Mounting Induction Heater
What is Mounting?
Mounting refers to the process of securely attaching or fixing an object or component to a support or base. This can involve using fasteners, adhesives, or other mechanical means to ensure that the object is held firmly in place. Mounting is commonly used in a variety of applications, such as in electronics, where components may need to be mounted onto a circuit board, or in construction, where fixtures and fittings are mounted onto walls or other surfaces. The specific method of mounting used will depend on the type and size of the object being mounted, as well as the requirements of the application. The most common method used for mounting is mechanical mounting, which involves using tools such as presses, hammers, and bearings to press-fit components onto a shaft or housing. However, in recent years, induction heating has become increasingly popular due to its ability to provide a quick, safe, and efficient method for expanding the inner diameter of components for mounting.
Why is the Induction Heater used for Mounting Processes?
An induction heater is used in mounting processes because it can quickly, safely, and efficiently expand the inner diameter of components for easy installation onto a shaft or housing. The electromagnetic induction process generates heat in the workpiece, allowing for precise temperature control to achieve the desired level of expansion. This method of heating eliminates the need for open flames or hot gases, making it a safer and more environmentally friendly alternative to traditional heating methods. Furthermore, induction heating can help ensure consistent quality and performance during the mounting process, resulting in increased reliability and reduced downtime.
Introduction to Industrial Induction Heater for Mounting
The action of installing or fastening parts, such as bearings, pinions, couplings, gears, etc. to larger systems or structures is referred to as mounting. The fitting of the component onto the proper shaft or housing, verification of its alignment, and securing it in place with the proper torque or fasteners constitute the mounting procedure. The effectiveness of the mounting procedure is essential to the equipment’s correct operation and durability, and poor mounting can result in excessive wear, noise, vibration, and even catastrophic failure. It could be necessary to use specialised equipment and methods to make sure the mounting procedure is done properly. Industrial induction heater is a device that produces heat inside a workpiece using electromagnetic induction. The workpiece can be expanded using this heat, which will make it simpler to place it into a shaft or housing. Induction heaters can be very helpful when mounting bearings because the heat they produce can expand the inner race of the bearing, making it simpler to fit onto the shaft. GM Industries is a prominent manufacturer and supplier of industrial induction heaters for a wide range of processes. Processes like mounting require precise and controlled heating, which is made possible by the high level of control offered by induction heating technology.
Advantages of Using an Industrial Induction Heater for Mounting
Using an industrial induction heater for mounting applications provides several advantages, including:
Efficiency
Induction heaters are a fast and efficient method for heating and expanding components, reducing the time and labour required for mounting.
Precision
Induction heating allows for precise temperature control, ensuring that the component is heated to the correct temperature for mounting without being overheated or damaged.
Safety
Induction heating eliminates the need for traditional heating methods such as torches, which can be hazardous to operators and damage the components being mounted.
Cost-effective
By reducing the time and labour required for mounting, induction heating can help lower labour costs and improve productivity.
Versatility
Industrial induction heaters can be used for a variety of mounting applications, from bearings and gears to couplings and pinions.
Consistency
Induction heating provides consistent and uniform heating, ensuring that components are mounted correctly and securely every time.
Overall, using an industrial induction heater for mounting applications offers a reliable and efficient solution that can help improve productivity, safety, and cost-effectiveness in industrial processes.
Induction Heater for Various Mounting Process
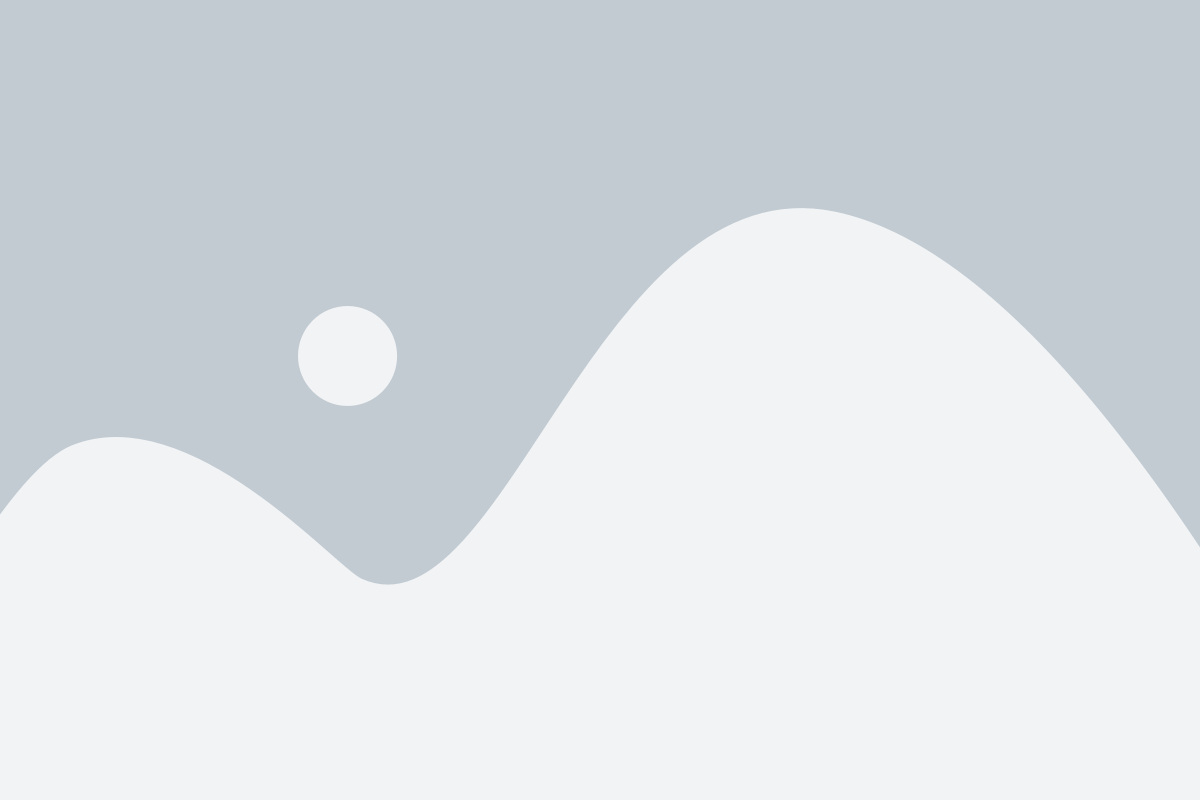
Induction Heater for Bearings
Bearings are components that support the rotation of a shaft or other moving parts. The mounting of bearings involves fitting a bearing onto the shaft or housing, ensuring proper alignment, and securing it in place. The process may involve using specialized tools, such as the Induction Heater. Industrial induction heaters are commonly used for mounting bearings because they provide a quick, safe, and efficient way to expand the bearing’s inner race. When a bearing is heated, it expands, making it easier to install onto a shaft or into a housing.
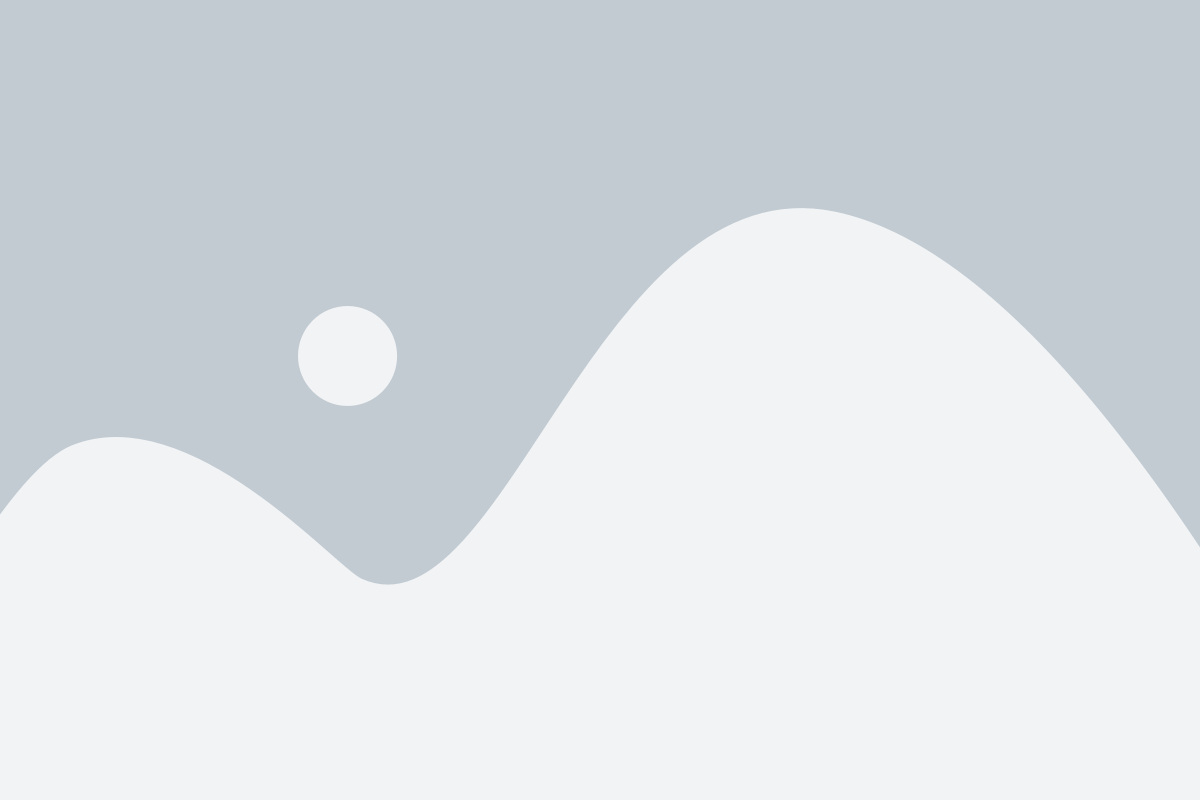
Induction Heater for Pinions
Pinions are gears that are used to transmit torque between rotating shafts. The mounting of pinions involves securing the pinion onto the shaft, ensuring proper alignment, and tightening the fasteners to the specified torque. Induction heaters are also commonly used for mounting pinions onto shafts because they provide a precise and efficient method for expanding the pinion’s bore. Pinions are typically used in gear assemblies and other mechanical systems to transfer torque from one component to another.
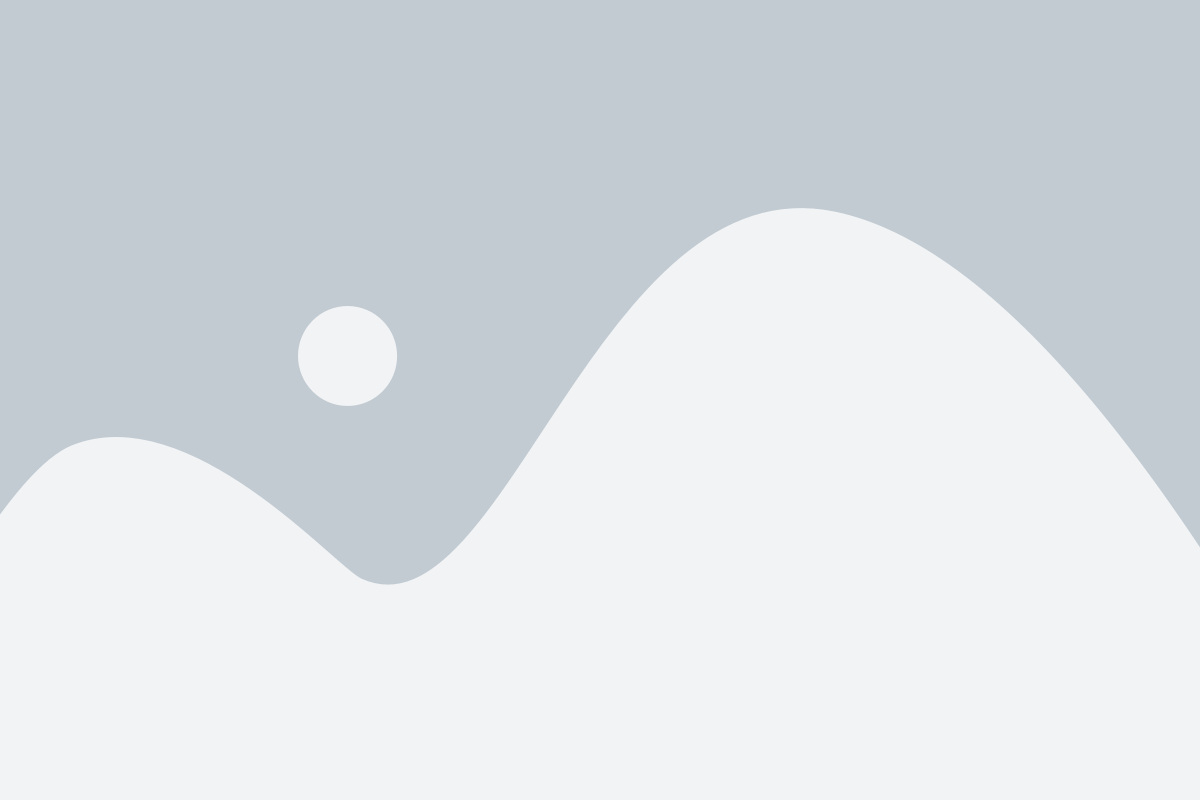
Coupling Induction
Couplings are used to connect two rotating shafts together while allowing for some misalignment and torque transmission. The mounting of couplings involves attaching the coupling halves to the respective shafts, ensuring proper alignment, and tightening the fasteners to the specified torque. Induction heaters are also commonly used for mounting couplings onto shafts because they provide a precise and efficient method for expanding the coupling’s bore. Couplings are typically used in mechanical systems to connect two shafts together
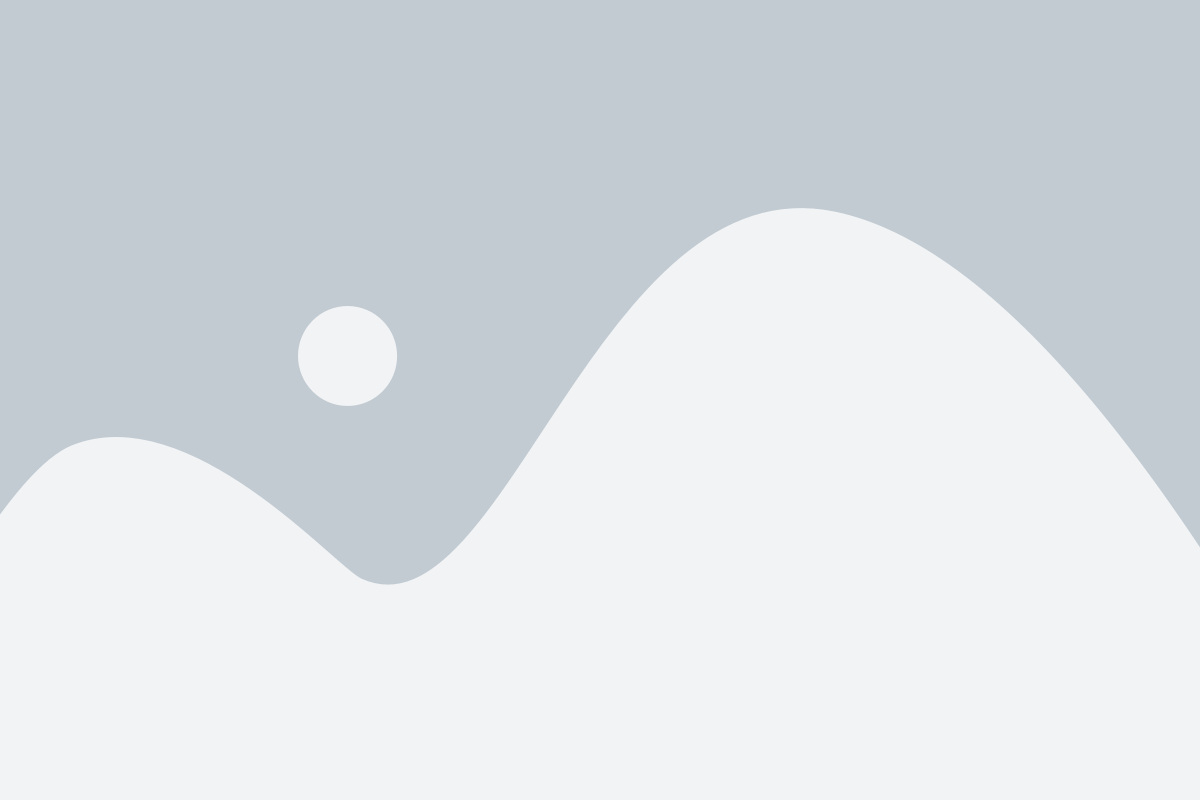
Gear Induction
Gears are components that transmit torque and motion between rotating shafts. The mounting of gears involves fitting the gear onto the shaft, ensuring proper alignment, and securing it in place. The process may involve using specialized tools, such as gear pullers or hydraulic presses, to ensure that the gear is properly seated and has the required clearance. Because they provide a precise and efficient method of expanding the gear’s bore, induction heaters are commonly used for mounting gears on shafts.
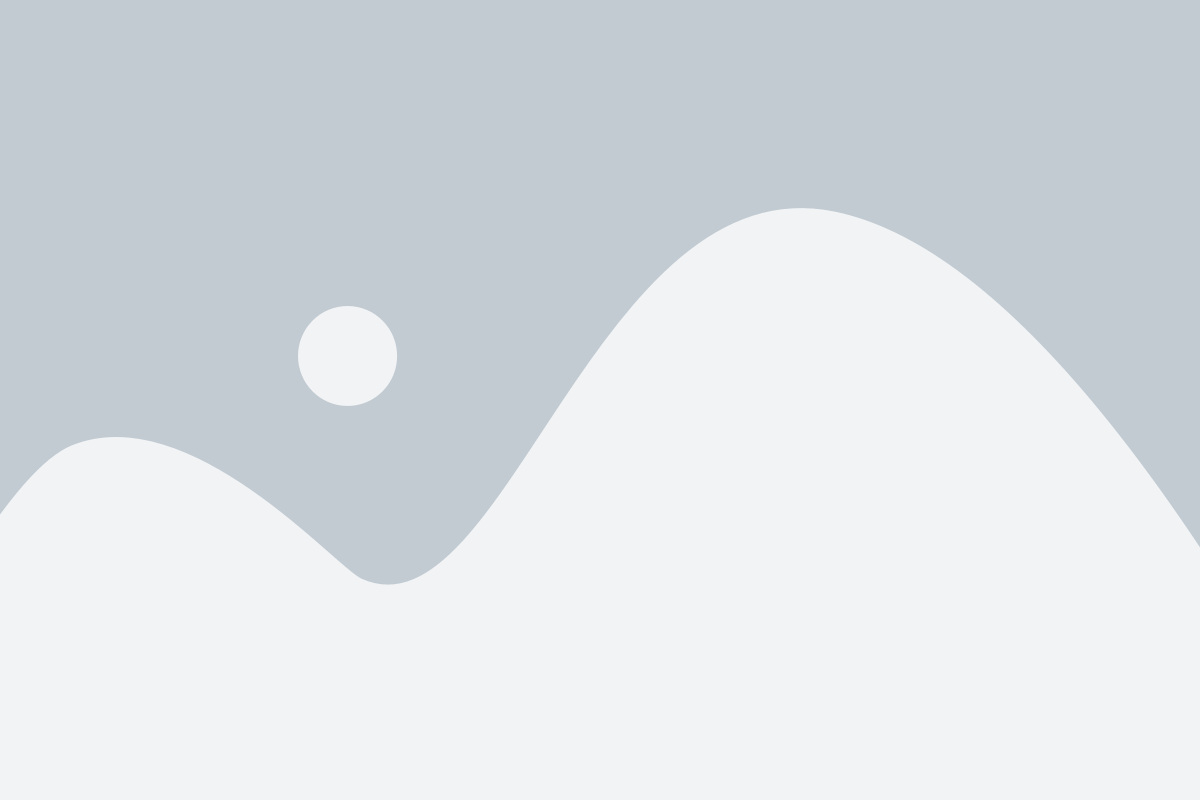
Induction Heater for Shafts
Shafts are critical components in many machines and equipment, and their proper installation is essential for optimal performance and longevity. Induction heaters can be used to heat shafts before mounting bearings, gears, or other components onto them. Induction heating allows for precise and localized heating, which can prevent distortion or damage to the shaft or other components.
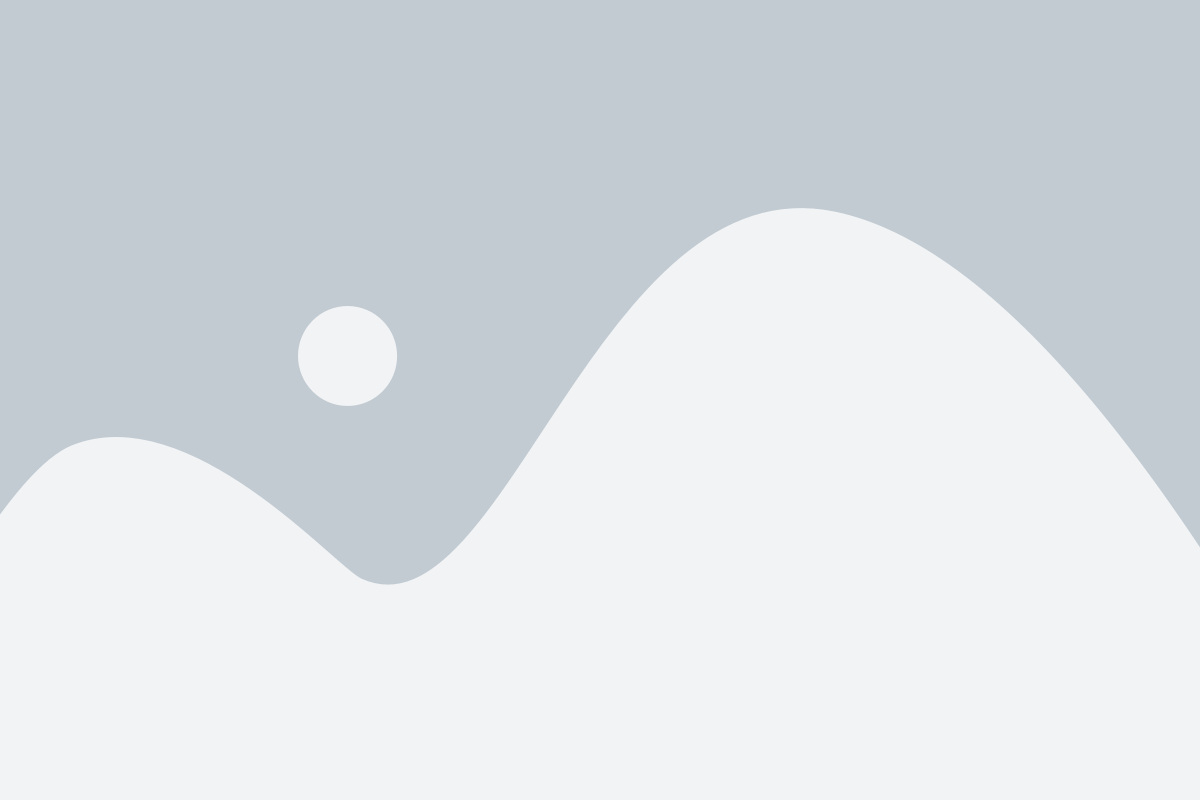
Induction Heater for Sprockets
Sprockets are key components in many industrial applications, and their proper installation is crucial for optimal performance and safety. Induction heaters can be used to heat sprockets before mounting them onto shafts or other components. Induction heating provides quick and efficient heating, which helps to ensure that the sprocket fits securely onto the shaft without damaging or distorting the surrounding components.
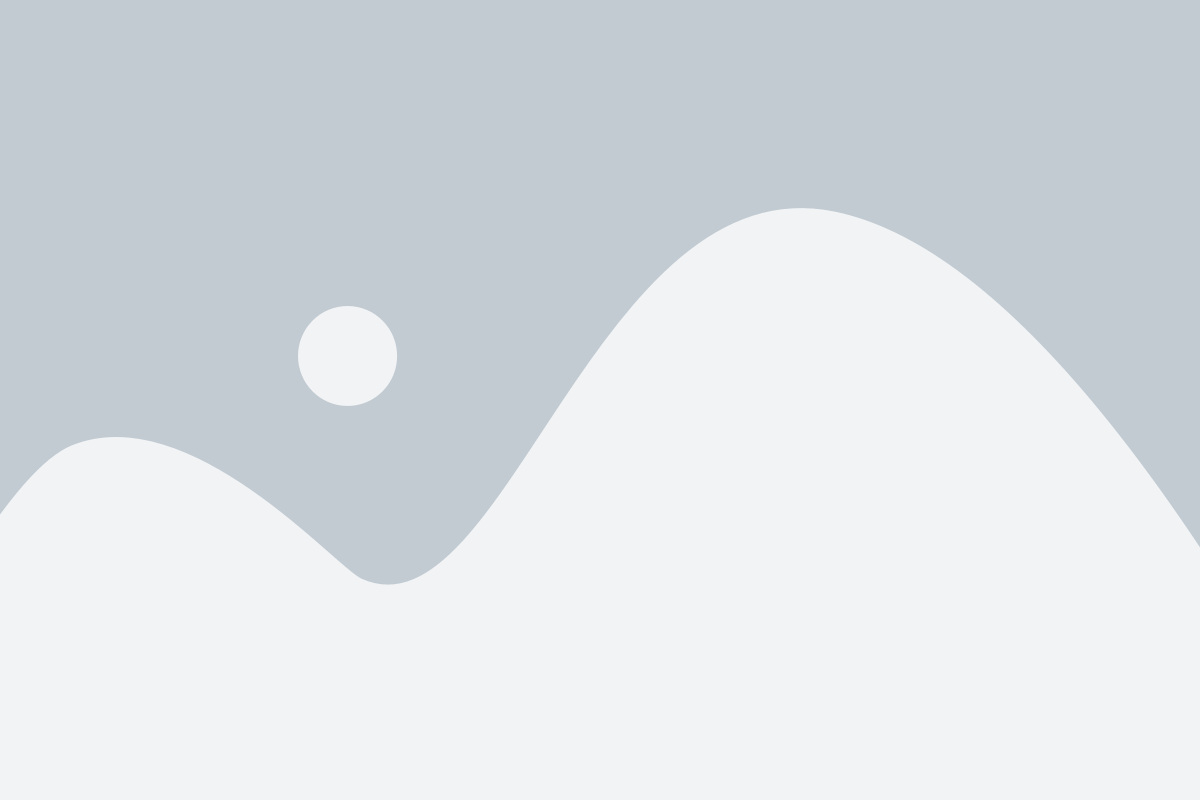
Induction Heater for Sleeves
Sleeves are used in a variety of industrial applications, and their proper installation is critical for optimal performance and safety. Induction heaters can be used to heat sleeves before mounting them onto shafts or other components. Induction heating allows for precise and controlled heating, which helps to ensure that the sleeve fits securely onto the shaft without causing damage or distortion to the surrounding components.
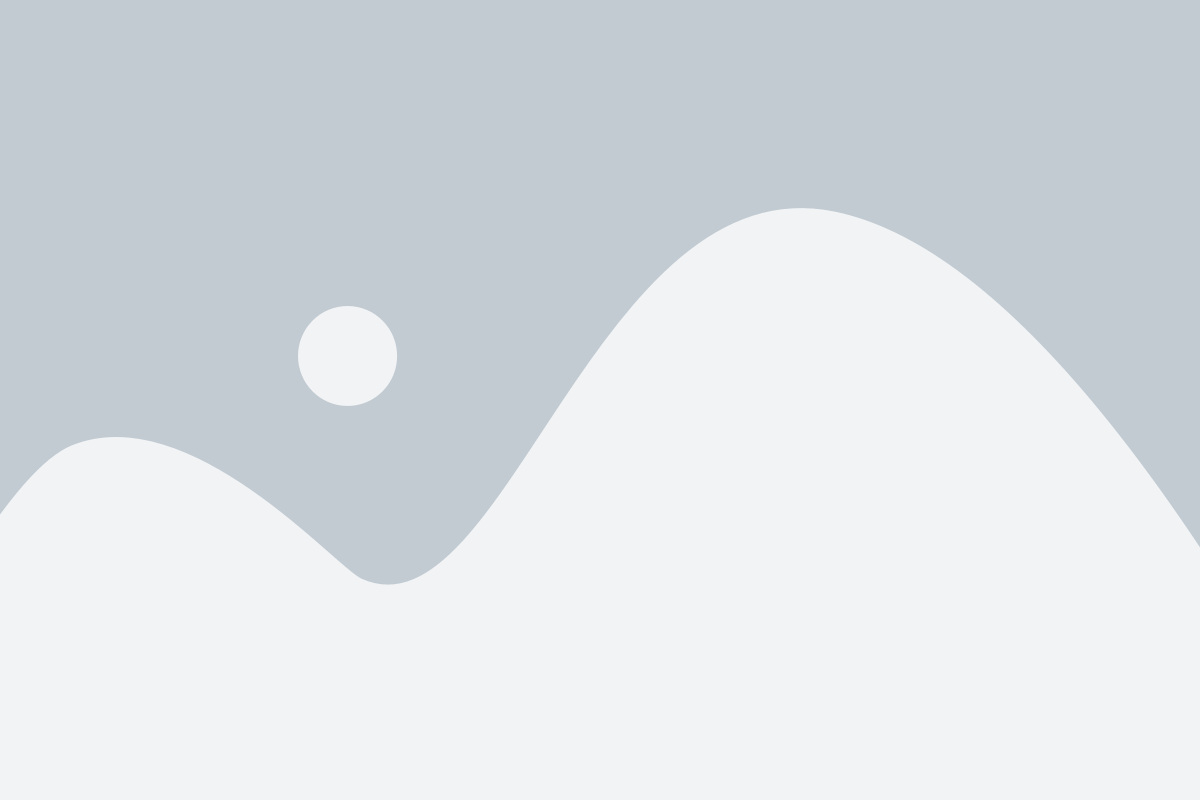
Induction Heating Roller
Rollers are used in many industrial applications, and their proper installation is essential for optimal performance and longevity. Induction heaters can be used to heat rollers before mounting bearings, gears, or other components onto them. Induction heating allows for precise and localized heating, which can prevent distortion or damage to the roller or other components.
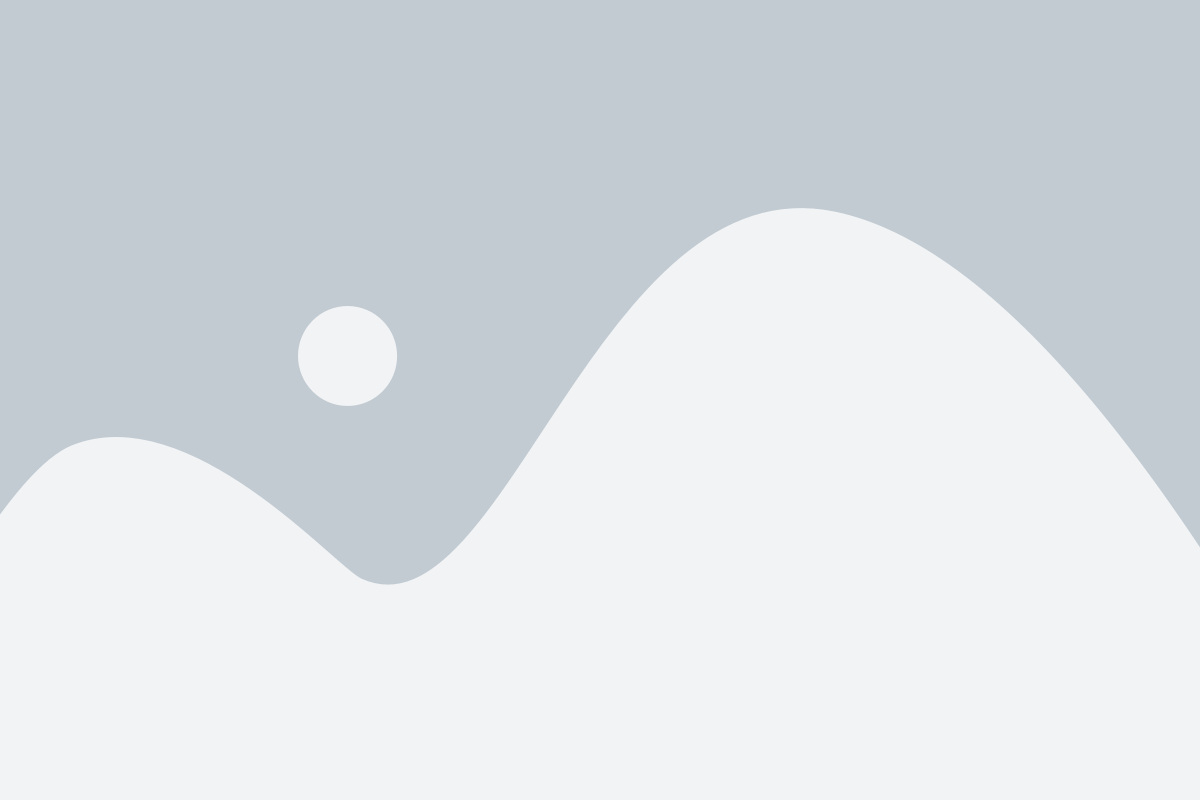
Induction Heater for Bushings
Bushings are used in a variety of industrial applications, and their proper installation is crucial for optimal performance and safety. Induction heaters can be used to heat bushings before mounting them onto shafts or other components. Induction heating provides quick and efficient heating, which helps to ensure that the bushing fits securely onto the shaft without damaging or distorting the surrounding components.
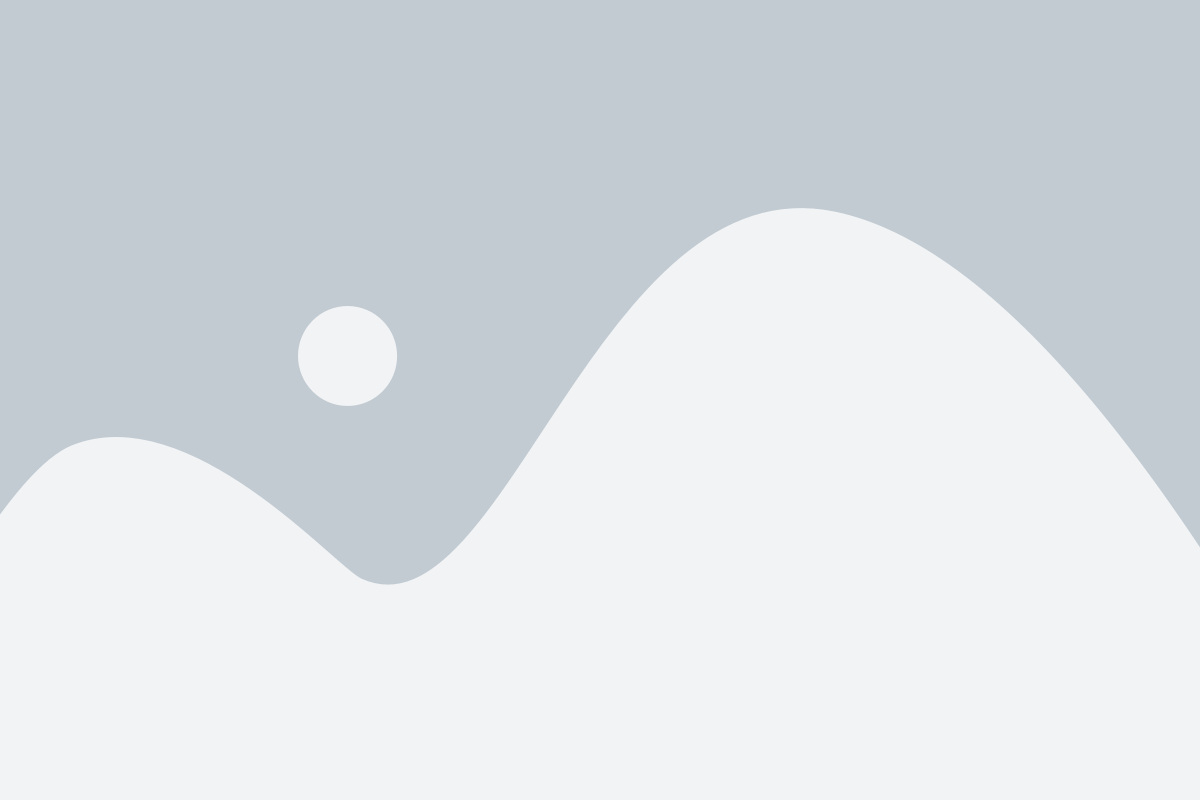
Induction Heater for Hubs
Hubs are critical components in many industrial applications, and their proper installation is essential for optimal performance and safety. Induction heaters can be used to heat hubs before mounting them onto shafts or other components. Induction heating allows for precise and controlled heating, which helps to ensure that the hub fits securely onto the shaft without causing damage or distortion to the surrounding components.
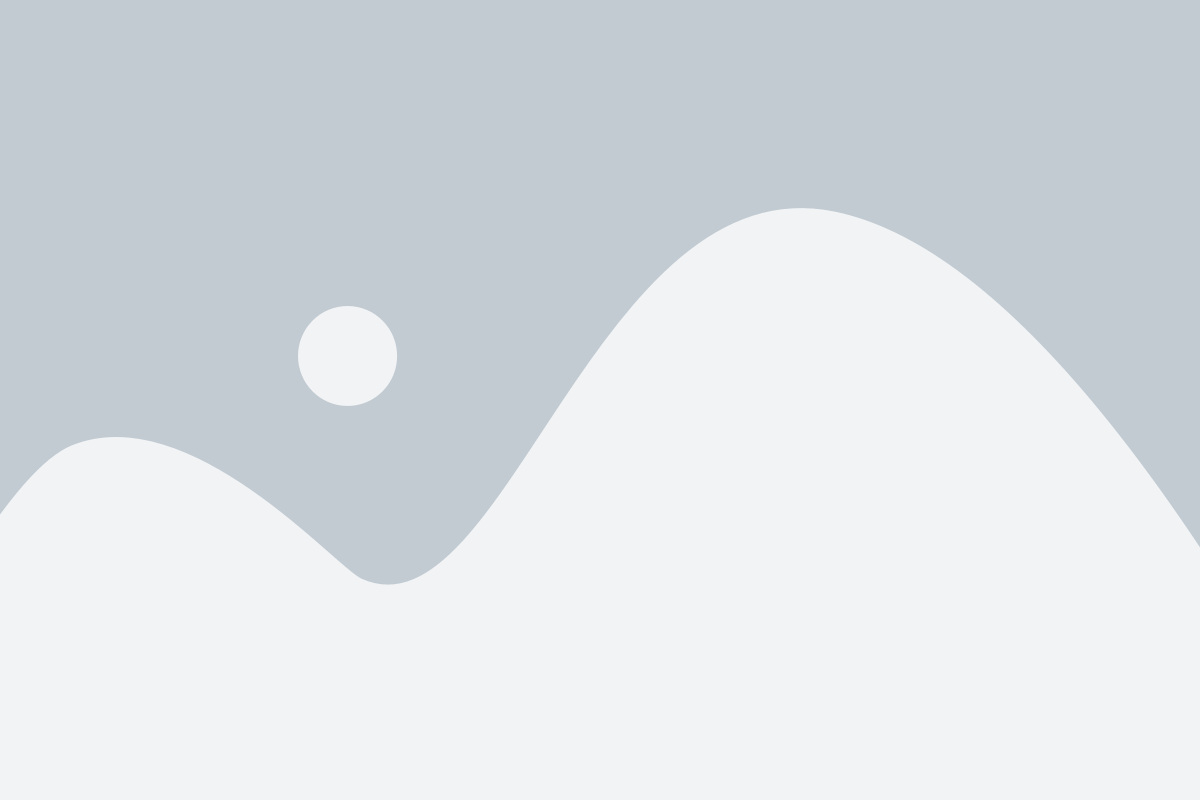
Induction Heater for Pulleys
Pulleys are used in many industrial applications, and their proper installation is crucial for optimal performance and safety. Induction heaters can be used to heat pulleys before mounting them onto shafts or other components. Induction heating provides quick and efficient heating, which helps to ensure that the pulley fits securely onto the shaft without damaging or distorting the surrounding components.
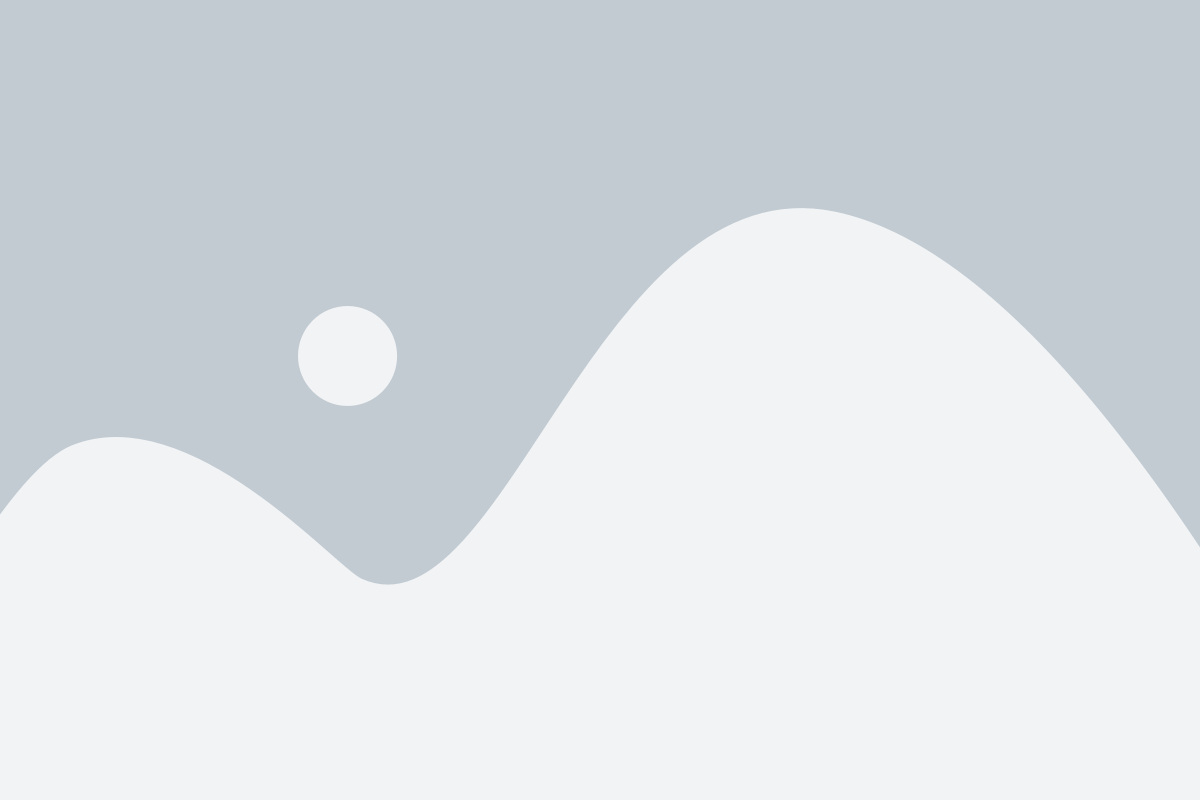
Induction Heater for Cylinders
Cylinders are used in a variety of industrial applications, and their proper installation is critical for optimal performance and safety. Induction heaters can be used to heat cylinders before mounting them onto shafts or other components. Induction heating provides precise and localized heating, which helps to ensure that the cylinder fits securely onto the shaft without causing damage or distortion to the surrounding components.
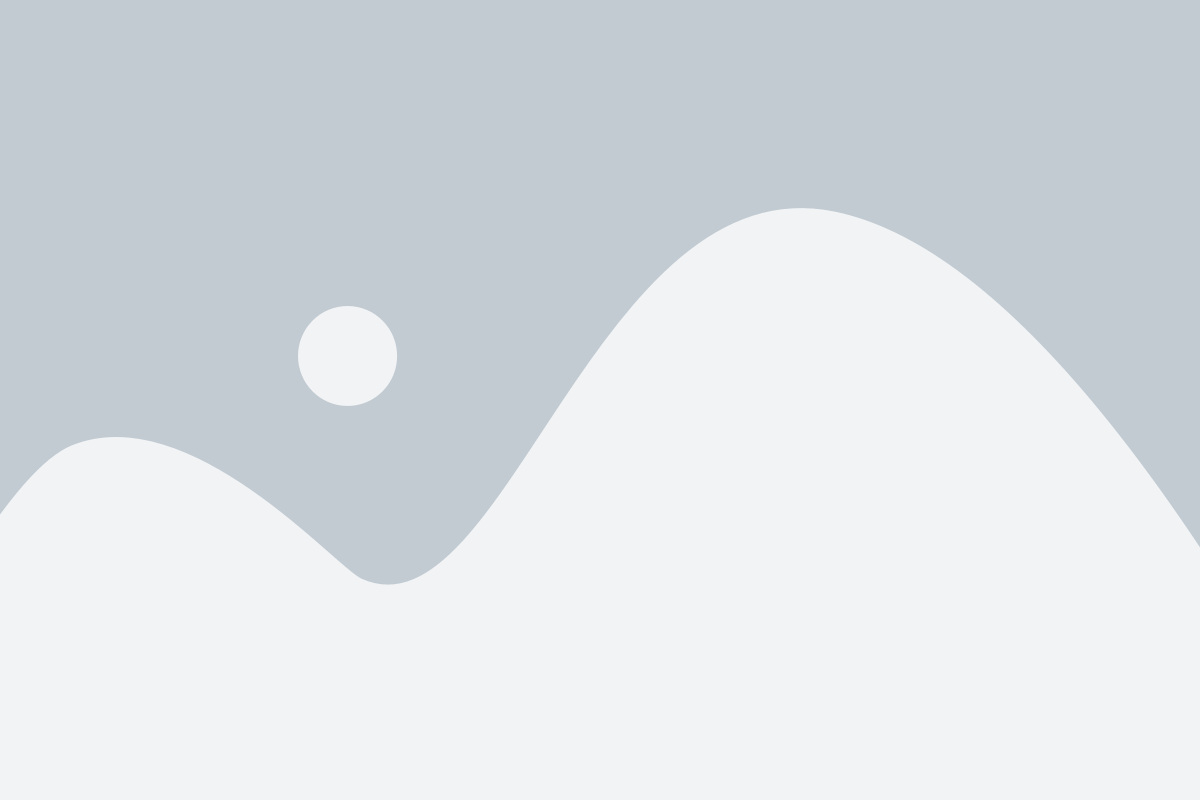
Induction Heater for Flywheels
Flywheels are critical components in many machines and equipment, and their proper installation is essential for optimal performance and longevity. Induction heaters can be used to heat flywheels before mounting them onto shafts or other components. Induction heating allows for precise and controlled heating, which helps to ensure that the flywheel fits securely onto the shaft without causing damage or distortion to the surrounding components.
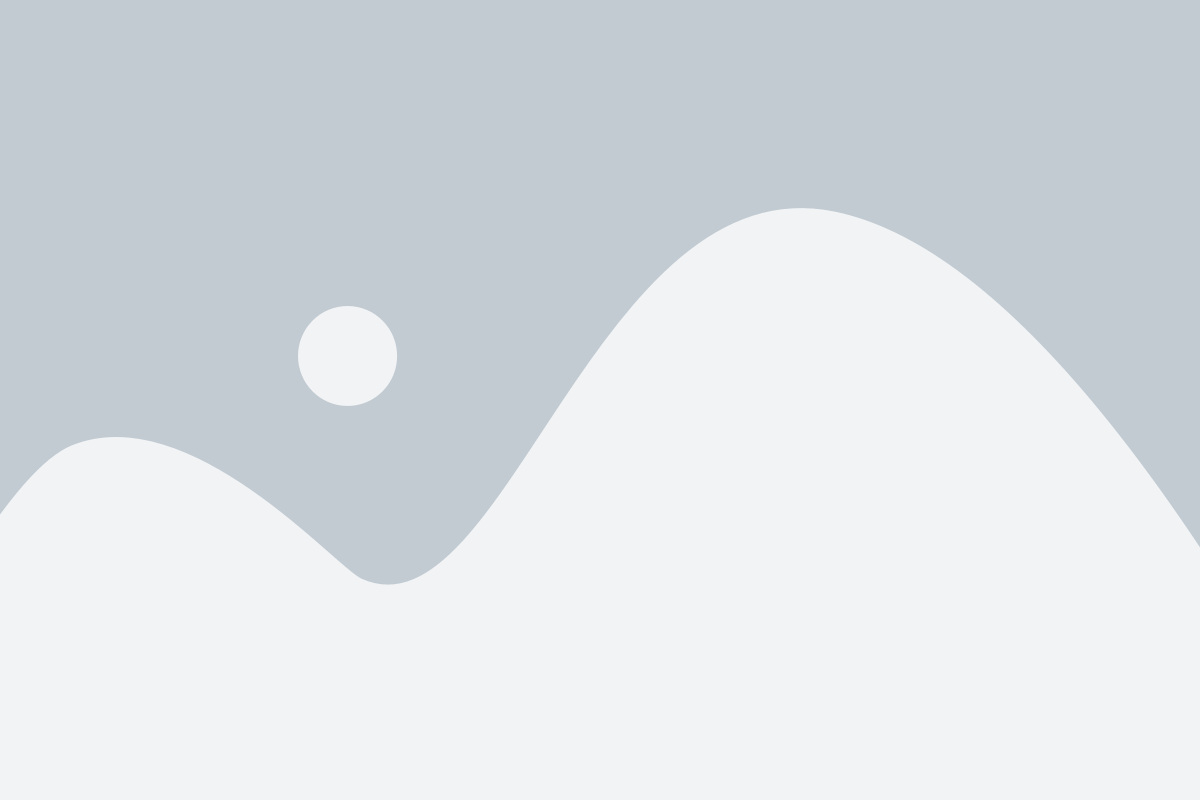
Induction Discs
Induction heating is a widely used process in the production of discs for various applications, such as brake discs, flywheels, and clutch discs. During the manufacturing process, the discs need to be heated to a specific temperature for shaping and forming. Induction heating provides a quick and efficient way to heat the discs evenly, allowing for precise control over the heating process. This ensures that the discs are formed accurately, with consistent quality and performance.
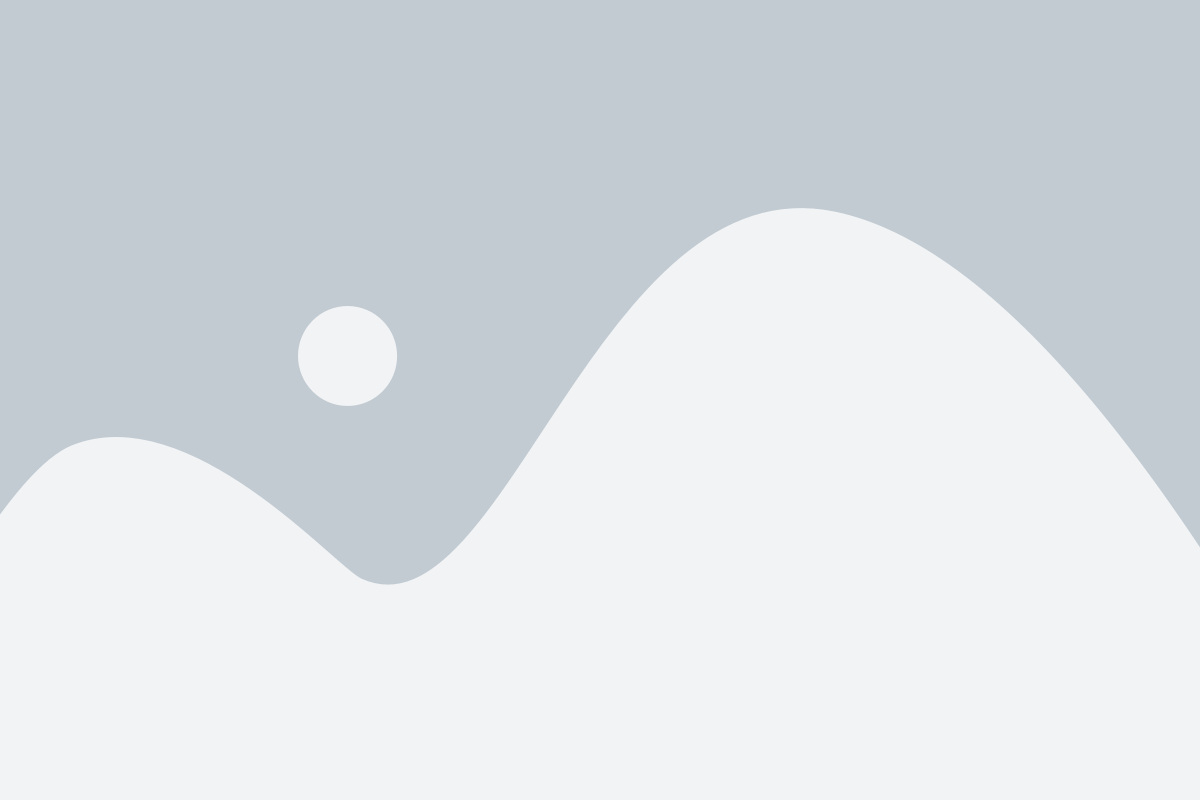
Induction Clutch
An induction heater is commonly used in the process of mounting a clutch onto a flywheel or a gearbox shaft. When a clutch is heated, it expands, making it easier to install onto the shaft. Induction heating provides a quick, safe, and efficient way to expand the clutch to the required size, ensuring proper alignment and secure attachment.
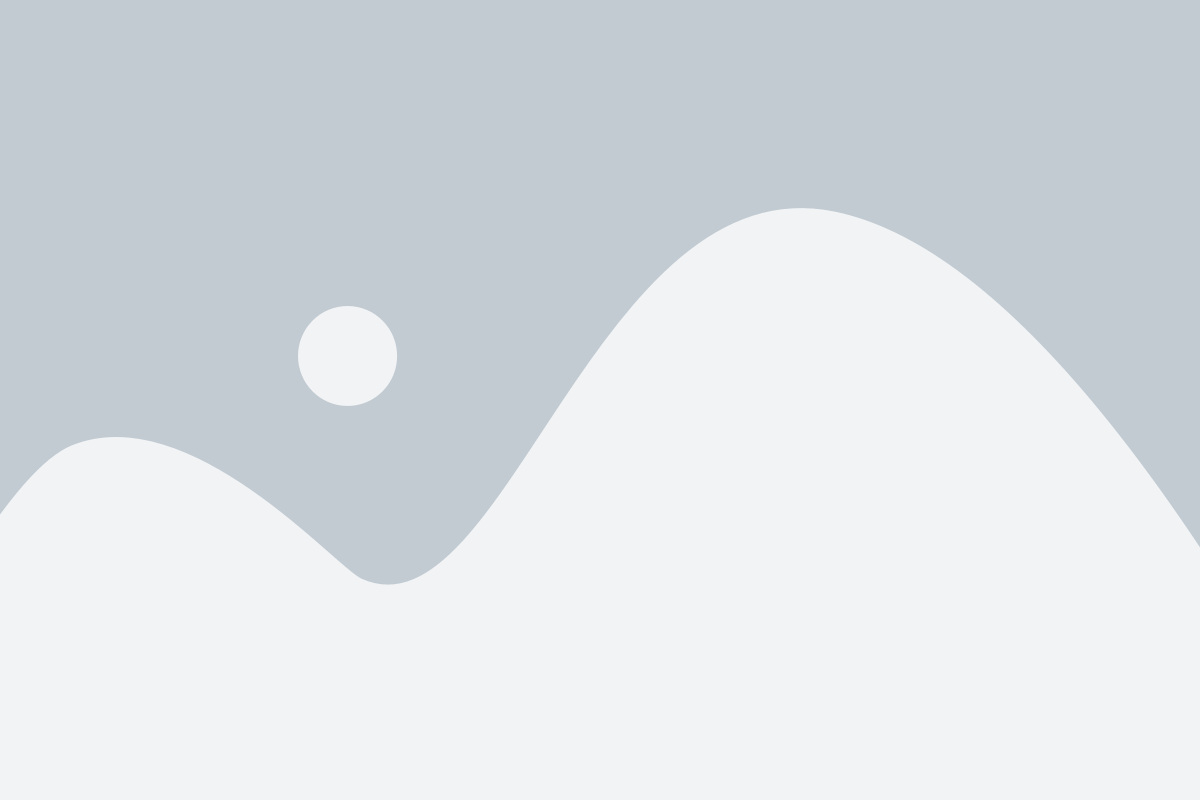
Induction Heater for Seals
Seals are critical components in various industrial applications, including automotive, aerospace, and oil and gas industries. The installation of seals can be a challenging task, as they need to be fitted into tight spaces with precision. Induction heating can be used to expand the seal, allowing for easier installation and a more secure fit. The process also reduces the risk of damaging the seal or the surrounding parts during installation.
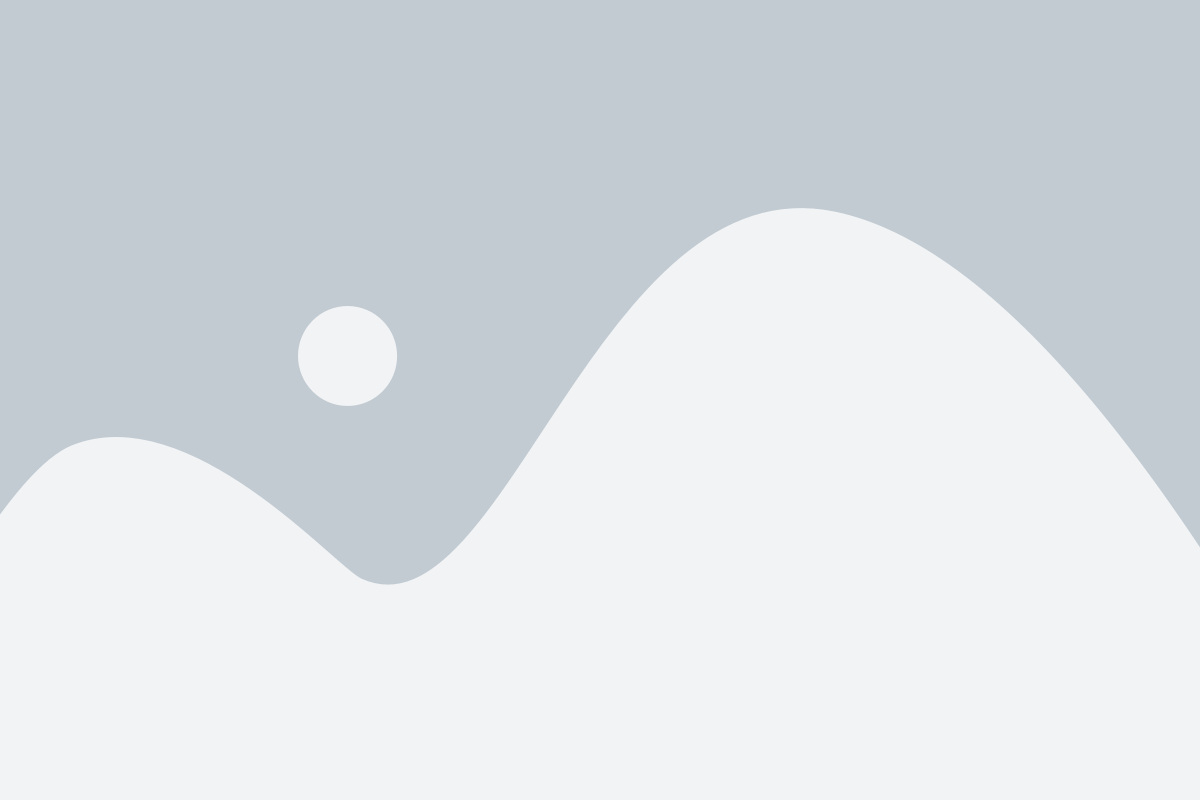
Induction Heater for Spindles
Spindles are widely used in various industries, including woodworking, metalworking, and textile manufacturing. The mounting of spindles involves fitting them onto a shaft or housing, ensuring proper alignment, and securing them in place. Induction heating provides a quick, safe, and efficient way to expand the spindle for installation. The process ensures accurate alignment, reducing the risk of damage to the spindle or surrounding parts.
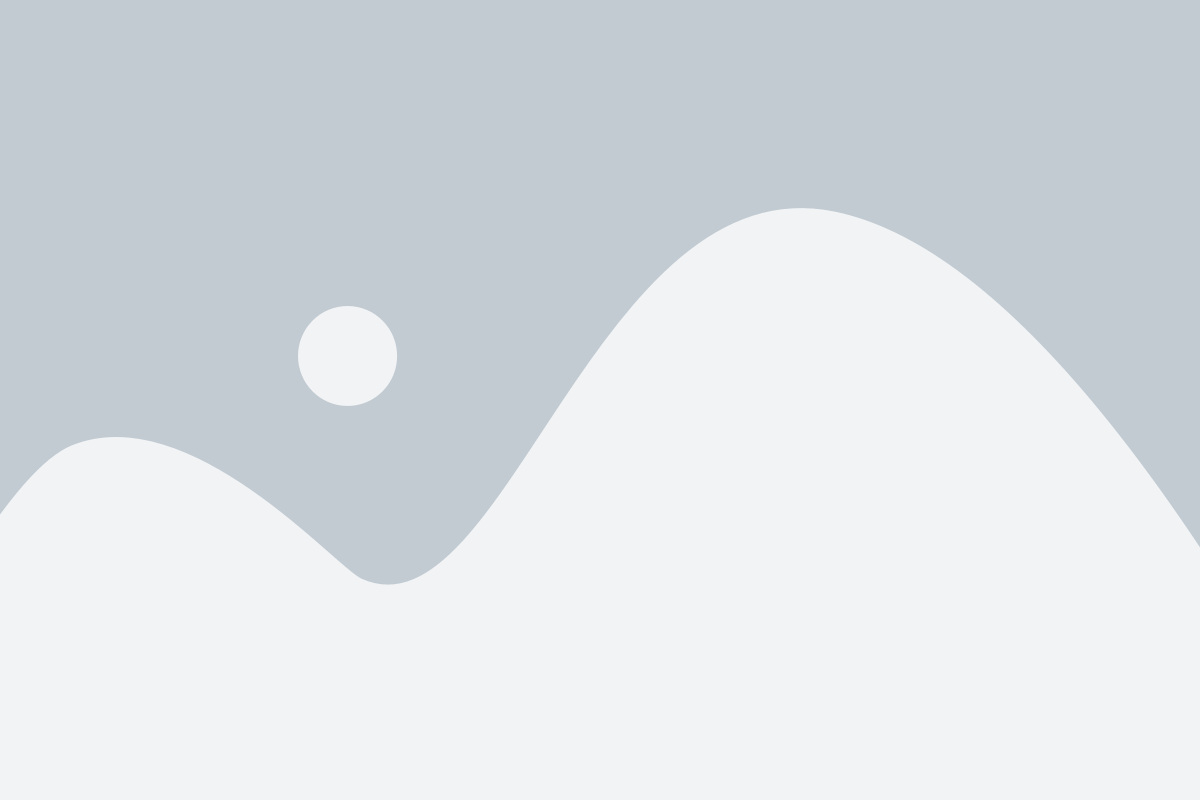
Induction Heater for Brake Rotors
Induction heating is commonly used in the production of brake rotors, which require heat treatment for shaping and hardening. The process involves heating the rotor to a specific temperature and then quenching it in a controlled manner to achieve the desired hardness and strength. Induction heating provides a quick, efficient, and precise way to heat the rotor, ensuring consistent quality and performance.
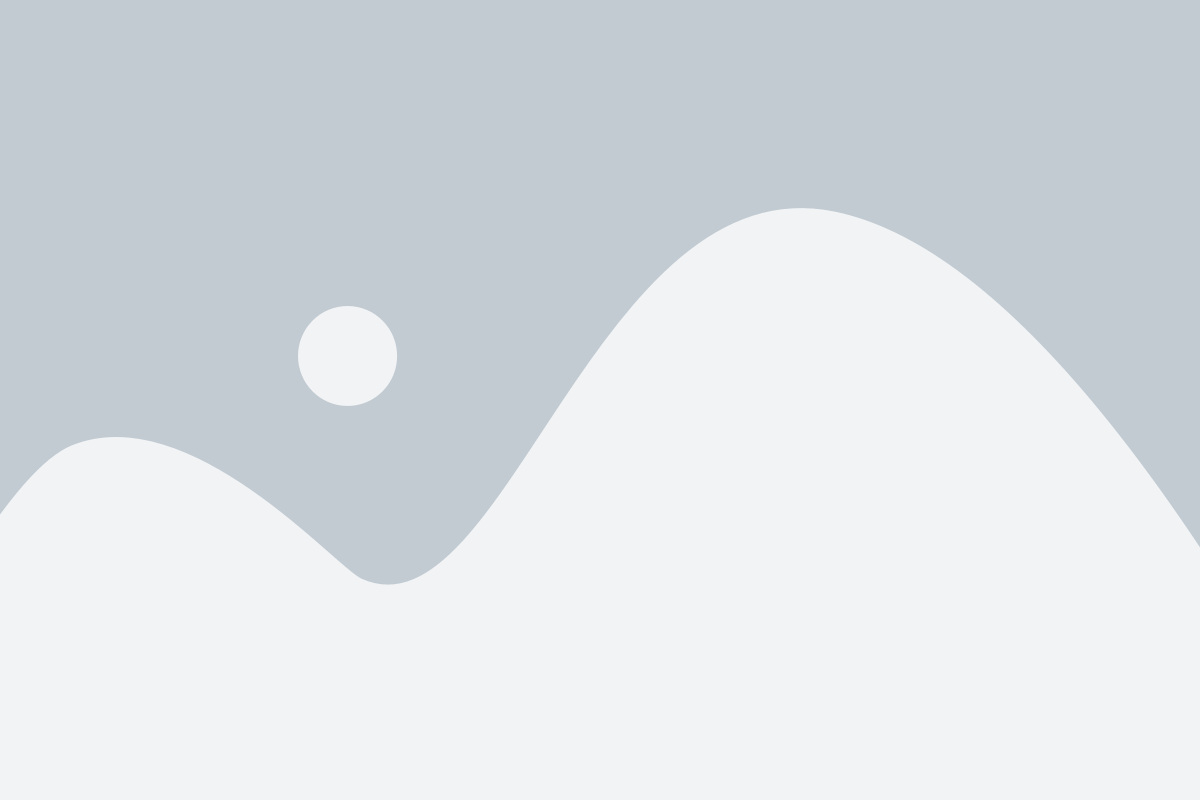
Induction Heater for Pump Impellers
Pump impellers are critical components in various industrial applications, including water treatment, chemical processing, and oil and gas production. The mounting of impellers onto a shaft involves fitting them onto the shaft and securing them in place. Induction heating can be used to expand the impeller for easier installation, ensuring accurate alignment and a secure fit. The process reduces the risk of damage to the impeller or surrounding parts during installation.
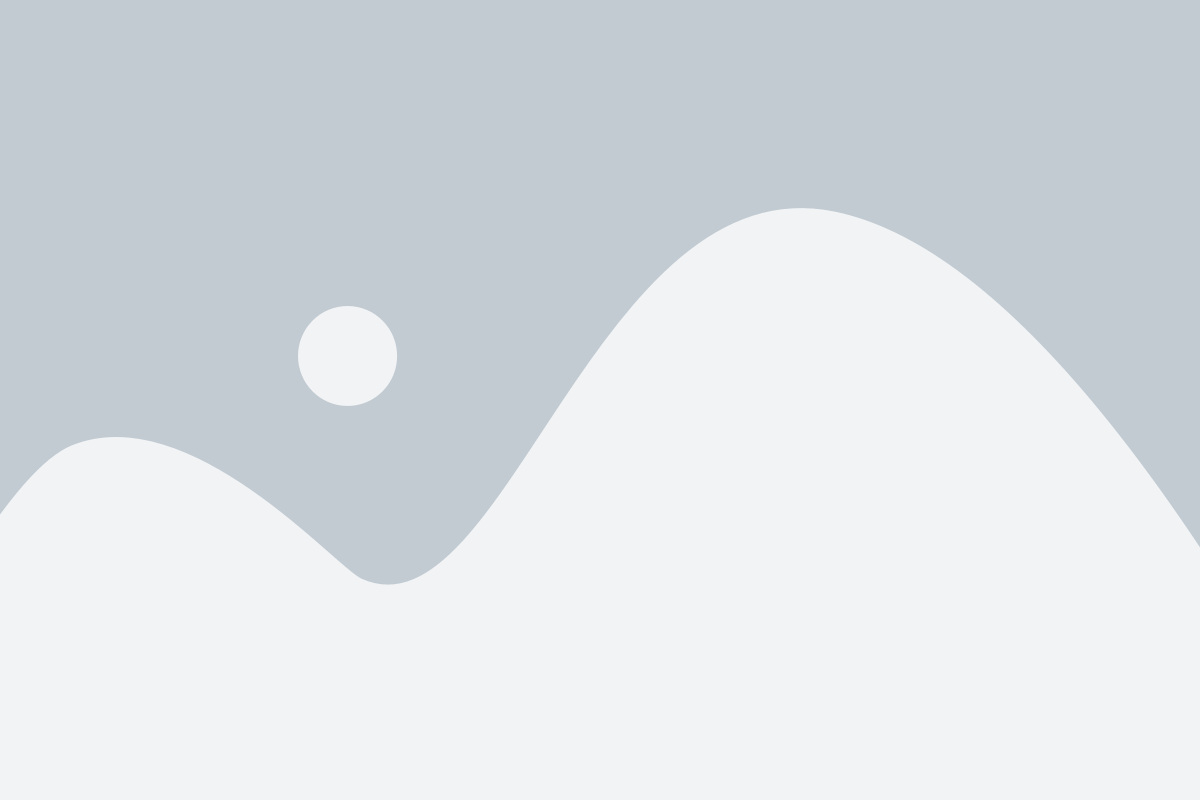
Induction Heater for Turbine Blades
Turbine blades are critical components in power generation, aerospace, and marine applications. The mounting of blades involves fitting them onto a rotor and securing them in place. Induction heating can be used to expand the blade for easier installation, ensuring accurate alignment and a secure fit. The process ensures consistent quality and performance, reducing the risk of damage to the blade or surrounding parts.
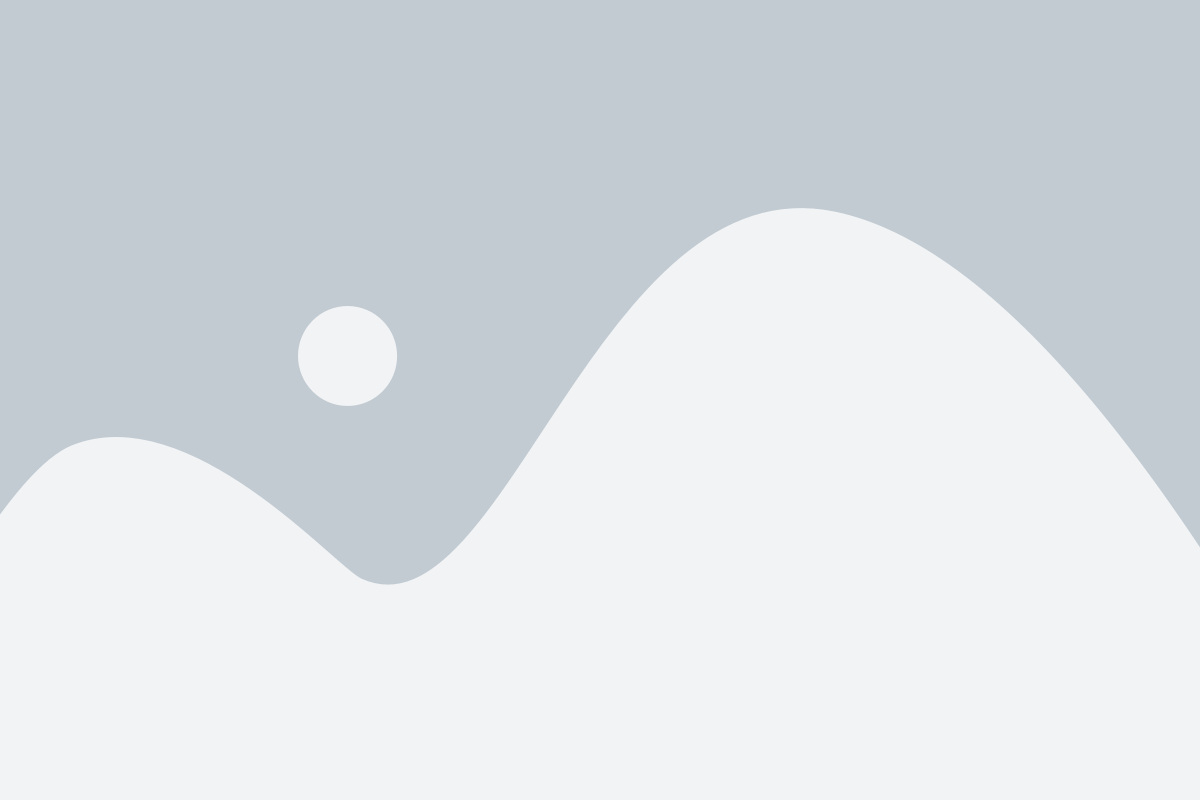
Induction Heater for Electrical Connectors
Electrical connectors are widely used in various industries, including automotive, aerospace, and electronics. The installation of connectors involves fitting them onto a wire or cable and securing them in place. Induction heating can be used to expand the connector for easier installation, ensuring accurate alignment and a secure fit. The process reduces the risk of damage to the connector or surrounding parts during installation.
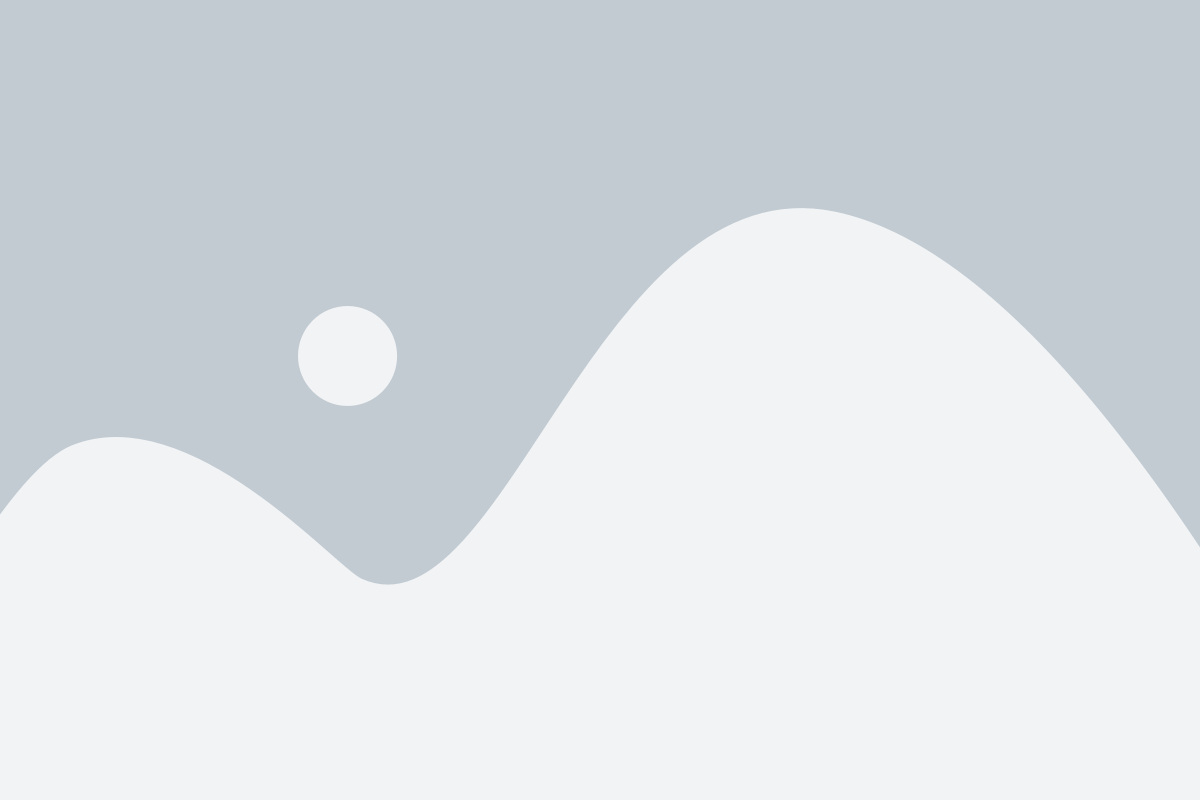
Induction Heater for Flanges
Flanges are critical components in various industrial applications, including pipelines, pressure vessels, and heat exchangers. The installation of flanges involves fitting them onto a pipe or vessel and securing them in place. Induction heating can be used to expand the flange for easier installation, ensuring accurate alignment and a secure fit. The process ensures consistent quality and performance, reducing the risk of leaks or other issues that can compromise the integrity of the system.
Induction Heaters Offered by GM Industries
For more information on any of our high quality products or getting accurate prices contact GM Industries at
Call Us
+(91)-9820533489 / 7738562224
Enquiry Form
Submit
Frequently Asked Questions
An industrial induction heater is a device that uses electromagnetic induction to generate heat in a workpiece, allowing for precise and controlled heating for various industrial processes, including mounting.
An induction heater can be used for mounting processes involving bearings, shafts, sprockets, sleeves, bushings, hubs, pulleys, cylinders, flywheels, seals, spindles, brake rotors, pump impellers, turbine blades, electrical connectors, flanges, and more.
Induction heating is used for mounting processes because it provides a quick, safe, and efficient way to expand the workpiece, making it easier to install onto a shaft or into a housing.
The benefits of using an induction heater for mounting processes include precise and controlled heating, reduced installation time, improved safety, consistent quality and performance, and reduced risk of damage to the workpiece.
Induction heating is different from other heating methods because it uses electromagnetic induction to generate heat directly within the workpiece, rather than heating from the outside.
An induction heater works by generating a high-frequency electromagnetic field, which induces eddy currents in the workpiece, causing it to heat up.
There are various types of induction heaters available for mounting processes, including Induction Heater GM 02 M (2.0 / 2.6 KVA), Induction Heater GM 04 (3.0/ 4.0 KVA), Induction Heater GM 04 M (3.6 /4.6 KVA), Induction Heater GM 10 (6.0 / 10.0 KVA).
Factors to consider when selecting an induction heater for mounting processes include the size and shape of the workpiece, the required heating temperature, the desired heating time, and the available power supply.
Safety measures when using an induction heater for mounting processes include wearing protective gear, ensuring proper grounding and electrical safety, and following the manufacturer’s instructions for use.
An induction heater can be used for mounting processes on a wide range of materials, including steel, aluminium, copper, brass, and more.
The maximum size of a workpiece that can be mounted using an induction heater depends on the capacity of the specific heater being used.
The heating time for a workpiece using an induction heater varies depending on the size and material of the workpiece, the desired temperature, and the power output of the heater.
Induction heaters are primarily used for heating processes but can also be used for cooling processes with the addition of a cooling element.
The power required to operate an induction heater for mounting processes varies depending on the size and type of the workpiece and the desired heating temperature.
The lifespan of an induction heater depends on the quality of the device and how well it is maintained, but can last for several years with proper use and maintenance.
Induction heaters can be used in hazardous environments, but the specific heater being used must be rated for such conditions.
The cost of an induction heater may vary depending on the size and specifications, but it is generally more expensive than other heating methods such as gas or electric heating. However, the efficiency and speed of induction heating can result in lower energy costs and higher productivity, making it a cost-effective solution in the long term.
Yes, induction heaters can be used for both small and large components, as long as the size and shape are suitable for the induction heating process. Larger components may require more powerful or specialized induction heaters, but the basic principles and benefits of induction heating apply to all sizes.