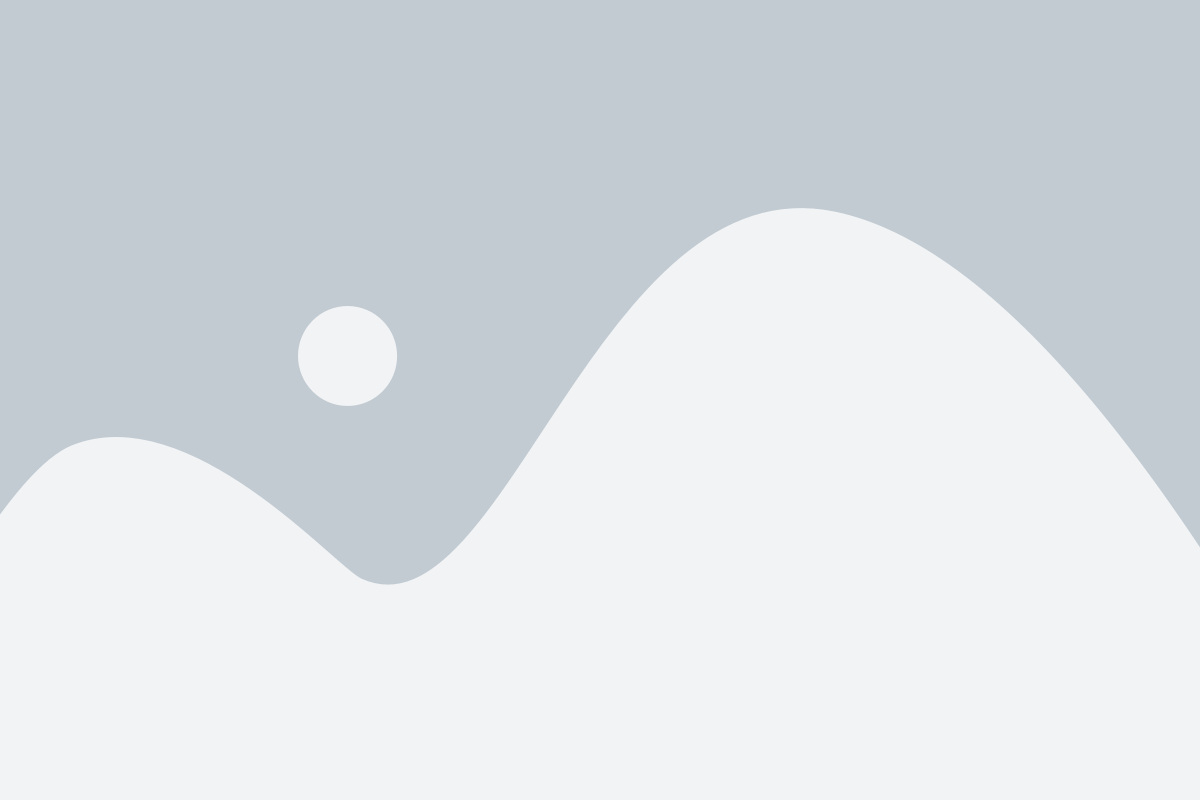
Induction Heater for Hardening Valve Seats
Valve seats are critical components in internal combustion engines that seal the combustion chamber and ensure efficient engine performance. To increase their durability and wear resistance, valve seats are hardened using induction heating. The process involves heating the valve seats to a specific temperature, usually between 800°C to 900°C, followed by quenching them in a bath of oil or water. An induction heater for hardening valve seats utilizes a high-frequency electromagnetic field to generate heat in the metal. This process is more efficient than traditional heating methods, such as gas or electric furnaces. Induction heating is more accurate and faster, allowing for precise control over the heating process and reducing the risk of distortion or cracking in the valve seats.
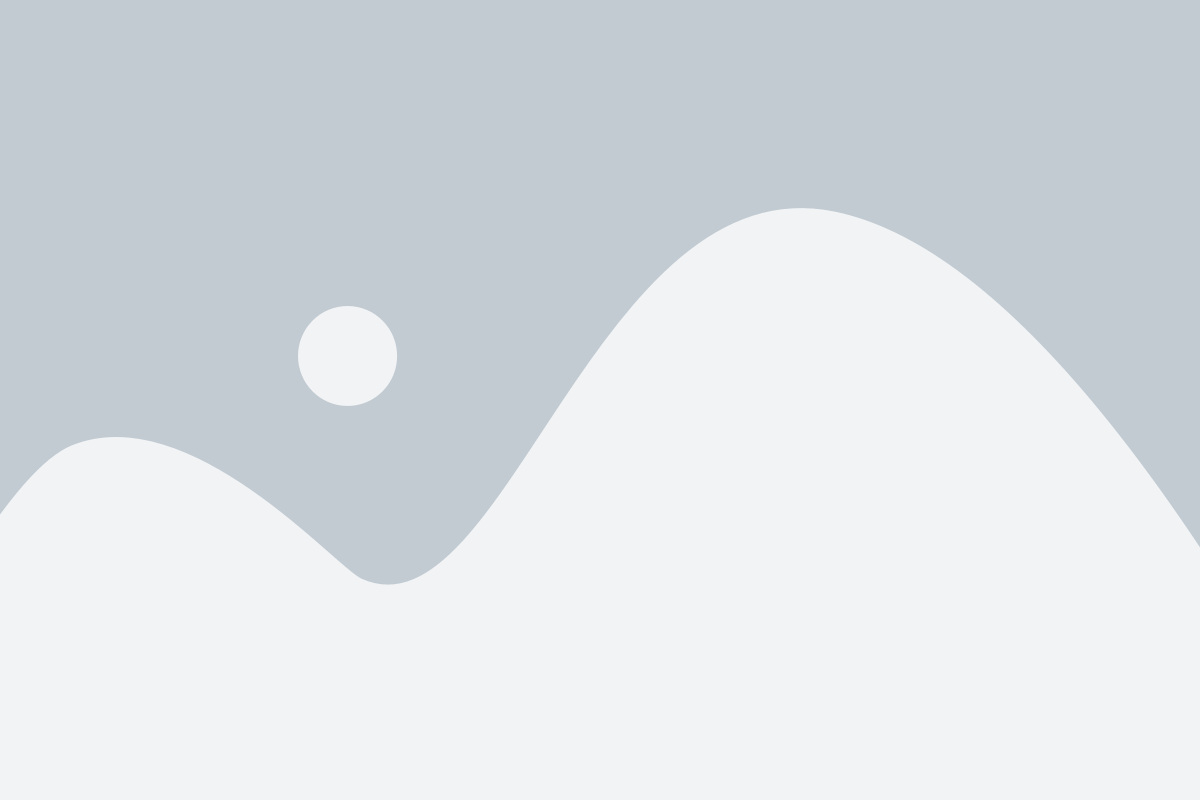
Induction Heater for Hardening Brake Discs
Brake discs are critical components in automotive braking systems that provide the necessary friction to slow down or stop the vehicle. To increase their durability and wear resistance, brake discs are hardened using induction heating. The process involves heating the brake discs to a specific temperature, usually between 800°C to 900°C, followed by quenching them in a bath of oil or water. An induction heater for hardening brake discs utilizes a high-frequency electromagnetic field to generate heat in the metal. This process is more efficient than traditional heating methods, such as gas or electric furnaces. Induction heating is more accurate and faster, allowing for precise control over the heating process and reducing the risk of distortion or cracking in the brake discs.
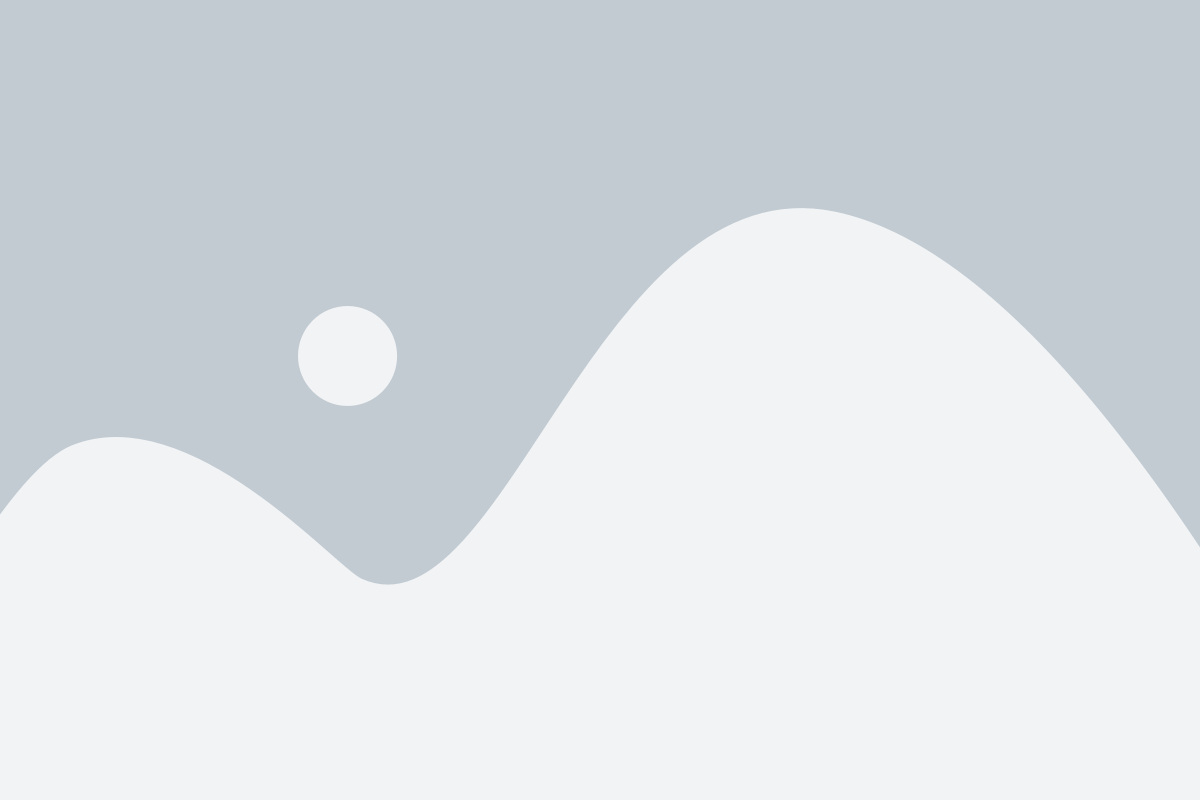
Induction heater for Hardening Piston Rings
Piston rings are a crucial component in an internal combustion engine as they create a seal between the piston and the cylinder wall, preventing combustion gases from escaping. Induction hardening is used to harden the outer surface of the piston ring, making it more wear-resistant and durable. The process involves heating the ring to a high temperature using an induction heater and then rapidly cooling it, which causes the surface to harden.
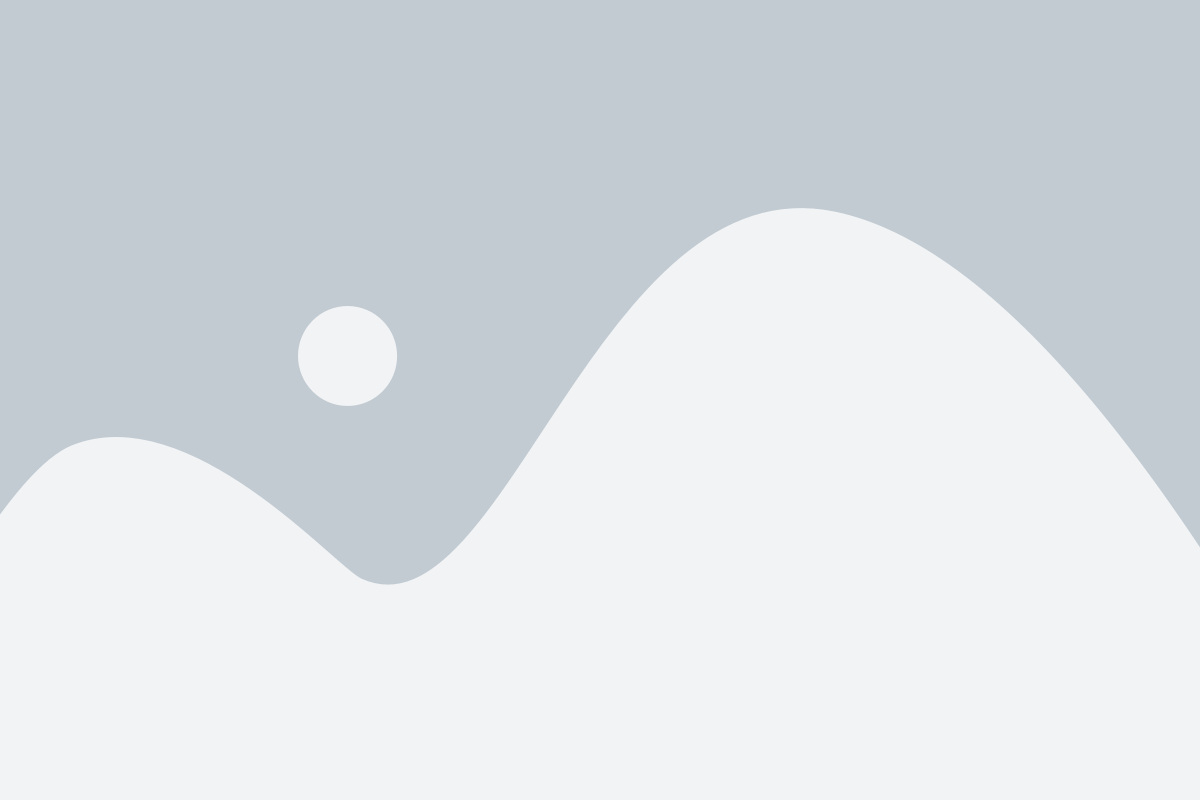
Induction heater for Hardening Sprockets:
Sprockets are used in various machines and equipment to transmit power from one part to another. Induction hardening is used to harden the teeth of sprockets, making them more wear-resistant and durable. The process involves heating the teeth of the sprocket to a high temperature using an induction heater and then rapidly cooling them, which causes the surface to harden.
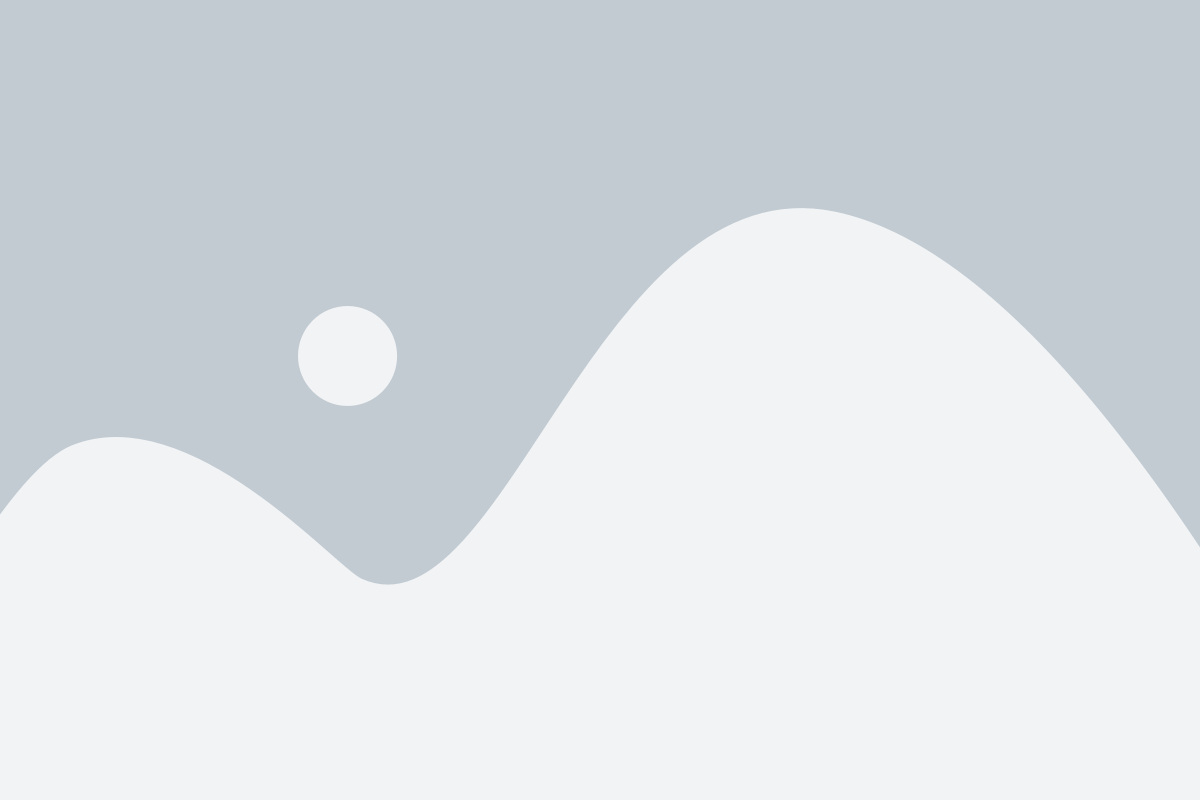
Induction heater for Hardening Transmission Components
Transmission components such as gears and shafts are subject to a lot of stress and need to be strong and durable. Induction hardening is used to increase the strength of these components by heating them to a high temperature using an induction heater and then rapidly cooling them. This causes the surface of the components to harden, making them more resistant to wear and damage.
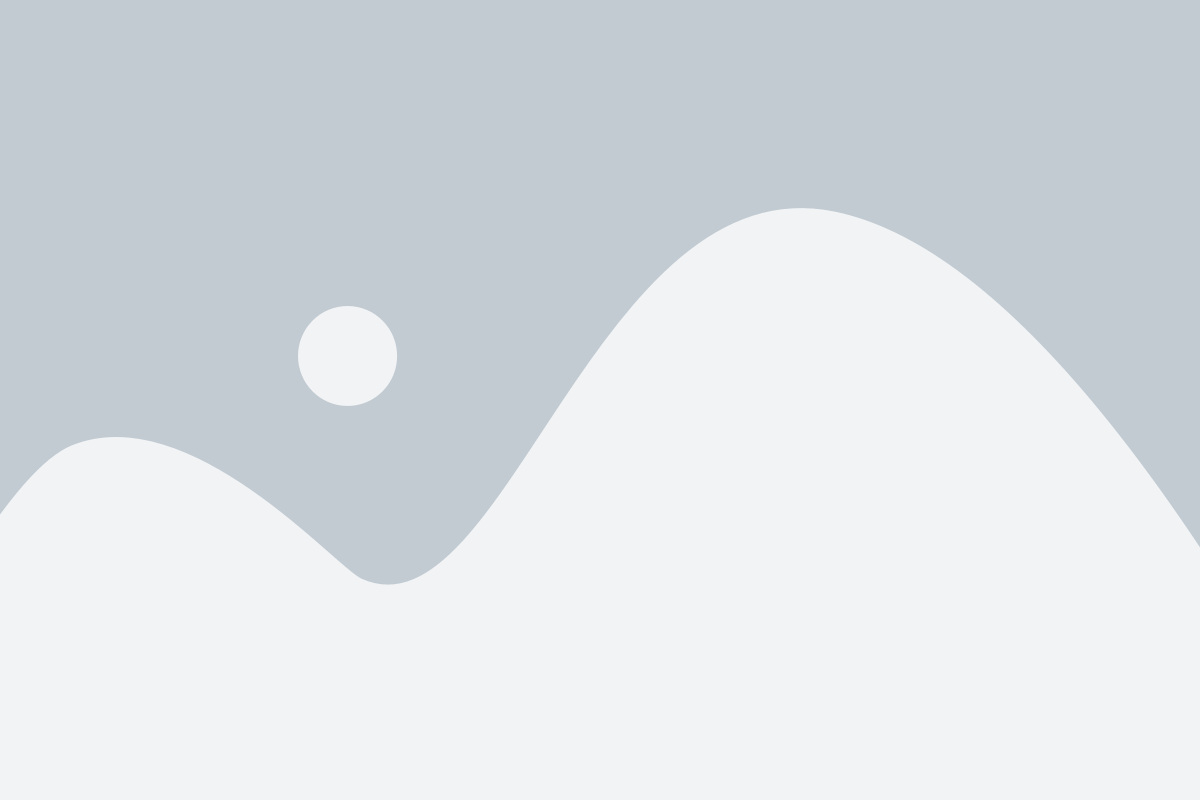
Induction heater for Hardening Pump Components
Pump components such as impellers and shafts are subject to a lot of stress and need to be strong and durable. Induction hardening is used to increase the strength of these components by heating them to a high temperature using an induction heater and then rapidly cooling them. This causes the surface of the components to harden, making them more resistant to wear and damage.
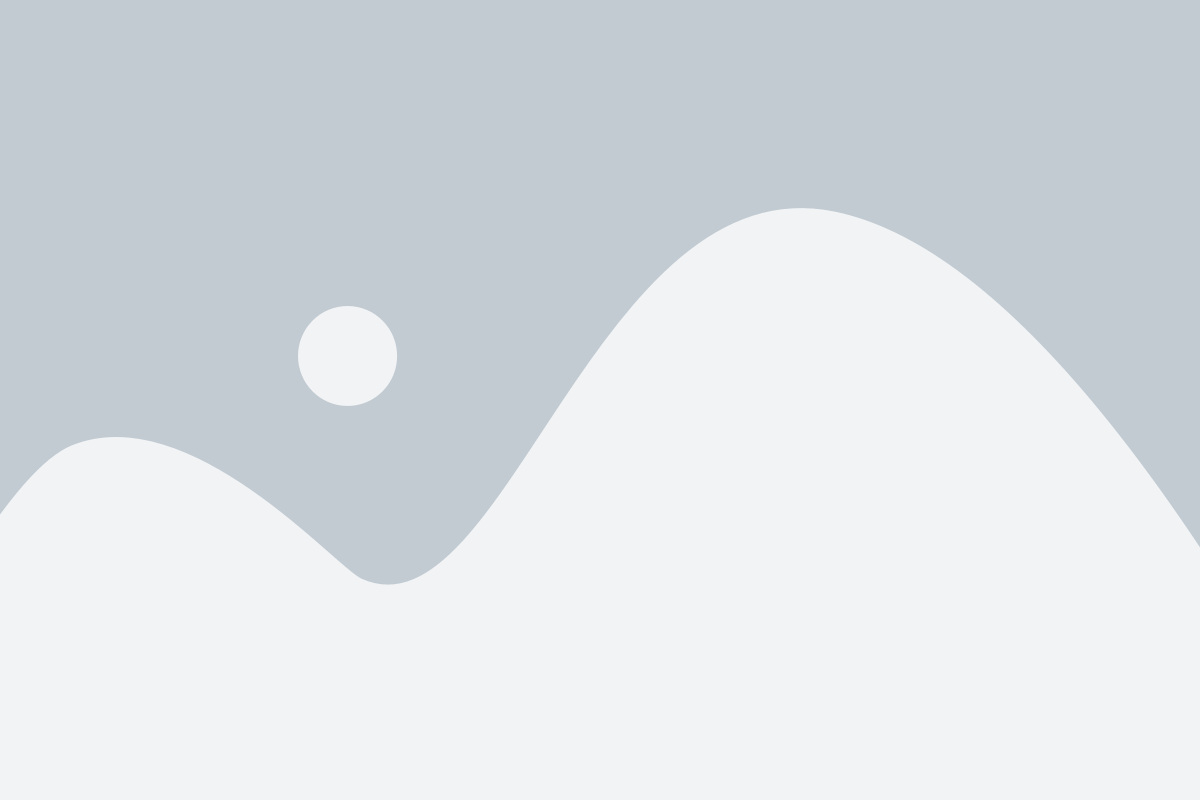
Induction heater for Hardening Engine Components
Various engine components such as camshafts, crankshafts, and valve seats can be hardened using induction heating. The process involves heating the components to a high temperature using an induction heater and then rapidly cooling them. This causes the surface of the components to harden, making them more wear-resistant and durable.
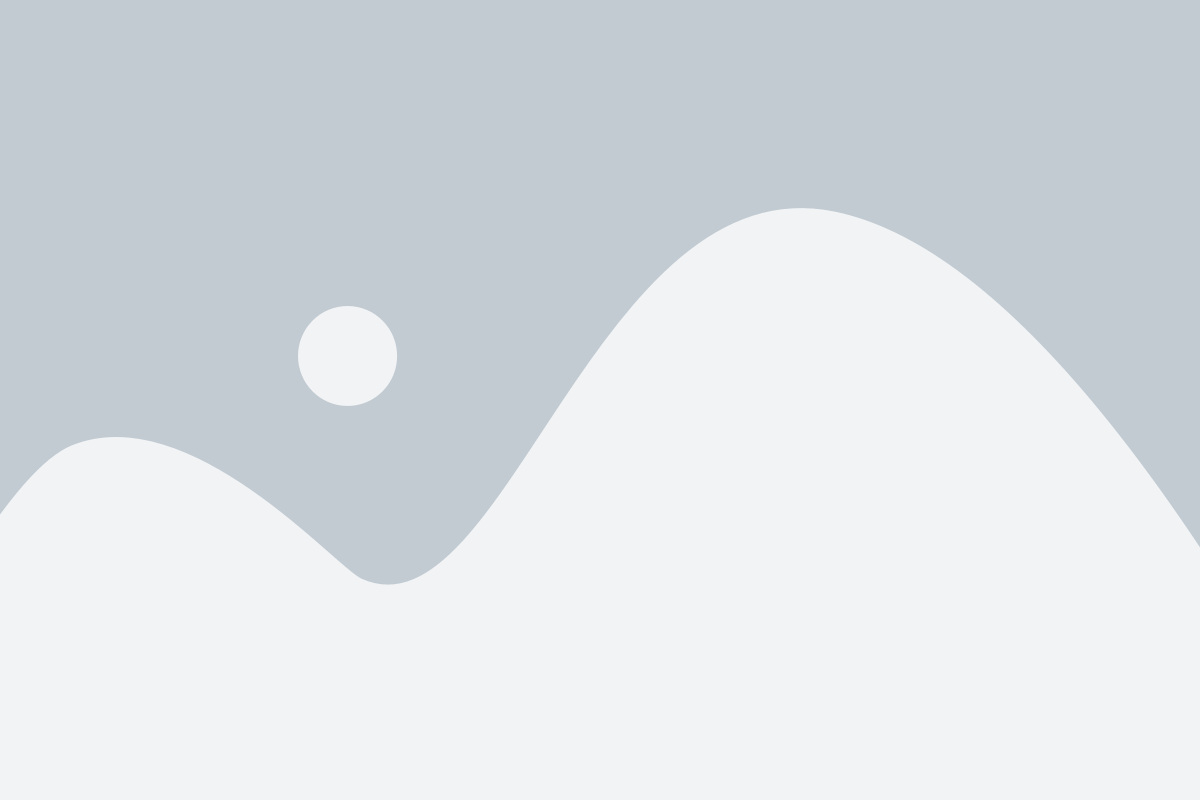
Induction heater for Hardening Cutting Tools
Cutting tools such as drills, taps, and milling cutters need to be hard and wear-resistant to be effective. Induction hardening is used to harden the cutting edges of these tools by heating them to a high temperature using an induction heater and then rapidly cooling them. This causes the cutting edges to harden, making them more effective and durable.
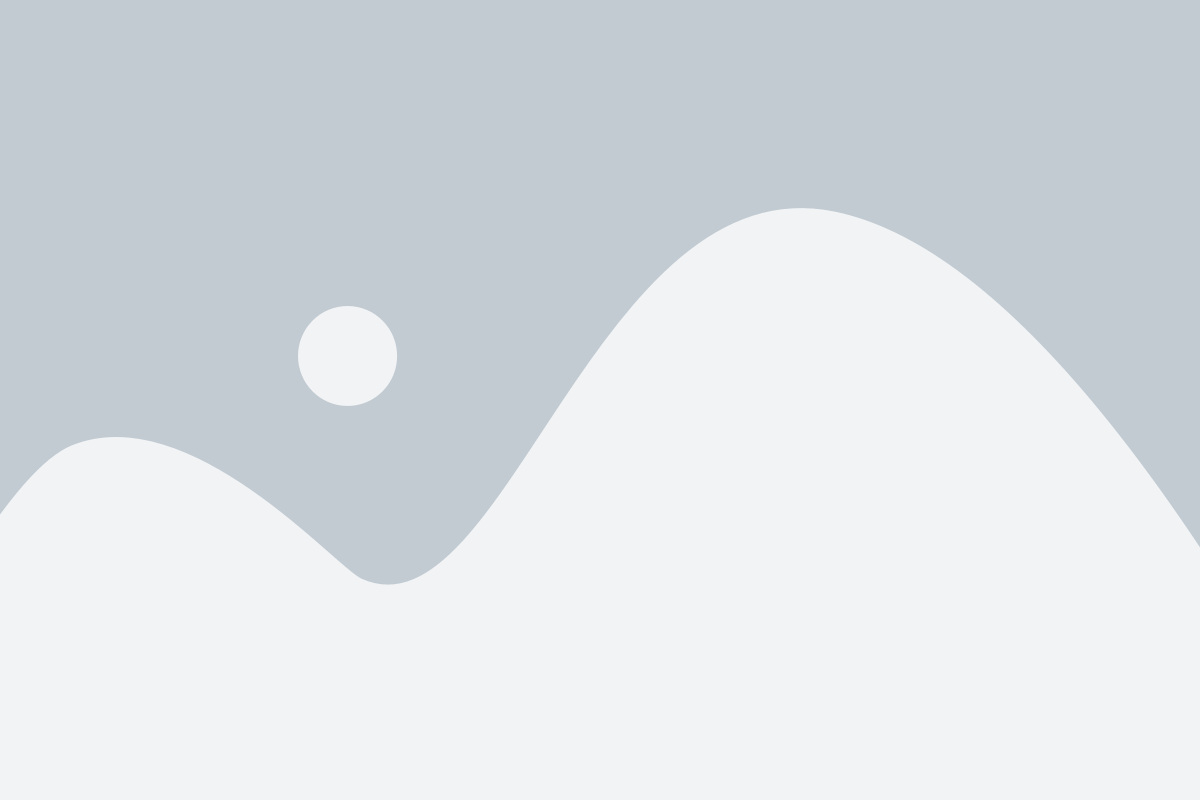
Induction heater for Hardening Rollers
Rollers are used in various machines and equipment to transmit power from one part to another. Induction hardening is used to harden the surface of the rollers, making them more wear-resistant and durable. The process involves heating the rollers to a high temperature using an induction heater and then rapidly cooling them, which causes the surface to harden.
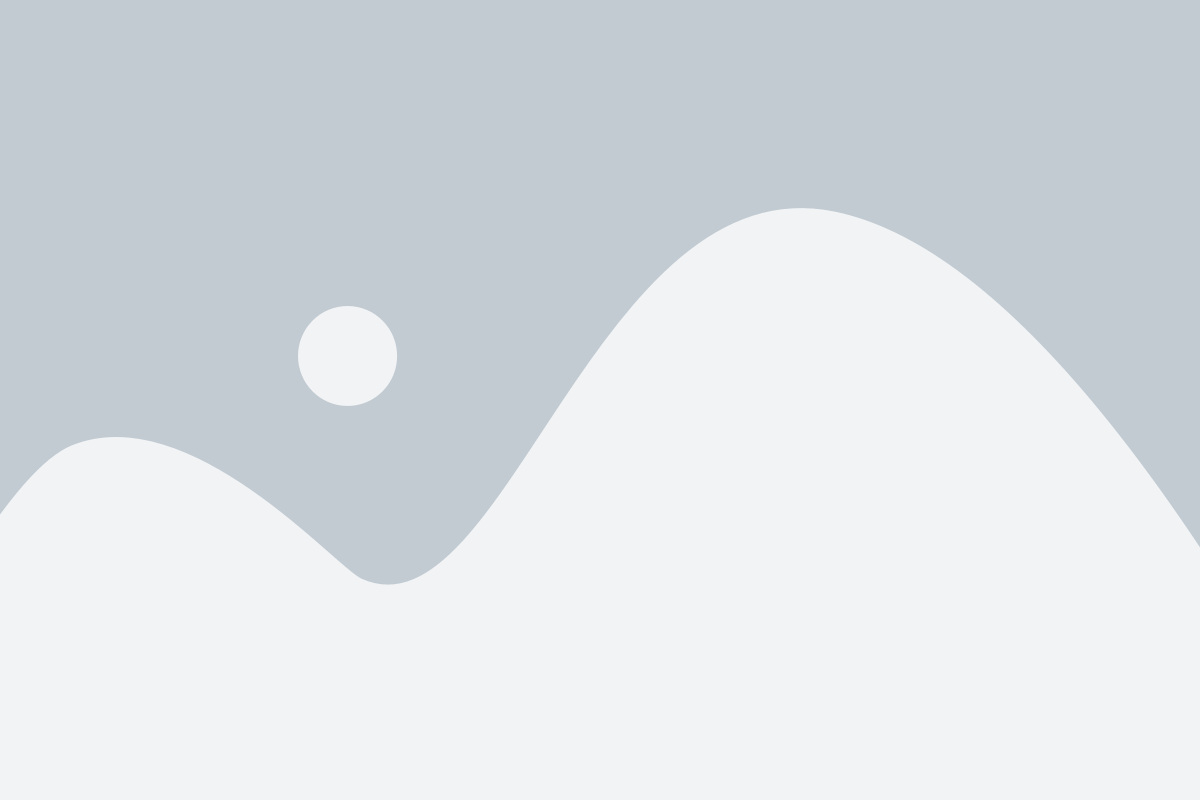
Induction heater for Hardening Pins and Bolts
Pins and bolts are used in various machines and equipment to hold parts together. Induction hardening is used to harden the surface of the pins and bolts, making them more wear-resistant and durable. The process involves heating the pins and bolts to a high temperature using an induction heater and then rapidly cooling them, which causes the surface to harden.
Induction Heaters Offered by GM Industries
For more information on any of our high quality products or getting accurate prices contact GM Industries at
Call Us
+(91)-9820533489 / 7738562224
Enquiry Form
Submit
Frequently Asked Questions
An induction heater is used to heat up the metal parts quickly and efficiently, allowing for precise control of the hardening process.
An induction heater uses electromagnetic energy to create heat within the metal part. The high-frequency current generates heat directly within the workpiece.
Induction heating can be used to harden a variety of ferrous and non-ferrous materials, including steel, stainless steel, aluminum, brass, and copper.
Induction heaters have a limited depth of hardening, making it unsuitable for some applications that require a deeper hardening depth.
Yes, induction heating is commonly used for surface hardening of metals to improve wear resistance.
Yes, induction hardening is an environmentally friendly process as it does not produce harmful emissions or waste products.
The time required to harden metal using an induction heater varies depending on the material and the required hardness level. However, it is typically faster than traditional heating methods.
Yes, induction heaters can be used to harden small parts, making them suitable for a wide range of applications.
The maximum size of parts that can be hardened using an induction heater depends on the capacity of the equipment. Large parts can be hardened using custom-built induction heating systems.
Induction hardening can cause distortion in the parts being hardened, especially in thin-walled parts or parts with uneven cross-sections. However, this can be minimized by careful control of the heating process.
Yes, induction heaters can be used for batch hardening of parts, making them a cost-effective solution for high-volume production.
Yes, induction heating provides precise temperature control, making it an ideal choice for precision forging.
Induction hardening offers better control of the hardening process, resulting in more consistent and precise results than flame hardening. It is also more energy-efficient and produces less distortion in the parts being hardened.
The cost of an induction heater for hardening varies depending on the size and capacity of the equipment. Custom-built systems can be more expensive than off-the-shelf systems.
Yes, induction heaters can be used to harden parts with complex shapes, as the heating process can be precisely controlled to avoid overheating or under heating of specific areas.
Induction hardening is a surface hardening process that only hardens the surface layer of the part. Case hardening, on the other hand, involves hardening the entire part.
Yes, regular maintenance and calibration are important to ensure the continued effectiveness and accuracy of an induction heating system used for hardening.