Induction Heating
What is Heat treatment?
Heat treatment is a process of heating and cooling a material to modify its properties. The purpose of heat treatment is to change the physical and/or chemical properties of a material, such as its hardness, strength, ductility, or toughness. This is done by heating the material to a specific temperature, holding it at that temperature for a certain amount of time, and then cooling it at a controlled rate. Heat treatment can be used on a variety of materials, including metals, and alloys. Heat treatment is used in a wide range of industries, such as manufacturing, construction, and aerospace. It can be used to improve the properties of a material, make it more resistant to wear and tear, or to enhance its performance in specific applications.
The most common method used for heat treating is conventional furnace heating. This involves heating the material in a furnace at a specific temperature for a set amount of time, followed by controlled cooling. Induction heating is also a popular method for heat treating, particularly for certain types of materials. Induction heating works by using an electromagnetic field to heat the material, rather than a direct flame or hot air.
Why Induction Heater is used for Heating Processes?
Induction heating heats the material directly, without the need for a heat transfer medium, such as air or water. This means that there is no heat lost to the surrounding environment, resulting in faster heating times and lower energy costs. Furthermore, induction heating provides precise and localized heating. The heat is generated within the material itself, allowing for greater control over the heating process. This can be especially useful when working with materials that are sensitive to temperature changes or require specific heating profiles. Thirdly, induction heating can be used to heat a wide variety of materials, including metal and composites. It can also be used to heat materials with complex shapes or geometries, as the heat can be focused precisely where it is needed. Overall, induction heating is a versatile and efficient method for heating processes, with a range of advantages over other heating methods.
Introduction to Industrial Induction Heater for Heating
Industrial induction heaters are widely used for heating processes in various industries. An induction heater works by generating an alternating electromagnetic field, which induces eddy currents within the material being heated. These currents cause the material to heat up rapidly and uniformly, without the need for a heat transfer medium, such as air or water. One of the main advantages of industrial induction heaters is their efficiency. They can provide fast and precise heating, with minimal energy loss to the surrounding environment. This can result in significant cost savings for industrial processes, as well as improved productivity and quality. Overall, industrial induction heaters are an important tool in many industrial processes, providing efficient and precise heating for a variety of materials and applications. GM Industries is a leading provider of industrial induction heaters for heat treatment processes. We offer a range of products designed to meet the specific needs of various industries, including automotive, aerospace, and manufacturing. GM Industries is committed to meet the unique needs of their clients and providing customized solutions to help them achieve their goals.
Advantages of Using an Industrial Induction Heater for Heating
There are several advantages to using an industrial induction heater for heating processes:
Energy Efficiency
Industrial induction heaters are highly efficient as they directly heat the material being processed, without any heat loss to the surrounding environment. This results in lower energy consumption and reduced operating costs.
Precise and Controlled Heating
Industrial induction heaters can provide precise and controlled heating, allowing for accurate temperature control and consistent results. This can be especially important for materials that are sensitive to temperature changes or require specific heating profiles.
Adaptability
Industrial induction heaters can be used to heat a wide range of materials, including metals, and composites as well as materials with complex shapes or geometries.
Reduced Heating Time
Industrial induction heaters can heat materials quickly, reducing overall processing time and improving productivity.
Improved Safety
Unlike other heating methods, such as open flames or hot surfaces, industrial induction heaters do not generate hazardous fumes or flames, making them a safer option for heating processes.
Overall, industrial induction heaters offer several advantages over other heating methods, including energy efficiency, precise and controlled heating, versatility, reduced heating time, and improved safety.
Induction Heater for Various Heating Process
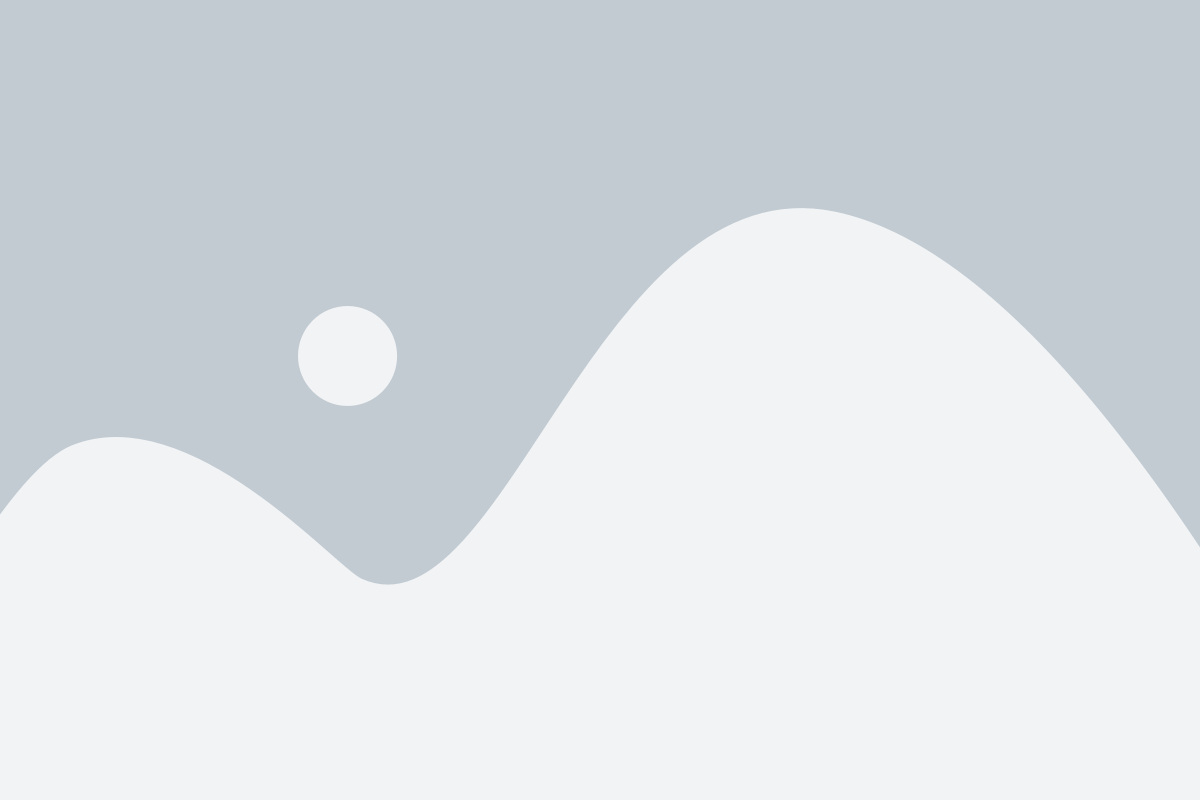
Induction Heater for Heat Treating Gears
Gears are essential components used in various mechanical systems to transmit power and motion between rotating shafts. Heat treatment is necessary to enhance the strength, hardness, and wear resistance of gears. The heat treatment process involves heating the gear to a specific temperature and then rapidly cooling it to harden the material. Induction heating is an efficient and precise method for heating gears in the heat treatment process. The induction heater uses electromagnetic fields to heat the gear uniformly and rapidly, which reduces distortion and improves the quality of the final product. Using an induction heater for heat treating gears is important because it increases productivity, reduces energy consumption, and improves the quality of the final product.
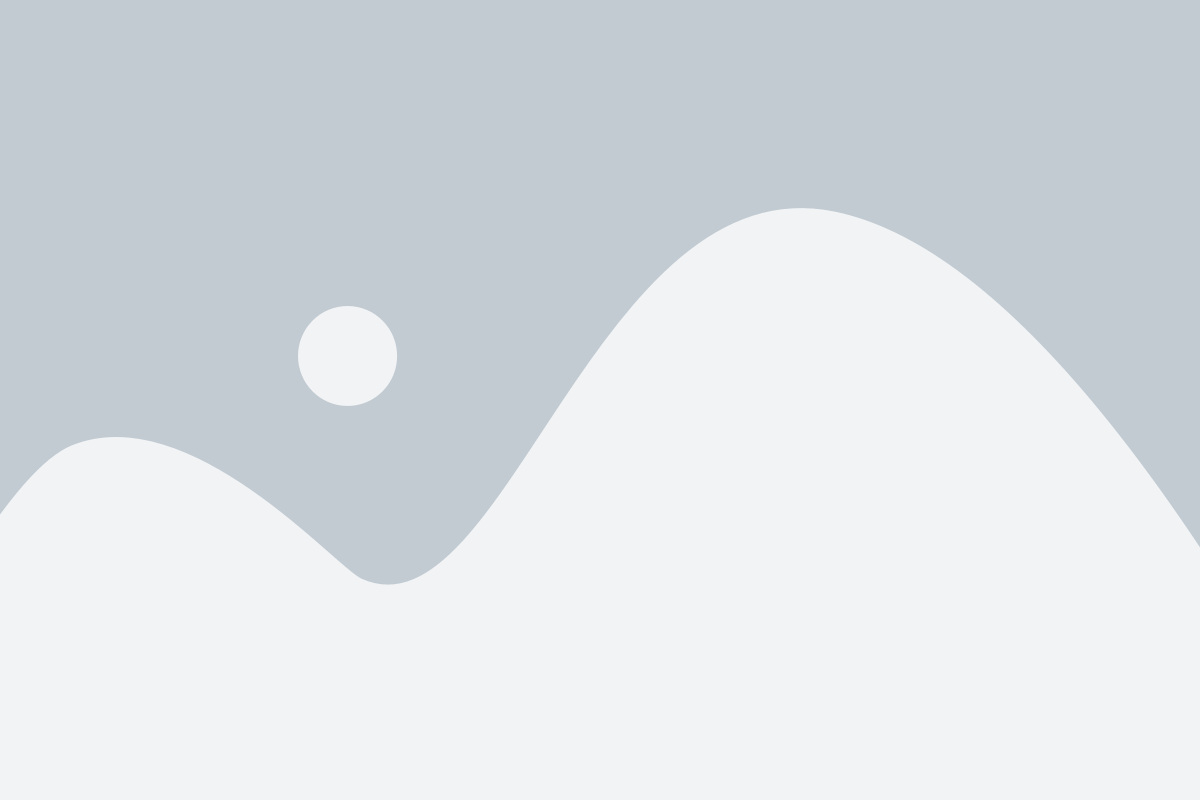
Induction Heater for Heat Treating Shafts
Shafts are essential components used in various mechanical systems to transmit torque and motion between rotating elements. Heat treatment is necessary to enhance the strength, hardness, and wear resistance of shafts. The heat treatment process involves heating the shaft to a specific temperature and then rapidly cooling it to harden the material. Induction heating is an efficient and precise method for heating shafts in the heat treatment process. The induction heater uses electromagnetic fields to heat the shaft uniformly and rapidly, which reduces distortion and improves the quality of the final product. Using an induction heater for heat treating shafts is important because it increases productivity, reduces energy consumption, and improves the quality of the final product.
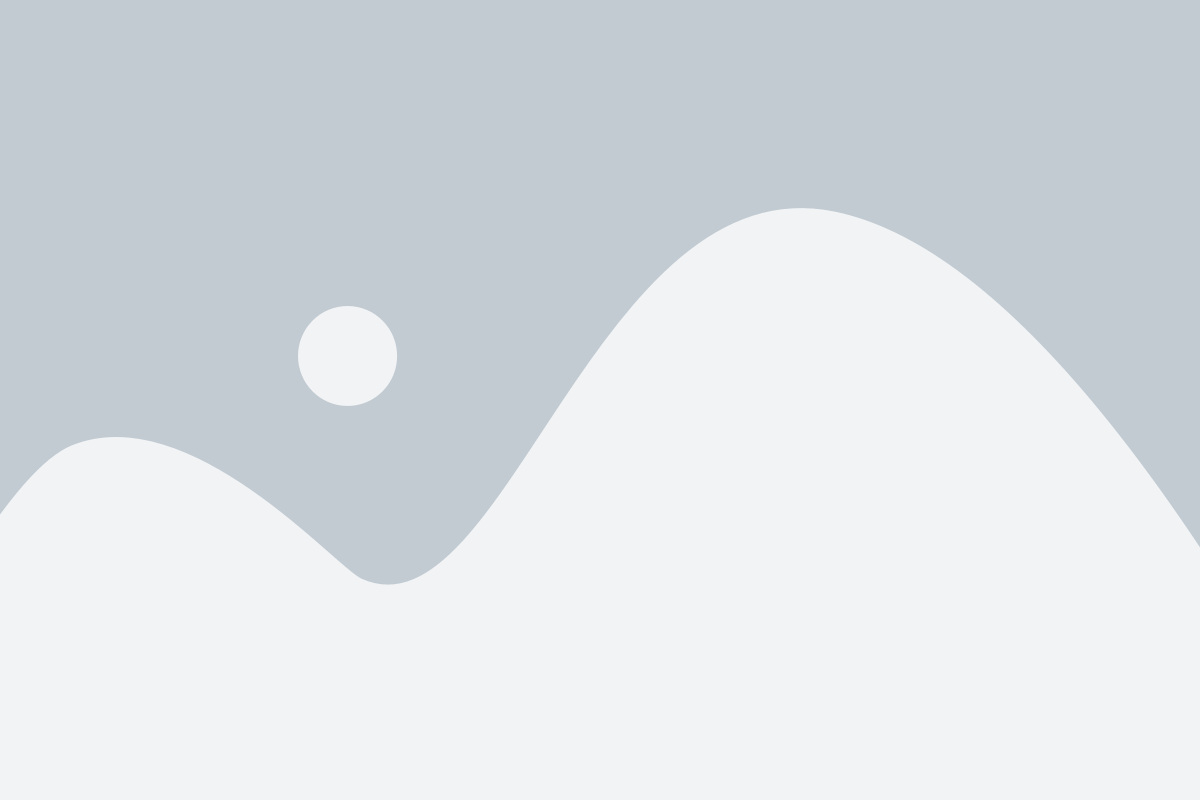
Induction Heater for Heat Treating Bearings
Bearings are essential components used in various mechanical systems to reduce friction between moving parts. Heat treatment is necessary to enhance the hardness and wear resistance of bearings. The heat treatment process involves heating the bearing to a specific temperature and then rapidly cooling it to harden the material. Induction heating is an efficient and precise method for heating bearings in the heat treatment process. The induction heater uses electromagnetic fields to heat the bearing uniformly and rapidly, which reduces distortion and improves the quality of the final product. Using an induction heater for heat treating bearings is important because it increases productivity, reduces energy consumption, and improves the quality of the final product.
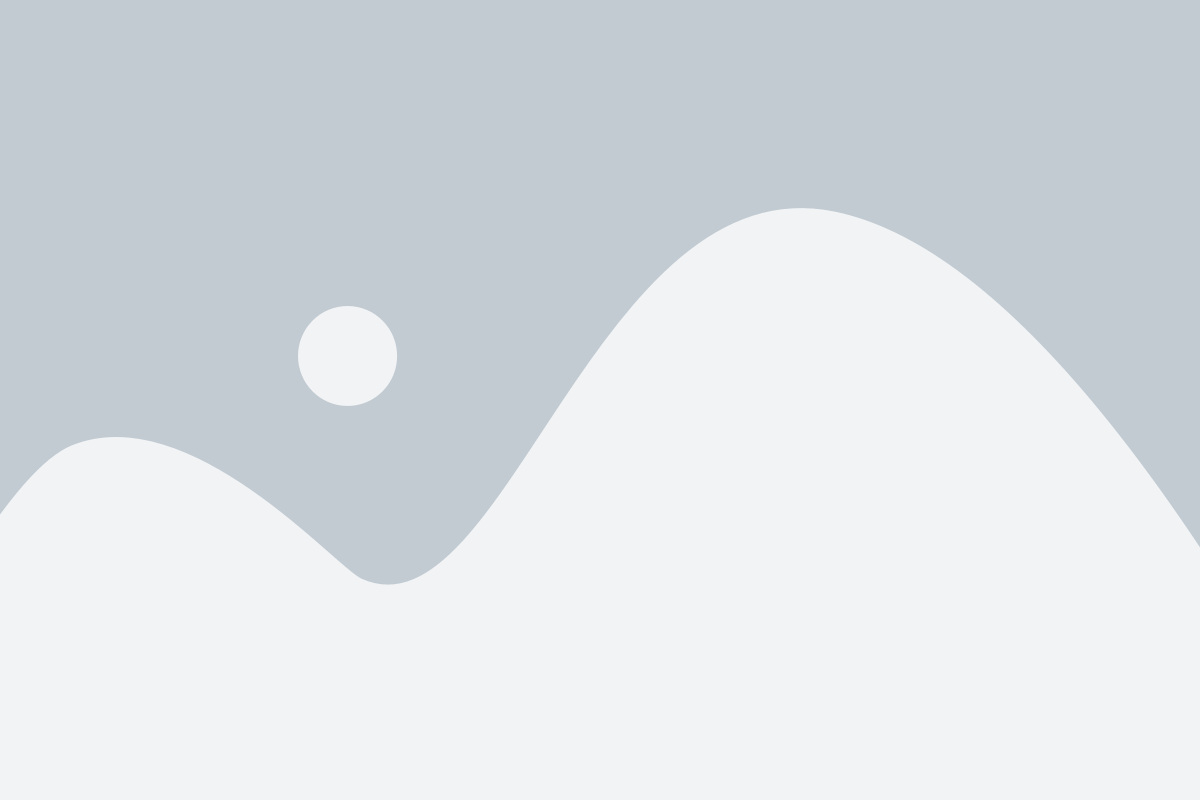
Induction Heater for Heat Treating Engine Parts
Engine parts are essential components used in various mechanical systems to convert fuel into mechanical energy. Heat treatment is necessary to enhance the strength, hardness, and wear resistance of engine parts. The heat treatment process involves heating the engine part to a specific temperature and then rapidly cooling it to harden the material. Induction heating is an efficient and precise method for heating engine parts in the heat treatment process. The induction heater uses electromagnetic fields to heat the engine part uniformly and rapidly, which reduces distortion and improves the quality of the final product. Using an induction heater for heat treating engine parts is important because it increases productivity, reduces energy consumption, and improves the quality of the final product.
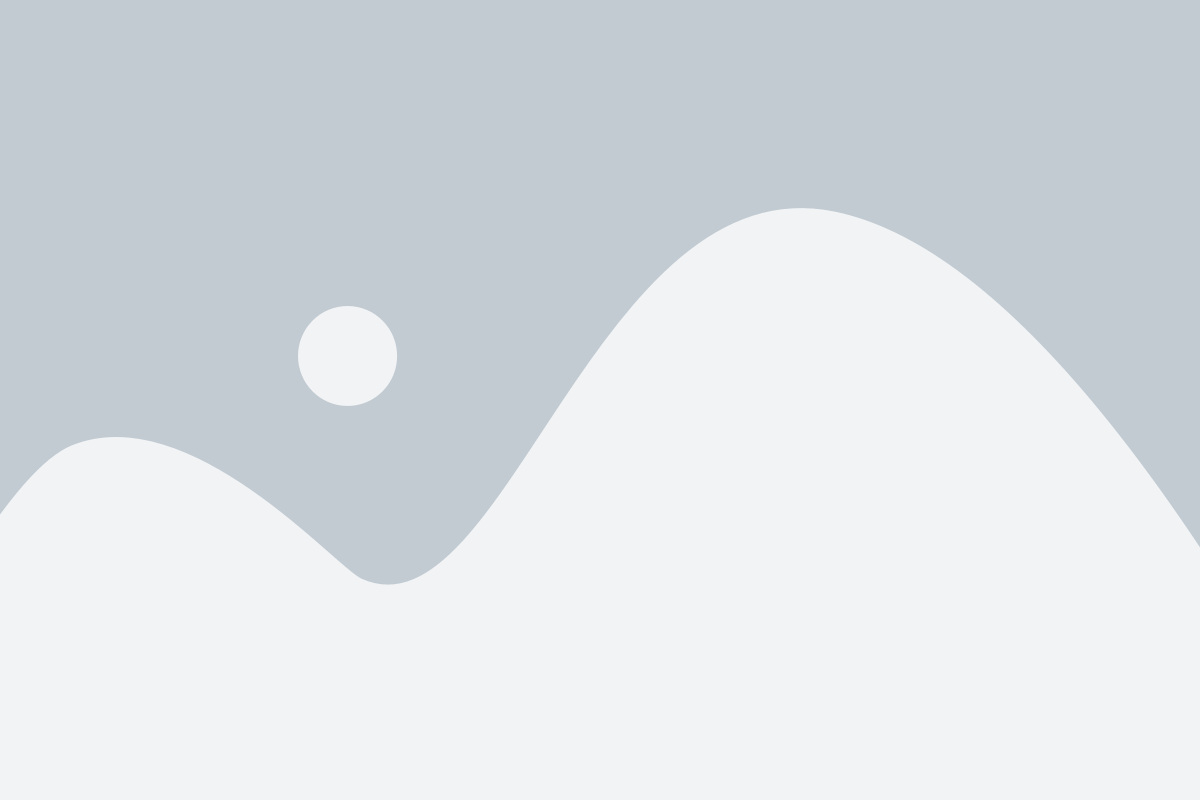
Induction Heater for Heat Treating Machine Tools
Machine tools are essential components used in various manufacturing processes to shape, cut, and form materials into precise shapes and sizes. Heat treatment is necessary to enhance the hardness and wear resistance of machine tools. The heat treatment process involves heating the tool to a specific temperature and then rapidly cooling it to harden the material. Induction heating is an efficient and precise method for heating machine tools in the heat treatment process. The induction heater uses electromagnetic fields to heat the tool uniformly and rapidly, which reduces distortion and improves the quality of the final product. Using an induction heater for heat treating machine tools is important because it increases productivity, reduces energy consumption, and improves the quality of the final product.
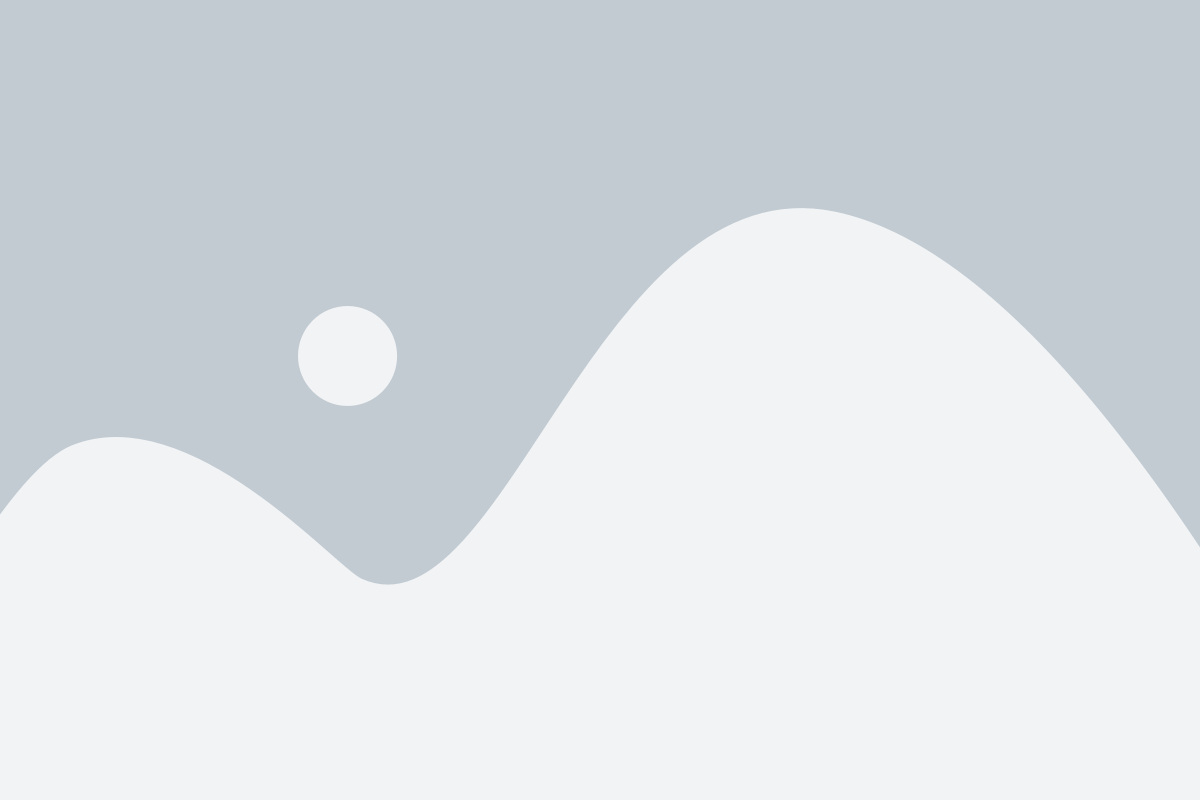
Induction Heater for Heat Treating Cutting Tools
Cutting tools are used in various industries such as manufacturing, construction, and aerospace to shape and cut materials. These tools are made of high-speed steel or carbide, which requires precise heat treatment to ensure they have the necessary hardness and toughness. Induction heaters are used for heat treating cutting tools due to their ability to provide precise and uniform heating. The process involves heating the cutting tool to a specific temperature, holding it at that temperature for a set amount of time, and then quenching it to rapidly cool it down. This process helps to increase the tool’s hardness and wear resistance, resulting in longer tool life and improved performance.
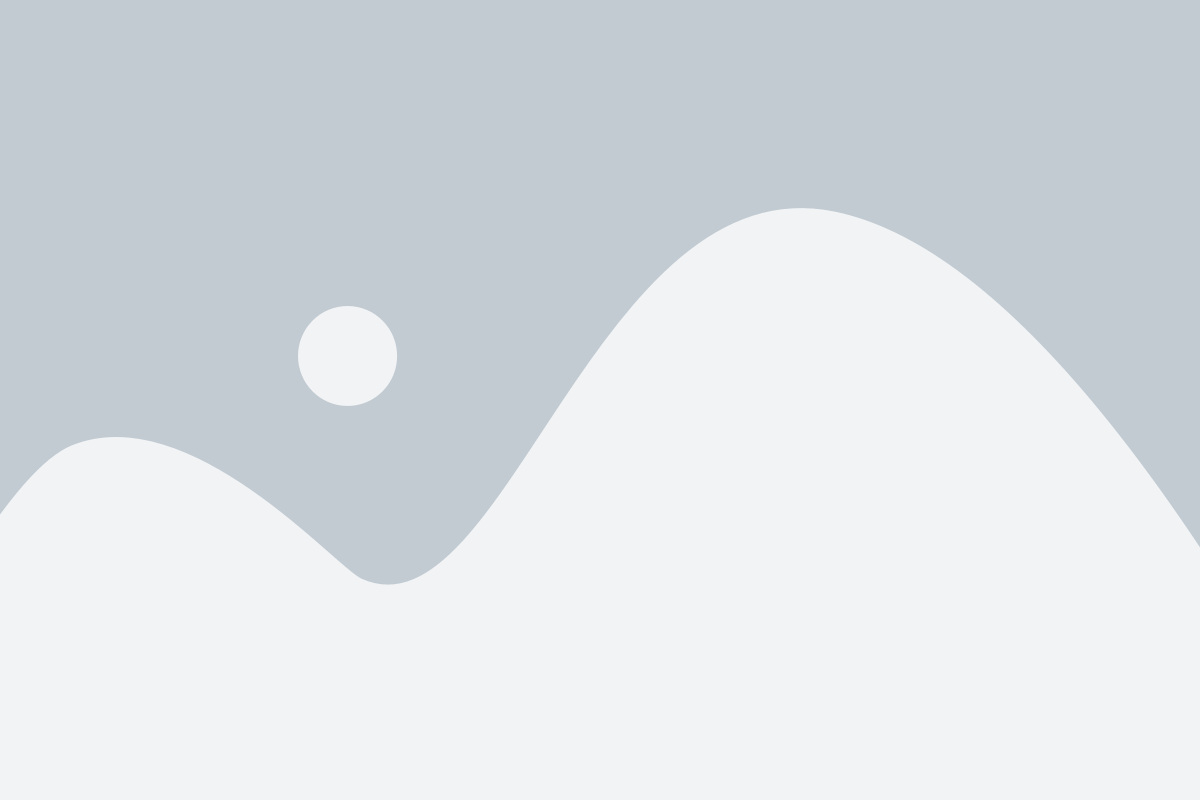
Induction Heater for Heat Treating Fasteners
Fasteners, such as bolts, nuts, and screws, are used to join two or more parts together in various industries. Heat treating these fasteners is necessary to increase their strength, hardness, and wear resistance. Induction heaters are used for heat treating fasteners due to their ability to provide rapid and precise heating. The process involves heating the fastener to a specific temperature, holding it at that temperature for a set amount of time, and then quenching it to rapidly cool it down. This process helps to increase the fastener’s strength and durability, resulting in improved performance and reliability.
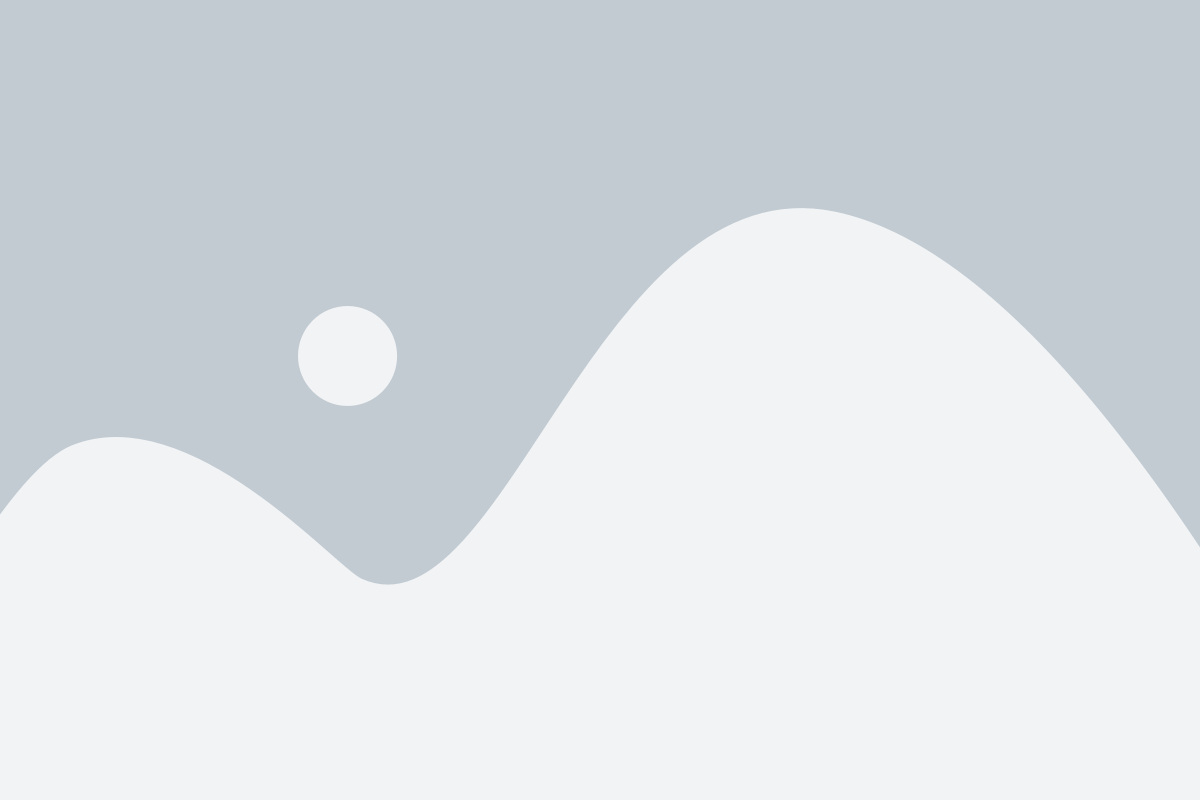
Induction Heater for Heat Treating Springs
Springs are used in various industries, including manufacturing, construction, and aerospace, to absorb and store energy. Heat treating springs is necessary to ensure they have the necessary strength, durability, and elasticity. Induction heaters are used for heat treating springs due to their ability to provide precise and uniform heating. The process involves heating the spring to a specific temperature, holding it at that temperature for a set amount of time, and then quenching it to rapidly cool it down. This process helps to increase the spring’s strength and durability, resulting in improved performance and reliability.
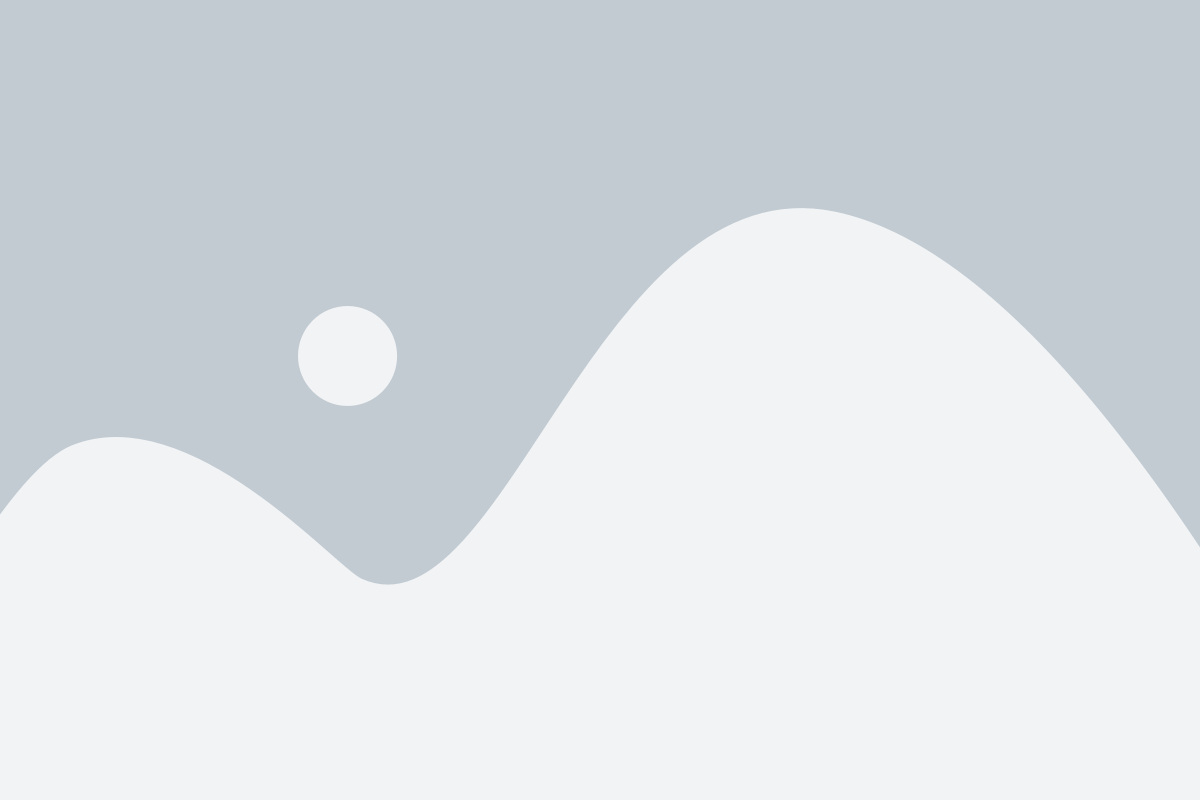
Induction Heater for Heat Treating Steel Beams
Steel beams are used in construction and manufacturing industries to support and bear heavy loads. Heat treating steel beams is necessary to improve their strength and durability. Induction heaters are used for heat treating steel beams due to their ability to provide rapid and precise heating. The process involves heating the steel beam to a specific temperature, holding it at that temperature for a set amount of time, and then cooling it down. This process helps to increase the steel beam’s strength and durability, resulting in improved performance and reliability.
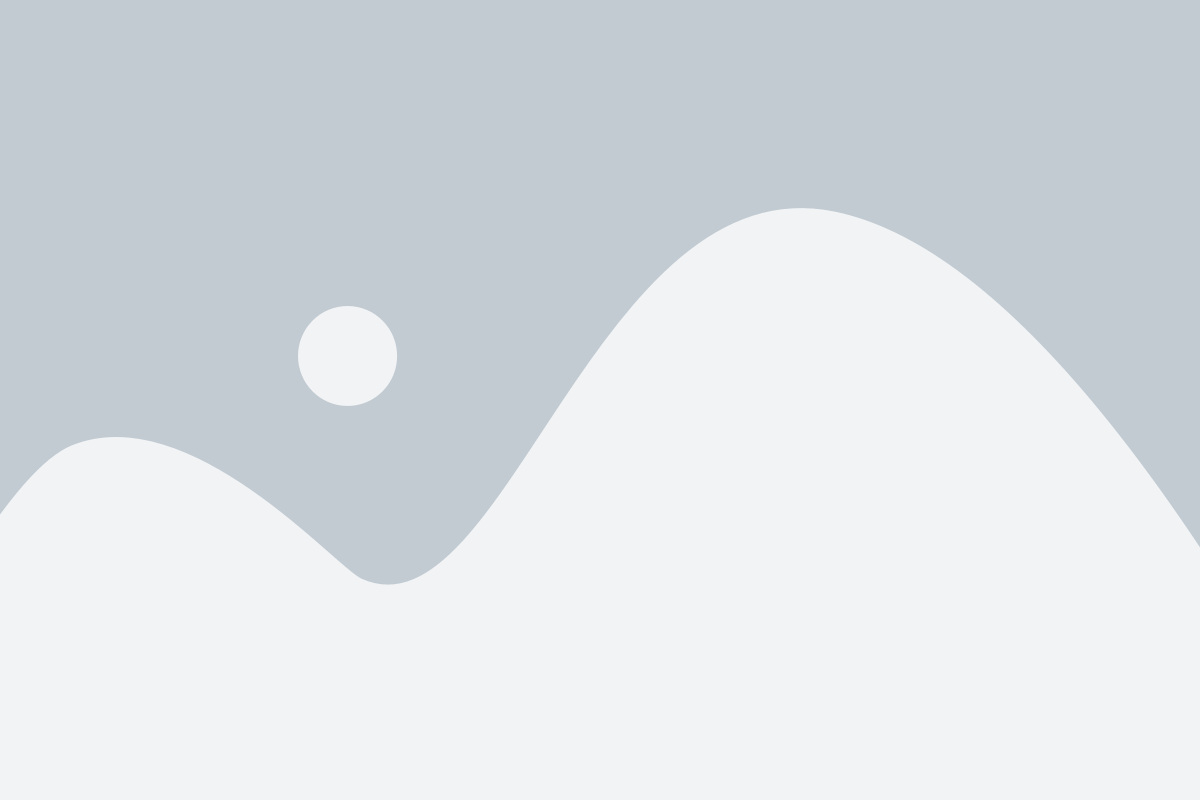
Induction Heater for Heat Treating Structural Components
Structural components, such as frames, brackets, and supports, are used in various industries to provide structural support and stability. Heat treating these components is necessary to increase their strength and durability. Induction heaters are used for heat treating structural components due to their ability to provide rapid and precise heating. The process involves heating the component to a specific temperature, holding it at that temperature for a set amount of time, and then cooling it down. This process helps to increase the component’s strength and durability, resulting in improved performance and reliability.
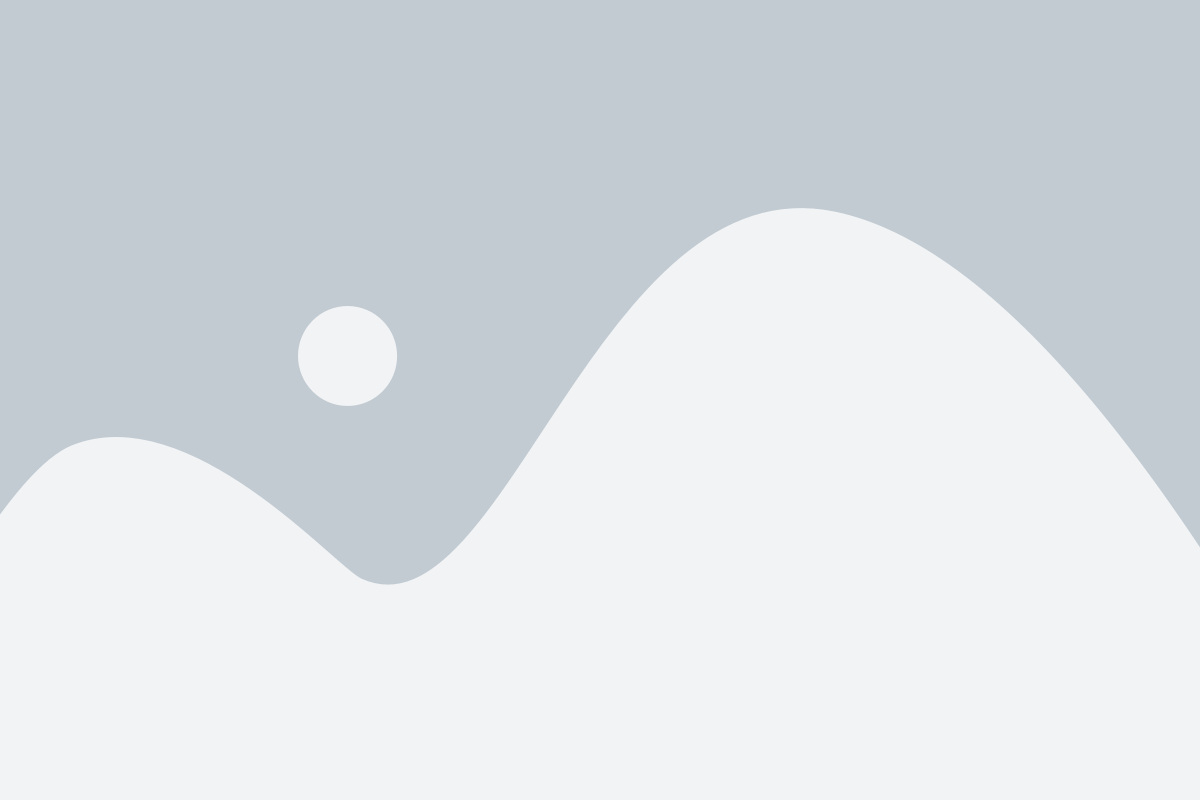
Induction Heater for Heat Treating Reinforcing Bars
Reinforcing bars, also known as rebar, are used in construction industries to provide structural support and stability in concrete structures. Heat treating reinforcing bars is necessary to increase their strength and durability. Induction heaters are used for heat treating reinforcing bars due to their ability to provide rapid and precise heating. The process involves heating the rebar to a specific temperature, holding it at that temperature for a set amount of time, and then cooling it down. This process helps to increase the rebar’s strength and durability, resulting in improved performance and reliability.
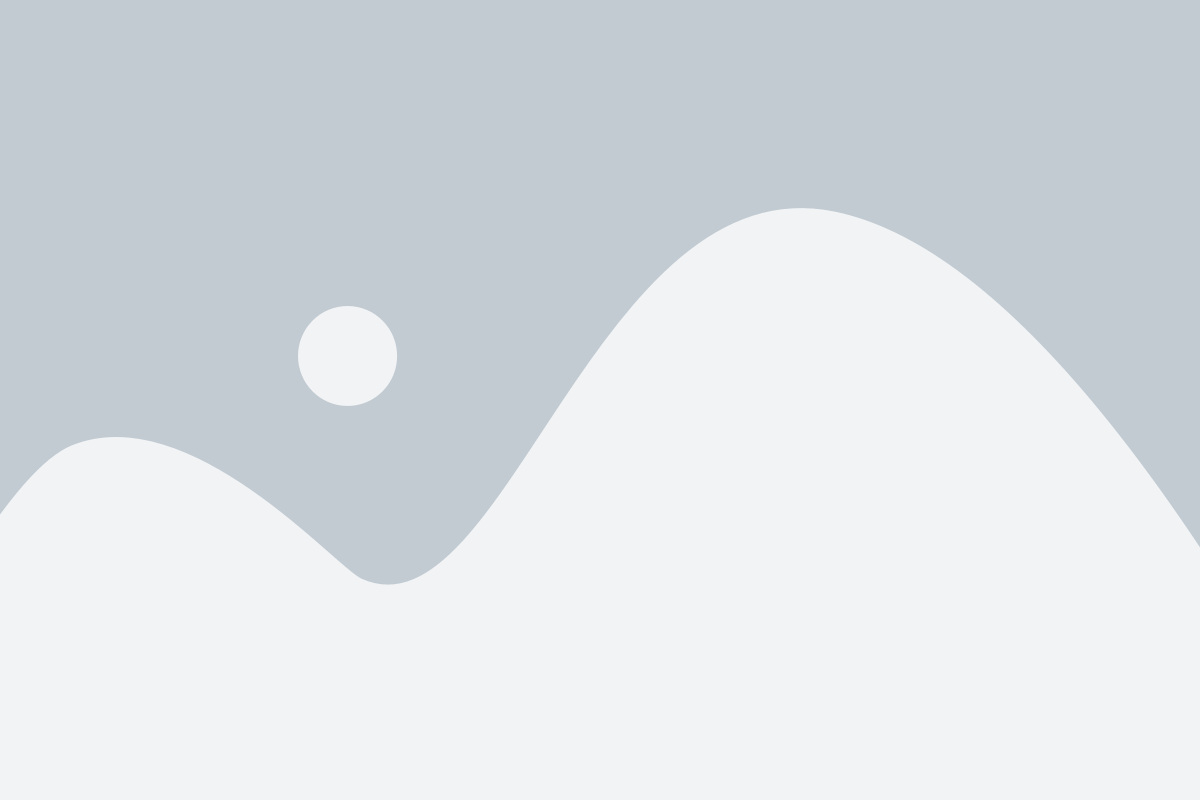
Induction Heater for Heat Treating Pipes and Tubes
Pipes and tubes are widely used in various industries such as oil and gas, chemical processing, and construction. The heat treatment process is essential for improving the strength and durability of these components. Induction heating is a common method used for heat treating pipes and tubes. The process involves heating the pipe or tube using an induction coil, which creates an electromagnetic field that induces electrical current in the material. This current generates heat, causing the material to reach the desired temperature for the heat treatment process. Induction heating is a fast and efficient method for heat treating pipes and tubes, as it allows for precise control of the heating process. This is important for achieving consistent and uniform results. The use of induction heating also reduces the risk of distortion, which can be a common issue in other heating methods.
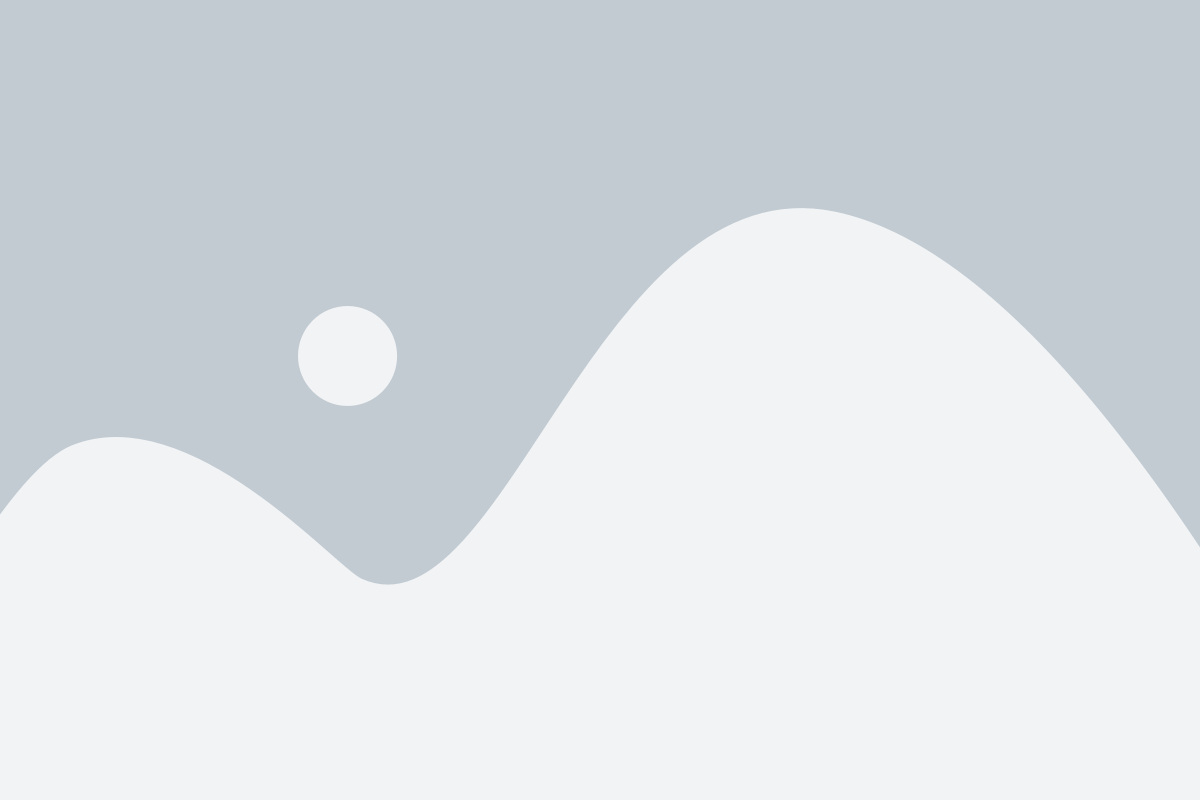
Induction Heater for Heat Treating Welded Assemblies
Welded assemblies are commonly used in manufacturing and construction industries. The heat treatment process is essential for improving the mechanical properties of the weld and reducing residual stress. Induction heating is a widely used method for heat treating welded assemblies. The process involves heating the welded area using an induction coil, which generates heat by inducing electrical current in the material. The heat is applied precisely to the welded area, allowing for localized heat treatment. Induction heating also offers a fast and efficient method for heat treating welded assemblies, as it can achieve the desired temperature quickly and with minimal distortion.
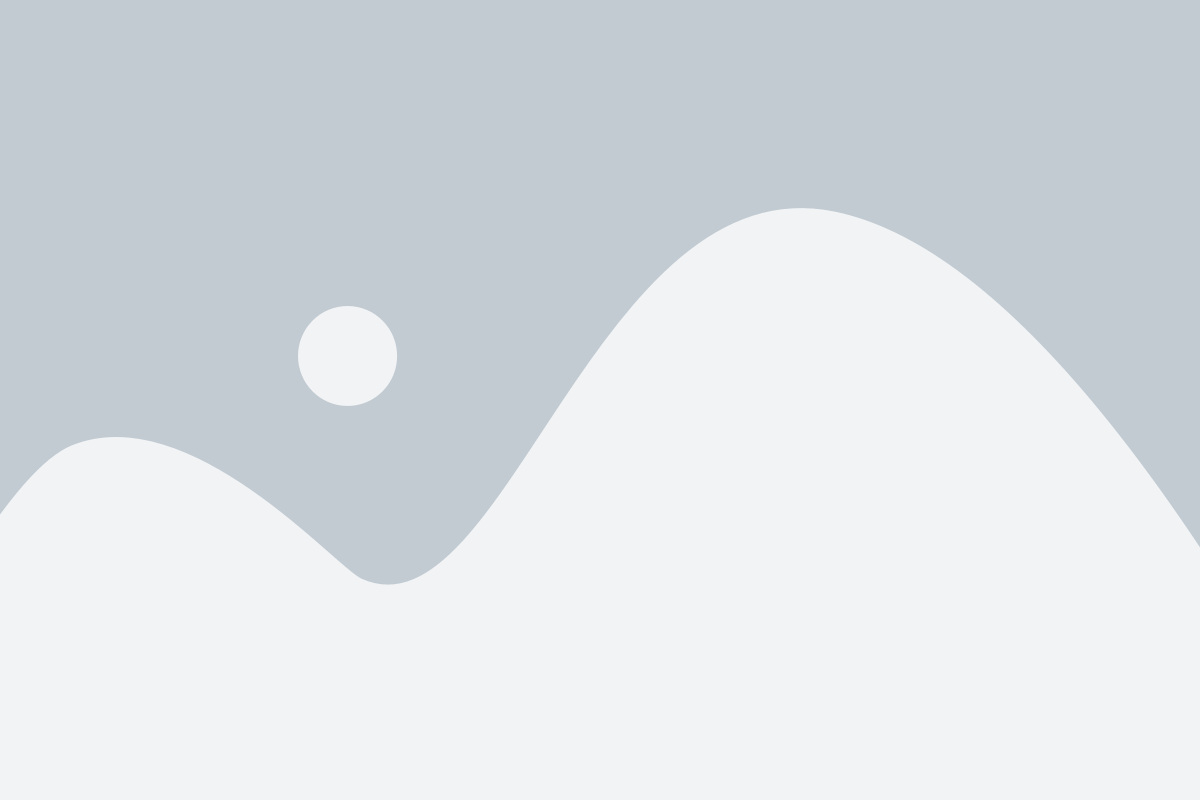
Induction Heater for Heat Treating Turbine Blades
Turbine blades are used in various industries, including aerospace and power generation. The heat treatment process is critical for improving the mechanical properties of the blades and ensuring their durability under high-stress conditions. Induction heating is a commonly used method for heat treating turbine blades. The process involves heating the blade using an induction coil, which generates heat by inducing electrical current in the material. The use of induction heating allows for precise control of the heating process, which is essential for achieving consistent and uniform results. The fast and efficient heating process also minimizes the risk of distortion, which is a common issue in other heating methods.
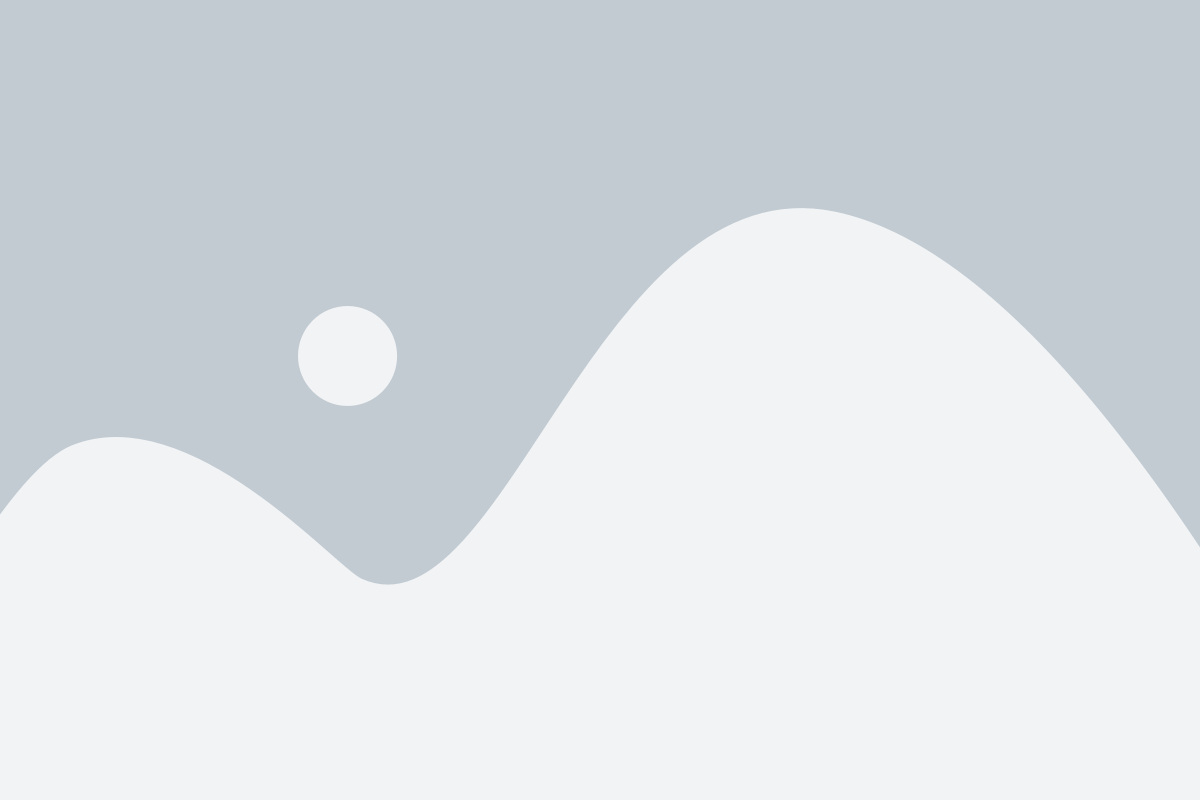
Induction Heater for Heat Treating Jet Engine Parts
Jet engine parts are exposed to high temperatures and stresses during operation, making heat treatment essential for improving their strength and durability. Induction heating is a commonly used method for heat treating jet engine parts. The process involves heating the parts using an induction coil, which generates heat by inducing electrical current in the material. Induction heating allows for precise control of the heating process, which is important for achieving consistent and uniform results. The fast and efficient heating process also minimizes the risk of distortion, which is a common issue in other heating methods.
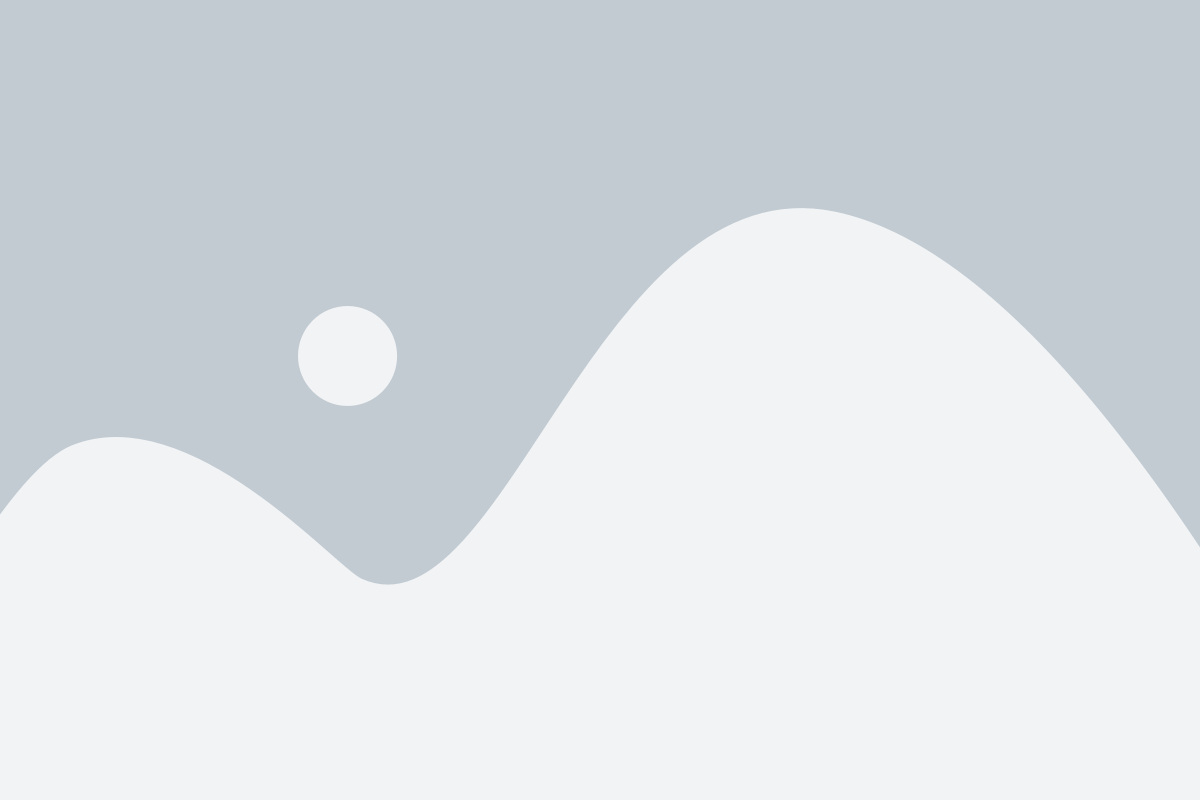
Induction Heater for Heat Treating Landing Gear Components
Landing gear components are critical for ensuring the safe operation of aircraft. The heat treatment process is essential for improving the strength and durability of these components. Induction heating is a widely used method for heat treating landing gear components. The process involves heating the parts using an induction coil, which generates heat by inducing electrical current in the material. Induction heating allows for precise control of the heating process, which is important for achieving consistent and uniform results. The fast and efficient heating process also minimizes the risk of distortion, which is a common issue in other heating methods.
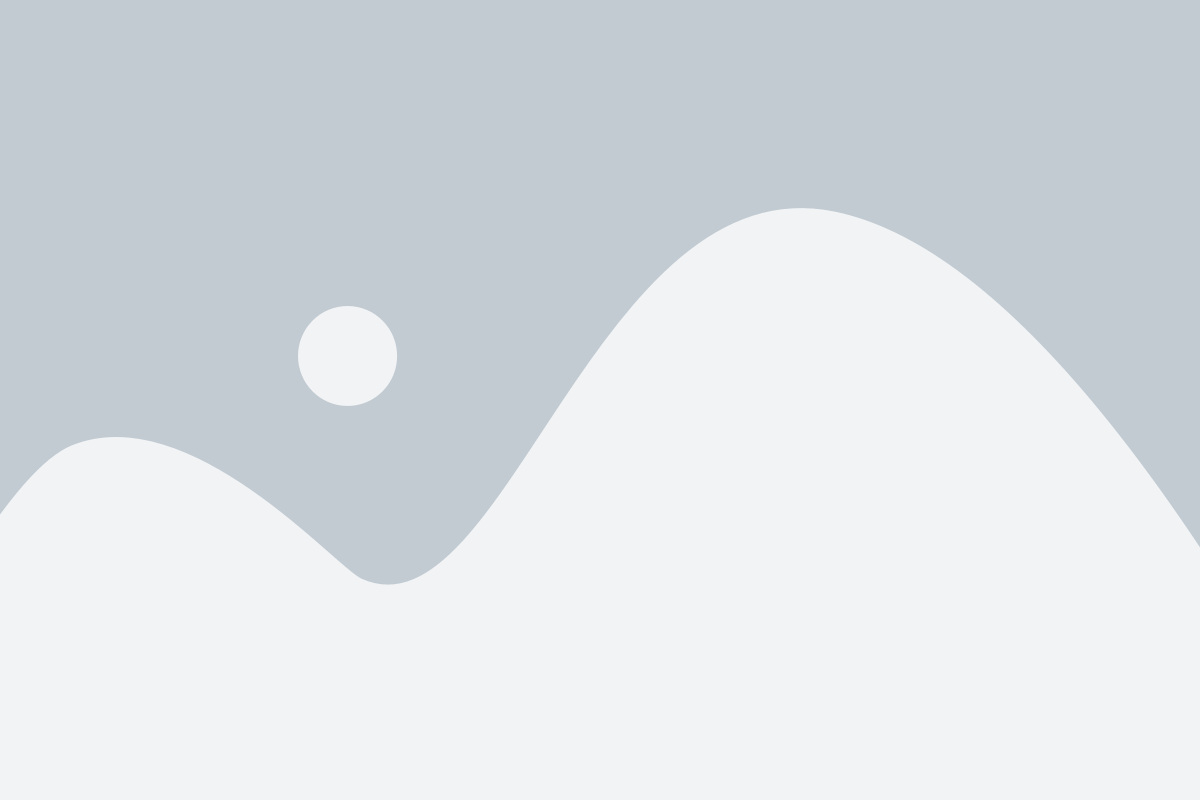
Induction Heater for Heat Treating Wing Spars
Wing spars are the primary structural components of an aircraft’s wing. They carry the majority of the wing’s weight and provide the necessary strength and stiffness for the wing to support the aircraft during flight. Wing spars are typically made from high-strength aluminium alloys, which must be heat treated to achieve the required strength and fatigue resistance. The heat treatment process for wing spars involves heating the aluminium alloy to a specific temperature and holding it at that temperature for a specified period of time before cooling it down. This process helps to refine the microstructure of the aluminium alloy, which improves its strength and fatigue resistance. Induction heaters are often used for heat treating wing spars because they can quickly and efficiently heat the aluminium alloy to the required temperature. Induction heating also provides precise temperature control, which is essential for achieving the desired microstructure and properties in the aluminium alloy.
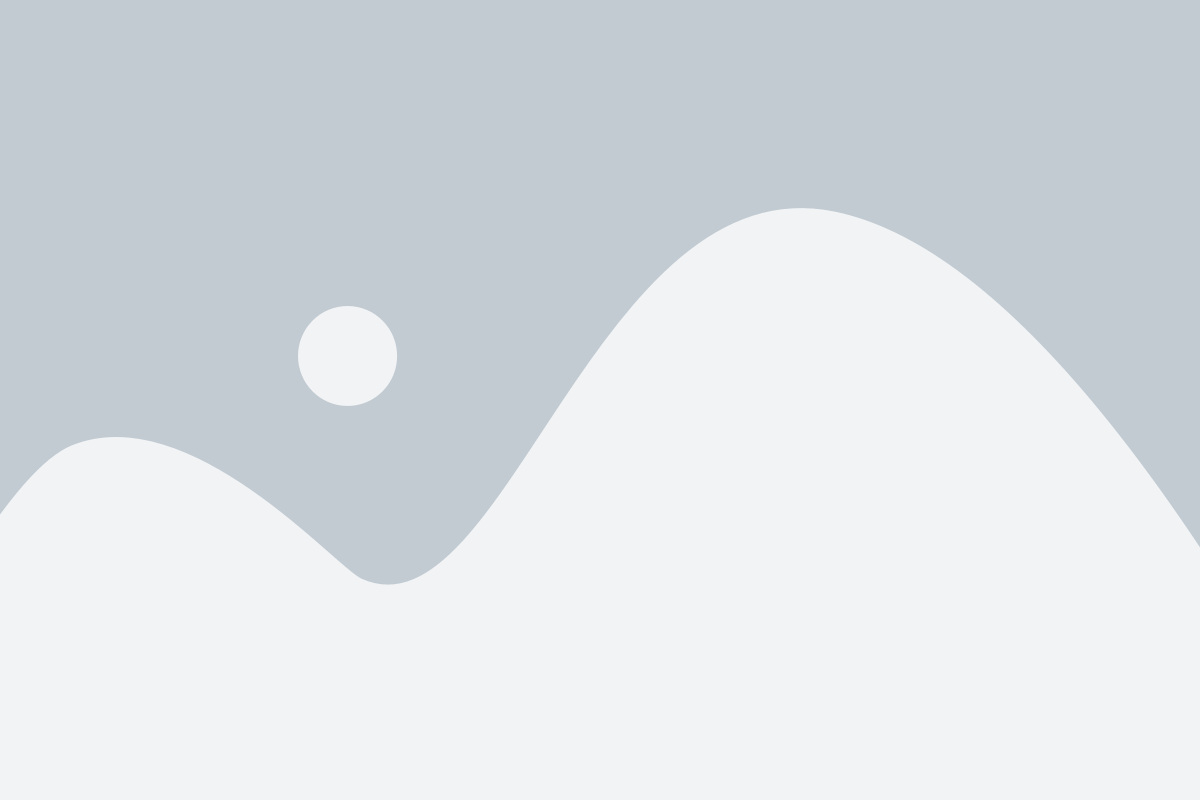
Induction Heater for Heat Treating Electrical Components
Electrical components, such as motors, transformers, and generators, often require heat treatment to improve their properties and performance. For example, heat treatment can help to improve the magnetic properties of electrical steel, which is used to make the cores of transformers and motors. The heat treatment process for electrical components typically involves heating the component to a specific temperature and holding it at that temperature for a specified period of time before cooling it down. This process helps to refine the microstructure of the material, which improves its magnetic properties and performance. Induction heaters are commonly used for heat treating electrical components because they provide fast and efficient heating, which can reduce cycle times and improve productivity. Induction heating also provides precise temperature control, which is essential for achieving the desired microstructure and properties in the material.
Induction Heaters Offered by GM Industries
For more information on any of our high quality products or getting accurate prices contact GM Industries at
Call Us
+(91)-9820533489 / 7738562224
Enquiry Form
Submit
Frequently Asked Questions
Induction heaters can be used to heat treat a wide variety of metal parts including gears, shafts, bearings, engine parts, cutting tools, fasteners, springs, steel beams, structural components, reinforcing bars, pipes and tubes, welded assemblies, turbine blades, jet engine parts, landing gear components, wing spars, and electrical components.
The two main types of induction heaters used in heat treatment depend upon the particular application.
Factors to consider when choosing an induction heater for heat treatment include the type and size of the metal parts being treated, the required heating temperature and time, the required level of precision and consistency, and the available power supply.
An induction heater can be calibrated for heat treatment by measuring the temperature of the metal parts using a thermocouple or pyrometer, and adjusting the heater settings as needed to achieve the desired temperature.
Safety precautions when using an induction heater in heat treatment include wearing protective clothing and equipment, ensuring proper ventilation and grounding, and following manufacturer instructions and safety guidelines.
Regular maintenance of an induction heater used in heat treatment may include cleaning the coils, checking the power supply and cooling system, and replacing any worn or damaged parts.
No, an induction heater is designed specifically for heating metal materials and is not suitable for non-metallic materials.
Yes, an induction heater can be used to heat treat small metal parts, and is often preferred due to its precise and localized heating capabilities.
Yes, an induction heater can be used to heat treat large metal parts, although the size and shape of the parts may require custom coils or multiple heaters.
The cost of an induction heater may be higher than other heat treatment methods, but the efficiency and precision of induction heating can lead to cost savings in the long run.
Using an induction heater for heat treatment requires specialized training and expertise, and should only be done by trained professionals.
The length of time required to heat treat a part using an induction heater depends on the size and type of the part, as well as the desired temperature and heat-treatment process. In some cases, parts can be heat-treated in just a few seconds, while in other cases, the process may take several hours.