Induction Welding
What is Welding?
Welding is a process of joining two or more pieces of metal or thermoplastic materials together by melting them at the point of contact and then allowing them to cool and solidify, creating a strong bond. The heat necessary for welding can be generated by an electric arc, gas flame, laser, or other sources. Welding is a commonly used method in manufacturing, construction, and repair work for creating or repairing structures and objects made of metal or thermoplastic materials. It requires skill and precision to ensure a strong, reliable, and safe weld.
The most common method used for welding is arc welding, which utilizes an electric arc to generate the heat necessary to melt the metal or thermoplastic materials being joined. Induction heating is becoming increasingly popular in welding applications because it uses an electromagnetic field to heat the materials being joined, rather than an open flame or electric arc which allows for precise, localized heating that can be tailored to the specific materials being welded.
Why is the Induction Heater used for Welding Processes?
Welding processes use induction heaters because they offer several benefits over other heating methods. Induction heaters can be used to heat only the area of the material that needs to be welded, resulting in a more precise and consistent weld. This is important because different materials require different levels of heat to weld properly, and too much heat can damage the material or surrounding areas. Induction heating is also more energy-efficient than other heating methods, as it does not waste energy by heating the air around the material. Instead, the electromagnetic field created by the induction heater heats the material directly, resulting in faster heating times and less energy consumption. This can lead to cost savings and reduced environmental impact.
Another benefit of induction heating in welding processes is that it can be automated and integrated into manufacturing processes. This allows for greater control and consistency in the welding process, resulting in higher quality and more reliable welds. Overall, the use of induction heaters in welding processes can improve efficiency, precision, and consistency, while reducing costs and environmental impact.
Introduction to Industrial Induction Heater for Welding
An industrial induction heater is a device that uses electromagnetic induction to generate heat in metals and other conductive materials. These heaters are commonly used in welding applications to heat specific areas of a workpiece in order to create a strong and consistent weld. The induction heating process works by creating a magnetic field around the workpiece, which induces electrical currents in the material. These currents generate heat, which can be controlled and directed to specific areas of the material using various induction coil designs.
One of the main advantages of using an industrial induction heater for welding is the ability to precisely control the amount of heat generated. This is important because different materials require different levels of heat to weld properly, and too much heat can cause damage to the material or surrounding areas. Induction heaters also offer fast heating times, resulting in faster welding speeds and increased productivity. Industrial induction heaters for welding can vary in size and design depending on the specific application.
One of the ways GM Industries plays a major role in finding the perfect industrial induction heater for welding is by working closely with customers to understand their specific requirements. In addition, We offer customization options for induction heaters to ensure they meet the exact needs of the customers.
Advantages of Using an Industrial Induction Heater for Welding
There are several advantages to using an industrial induction heater for welding, including:
Precise and consistent heating
Induction heating allows for precise and consistent heating of the workpiece, resulting in a stronger and more reliable weld. This is because induction heating can be directed to specific areas of the material and controlled to avoid overheating or under heating.
Fast heating times
Induction heating can heat up materials much faster than other heating methods, resulting in faster welding times and increased productivity.
Efficient energy use
Induction heaters are energy efficient and waste less energy compared to other heating methods. This can result in cost savings and reduced environmental impact.
Cleaner process
Induction heating is a cleaner process compared to gas or flame heating methods, as it does not produce harmful fumes or waste energy by heating the surrounding air. This results in a safer and more environmentally friendly welding process.
Customizable
Industrial induction heaters can be customized to meet the specific needs of the welding application. This includes custom coil designs, power output adjustments, and integration with existing manufacturing processes.
Overall, the use of an industrial induction heater for welding offers several advantages over other heating methods, including precise and consistent heating, fast heating times, efficient energy use, a cleaner process, and customization options. These benefits can result in higher quality and more efficient welding processes, leading to cost savings and increased productivity.
Induction Heater for Various Welding Process
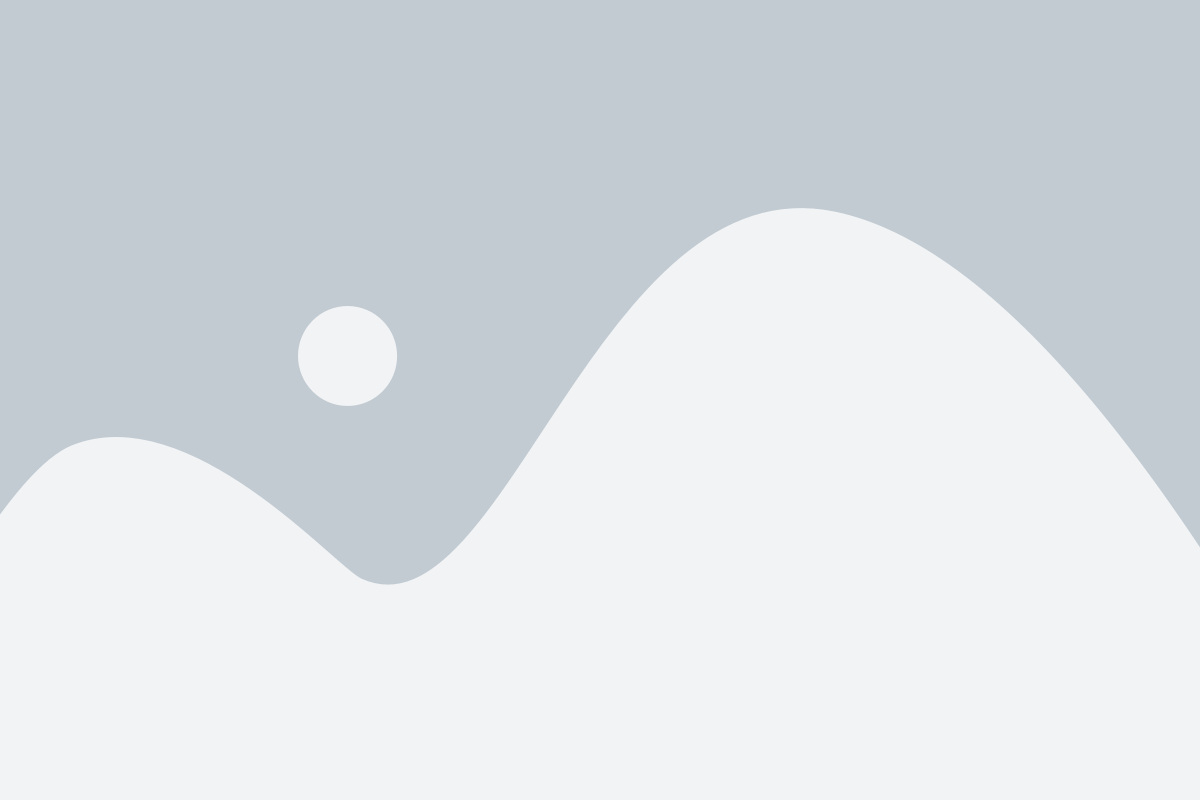
Induction Heater for Welding Tubes
Tubes are often used in various industries such as construction, automotive, and aerospace. Welding tubes require a precise and consistent heating process to ensure the weld is strong and reliable. An induction heater is used to heat the tube before welding. The heater generates an electromagnetic field that induces electrical currents in the material, resulting in rapid and even heating. Induction heating is important for welding tubes because it allows for precise control over the heating process, resulting in a stronger and more reliable weld.
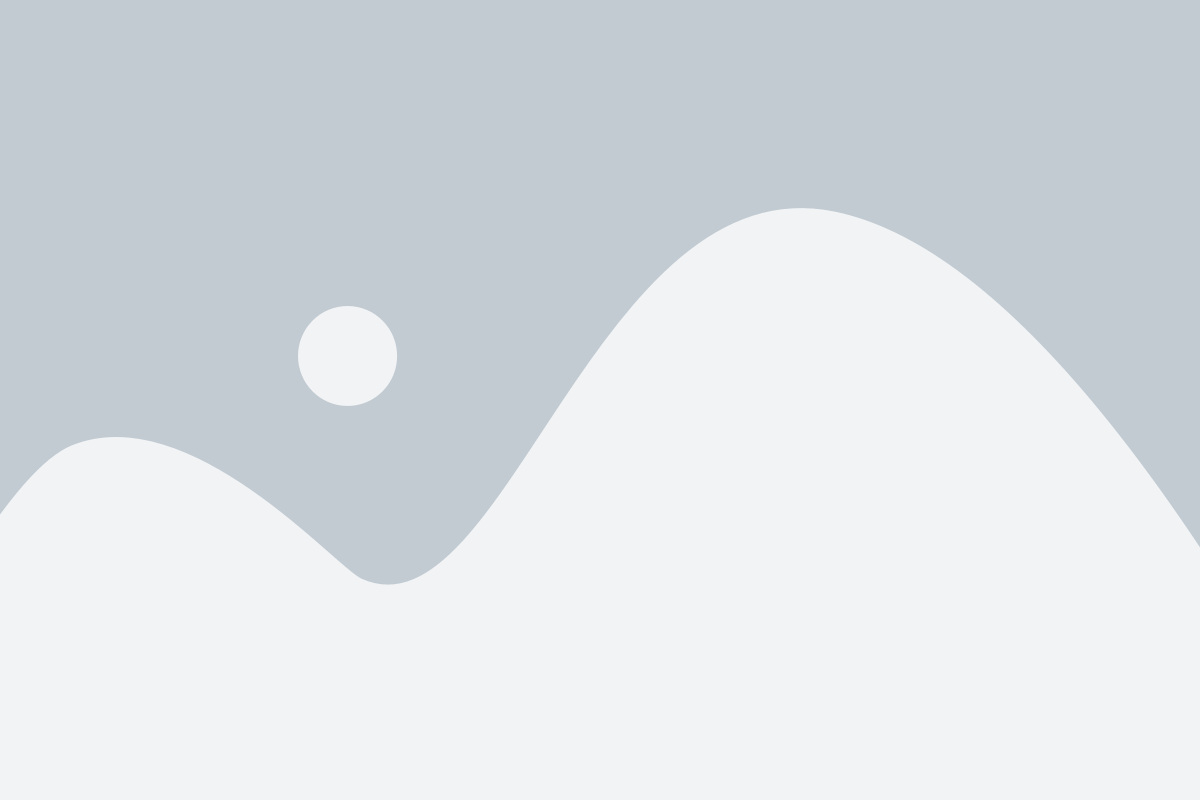
Induction Heater for Welding Sheets
Sheets are commonly used in the manufacturing of products such as automotive parts, appliances, and electronic devices. Welding sheets requires a uniform and controlled heating process to ensure a strong and consistent weld. An induction heater is used to heat the sheet before welding. The heater generates an electromagnetic field that heats the material evenly and quickly. Induction heating is important for welding sheets because it allows for precise control over the heating process, resulting in a stronger and more reliable weld.
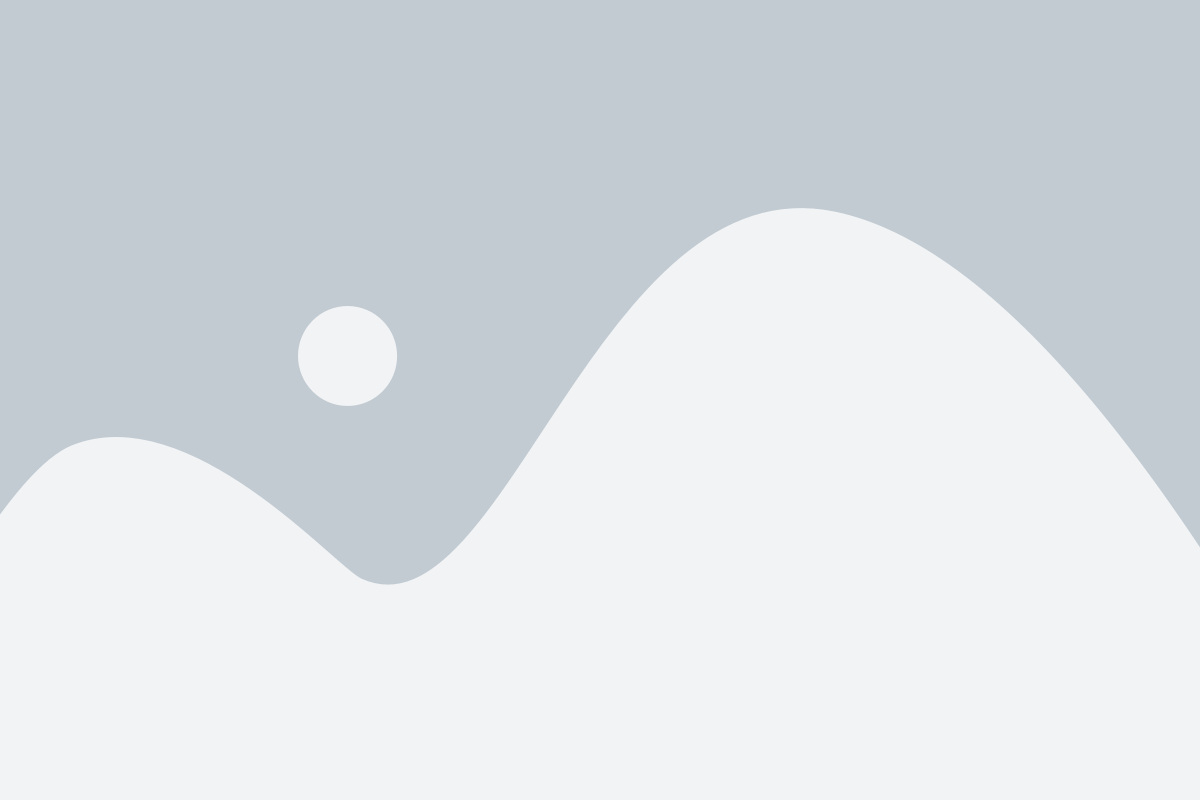
Induction Heater for Welding Wires
Wires are used in a variety of industries such as electronics, telecommunications, and aerospace. Welding wires require a quick and precise heating process to ensure a strong and consistent weld. An induction heater is used to heat the wire before welding. The heater generates an electromagnetic field that heats the material rapidly and uniformly. Induction heating is important for welding wires because it allows for a quick and precise heating process, resulting in a stronger and more reliable weld.
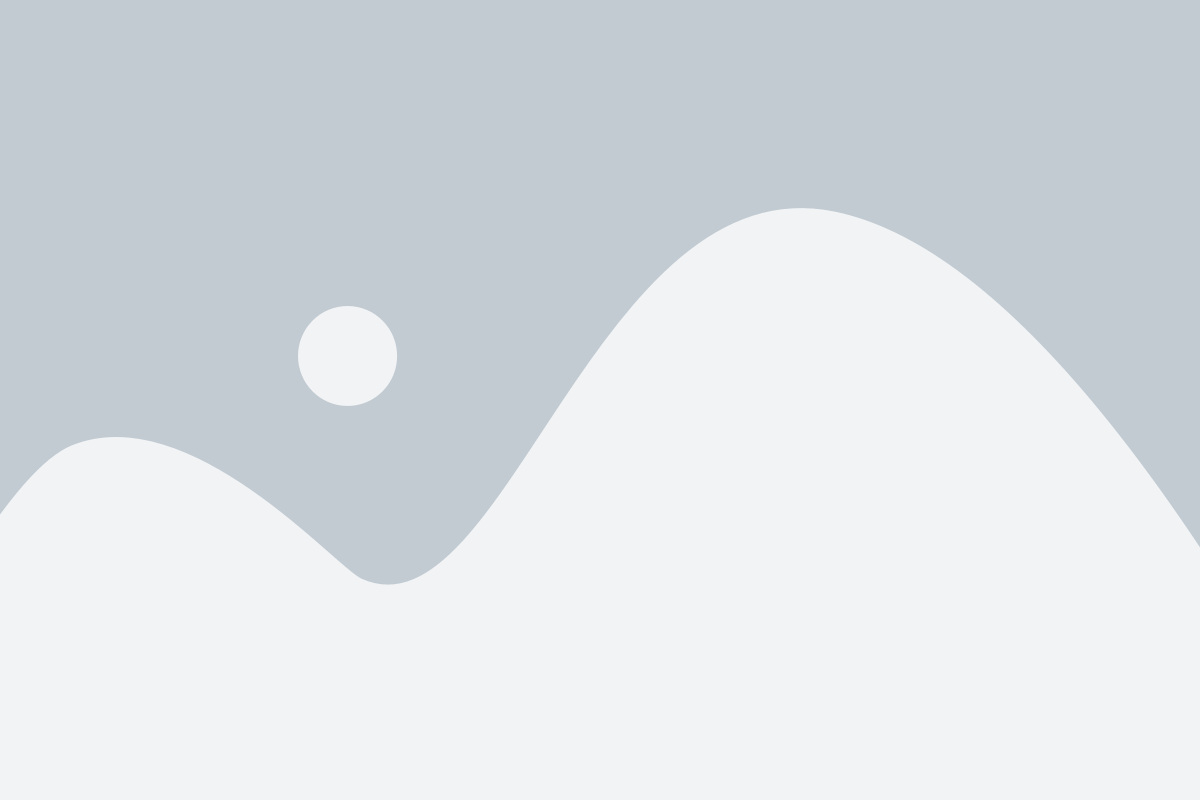
Induction Heater for Welding Bars
Bars are used in various industries such as construction, automotive, and manufacturing. Welding bars require a uniform and controlled heating process to ensure a strong and consistent weld. An induction heater is used to heat the bar before welding. The heater generates an electromagnetic field that heats the material evenly and quickly. Induction heating is important for welding bars because it allows for precise control over the heating process, resulting in a stronger and more reliable weld.
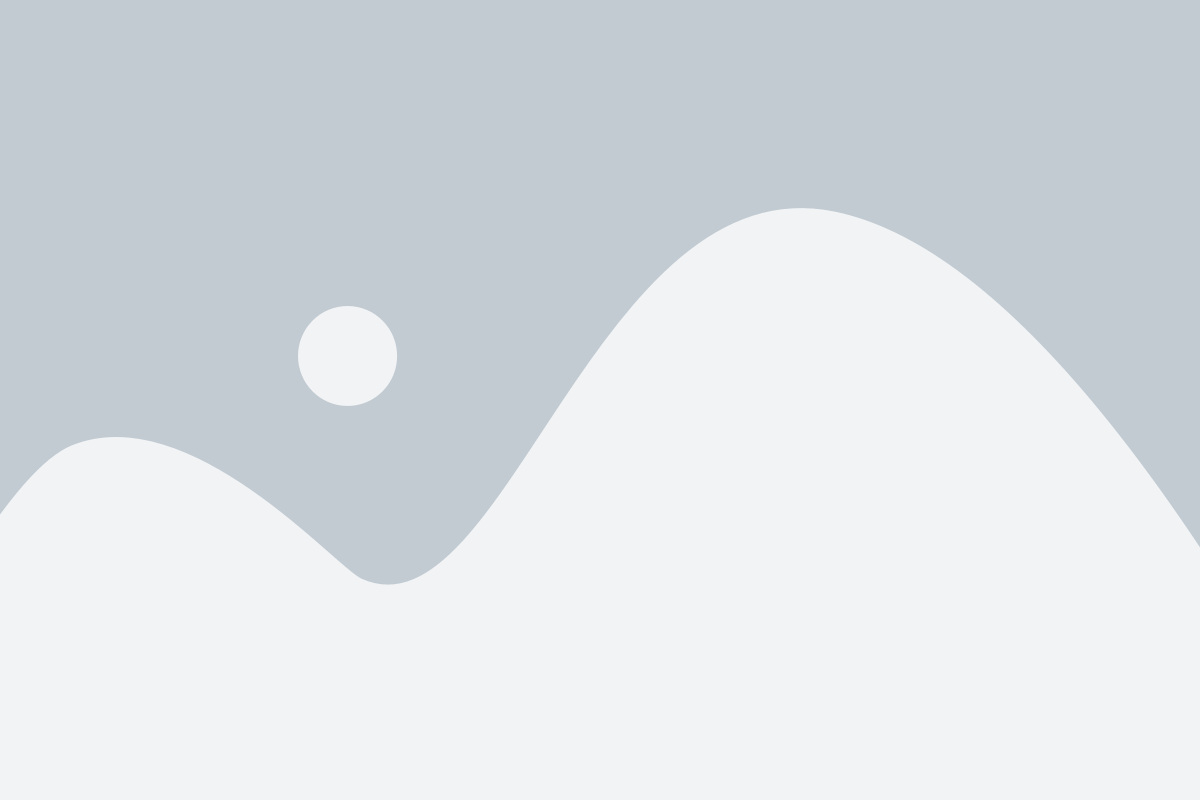
Induction Heater for Welding Gears
Gears are used in various industries such as automotive, aerospace, and manufacturing. Welding gears require a precise and consistent heating process to ensure a strong and reliable weld. An induction heater is used to heat the gear before welding. The heater generates an electromagnetic field that induces electrical currents in the material, resulting in rapid and even heating. Induction heating is important for welding gears because it allows for precise control over the heating process, resulting in a stronger and more reliable weld.
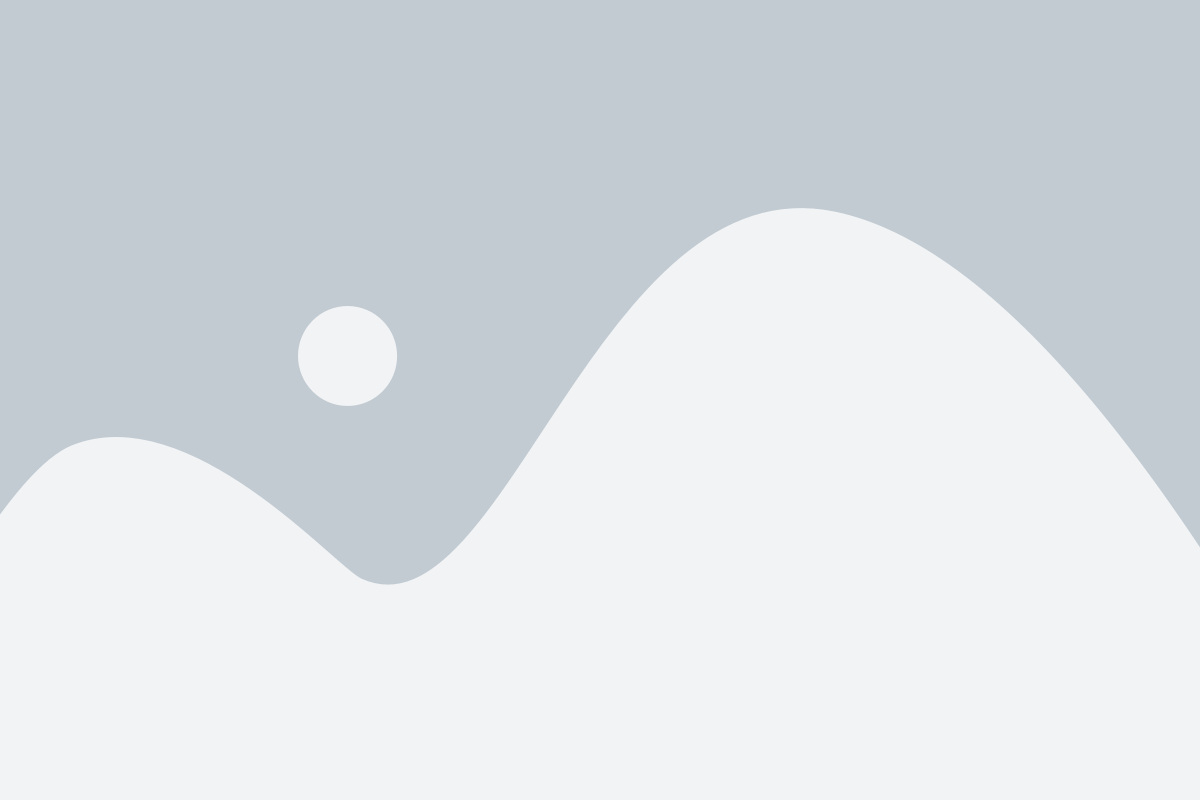
Induction Heater for Welding Bearings
Bearings are used in a variety of industries such as automotive, aerospace, and manufacturing. Welding bearings requires a precise and uniform heating process to ensure a strong and consistent weld. An induction heater is used to heat the bearing before welding. The heater generates an electromagnetic field that heats the material evenly and quickly. Induction heating is important for welding bearings because it allows for precise control over the heating process, resulting in a stronger and more reliable weld.
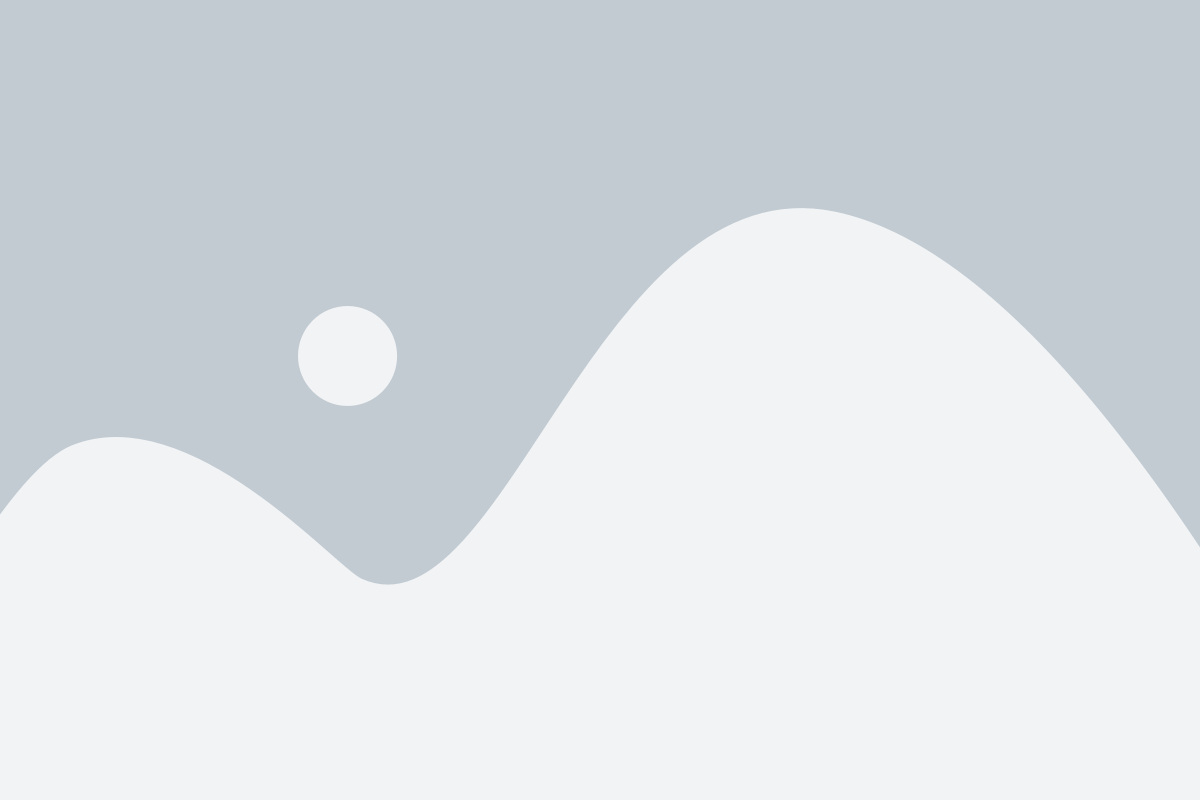
Induction Heater for Welding Engine Blocks
Engine blocks are a critical component in the automotive industry. Welding engine blocks requires a precise and uniform heating process to ensure a strong and consistent weld. An induction heater is used to heat the engine block before welding. The heater generates an electromagnetic field that heats the material evenly and quickly. Induction heating is important for welding engine blocks because it allows for precise control over the heating process, resulting in a stronger and more reliable weld.
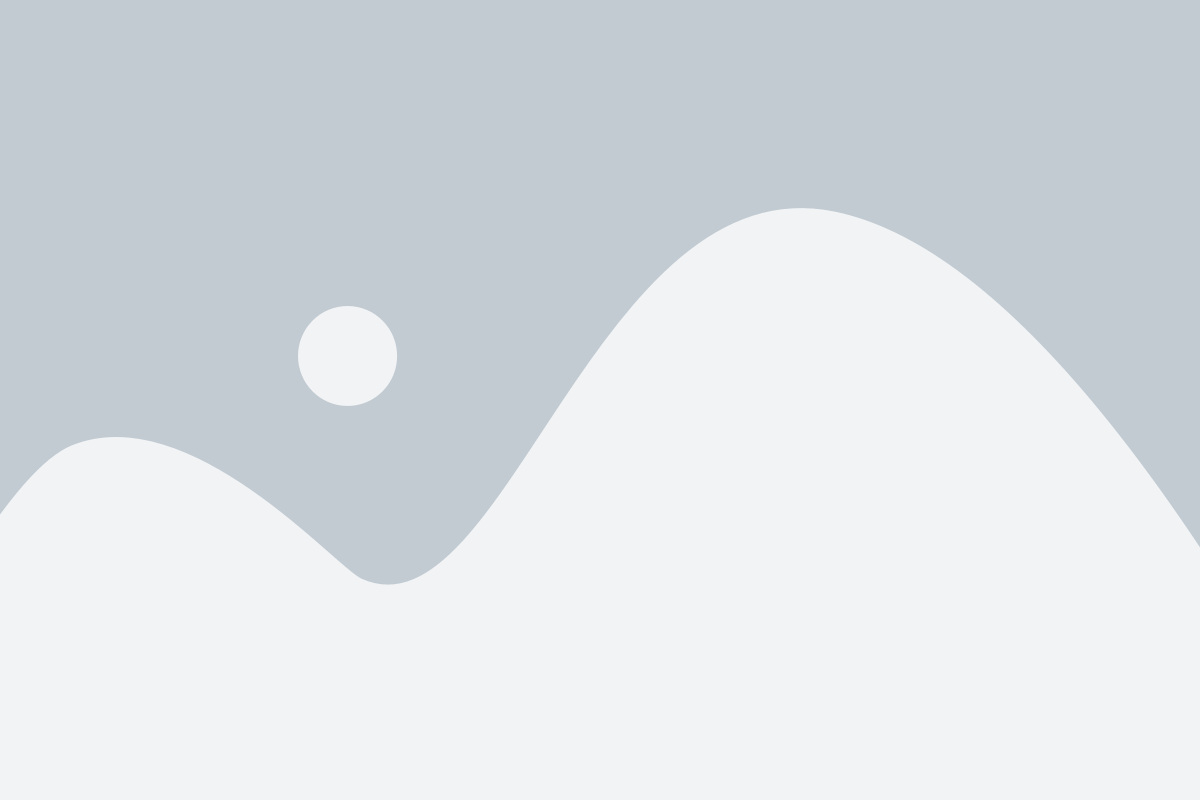
Induction Heater for Welding Cylinder Heads
Cylinder heads are an essential component of internal combustion engines that require precise welding to maintain their integrity. Induction heating is commonly used for welding cylinder heads due to its accuracy and efficiency. In the process, the cylinder head is heated with an induction heater to a precise temperature before being welded. This process ensures that the weld is strong and does not crack due to thermal stresses. Induction heating also provides uniform heating, which minimizes the risk of distortion and warping of the cylinder head during the welding process.
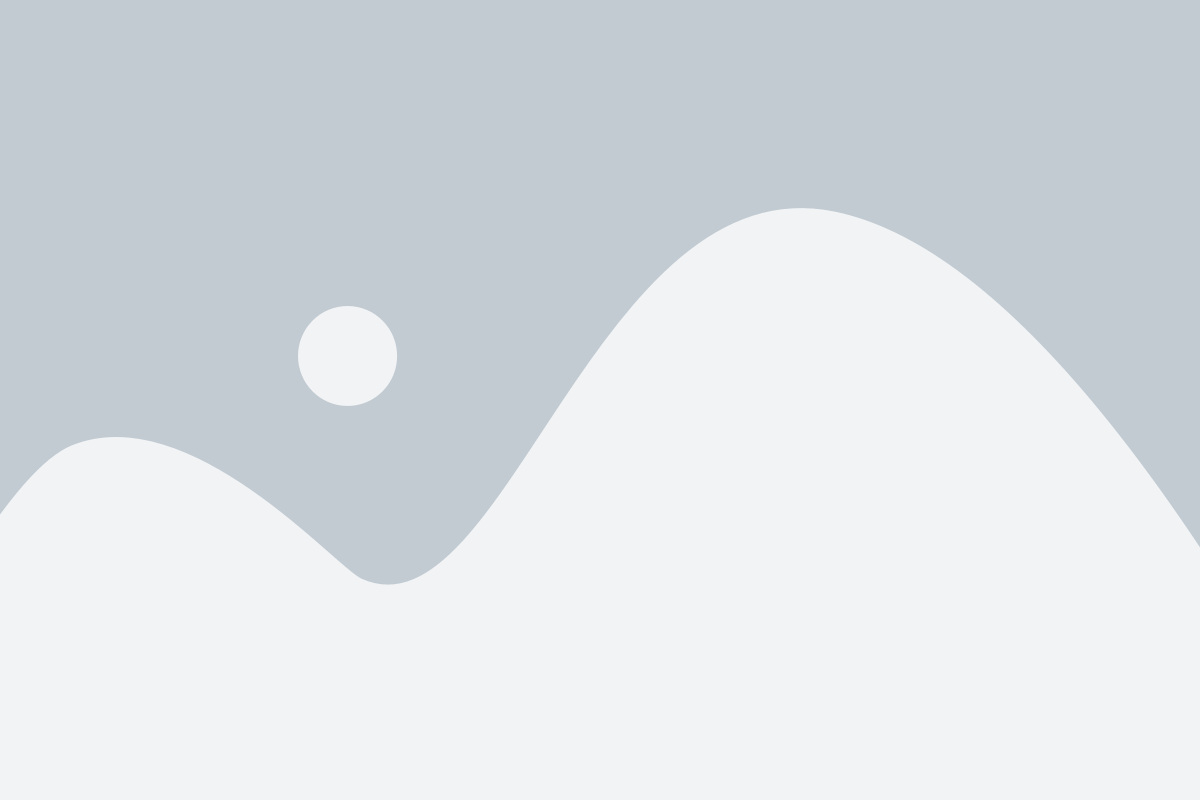
Induction Heater for Welding Axles
Axles are used in a variety of applications, including vehicles, machinery, and equipment. Welding of axles requires precise heating and control to ensure that the weld is strong and durable. Induction heating is a popular method for welding axles due to its speed, accuracy, and efficiency. The process involves heating the axle to a precise temperature using an induction heater before welding. This method ensures that the weld is strong and does not crack due to thermal stresses. Induction heating also provides uniform heating, which minimizes the risk of distortion and warping of the axle during the welding process.
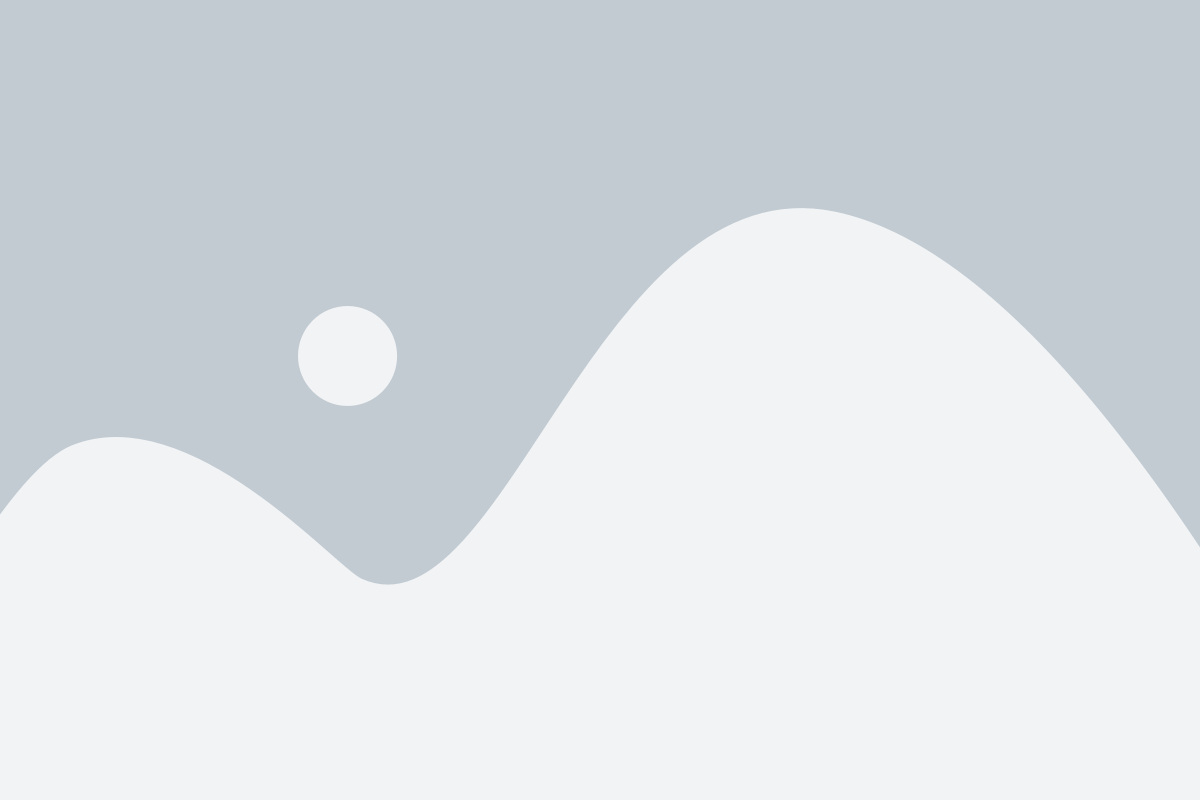
Induction Heater for Welding Hubs
Hubs are used in a variety of applications, including vehicles, machinery, and equipment. Welding of hubs requires precise heating and control to ensure that the weld is strong and durable. Induction heating is a popular method for welding hubs due to its speed, accuracy, and efficiency. The process involves heating the hub to a precise temperature using an induction heater before welding. This method ensures that the weld is strong and does not crack due to thermal stresses. Induction heating also provides uniform heating, which minimizes the risk of distortion and warping of the hub during the welding process.
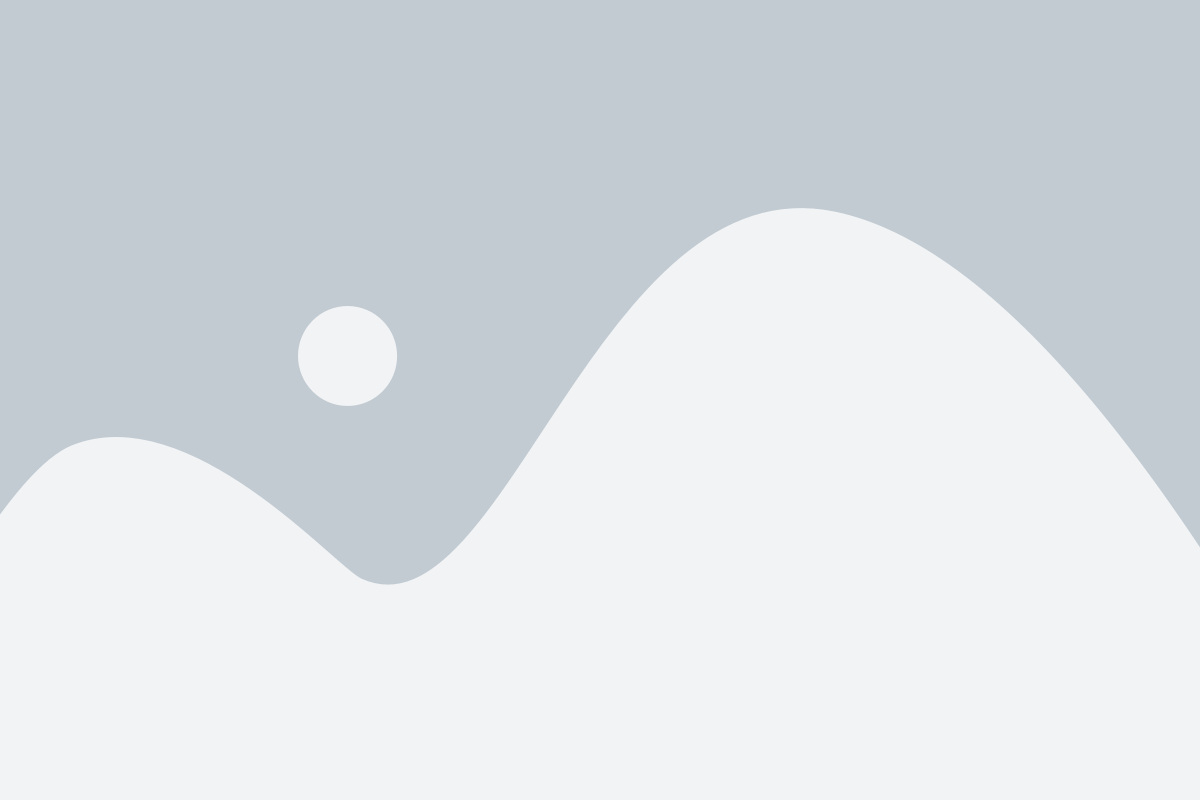
Induction Heater for Welding Motors
Motors are used in a wide range of applications, from small electronic devices to heavy machinery. Welding of motors requires precise heating and control to ensure that the weld is strong and durable. Induction heating is a popular method for welding motors due to its speed, accuracy, and efficiency. The process involves heating the motor to a precise temperature using an induction heater before welding. This method ensures that the weld is strong and does not crack due to thermal stresses. Induction heating also provides uniform heating, which minimizes the risk of distortion and warping of the motor during the welding process.
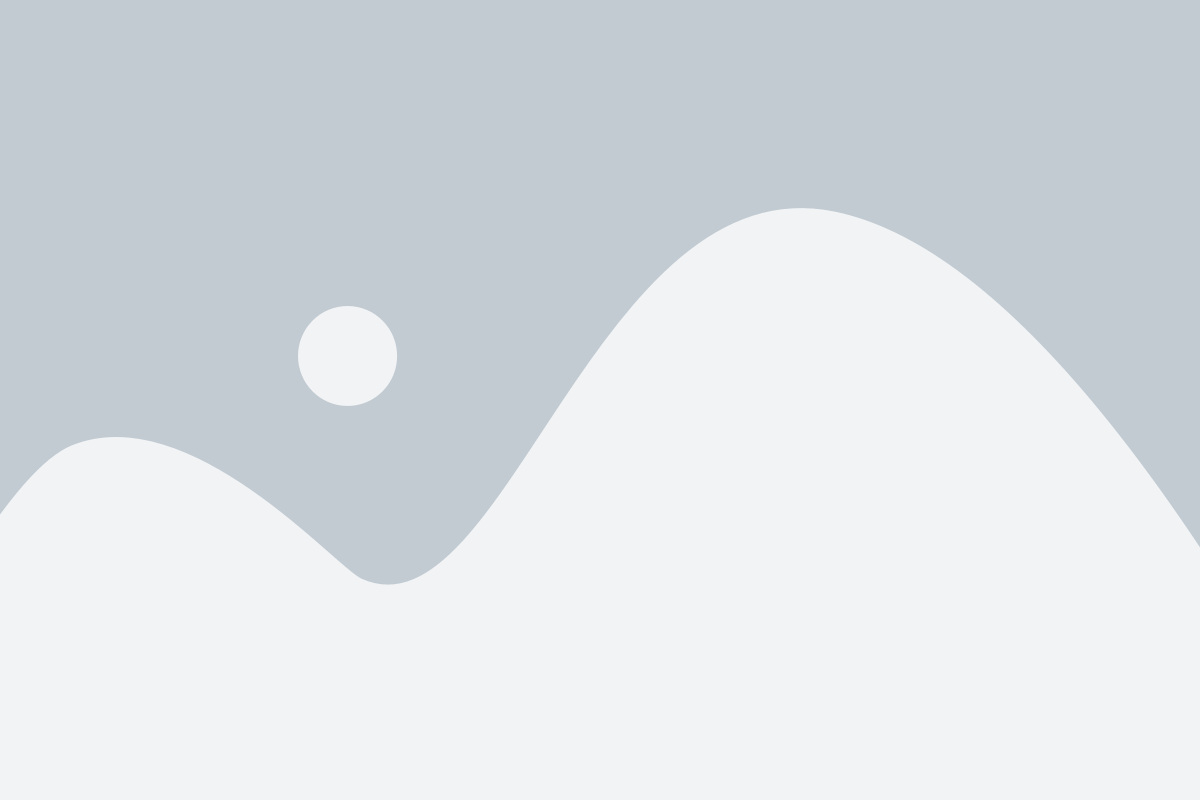
Induction Heater for Welding Heat Exchangers
Heat exchangers are used in a wide range of industrial applications, including power generation, chemical processing, and HVAC systems. Welding of heat exchangers requires precise heating and control to ensure that the weld is strong and durable. Induction heating is a popular method for welding heat exchangers due to its speed, accuracy, and efficiency. The process involves heating the heat exchanger to a precise temperature using an induction heater before welding. This method ensures that the weld is strong and does not crack due to thermal stresses. Induction heating also provides uniform heating, which minimizes the risk of distortion and warping of the heat exchanger during the welding process.
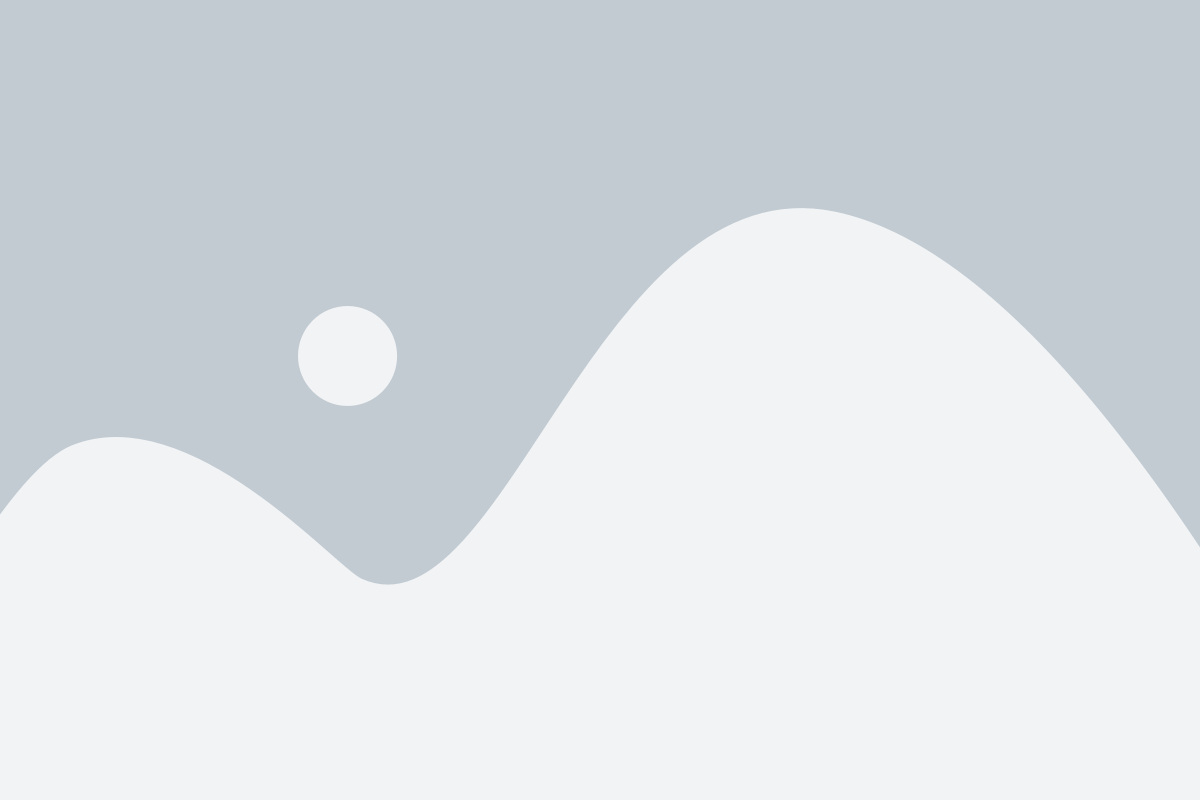
Induction Heater for Welding Radiators
Radiators are used in a wide range of applications, including vehicles, HVAC systems, and industrial machinery. Welding of radiators requires precise heating and control to ensure that the weld is strong and durable. Induction heating is a popular method for welding radiators due to its speed, accuracy, and efficiency. The process involves heating the radiator to a precise temperature using an induction heater before welding. This method ensures that the weld is strong and does not crack due to thermal stresses. Induction heating also provides uniform heating, which minimizes the risk of distortion and warping of the radiator during the welding process.
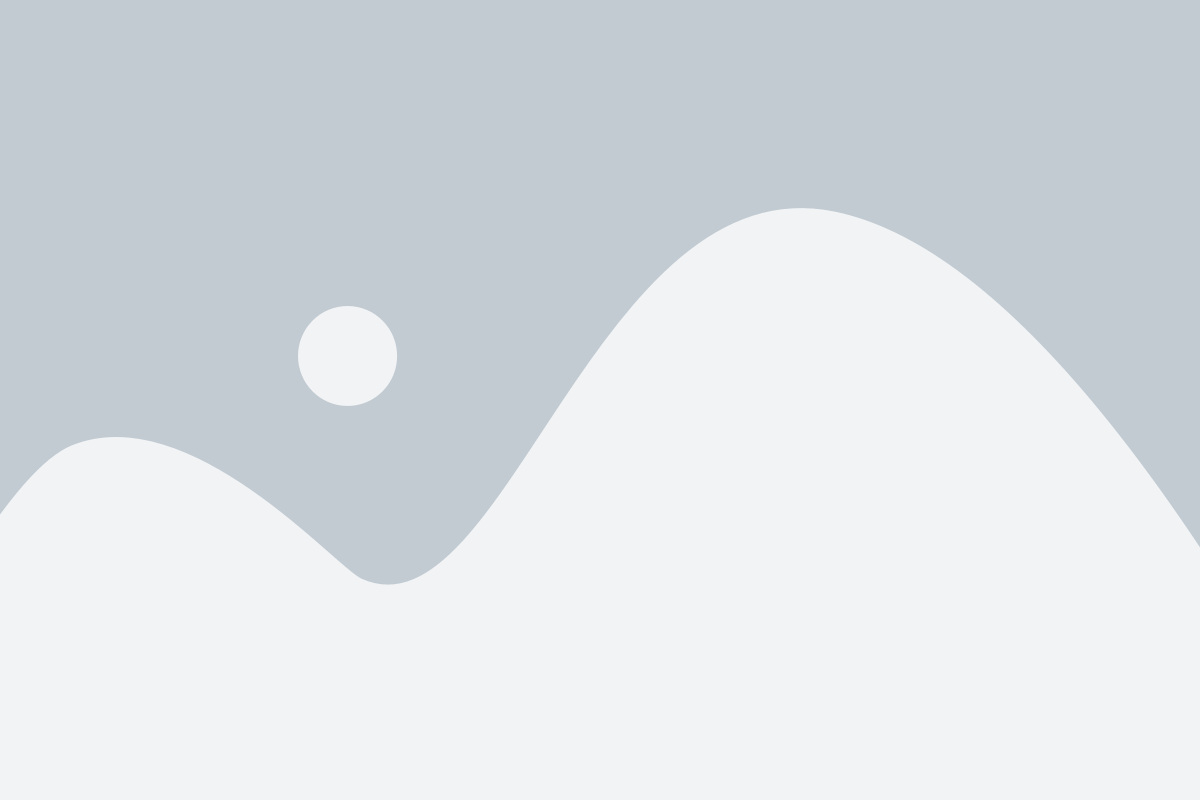
Induction Heater for Welding Transformers
Transformers are essential components in power generation, transmission, and distribution systems. They work by transferring electrical energy from one circuit to another through the principle of electromagnetic induction. Transformers are typically made of copper or aluminium coils wound around a magnetic core. The coils need to be joined and welded to form a continuous electrical circuit. Induction heating is the most effective method for welding transformer coils. The process involves using an induction heater to heat the coils to the required temperature without any contact with the heating element. This method allows for precise and controlled heating of the coils, which is critical for welding high-quality transformer components. Induction heating is important for welding transformers because it provides consistent and reliable heat to the coils, resulting in stronger welds and increased durability. Additionally, because induction heating is a non-contact process, it eliminates the risk of contamination from the heating element, ensuring a clean and high-quality weld.
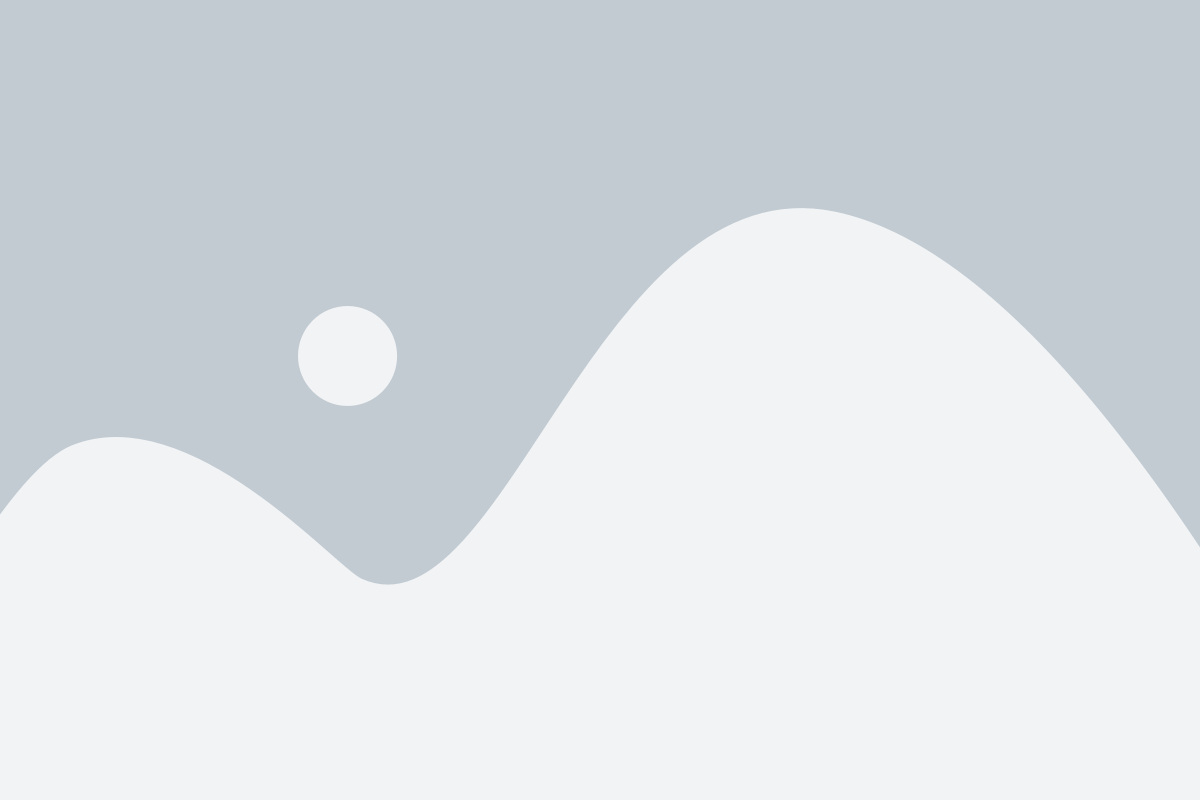
Induction Heater for Welding Generators
Generators are used to convert mechanical energy into electrical energy. They consist of a rotor, a stator, and a magnetic field. The stator is typically made up of copper or aluminium windings that are welded together to create a continuous electrical circuit. Induction heating is an effective method for welding generator stators. The process involves using an induction heater to heat the stator windings to the required temperature without any contact with the heating element. This method allows for precise and controlled heating of the stator windings, which is critical for welding high-quality generator components. Induction heating is important for welding generators because it provides consistent and reliable heat to the stator windings, resulting in stronger welds and increased durability. Additionally, because induction heating is a non-contact process, it eliminates the risk of contamination from the heating element, ensuring a clean and high-quality weld. The use of an induction heater also reduces the risk of damage to the stator windings due to overheating or uneven heating, which can result in costly repairs or replacements.
Induction Heaters Offered by GM Industries
For more information on any of our high quality products or getting accurate prices contact GM Industries at
Call Us
+(91)-9820533489 / 7738562224
Enquiry Form
Submit
Frequently Asked Questions
An induction heater works by using electromagnetic induction to heat the metal parts. The heater produces a high-frequency magnetic field that induces electrical currents in the metal, which in turn creates heat.
An induction heater can be used to weld a wide range of metals, including steel, aluminum, copper, and brass.
Yes, induction heaters can be used for both manual and automated welding processes, depending on the specific application.
Yes, induction heating is a safe and environmentally friendly process as it does not produce any harmful emissions or require the use of hazardous chemicals.
Induction heaters can reach temperatures up to 2,500°F (1,370°C), depending on the specific application.
Yes, induction heaters can be used for brazing and soldering as well as welding.
Induction heating offers faster heating times, more precise and controlled heating, and increased efficiency compared to other heating methods.
The heating time depends on the size and type of metal part, but typically ranges from a few seconds to a few minutes.
Yes, induction heaters can be used in hazardous environments as they do not produce any open flames or require the use of fuel.
Yes, induction heaters can be used for both small and large metal parts, depending on the specific application.
Induction heating offers faster and more precise heating, and produces stronger and more durable welds compared to traditional welding methods.
Regular cleaning and inspection of the induction heater is required to ensure proper functioning and prevent any damage or wear.
Yes, induction heaters can be used for both production and repair welding applications.
The cost of an induction heater for welding depends on the specific application and requirements, but generally ranges from several thousand to tens of thousands of dollars.
Consulting with an experienced welding supplier or manufacturer can help determine the appropriate induction heater for your specific application and requirements.
Operators should wear appropriate personal protective equipment, and follow all safety procedures and guidelines provided by the manufacturer.
Yes, training is required to operate an induction heater safely and effectively.
Yes, induction heaters can be used in conjunction with other welding methods, such as gas and electric welding, to enhance the overall welding process.