Induction Soldering
What is Soldering?
Soldering is a process of joining two metal parts together using a filler metal called solder. The solder is heated to a temperature that causes it to melt and flow between the two metal parts, creating a strong mechanical and electrical bond when it cools and solidifies. Soldering is commonly used in electronics and plumbing applications to connect wires, components, and pipes. It requires a soldering iron, solder wire, and flux, which helps the solder to flow evenly and adhere to the metal parts.
Soldering is different from welding, which involves melting the two metal parts themselves to create a bond, which uses a filler metal with a higher melting point than solder. The most common method used for soldering is the use of a soldering iron. A soldering iron is a handheld tool with a pointed tip that is heated electrically. The tip is used to melt the solder, which is then applied to the joint between the two metal parts. Induction heating is becoming increasingly popular in soldering because it uses high-frequency electromagnetic waves to heat the metal parts directly, rather than relying on a heated tool like a soldering iron.
Why is the Induction Heater used for Soldering Processes?
Induction heating is a popular method for soldering processes because it offers several advantages over traditional methods like using a soldering iron. Firstly, induction heating is a non-contact heating method, which means that the heat is generated directly within the metal parts being soldered. This leads to more precise and even heating, which in turn can lead to stronger and more reliable soldered joints. Furthermore, induction heating is a fast and efficient heating method. The high-frequency electromagnetic waves used in induction heating can heat the metal parts quickly and evenly, resulting in faster heating times and higher productivity. Thirdly, induction heating can be safer than traditional methods. Because there is no open flame or hot surface, there is a reduced risk of accidents or injuries, making it a safer option for soldering in certain environments. Lastly, induction heating can be automated, allowing for more consistent and reliable soldering results in manufacturing settings. With automated induction heating, soldering can be performed with a high degree of accuracy and repeatability, reducing the risk of errors and inconsistencies in the soldered joints. Overall, induction heating is an effective and efficient method for soldering processes, offering many advantages over traditional methods.
Introduction to Industrial Induction Heater for Soldering
An industrial induction heater is a specialized device used in manufacturing and production settings for soldering and other heating applications. It utilizes the principle of electromagnetic induction to generate heat in metal parts, without the need for an open flame or hot surface. In the context of soldering, an industrial induction heater can be used to quickly and efficiently heat metal parts to the required temperature for soldering, resulting in strong and reliable soldered joints. The high-frequency electromagnetic waves used in induction heating can heat the metal parts quickly and evenly, leading to faster heating times and increased productivity.
An industrial induction heater can also be automated, allowing for consistent and precise heating in manufacturing settings. This can lead to more consistent and reliable soldering results, reducing the risk of errors or defects in the final product. Overall, an industrial induction heater is a powerful and versatile tool for soldering and other heating applications in industrial settings. It offers many advantages over traditional heating methods, including faster heating times, greater precision, and increased safety.
GM Industries is a leading provider of industrial induction heaters for soldering and other heating applications. One of the major advantages of working with GM Industries is our in-depth knowledge of the various types of induction heaters available on the market, as well as the ability to customize and tailor solutions to meet the specific requirements of clients.
Advantages of Using an Industrial Induction Heater for Soldering
Using an industrial induction heater for soldering offers several key features and advantages over traditional heating methods:
Faster Heating Times
Industrial induction heaters use high-frequency electromagnetic waves to heat metal parts directly, resulting in faster and more efficient heating times compared to traditional methods like using a soldering iron.
Precision and Control
Industrial induction heaters allow for precise and even heating, resulting in stronger and more reliable soldered joints. Additionally, many industrial induction heaters can be automated, providing even greater control and consistency.
Safety
Industrial induction heaters do not require an open flame or hot surface, making them a safer option for soldering in certain environments. They also produce less smoke and fumes, creating a safer working environment.
Versatility
Industrial induction heaters can be used for a range of heating applications beyond soldering, including brazing, annealing, and heat treating.
Cost-Effective
While industrial induction heaters may have a higher upfront cost than traditional heating methods, they are often more cost-effective in the long run due to their efficiency and productivity.
Overall, using an industrial induction heater for soldering offers a range of features and benefits that can help improve efficiency, precision, and safety in manufacturing and production settings.
Induction Heater for Various Soldering Process
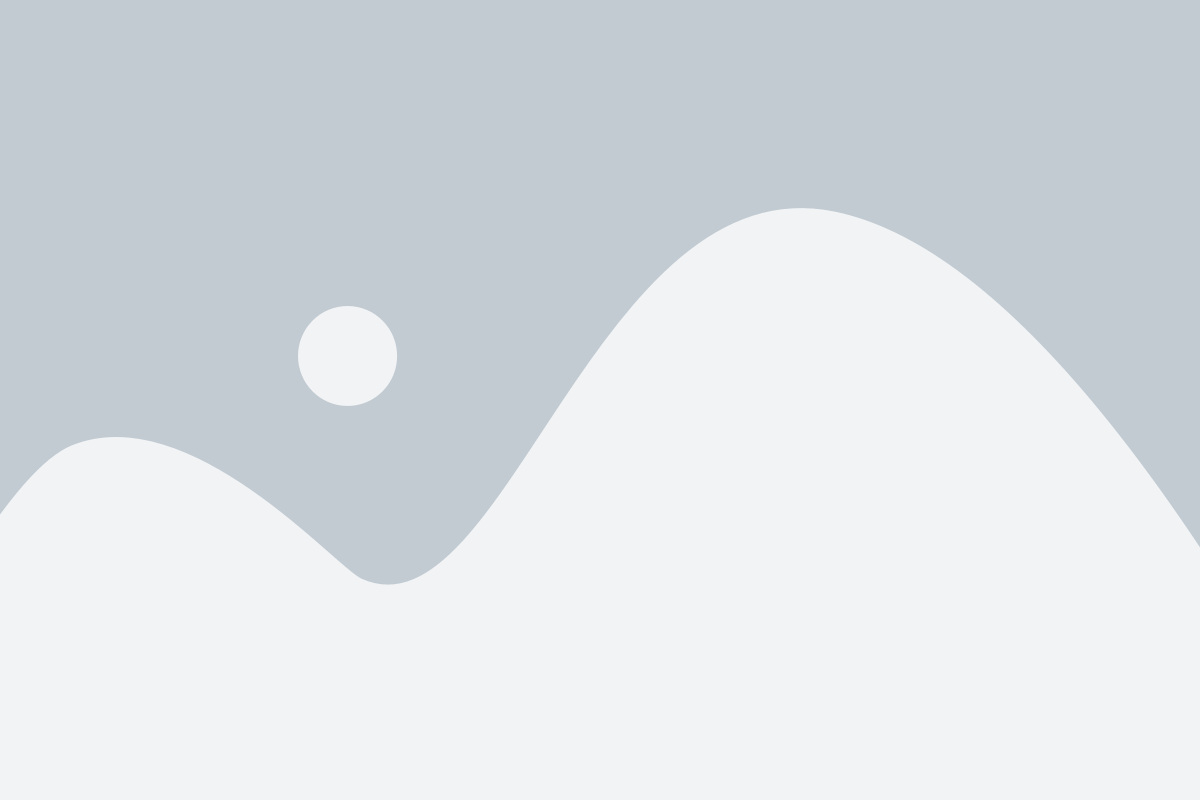
Induction heater for soldering Printed circuit boards
Printed circuit boards (PCBs) are a critical component in electronic devices, and reliable soldering is essential for their manufacture. Induction heating is an effective method for soldering PCBs due to its precision, speed, and consistency. An induction heater can be used to heat the PCB to the required temperature for soldering, resulting in strong and reliable connections between components.
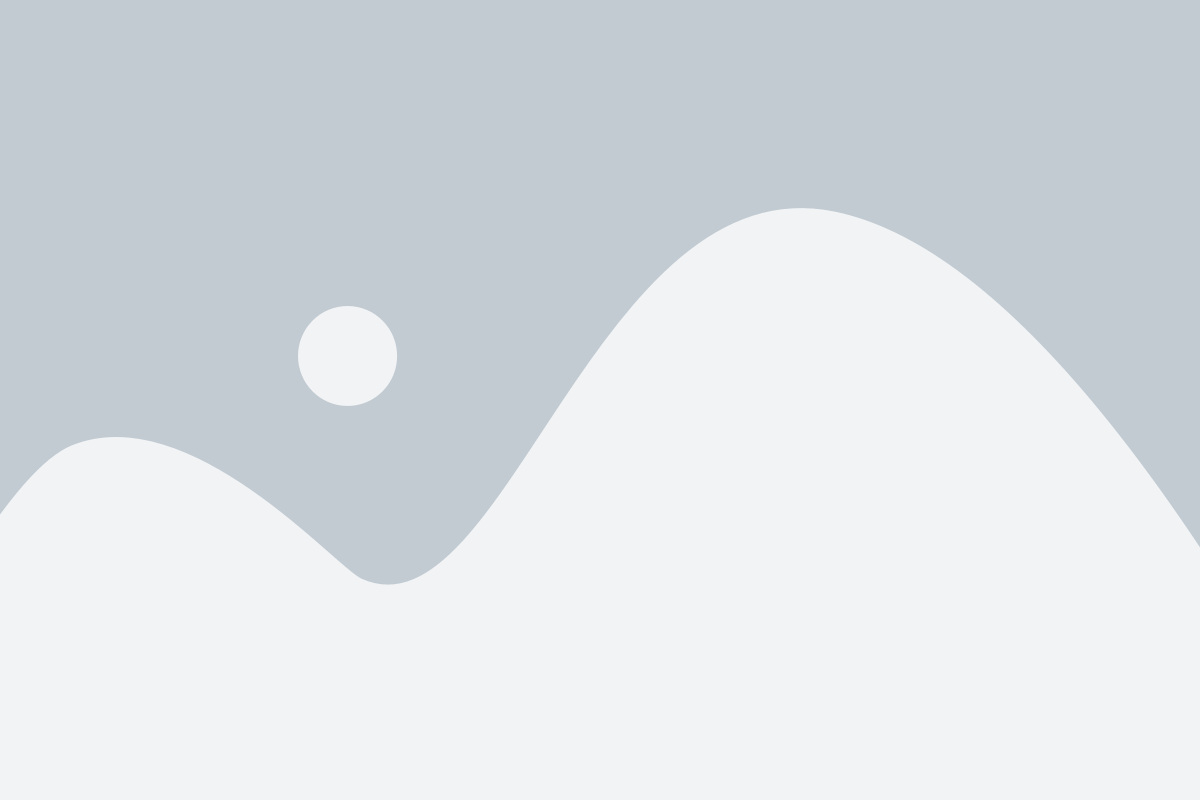
Induction heater for soldering Wires
Soldering wires is a common task in electrical work, and using an induction heater can make the process faster and more precise. An induction heater can be used to heat the wire and solder simultaneously, resulting in stronger connections and reduced risk of damage to the wire.
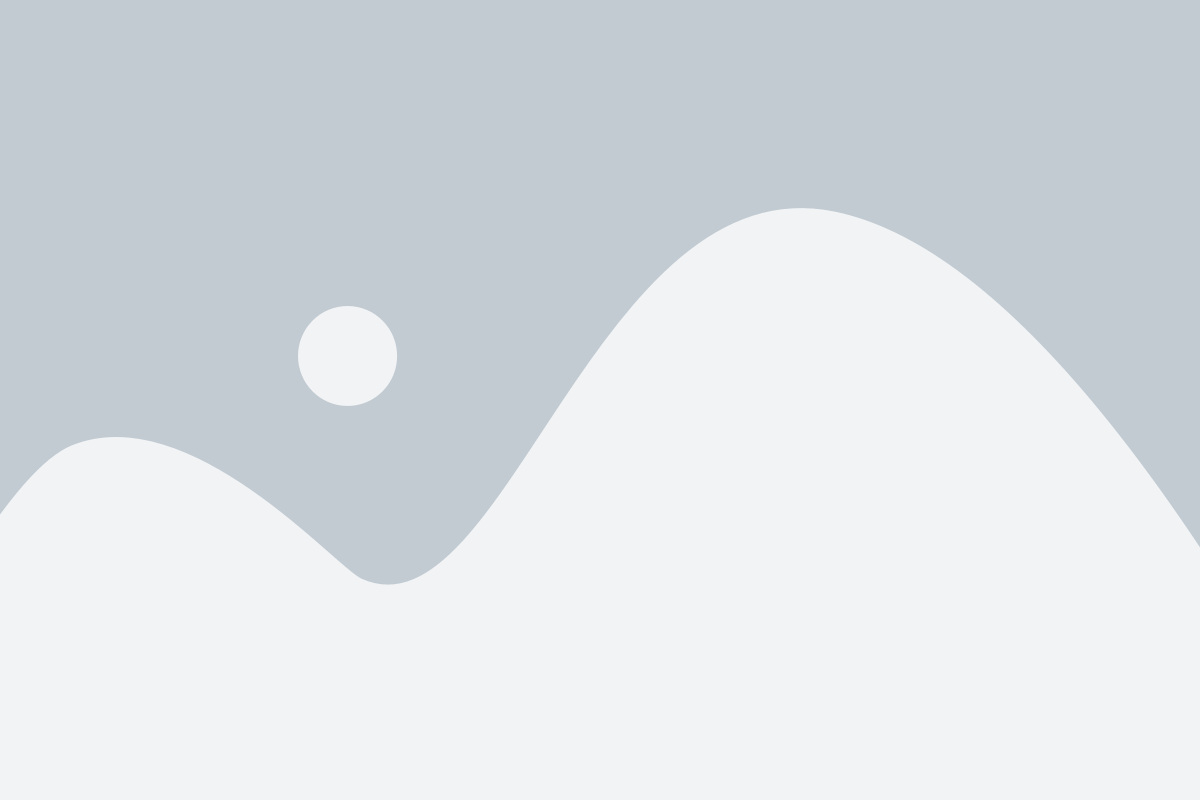
Induction heater for soldering Connectors
Connectors are used in a range of electrical and electronic applications, and soldering is often required for reliable connections. Induction heating is a fast and precise method for soldering connectors, resulting in strong and reliable connections between components.
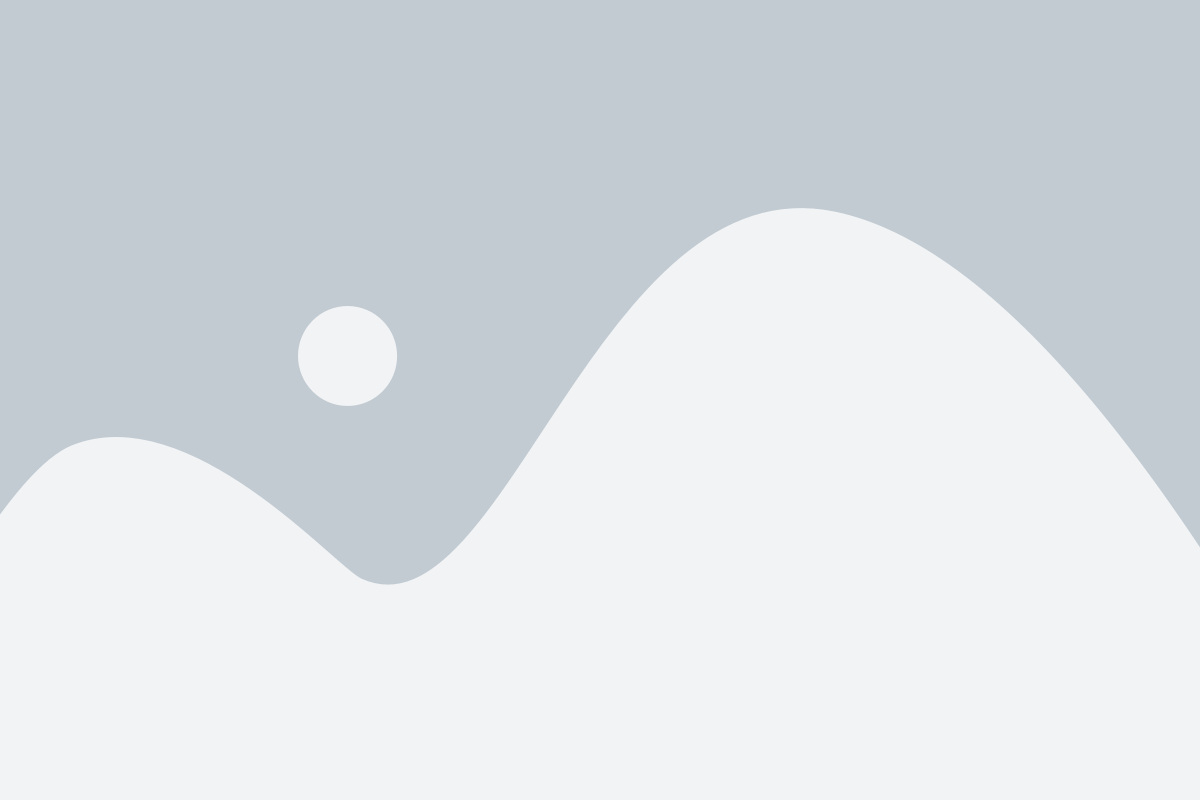
Induction heater for soldering Fuel injectors
Fuel injectors are critical components in automotive engines, and precise soldering is essential for their manufacture. Induction heating can be used to heat the injector and solder to the required temperature, resulting in strong and reliable connections between components.
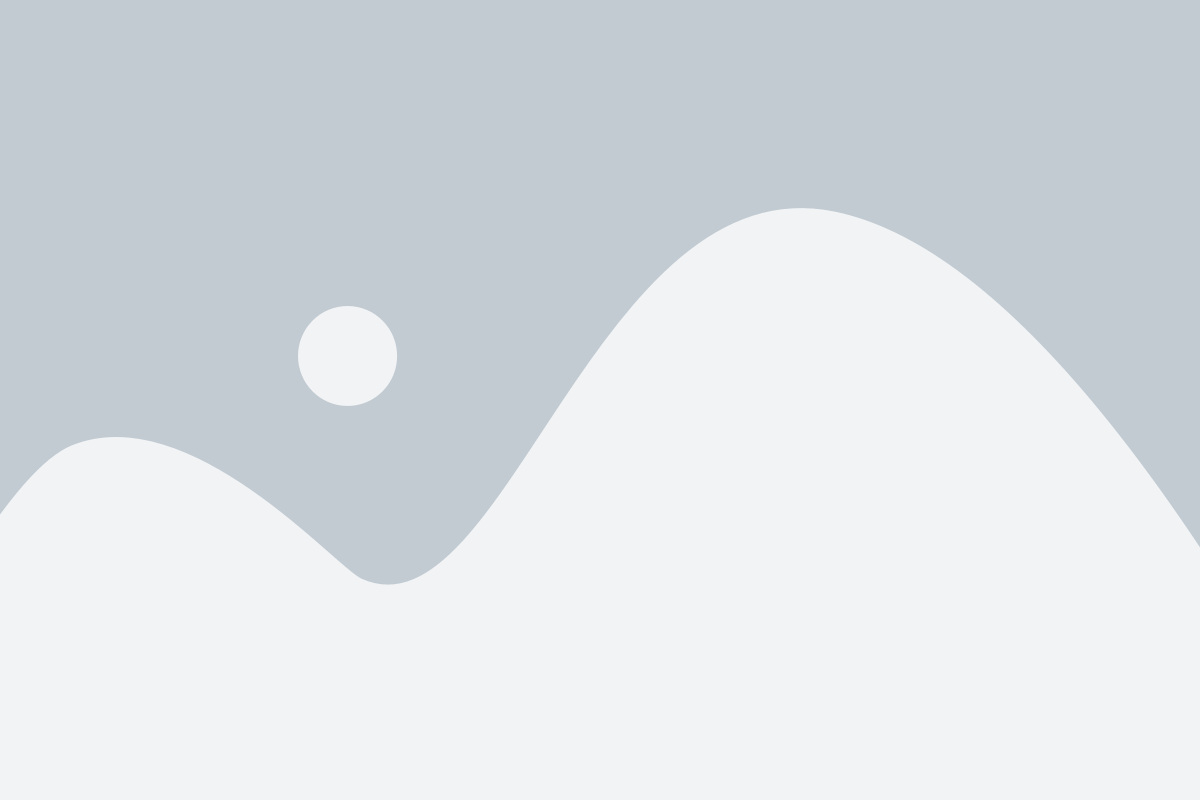
Induction heater for soldering Sensors
Sensors are used in a range of applications, from automotive to medical devices, and reliable soldering is essential for their manufacture. Induction heating is a fast and precise method for soldering sensors, resulting in strong and reliable connections between components.
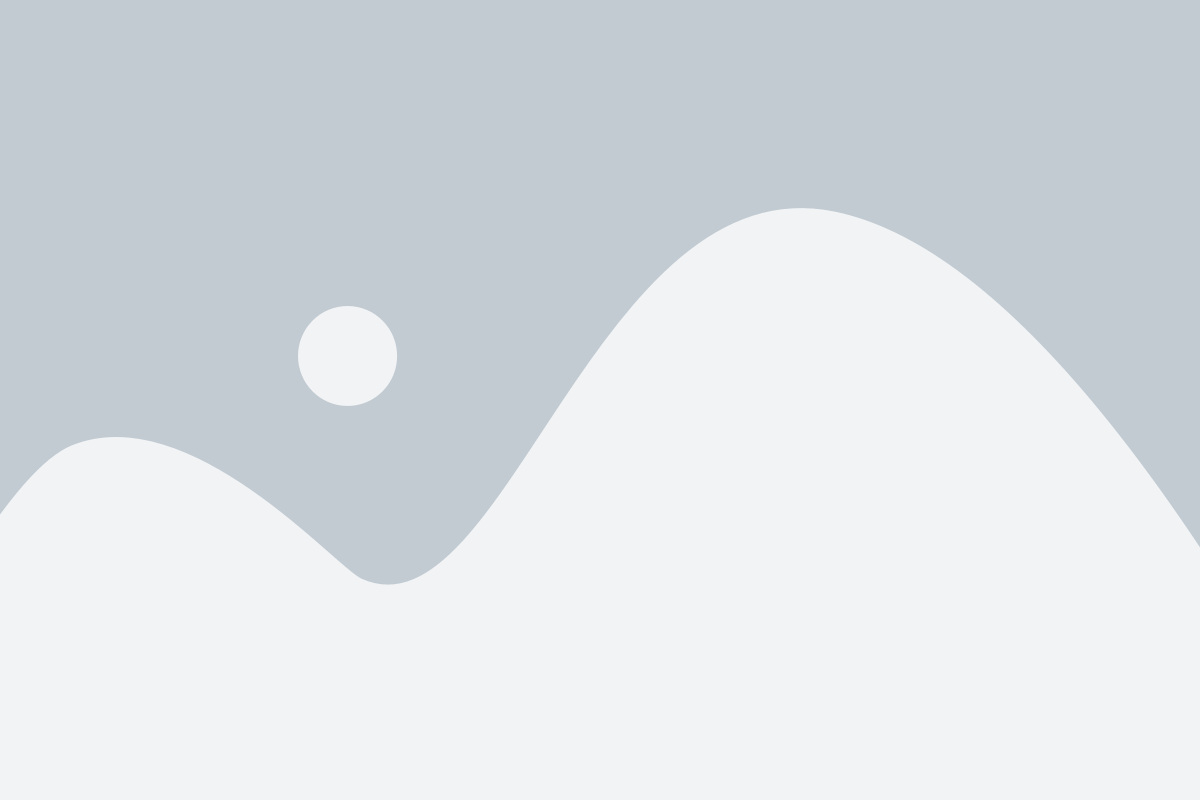
Induction heater for soldering Switches
Switches are used in a range of electrical and electronic applications, and precise soldering is essential for their manufacture. Induction heating is a fast and precise method for soldering switches, resulting in strong and reliable connections between components.
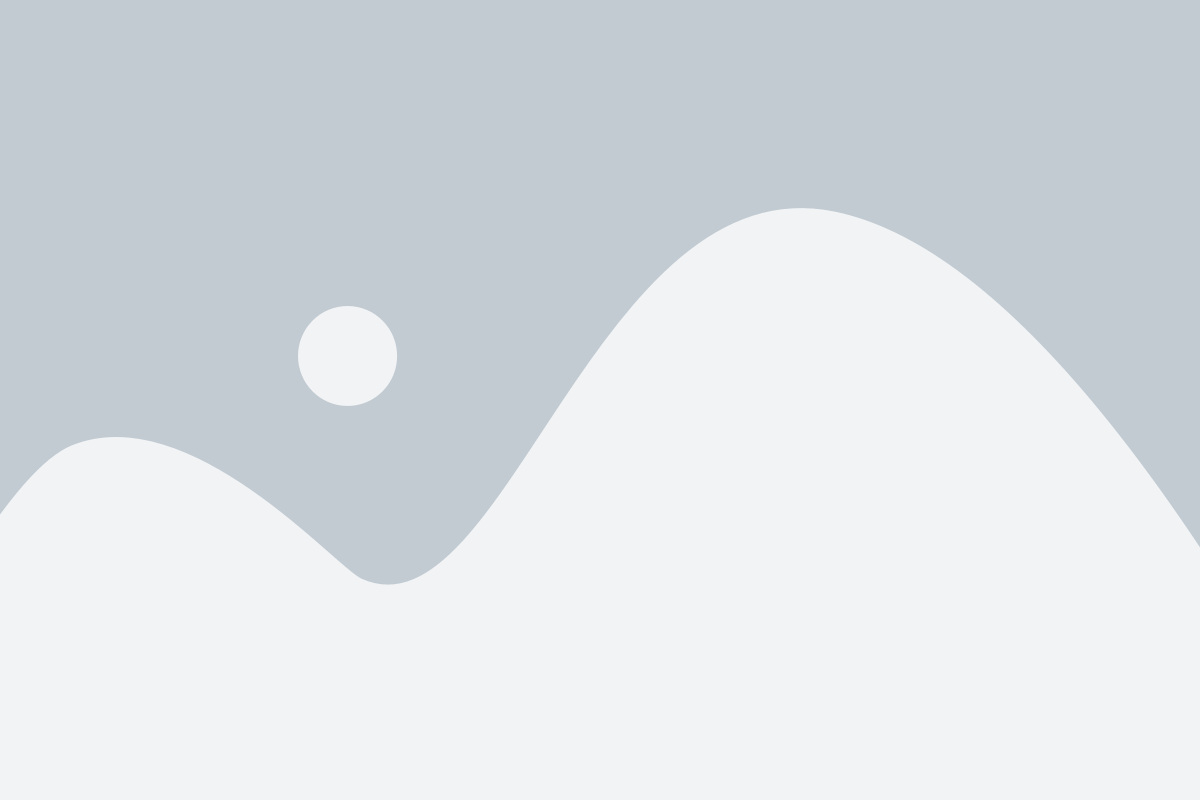
Induction heater for soldering Catheters
Catheters are used in medical procedures, and precise soldering is essential for their manufacture. Induction heating is a precise and controlled method for soldering catheters, resulting in strong and reliable connections between components.
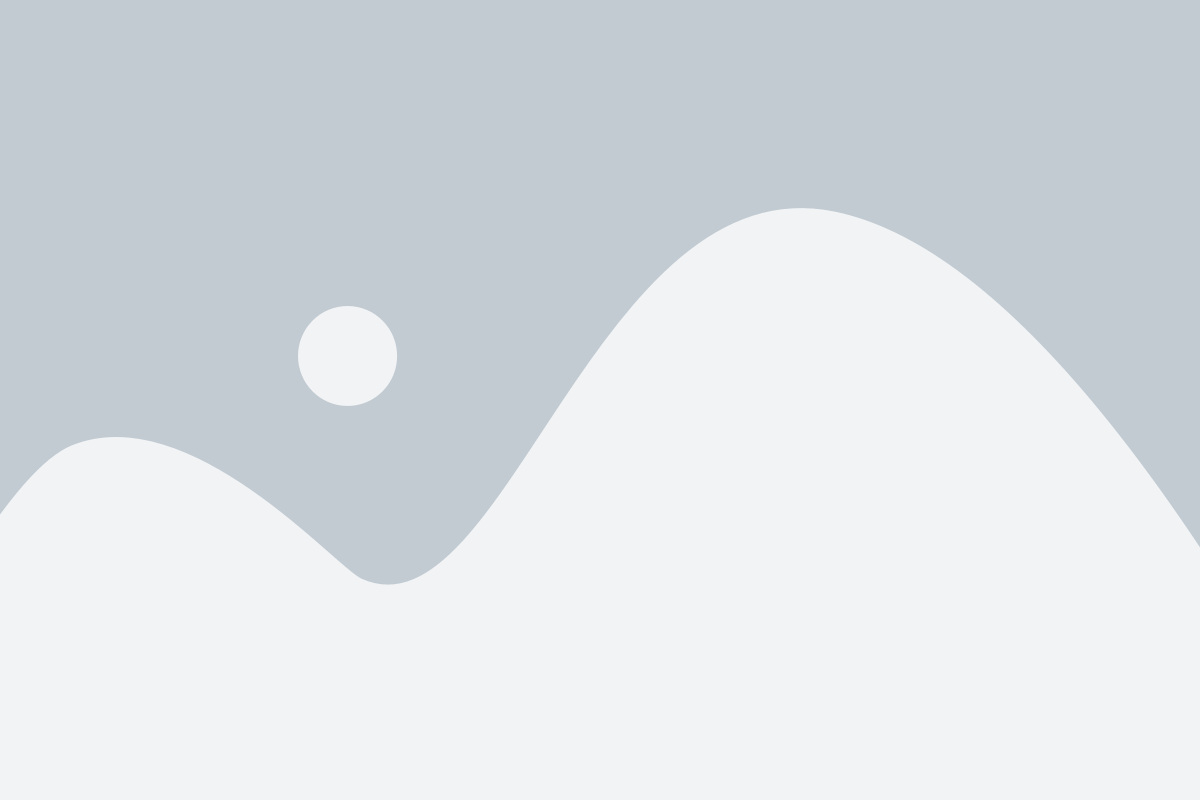
Induction heater for soldering Implants
Implants are used in medical procedures, and reliable soldering is essential for their manufacture. Induction heating can be used to heat the implant and solder to the required temperature, resulting in strong and reliable connections between components.
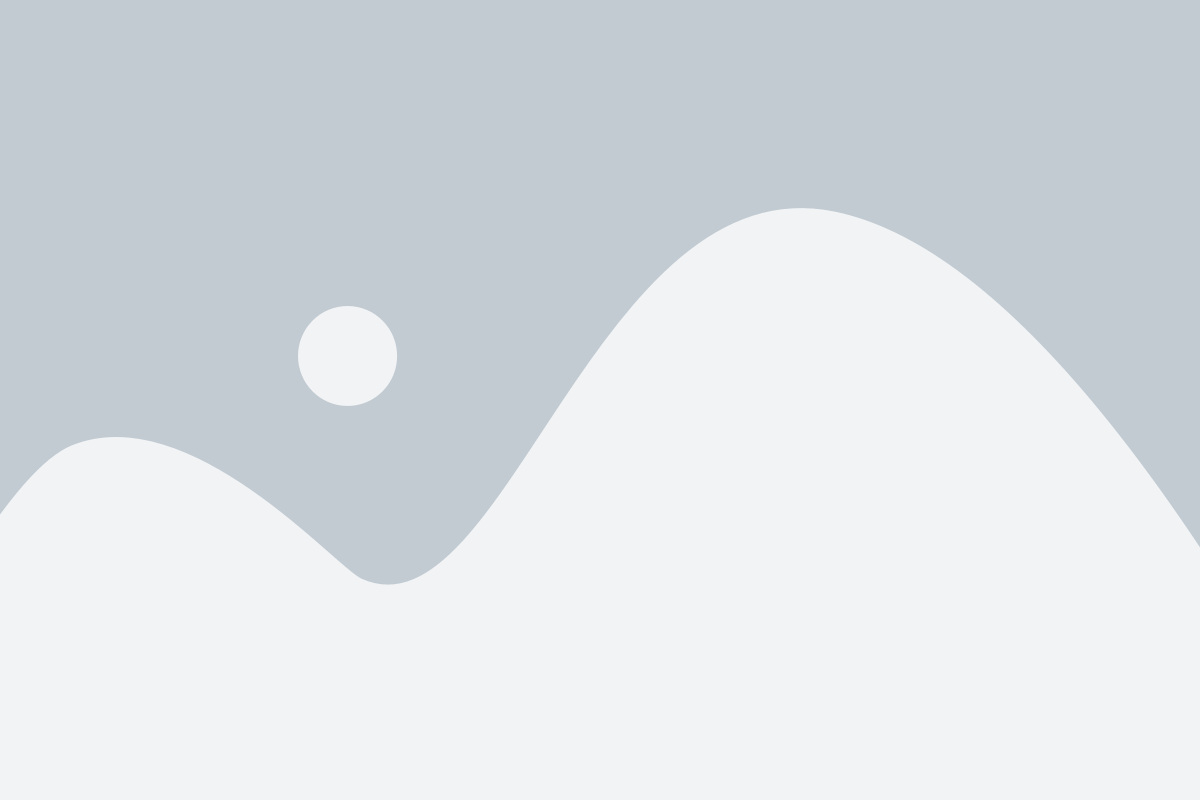
Induction heater for soldering Turbine blades
Turbine blades are critical components in aviation and power generation industries, and precise soldering is essential for their manufacture. Induction heating is a fast and precise method for soldering turbine blades, resulting in strong and reliable connections between components.
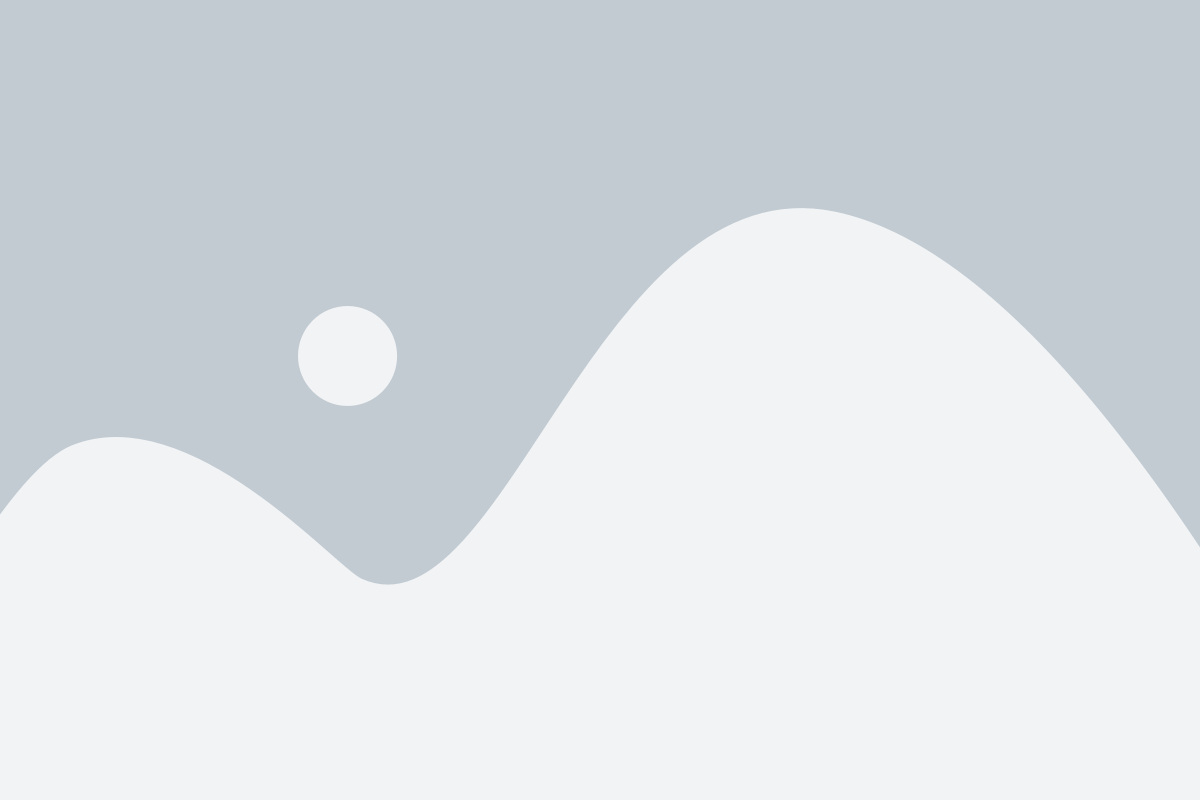
Induction heater for soldering Fuel nozzles
Fuel nozzles are critical components in automotive and aerospace industries, and precise soldering is essential for their manufacture. Induction heating can be used to heat the fuel nozzle and solder to the required temperature, resulting in strong and reliable connections between components.
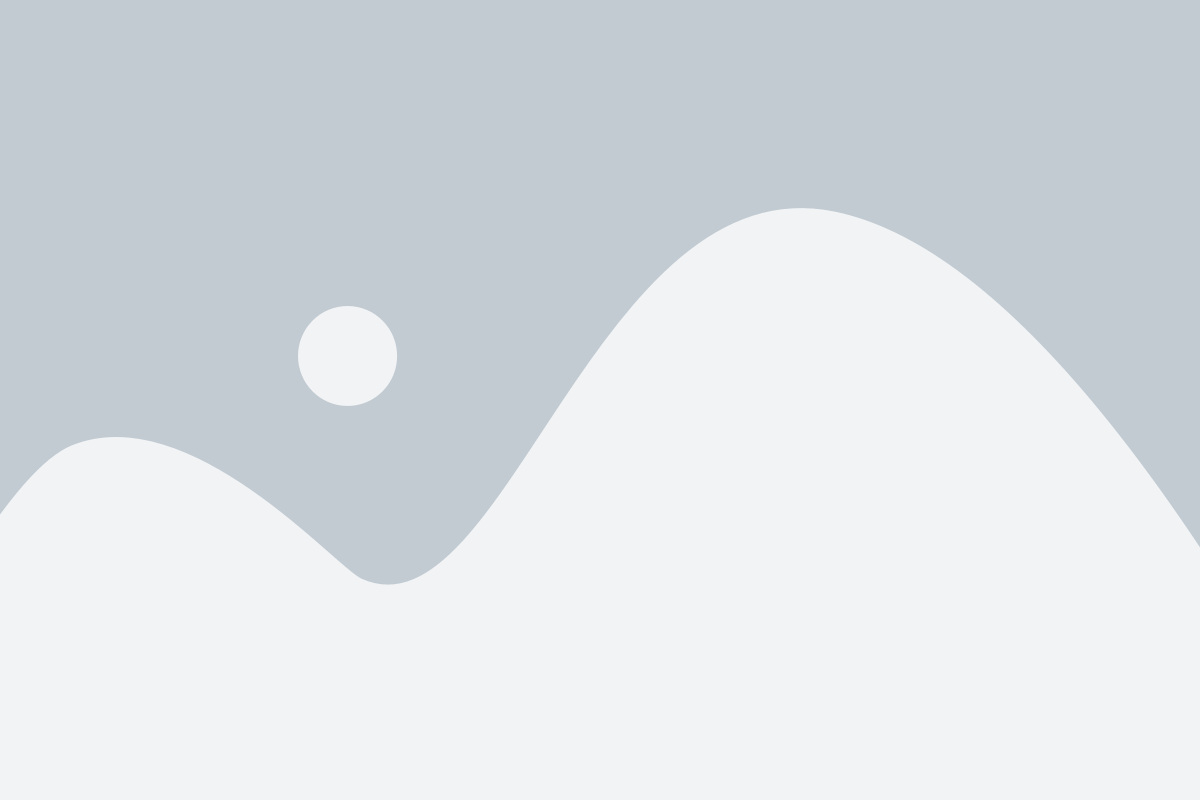
Induction heater for soldering Rings
Rings are a common jewelry item made from various metals, including gold, silver, and platinum. During the manufacturing process, different parts of the ring are joined together using soldering techniques. The process involves heating the joint to a temperature where the solder melts and flows, creating a strong and permanent bond. Induction heaters are commonly used in the jewelry industry for soldering rings. They provide precise and localized heating, allowing for accurate control of temperature and avoiding damage to delicate gemstones or other parts of the ring. Induction heaters also offer fast heating times and uniform heating, which results in a consistent quality of the solder joint. The use of induction heaters reduces the risk of overheating, which can cause discoloration or deformation of the metal.
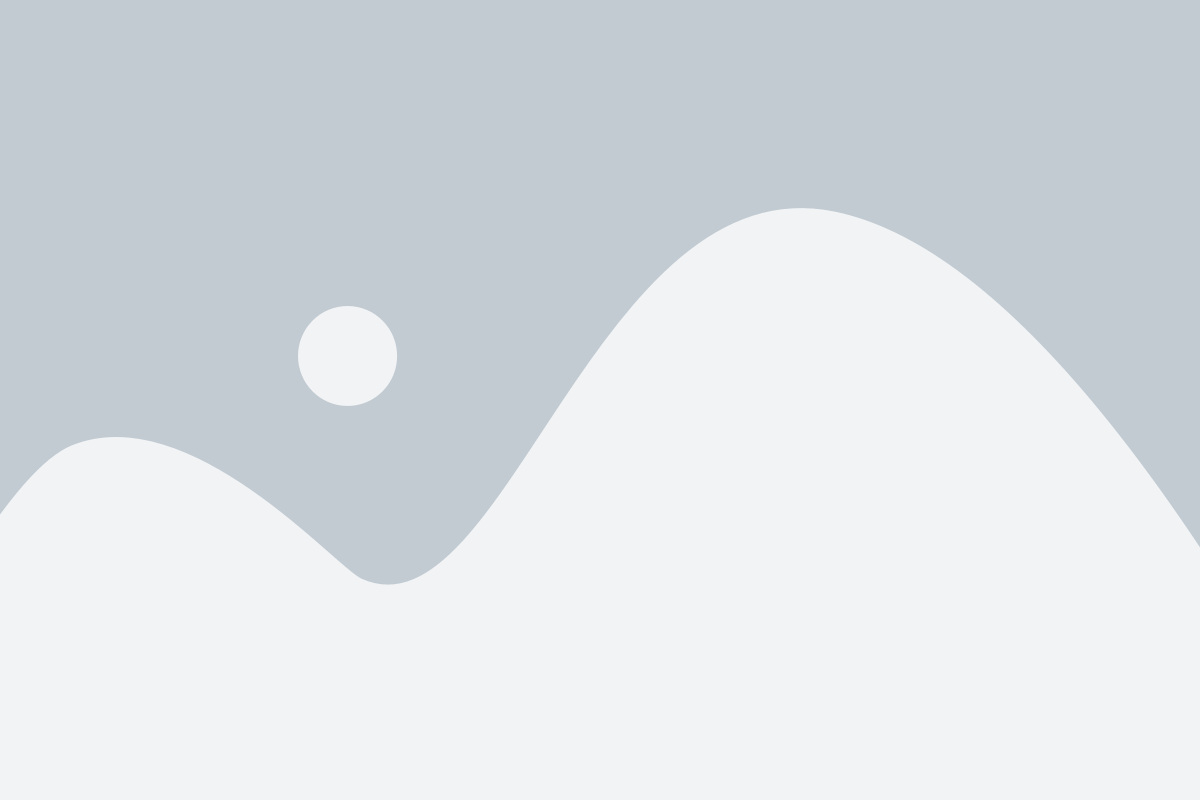
Induction heater for soldering Bracelets
Bracelets are another jewelry item that requires soldering during the manufacturing process. Bracelets are typically made from various metals and may have different components, such as clasps, links, and charms. Soldering is used to join these components together to create a finished piece. Induction heaters are commonly used for soldering bracelets due to their ability to provide precise and localized heating. The heating is accomplished by generating an electromagnetic field that induces current in the metal, creating heat. Induction heaters are ideal for bracelet soldering because they offer fast heating times, uniform heating, and accurate temperature control. They also eliminate the need for open flames or other heating sources, reducing the risk of damage to the bracelet or the workspace.
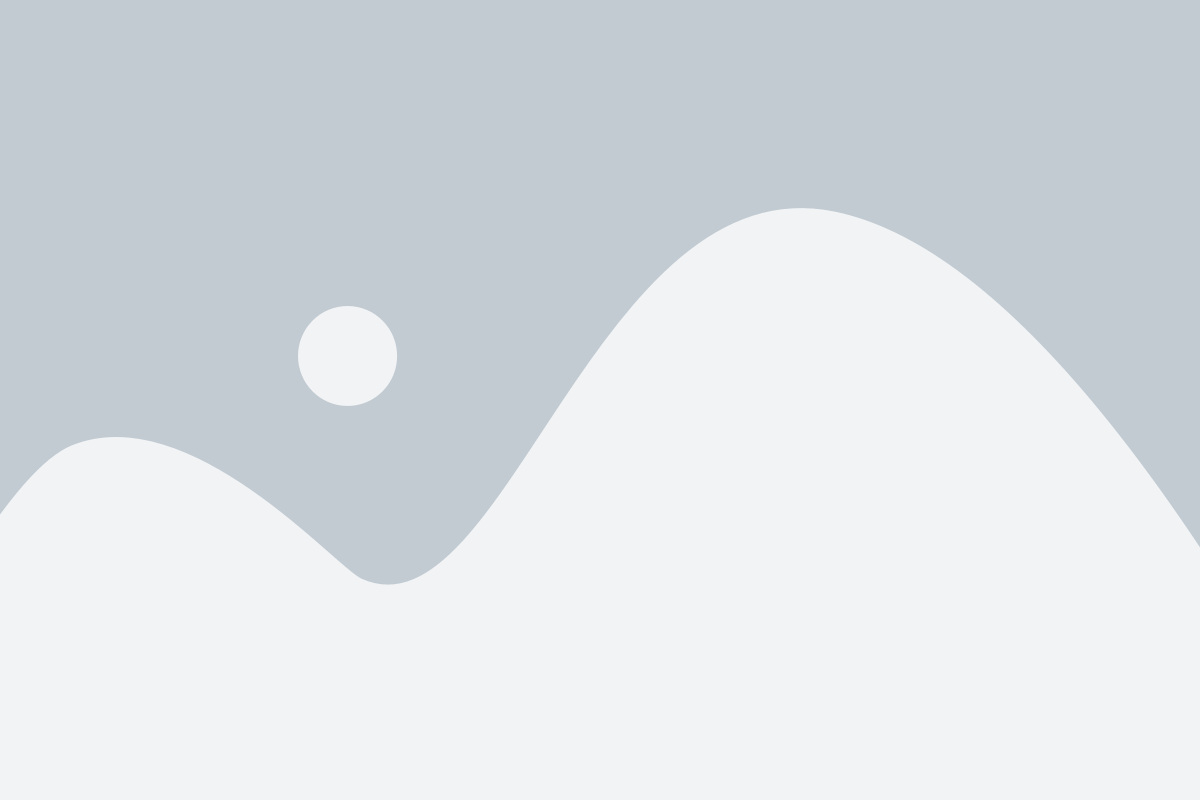
Induction heater for soldering Earrings
Earrings are a popular jewelry item that comes in various styles and materials. Soldering is often used during the manufacturing process to join different components, such as posts, backs, and decorative elements. Induction heaters are commonly used for soldering earrings due to their ability to provide fast and precise heating. Induction heating is a non-contact process, which means that the heat is generated directly in the metal, without any physical contact with the heating element. This makes it ideal for soldering delicate components without causing damage or discoloration. Induction heaters offer precise temperature control and uniform heating, which ensures a consistent quality of the solder joint.
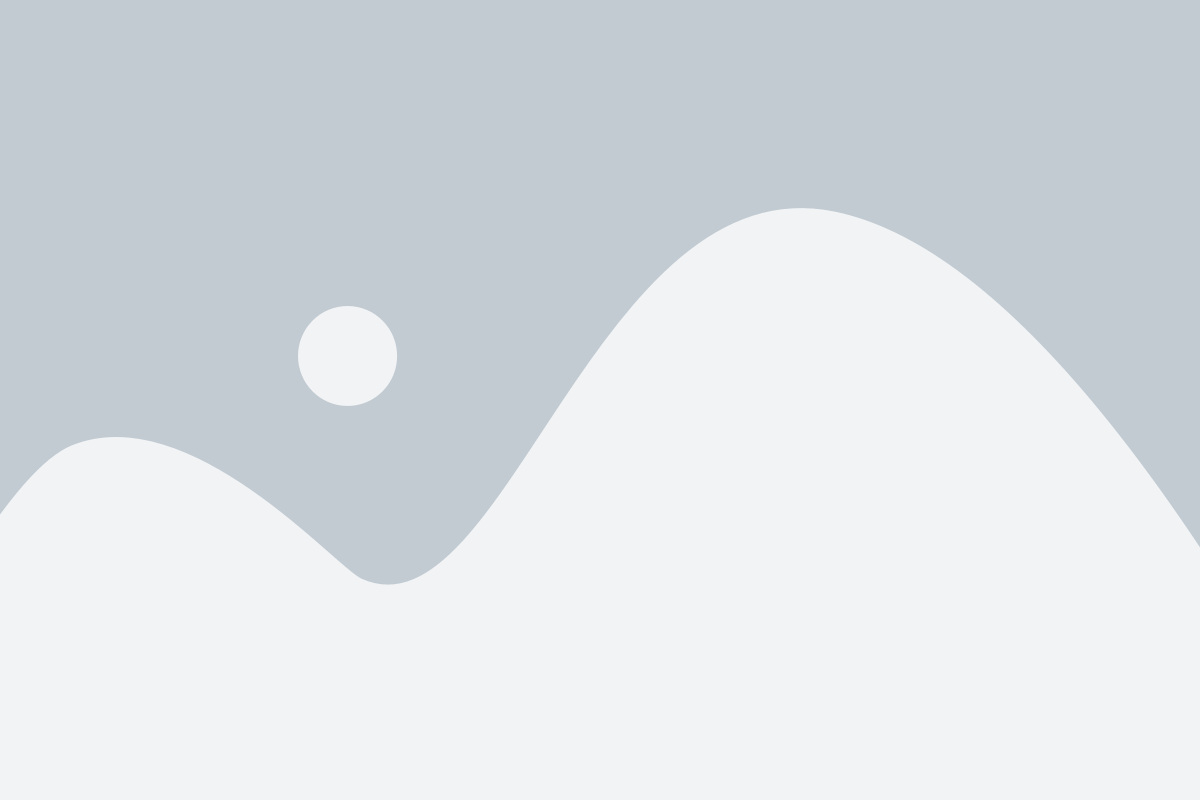
Induction heater for soldering Faucets
Faucets are an essential part of any plumbing system and are typically made from various metals, such as brass or stainless steel. Soldering is used during the manufacturing process to join different components, such as valves, handles, and spouts. Induction heaters are commonly used for soldering faucets because they offer precise and localized heating. The use of induction heating eliminates the need for open flames or other heating sources, reducing the risk of damage to the faucet or the workspace. Induction heaters also offer fast heating times and uniform heating, which ensures a consistent quality of the solder joint. The use of induction heaters in faucet manufacturing also improves the overall efficiency of the process, reducing production time and costs.
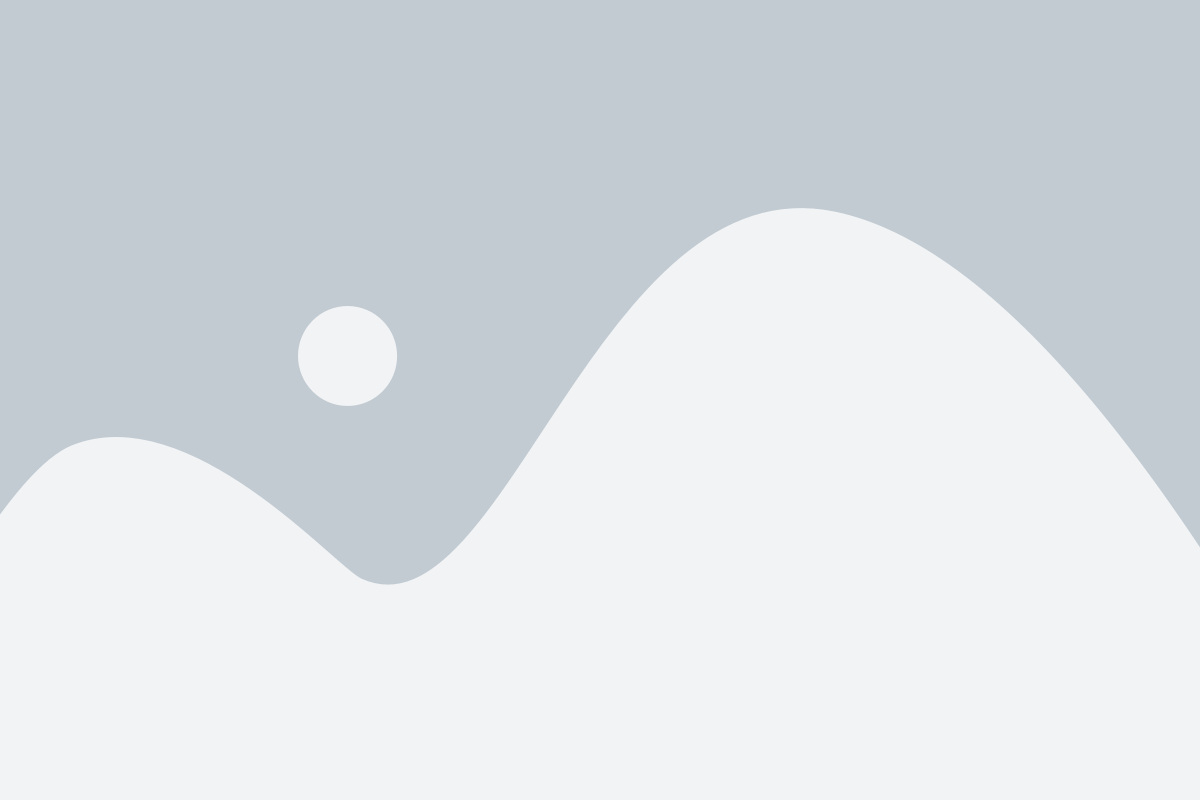
Induction heater for soldering Valves
Valves are an essential component in many mechanical systems, such as engines and pipelines. They are typically made from various metals, such as steel or brass, and require soldering during the manufacturing process to join different components together. Induction heaters are commonly used for soldering valves due to their ability to provide fast and precise heating. The use of induction heating eliminates the need for open flames or other heating sources, reducing the risk of damage to the valve or the workspace. Induction heaters also offer accurate temperature control and uniform heating, which ensures a consistent quality of the solder joint. The use of induction heaters in valve manufacturing also improves the overall efficiency of the process, reducing production time and costs.
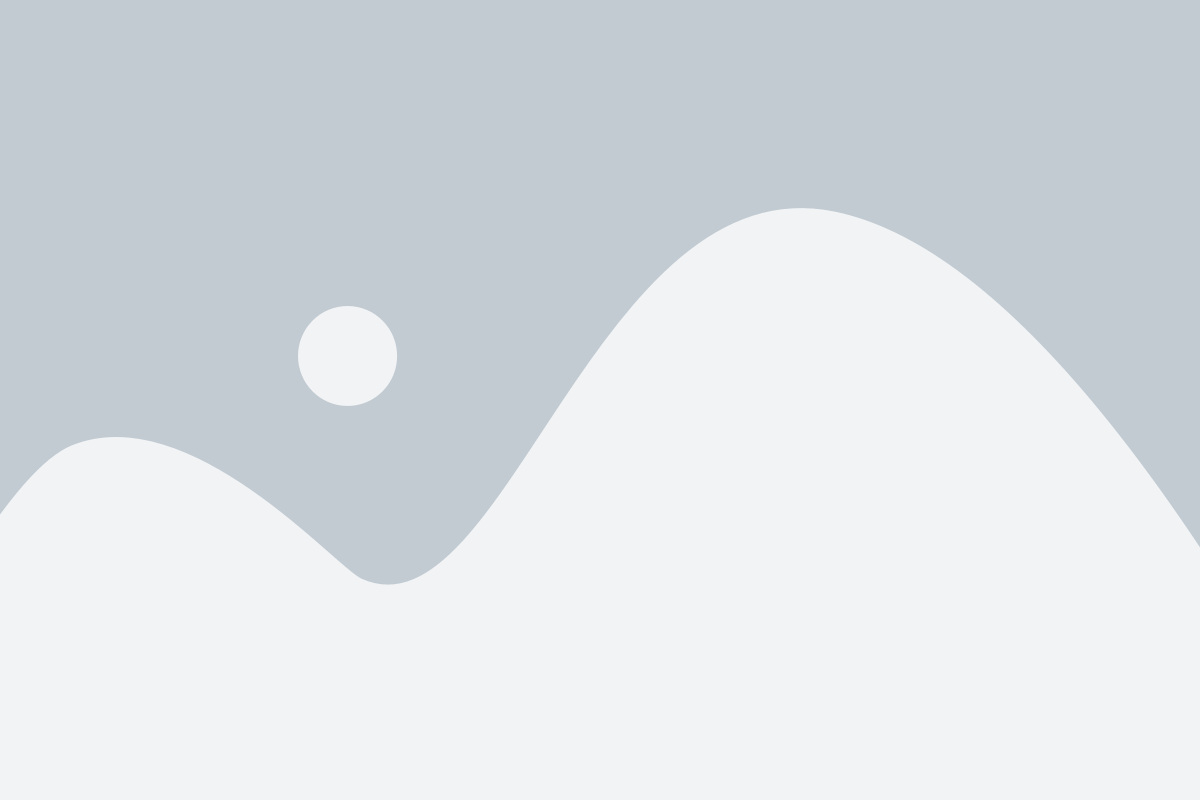
Induction Heater for Soldering Pipes
Pipes are used in many industries, including plumbing, heating, and cooling systems. Soldering is a common method used to join the various parts of pipes together. The soldering process involves heating the pipes and the joint to a temperature where the solder material melts and fuses the parts together.
Induction Heaters Offered by GM Industries
For more information on any of our high quality products or getting accurate prices contact GM Industries at
Call Us
+(91)-9820533489 / 7738562224
Enquiry Form
Submit
Frequently Asked Questions
Induction heaters can be used to solder a wide range of metal objects, including wires, connectors, printed circuit boards, fuel injectors, sensors, switches, turbine blades, fuel nozzles, rings, bracelets, earrings, faucets, valves, and pipes.
Yes, induction heaters are generally safe to use because they do not generate open flames or other sources of heat that could cause fires or explosions.
There are several types of induction heaters for soldering depending upon the applications.
The maximum temperature that an induction heater can reach depends on the model and the application. Some induction heaters can reach temperatures of up to 2000 degrees Celsius.
Yes, induction heaters can be used for brazing, which is a similar process to soldering but involves higher temperatures and different materials.
Yes, induction heaters typically require high-frequency power sources that generate currents in the range of 100 kHz to 1 MHz.
Yes, induction heaters have many other applications, including welding, annealing, and heat treating.
An induction heater uses electromagnetic induction to heat up metal objects, while a traditional soldering iron uses an electric heating element to generate heat.
The heating time depends on the size and material of the object, as well as the power and frequency of the induction heater. In general, induction heaters can heat up small objects in seconds and larger objects in minutes.
The temperature of an induction heater can be controlled by adjusting the power and frequency of the electromagnetic field.
Yes, induction heaters are generally more energy-efficient than traditional heating methods because they only heat up the object being soldered, rather than the surrounding air.
Induction heater coils are typically made from copper or aluminum, which are good conductors of electricity.
The lifespan of an induction heater depends on the model and the frequency of use. With proper maintenance, an induction heater can last for many years.
Safety precautions include wearing protective gear, such as gloves and goggles, keeping the work area clean and free of debris, and following the manufacturer’s instructions.
Maintenance requirements vary by model, but typically include cleaning the coils and checking the power source and connections.
Yes, induction heaters are often used in high-volume production settings because they offer fast and efficient heating capabilities.